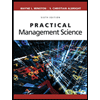
Concept explainers
. Goop Inc. needs to order a raw material to make a special polymer. The demand for
the polymer is
a standard deviation of 100 gallons. Goop sells the polymer for $25 per gallon. Goop
purchases raw material for $10 per gallon and must spend $5 per gallon to dispose of all
unused raw material due to government regulations. (One gallon of raw material yields
one gallon of polymer.) If demand is more than Goop can make, then Goop sells only
what it has made and the rest of the demand is lost.
a. How many gallons should Goop purchase to maximize its expected profit?
b. Suppose Goop purchases 150 gallons of raw material. What is the probability that it
will run out of raw material?
c. Suppose Goop purchases 300 gallons of raw material. What are the expected sales (in
gallons)?
d. Suppose Goop purchases 400 gallons of raw material. How much should it expect to
spend on disposal costs (in dollars)?
e. Suppose Goop wants to ensure that there is a 92 percent probability that it will be able
to satisfy its customers’ entire demand. How many gallons of the raw material should
it purchase?

Trending nowThis is a popular solution!
Step by stepSolved in 5 steps

- A golf specialty wholesaler operates 50 weeks per year. Management is trying to determine an inventory policy for its 1-irons, which have the following characteristics: > Demand (D) = 2,000 units/year > Demand is normally distributed > Standard deviation of weekly demand = 2 units > Ordering cost = $30/order > Annual holding cost (H) = $5.00/unit > Desired cycle-service level = 85% > Lead time (L) = 4 weeks Refer to the standard normal table for z-values. a. If the company uses a periodic review system, P should be 3.87 weeks. (Enter your response rounded to the nearest whole number.) T should be units. (Enter your response rounded to the nearest whole number.)arrow_forwardDalia, the office manager of a desktop publishing outfit, stocks replacement toner cartridges for laser printers. Demand for cartridges is approximately 30 per year and is quite variable (Le., can be represented using the Poisson distribution). Cartridges cost $100 each and require three weeks to obtain from the vendor. Dalia uses a (Q, r) approach to control stock levels (a). If Dalia wants to restrict replenishment orders to twice per year on average, what batch size Q should she use? If she wants to ensure a service level (i.e., probability of having the cartridge in stock when 2 out of 2 needed) of at least 98 percent, what reorder point r should she use? (Hint: Use Table 2.6.(b). If Dalia is willing to increase the number of replenishment orders per year to six, how do Q and r change? Explain the difference in r.arrow_forwardA small grocery store sells fresh produce, which it obtains from a local farmer. During the strawberry season, demand for fresh strawberries can be reasonably approximated using a normal distribution with a mean of 36 quarts per day and a standard deviation of 7 quarts per day. Excess costs run .40 cents per quart. The grocer orders 42 quarts per day.Use Table. What is the implied cost of shortage per quart?arrow_forward
- Gentle Ben's Bar and Restaurant uses 7,200 quart bottles of an imported wine each year. The effervescent wine costs $9 per bottle and is served only in whole bottles because it loses its bubbles quickly. Ben figures that it costs $25 each time an order is placed, and holding costs are 40 percent of the purchase price. It takes six weeks for an order to arrive. Weekly demand is 144 bottles (closed two weeks per year) with a standard deviation of 40 bottles. Ben would like to use an inventory system that minimizes inventory cost and will provide a 99 percent service probability. a. What is the economic quantity for Ben to order? b. At what inventory level should he place an order?arrow_forwardSouthern Markets, Inc. is considering the use of ABCanalysis to focus on the most critical SKUs in its inventory.Currently, there are approximately 20,000 different SKUswith a total dollar usage of $10,000,000 per year.a. What would you expect to be the number of SKUs and thetotal annual dollar usage for A items, B items, and C itemsat Southern Markets, Inc.? b. The following table provides a random sample of the unitvalues and annual demands of eight SKUs. Categorizethese SKUs as A, B, and C items.arrow_forwardPalin’s Muffler Shop has one standard muffler that fits a large variety of cars. The shop wishes to establish a periodic review system to manage inventory of this standard muffler. Use the information in the following table to determine the optimal inventory target level (or order-up-to level). Annual demand 2,750 mufflers Ordering cost $ 35 per order Standard deviation of daily demand 6 mufflers per working day Service probability 76 % Item cost $ 28.00 per muffler Lead time 4 working days Annual holding cost 22 % of item value Working days 275 per year Review period 21 working days a. What is the optimal target level (order-up-to level)? If the service probability requirement is 93 percent, the optimal target level will: Increase Decrease Stay the samearrow_forward
- Fisk Corporation is trying to improve its inventory control system and has installed an online system at its retail stores. Fisk anticipates sales of 58,800 units per year, an ordering cost of $4 per order, and carrying costs of $1.50 per unit. In the second year, Fisk Corporation finds that it can reduce ordering costs to $1 per order, but carrying costs will stay the same at $1.50 per unit. a-1. What is the economic ordering quantity for the second year? Economic ordering quantity (EOQ) a-2. How many orders will be placed during the second year? Number of orders a-3. What will the average inventory be for the second year? Average inventory Total costs units units a-4. What is the total cost of ordering and carrying inventory for second year? LAarrow_forwardA coffee shop consumes 350 lbs of coffee per week at a steady rate. The coffee shop buys coffee from a supplier at the cost of $10 per lb, and ordering cost of $5 per order. The supplier takes 8 days to deliver an order (assume that 1 week = 7 days). What should be the reorder point (in pounds) for the coffee shop (i.e., at what level of inventory it should place an order with the supplier).arrow_forwardExplain the following based on Demand Management Demand Management Independent Demand Dependent Demand Random Variations Safety Stocksarrow_forward
- Andy's Job Shop buys two parts (Tegdiws and Widgets) for use in its production system from two different suppliers. The parts are needed throughout the entire 52-week year to assemble Uediracs for sale. Tegdiws are used at a relatively constant rate but the use of Widgets vary with demand. Andy wants to improve his inventory management system and use either a "P" system or a "Q" system. What are the advantages and disadvantages of each system in this application and what information is needed to choose between them?arrow_forwardIn an ABC system based on revenue, C items individually make the lowest annual revenue contribution. TRUE FALSEarrow_forwardPlease do not give solution in image format thankuarrow_forward
- Practical Management ScienceOperations ManagementISBN:9781337406659Author:WINSTON, Wayne L.Publisher:Cengage,Operations ManagementOperations ManagementISBN:9781259667473Author:William J StevensonPublisher:McGraw-Hill EducationOperations and Supply Chain Management (Mcgraw-hi...Operations ManagementISBN:9781259666100Author:F. Robert Jacobs, Richard B ChasePublisher:McGraw-Hill Education
- Purchasing and Supply Chain ManagementOperations ManagementISBN:9781285869681Author:Robert M. Monczka, Robert B. Handfield, Larry C. Giunipero, James L. PattersonPublisher:Cengage LearningProduction and Operations Analysis, Seventh Editi...Operations ManagementISBN:9781478623069Author:Steven Nahmias, Tava Lennon OlsenPublisher:Waveland Press, Inc.
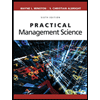
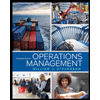
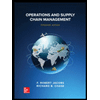
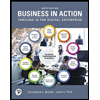
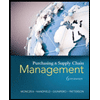
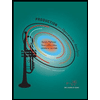