OIM 350 HW#4
docx
keyboard_arrow_up
School
University of Massachusetts, Amherst *
*We aren’t endorsed by this school
Course
350
Subject
Mechanical Engineering
Date
Jan 9, 2024
Type
docx
Pages
5
Uploaded by ElderWillpower12773
Problem 1
1.
Construct an X-bar R chart using subgroups of size 6.
2.
Comment on the results from this analysis.
As you can see above in the X-bar & R chart, all points fall within the control limits and
there does not seem to be any trend or pattern within the control limits. This tells us
that the process is stable. We can say that any variation that occurs is due to the
common variation of the process.
3.
Plot the data as a time series and comment (hint: sample/head on the x-axis and height
on the y- axis). Do you see any patterns or assignable causes?
By using the data as a time series, we can observe that the patterns are repeated. Every
bottle created according to their rank in manifaturing is the almost the same as the
product created 30 later but with the same rank. For ex. A bottle created 1
st
has the
same Hight as the 7
th
bottle and the 13
th
bottle and so on. You can see it better in the
data table labeled Time series height by sample in JMP (check JMP data table).
4.
Construct a comparison boxplot (compare box plots of the 6 “heads”). Comment on the
graph.
As you can see in the box plot the height when compared to the head is very similar.
Other than no.2 most of the highest fall within 0.05 of each other and in some cases the
height is the same. This tells us that if a bottle is produced in the 1
st
head all the 1
st
head
bottles are going to be of similar height.
5.
Perform a one-way ANOVA. What does this analysis tell you (and how did you get to
your conclusion)?
Looking at ANOVA we can tell that Since the p-value is less than 0.05 we reject the null
hypothesis and conclude that not all means are equal (at least one mean is different).
We can also tell that head 4 has the heist mean and the lowest amount of gap between
each bottle produced. (Graph was too long see JMP file attached to look at the graph
and data table for ANOVA).
6.
Using the output in 3-5 to comment on what you think the problem is as well as any
assignable causes and how the shampoo company can resolve the label variability
problem. Why do you think the X-bar R chart did not provide obvious clues as to what
the problem was?
I think our problem is a malfunction in the production line where the height of the bottle is
determined by which head the bottle belongs in. the bottle produced 1
st
is going to have
different 1
st
has different height than other bottles but the bottle produced 1
st
in the
second batch has similar height as the first one. So, to fix the problem we need to fix the
malfunction in the production line or maybe do the following: all products produced 1
st
will go in the same box, all bottles produced second should go in the same box, so on
and so forth. This will lead to all the heights in being same as the rest when a supplier
gets their boxes of shampoo. You could also produce all the bottles same as head 4
since it has the least distribution resulting in all the bottles being similar.
X-bar & R chart
could not provide us with this data because it cannot scale the difference when the input
in very tiny. It only looks at whether the process is within the control limit or not.
Problem #2
1.
After watching the video (and/or read the transcript), briefly
summarize the problem
that the company encountered (what is tin dust? Why do they want to reduce it?...) and
what did they do to solve the problem
. Make note of who participated in the project
and which steps did they take (refer to DMAIC or PDCA). Focus on the solution process.
You will analyze the data in the subsequent questions
The problem the company encountered was having tin dust in their production lines. Tin
dust is the dust produced by tin. The company used lots of tin. The y wanted to reduce
tin dust because it resulted in them having to clean tin dust-off production line all the
time. To address this issue, the quality manager, Marcus, assembled a cross-functional
team consisting of individuals from production, technical, and maintenance departments.
The team adopted a problem-solving approach inspired by the Six Sigma DMAIC
(Define, Measure, Analyze, Improve, Control) framework. To solve the problem by
following these steps:
Define:
Identified the problem: Excessive tin dust in production lines causing frequent
cleaning.
Goal: Reduce tin dust to enhance production efficiency.
Measure:
Established a baseline by observing and measuring tin dust production after
25,000 lids.
Your preview ends here
Eager to read complete document? Join bartleby learn and gain access to the full version
- Access to all documents
- Unlimited textbook solutions
- 24/7 expert homework help
Determined that more than two kilograms of tin dust triggered the need for line
cleaning.
Analyze:
Formed a team to brainstorm potential root causes for tin dust.
Identified key variables, including thickness of tin sheet, piston measurements,
and coating presence on the piston.
Improve:
Utilized SAS JMP to set up a Design of Experiments (DOE) to analyze the impact
of variables on tin dust.
Executed experiments over a week, collecting data on tin dust with varying
settings.
Analyzed the data using statistical tools to identify significant factors affecting tin
dust.
Control:
Conducted further trials to validate the proposed changes.
