5. Define a Master Production Schedule (MPS) and explain how it differs from a final assembly schedule. 6. Define Material Requirements Planning (MRP) and how it can benefit an organization. 7. Explain a bill of materials (BOM), bill of labor (BOL), and bill of resources (BOR) relate. 8. What are the components of an MRP record? 9. Explain the three lot-sizing methods, and under what circumstances each work best: a. Lot-for-Lot (LFL) b. Fixed Order Quantity (FOQ) c. Periodic Order Quantity (POQ) 10. What is capacity requirements planning (CRP)? PROBLEM 1. A company currently has no items in inventory. The demand for the next four months is 200, 400, 250 and 350 units. Determine the level production rate if a level strategy is selected with the goal of ending Period 4 with 100 units in inventory. 2. A company currently has no items in inventory. The demand for the next four months is 200, 400, 250 and 350 units. Assuming a level production rate of 250 units per month, determine the month in which a backorder will materialize. 3. The Academic Company mixes and bottles a high-energy beverage in various container types and sizes for college students. The aggregate forecast for the next four quarters (1 year) in thousands of gallons is as follows: Quarter Forecast Demand per 1,000 Gallons 1 400 2 700 3 850 4 650 Total 2,600 Academic’s management makes the following assumptions: · Each employee works 550 standard hours of regular time each quarter. · On average, it takes 27 hours to produce and package 1 unit (1,000 gallons). · Regular-time labor costs $6.00/hour; overtime labor costs $9.00/hour. · Inventory holding cost is approximately $4.50/unit (1,000 gallons) per quarter based upon the ending inventory per quarter. · Because of extremely hot weather, there is no beginning inventory available to start Quarter 1. · Management wants a constant work force (no hiring or firing). · Managers have also decided to always round up the number of employees needed to the next whole integer, i.e., 37.2 yields 38 employees. a. Determine how many employees would be needed to meet the peak required in Quarter 3. b. Determine the annual inventory holding cost if Academic decides to use a level production rate of 650 units per quarter. c. Using a level schedule of 650 units per quarter, what will be the annual employee costs? d. Using a level schedule of 650 units per quarter, what will be the annual employee costs if only 30 employees are available and overtime is used? e. If management decides on a chase demand strategy, with production last quarter of 600 units and a rate change cost of $3.00/1000 gallons, determine the total rate change cost. 4. A paint company has the following aggregate demand requirements and cost data for the upcoming year by quarter. Quarter Forecast Demand (units) 1 1,200 2 1,500 3 1,900 4 1,000 Total 5,600 Previous quarter’s production: 900 units Beginning inventory: 0 units Backorder costs: $60/unit Inventory holding cost (on ending inventory): $12/unit/quarter Hiring employees: $30/unit increase Firing employees: $70/unit decrease a. Determine the change in workforce costs (hiring and firing employees) if the paint company decides to use a chase demand strategy. b. Determine the inventory holding and backorder costs for the year if the paint company wants to use a level production strategy, ending Quarter 4 with no inventory. 5. The bill of material for end item A is shown below: .jpg”> a. If A has a gross requirement to build 250 units and an on-hand inventory for A of 40, determine the net requirement for D if its current on-hand inventory balance for D is 20 (all other components have no current inventory). b. Determine the net requirement for F if the gross requirement for A is still 250 and current on-hand inventory balance for A is 40, D is 20 and F is 60. 6. The BOM for Product X is shown below, followed by a table of inventory data. The master production schedule quantity calls for the completion of 300 Xs in Week 7. The lead-time for production of X is 2 weeks and there are currently no units of X available. .jpg”> Data Category C D Lot Sizing Rule FOQ = 700 LFL Lead-Time 2 weeks 1 week Scheduled Receipts 0 0 Beginning (On-Hand Inventory) 200 200 a. When and what quantity will be the planned order release for Item C? b. Determine the week and the quantity of the planned order release for Item D. 7. Given the information below, complete the MRP record and explain what it tells the inventory analyst to do. Lot Size Rule: Fixed Q = 200 units Safety Stock: 0 units Lead Time = 2 weeks Current On-Hand Quantity = 100 units Week 1 2 3 4 5 6 7 8 Gross Requirement 50 100 60 0 0 50 90 200 Scheduled Receipts 200 Projected On Hand 100 Planned Receipts Planned Order Release 8. A manufacturing company is interested in making a product structure tree for one of its major products. They know that product A is made up of assemblies B, C, and D. Each B assembly is made up of one raw material F, and 2 E parts. Each C assembly is composed of 2 G parts and one H subassembly. Each H sub?assembly is made up of 2 F raw materials, 2 1 parts and 2 J parts. .png”> a. How many units of part G are needed to make one unit of product A? b. How many units of raw material F are needed to make up one unit of product A? 9. A company makes traffic signals for downtown streets. They are interested in developing a product structure tree for one of their traffic signal models. Each traffic signal is composed of a housing and bracket assembly. Each housing assembly is composed of optical and casing sub?assemblies. Each bracket assembly is composed of a hanger part and a wire outlet part. The optical sub?assembly is composed of 4 wire lead sub?assemblies, 3 lens parts, 3 bulbs, and 3 socket parts. Each casing sub?assembly is composed of 3 plastic molds and 3 hardware sub?assemblies. Each wire lead sub?assembly is made up of 1 conductor part, 1 insulation part, and 4 spade connector parts. Each hardware subassembly is made up of 4 nuts, 4 bolts, and 8 washers. .png”> a. How many spade connectors are needed to make one traffic signal? b. How many bolts are needed to make one traffic signal? 10. A hardware company is interested in developing a net requirement schedule for one of its products, a claw hammer. The beginning inventory for the product is 1500 units and the safety stock is 300 units. The weekly demand over a six-week planning horizon is 400, 850, 560, 900, 600, and 700 units. a. What would the net requirements be for week 2? b. What is the ending inventory in week 4?
5. Define a Master Production
explain how it differs from a final assembly schedule.
6. Define
Material Requirements Planning (MRP) and how it can benefit an organization.
7. Explain a bill of materials (BOM), bill of
labor (BOL), and bill of resources (BOR) relate.
8. What
are the components of an MRP record?
9. Explain
the three lot-sizing methods, and under what circumstances each work best:
a.
Lot-for-Lot
(LFL)
b.
Fixed Order
Quantity (FOQ)
c.
Periodic
Order Quantity (POQ)
10. What
is capacity requirements planning (CRP)?
PROBLEM
1. A
company currently has no items in inventory. The demand for the next four
months is 200, 400, 250 and 350 units. Determine the level production rate if a
level strategy is selected with the goal of ending Period 4 with 100 units in
inventory.
2. A
company currently has no items in inventory. The demand for the next four
months is 200, 400, 250 and 350 units. Assuming a level production rate of 250
units per month, determine the month in which a backorder will materialize.
3. The Academic Company mixes and bottles a high-energy beverage in
various container types and sizes for college students. The aggregate
for the next four quarters (1 year) in thousands of gallons is as follows:
Quarter
Forecast Demand
per 1,000 Gallons
1
400
2
700
3
850
4
650
Total
2,600
Academic’s management makes the
following assumptions:
·
Each
employee works 550 standard hours of regular time each quarter.
·
On average,
it takes 27 hours to produce and package 1 unit (1,000 gallons).
·
Regular-time
labor costs $6.00/hour; overtime labor costs $9.00/hour.
·
Inventory
holding cost is approximately $4.50/unit (1,000 gallons) per quarter based
upon the ending inventory per quarter.
·
Because of
extremely hot weather, there is no beginning inventory available to start
Quarter 1.
·
Management
wants a constant work force (no hiring or firing).
·
Managers
have also decided to always round up the number of employees needed to the
next whole integer, i.e., 37.2 yields 38 employees.
a. Determine how many employees would be needed
to meet the peak required in Quarter 3.
b. Determine the annual inventory holding cost
if Academic decides to use a level production rate of 650 units per quarter.
c. Using a level schedule of 650 units per quarter, what will be the
annual employee costs?
d. Using a level schedule of 650 units per
quarter, what will be the annual employee costs if only 30 employees are
available and overtime is used?
e. If management decides on a chase demand
strategy, with production last quarter of 600 units and a rate change cost of
$3.00/1000 gallons, determine the total rate change cost.
4. A paint company has the following aggregate demand requirements
and cost data for the upcoming year by quarter.