Implemented optimal solutions, including coating the piston and adjusting
Measurement 3 to 2.0, based on statistical analysis.
Emphasized the importance of controlling the production process to maintain
reduced tin dust levels.
2.
Related Documents
Related Questions
What is relation between product tolerance (engineering tolerance) and process variation.? Explain in some details showing some representation.
Analyze the following study in terms:
Components of variations and their contributions
X Chart and R Chart
arrow_forward
The sales of a product during the last four years were 860, 880, 870 and 890 units. The forecast for the fourth year was 876 units. If the forecast for the fifth year, using simple exponential smoothing, is equal to the forecast using a three period moving average, what is the value of the exponential smoothing constant?
arrow_forward
A company uses exponential smoothing with trend toforecast monthly sales of its product, which show a trend pattern.At the end of week 5, the company wants to forecast sales for week6. Th e trend through week 4 has been 20 additional cases sold perweek. Average sales have been 85 cases per week. The demand forweek 5 was 90 cases. Th e company uses α = 0.20 and β = 0.10.Make a forecast including trend for week 6
arrow_forward
The data shown in Table 1 are the deviations from nominal diameter for holes drilled in a
carbon-fiber composite material used in aerospace manufacturing. The values reported are
deviations from nominal in ten-thousandths of an inch.
(a) Set up and R charts on the process. Is the process in statistical control?
(b) Estimate the process standard deviation using the range method.
(c) If specifications are at nominal ±100, what can you say about the capability of this
process? Calculate the PCR Cp
Table 1. Hole Diameter Data
Sample
Number X1 X2
1
2
3
4
5
6
7
8
9
10
11
12
14
15
16
17
18
19
20
-30 +50
0
-50
-10 -10
+20
-40
0
0
-30
0
+20
0
0
+70
0
+10
+40
+30
+30
+30
+10
0
+20
+50
+50
-20
+50 -60
+10
0
0
+20
+10 -20
-10
0
+20
X3 X4 X5
-30
+20
+30
+50
+40
+20
+30
+20
+30
+20
+30
0
+20
+10 +40
+10 +10
-10 +50
-10 -30
-10
+50
+40
0
+30
-10
0
+30
+30
-20
+50 +30 +10
+40
+20
0 +30
+10 +30
-20 +30
+30
+20
-20 +50
+20
+10
-40 +20
-20
-10
-10
0
-20
+10
+10 +50
0
+10
arrow_forward
Given the cost function C(x) and the revenue function R(x), find the number of units x that must be sold to break even.
C(x) = 14x + 56,000 and R(x) = 18x.
How many units must be produced and sold in order to break even?
units
Help me solve this
View an example
Get more help -
Clear a
arrow_forward
What is the relation between product tolerance and product variation?
arrow_forward
Question 4
What is relation between product tolerance (engineering tolerance) and process variation.? Explain in some details showing some representation.
Analyze the following study in terms:
Components of variations and their contributions
X Chart and R Chart
3.
Calculate the process capability (show your method). Is it acceptable? Comment on this result.
arrow_forward
Please show all your work neatly including finding the correct units.
for : A% = 40+51, so A =91%
for : P_LA=B hPa. B= 0+1012, so B = 1012
for : P_denver=C hPa. C=3+838, so C =841
arrow_forward
production planning and control help please
arrow_forward
True, False or Uncertain. Explain your answer.
Own wage elasticity JELLlincrease if product demand elasticity n? is high.
In short run, when there is an increase in wage rate, each firm will hire less labor
and so the industry labor demand is simply the horizontal summation of firm's
labor demand.
а.
b.
Labor demand is represented by the marginal revenue produce schedule (MRP)
when we have competitive product market while it will be represented by the
value of marginal product schedule (VMP) when we have a product market
monopolist.
When elasticity of substitution, SLK, increase that means the L and K are less
substitutable, and the isoquant will be L-shaped.
Minimum wage imposed by the government is always bad for the economy
because it increase unemployment and deadweight loss.
с.
d.
e.
3.
arrow_forward
8. Why do experiments have a control group as part of the design?
to see if the treatment (changing the independent variable) has any effect
to use as a backup, In case the experiment fails the first time
O to help the scientists determine which varlable is the dependent variable
to minimize the number of varlables in the experiment
arrow_forward
A process is in statistical control with and ?= 39.7. The control chart uses a sample size of n = 2. Specifications are at 40 ± 5. The quality characteristic is normally distributed. How much improvement could be made in process performance if the mean could be centered at the nominal value?
arrow_forward
A dealer of white goods buys washing machines from Arçelik. In their next order, they plan to buy two models for which the related data are as follows:
Washing machine model
2.
Annual demand (units)
6800
8500
Ordering cost (TL)
125
125
Unit purchasing cost (TL)
2400
1900
Transportation cost per unit (TL.)
250
220
The dealer has allocated a budget of 23,000 TL for the transportation of the machines from the factory. Assume that the anmual invontory carrying cost rate is 30 percent.
Calculate the unconstrained order quantities. Are these values optimal? If not, determine the optimal quantities to be stored from each model (Hint: is 0.337)
arrow_forward
Basic Manufacturing Process with 2 Job Types +
Inspection
Time between job arrivals at a machining station is exponentially distributed with mean 4.4 minutes.
There are 2 types of jobs to be processed 30% of which is Type 1 and, 70% are of Type 2. Processing
times are exponentially distributed. Mean processing time for Type 1 is 4.8 minutes, for Type 2 it is
2.5 minutes.
After the job is processed, they go through an inspection process with one single inspector and an
inspection time with triangular distribution (1,2,3.5). Inspector decides whether the part is good
enough, scrap or should be reworked. 80% of the parts produced is good, 10 % is scrap and the rest
needs rework.
Rework is done by the same manufacturing machine. The priority among the parts will be Part1 first,
part2 second and reworks of both type comes later. Rework time is normally distributed with mean 2
minutes and 0,2 std dev.
Simulate the system for one 8-hour day.
arrow_forward
Do not provide handwritten solution,Maintain accuracy and quality in your answer,Take care of plagiarism,Answer completely,You will get up vote for sure.
arrow_forward
SEE MORE QUESTIONS
Recommended textbooks for you
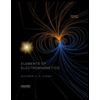
Elements Of Electromagnetics
Mechanical Engineering
ISBN:9780190698614
Author:Sadiku, Matthew N. O.
Publisher:Oxford University Press
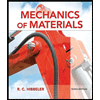
Mechanics of Materials (10th Edition)
Mechanical Engineering
ISBN:9780134319650
Author:Russell C. Hibbeler
Publisher:PEARSON
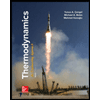
Thermodynamics: An Engineering Approach
Mechanical Engineering
ISBN:9781259822674
Author:Yunus A. Cengel Dr., Michael A. Boles
Publisher:McGraw-Hill Education
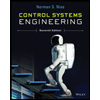
Control Systems Engineering
Mechanical Engineering
ISBN:9781118170519
Author:Norman S. Nise
Publisher:WILEY
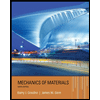
Mechanics of Materials (MindTap Course List)
Mechanical Engineering
ISBN:9781337093347
Author:Barry J. Goodno, James M. Gere
Publisher:Cengage Learning
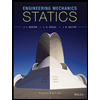
Engineering Mechanics: Statics
Mechanical Engineering
ISBN:9781118807330
Author:James L. Meriam, L. G. Kraige, J. N. Bolton
Publisher:WILEY
Related Questions
- What is relation between product tolerance (engineering tolerance) and process variation.? Explain in some details showing some representation. Analyze the following study in terms: Components of variations and their contributions X Chart and R Chartarrow_forwardThe sales of a product during the last four years were 860, 880, 870 and 890 units. The forecast for the fourth year was 876 units. If the forecast for the fifth year, using simple exponential smoothing, is equal to the forecast using a three period moving average, what is the value of the exponential smoothing constant?arrow_forwardA company uses exponential smoothing with trend toforecast monthly sales of its product, which show a trend pattern.At the end of week 5, the company wants to forecast sales for week6. Th e trend through week 4 has been 20 additional cases sold perweek. Average sales have been 85 cases per week. The demand forweek 5 was 90 cases. Th e company uses α = 0.20 and β = 0.10.Make a forecast including trend for week 6arrow_forward
- The data shown in Table 1 are the deviations from nominal diameter for holes drilled in a carbon-fiber composite material used in aerospace manufacturing. The values reported are deviations from nominal in ten-thousandths of an inch. (a) Set up and R charts on the process. Is the process in statistical control? (b) Estimate the process standard deviation using the range method. (c) If specifications are at nominal ±100, what can you say about the capability of this process? Calculate the PCR Cp Table 1. Hole Diameter Data Sample Number X1 X2 1 2 3 4 5 6 7 8 9 10 11 12 14 15 16 17 18 19 20 -30 +50 0 -50 -10 -10 +20 -40 0 0 -30 0 +20 0 0 +70 0 +10 +40 +30 +30 +30 +10 0 +20 +50 +50 -20 +50 -60 +10 0 0 +20 +10 -20 -10 0 +20 X3 X4 X5 -30 +20 +30 +50 +40 +20 +30 +20 +30 +20 +30 0 +20 +10 +40 +10 +10 -10 +50 -10 -30 -10 +50 +40 0 +30 -10 0 +30 +30 -20 +50 +30 +10 +40 +20 0 +30 +10 +30 -20 +30 +30 +20 -20 +50 +20 +10 -40 +20 -20 -10 -10 0 -20 +10 +10 +50 0 +10arrow_forwardGiven the cost function C(x) and the revenue function R(x), find the number of units x that must be sold to break even. C(x) = 14x + 56,000 and R(x) = 18x. How many units must be produced and sold in order to break even? units Help me solve this View an example Get more help - Clear aarrow_forwardWhat is the relation between product tolerance and product variation?arrow_forward