Quarter
Forecast Demand (units)
1
1,200
2
1,500
3
1,900
4
1,000
Total
5,600
Previous
quarter’s production:
900 units
Beginning
inventory:
0 units
Backorder
costs:
$60/unit
Inventory
holding cost
(on ending
inventory):
$12/unit/quarter
Hiring
employees:
$30/unit
increase
Firing
employees:
$70/unit
decrease
a. Determine the change in workforce costs
(hiring and firing employees) if the paint company decides to use a chase
demand strategy.
b. Determine the inventory holding and backorder
costs for the year if the paint company wants to use a level production
strategy, ending Quarter 4 with no inventory.
5. The bill of material for end item A is shown
below:
.jpg”>
a. If A has a gross requirement to build 250
units and an on-hand inventory for A of 40, determine the net requirement for D
if its current on-hand inventory balance for D is 20 (all other components have
no current inventory).
b. Determine the net requirement for F if the
gross requirement for A is still 250 and current on-hand inventory balance for
A is 40, D is 20 and F is 60.
6. The BOM for Product X is shown below, followed by a table of
inventory data. The master production schedule quantity calls for the
completion of 300 Xs in Week 7. The lead-time for production of X is 2 weeks
and there are currently no units of X available.
.jpg”>
Data
Category
C
D
Lot Sizing
Rule
FOQ = 700
LFL
Lead-Time
2 weeks
1 week
Scheduled
Receipts
0
0
Beginning
(On-Hand Inventory)
200
200
a. When and what quantity will be the planned
order release for Item C?
b. Determine the week and the quantity of the
planned order release for Item D.
7. Given the information below, complete the MRP
record and explain what it tells the inventory analyst to do.
Lot Size
Rule: Fixed Q = 200 units
Safety
Stock: 0 units
Lead Time =
2 weeks
Current
On-Hand Quantity = 100 units
Week
1
2
3
4
5
6
7
8
Gross
Requirement
50
100
60
0 0
50
90
200
Scheduled
Receipts
200
Projected On
Hand 100
Planned
Receipts
Planned
Order Release
8. A
manufacturing company is interested in making a product structure tree for one
of its major products. They know that product A is made up of assemblies B, C,
and D. Each B assembly is made up of one raw material F, and 2 E parts. Each C
assembly is composed of 2 G parts and one H subassembly. Each H sub?assembly is
made up of 2 F raw materials, 2 1 parts and 2 J parts.
.png”>
a. How many units of part G are
needed to make one unit of product A?
b. How many units of raw
material F are needed to make up one unit of product A?
9. A company
makes traffic signals for downtown streets. They are interested in developing a
product structure tree for one of their traffic signal models. Each traffic
signal is composed of a housing and bracket assembly. Each housing assembly is
composed of optical and casing sub?assemblies. Each bracket assembly is
composed of a hanger part and a wire outlet part. The optical sub?assembly is
composed of 4 wire lead sub?assemblies, 3 lens parts, 3 bulbs, and 3 socket
parts. Each casing sub?assembly is composed of 3 plastic molds and 3 hardware
sub?assemblies. Each wire lead sub?assembly is made up of 1 conductor part, 1
insulation part, and 4 spade connector parts. Each hardware subassembly is made
up of 4 nuts, 4 bolts, and 8 washers.
.png”>
a. How many spade connectors are needed to make one traffic signal?
b. How many bolts are needed to
make one traffic signal?
10. A hardware
company is interested in developing a net requirement schedule for one of its
products, a claw hammer. The beginning inventory for the product is 1500 units
and the safety stock is 300 units. The weekly demand over a six-week planning
horizon is 400, 850, 560, 900, 600, and 700 units.
a. What would the net requirements be for week 2?
b. What
is the ending inventory in week 4?

Trending now
This is a popular solution!
Step by step
Solved in 4 steps

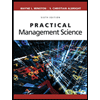
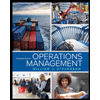
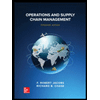
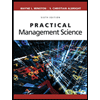
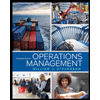
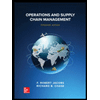
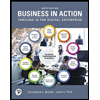
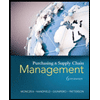
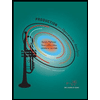