- Question 4 What is relation between product tolerance (engineering tolerance) and process variation.? Explain in some details showing some representation. Analyze the following study in terms: Components of variations and their contributions X Chart and R Chart 3. Calculate the process capability (show your method). Is it acceptable? Comment on this result.arrow_forwardPlease show all your work neatly including finding the correct units. for : A% = 40+51, so A =91% for : P_LA=B hPa. B= 0+1012, so B = 1012 for : P_denver=C hPa. C=3+838, so C =841arrow_forwardproduction planning and control help pleasearrow_forward
- True, False or Uncertain. Explain your answer. Own wage elasticity JELLlincrease if product demand elasticity n? is high. In short run, when there is an increase in wage rate, each firm will hire less labor and so the industry labor demand is simply the horizontal summation of firm's labor demand. а. b. Labor demand is represented by the marginal revenue produce schedule (MRP) when we have competitive product market while it will be represented by the value of marginal product schedule (VMP) when we have a product market monopolist. When elasticity of substitution, SLK, increase that means the L and K are less substitutable, and the isoquant will be L-shaped. Minimum wage imposed by the government is always bad for the economy because it increase unemployment and deadweight loss. с. d. e. 3.arrow_forward8. Why do experiments have a control group as part of the design? to see if the treatment (changing the independent variable) has any effect to use as a backup, In case the experiment fails the first time O to help the scientists determine which varlable is the dependent variable to minimize the number of varlables in the experimentarrow_forwardA process is in statistical control with and ?= 39.7. The control chart uses a sample size of n = 2. Specifications are at 40 ± 5. The quality characteristic is normally distributed. How much improvement could be made in process performance if the mean could be centered at the nominal value?arrow_forward
arrow_back_ios
SEE MORE QUESTIONS
arrow_forward_ios
Recommended textbooks for you
- Elements Of ElectromagneticsMechanical EngineeringISBN:9780190698614Author:Sadiku, Matthew N. O.Publisher:Oxford University PressMechanics of Materials (10th Edition)Mechanical EngineeringISBN:9780134319650Author:Russell C. HibbelerPublisher:PEARSONThermodynamics: An Engineering ApproachMechanical EngineeringISBN:9781259822674Author:Yunus A. Cengel Dr., Michael A. BolesPublisher:McGraw-Hill Education
- Control Systems EngineeringMechanical EngineeringISBN:9781118170519Author:Norman S. NisePublisher:WILEYMechanics of Materials (MindTap Course List)Mechanical EngineeringISBN:9781337093347Author:Barry J. Goodno, James M. GerePublisher:Cengage LearningEngineering Mechanics: StaticsMechanical EngineeringISBN:9781118807330Author:James L. Meriam, L. G. Kraige, J. N. BoltonPublisher:WILEY
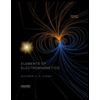
Elements Of Electromagnetics
Mechanical Engineering
ISBN:9780190698614
Author:Sadiku, Matthew N. O.
Publisher:Oxford University Press
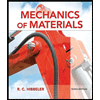
Mechanics of Materials (10th Edition)
Mechanical Engineering
ISBN:9780134319650
Author:Russell C. Hibbeler
Publisher:PEARSON
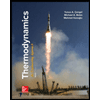
Thermodynamics: An Engineering Approach
Mechanical Engineering
ISBN:9781259822674
Author:Yunus A. Cengel Dr., Michael A. Boles
Publisher:McGraw-Hill Education
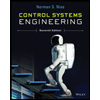
Control Systems Engineering
Mechanical Engineering
ISBN:9781118170519
Author:Norman S. Nise
Publisher:WILEY
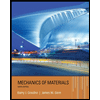
Mechanics of Materials (MindTap Course List)
Mechanical Engineering
ISBN:9781337093347
Author:Barry J. Goodno, James M. Gere
Publisher:Cengage Learning
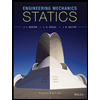
Engineering Mechanics: Statics
Mechanical Engineering
ISBN:9781118807330
Author:James L. Meriam, L. G. Kraige, J. N. Bolton
Publisher:WILEY