Sample_Group_Lab_Report
docx
School
Pennsylvania State University *
*We aren’t endorsed by this school
Course
337
Subject
Mechanical Engineering
Date
Jan 9, 2024
Type
docx
Pages
14
Uploaded by KidMetal1279
Exercise 10: Direct Shear Test
CE 337, Section 13, Team 5
Experimental data acquired on April 28
th
, 2009 by:
Jane Doe (Role: A – Team Leader)
John Doe (Role: B)
Jonathan Doe (Role: B)
Submittal Date: May 5
th
, 2009
The Pennsylvania State University
Department of Civil and Environmental Engineering
ABSTRACT
The objective of the laboratory exercise presented in this report was to determine the shear
strength – cohesion and internal friction angle – of a dry sand specimen in terms of total stress
and to observe the specimen contraction and expansion during shearing. The test was performed
using a standard direct shear apparatus consisting of a manual loading yoke for applying normal
force to the specimen, a proving ring to measure the soil specimen’s resistance to shear, and
manual dial gages for measuring the deflection of the proving ring, displacement of the shear
box, and vertical expansion of the specimen. Displacement of the shear box was driven by the
apparatus’ internal motor and occurred at a constant rate (i.e. the test was strain-controlled).
Upon analysis of the experimental data, it was discovered that an error was made during testing.
This error led to invalid results and as a consequence, the soil sample’s shear strength properties
were unable to be determined. However, this testing error did not affect the volume change
results, which indicated that the soil specimens were densely compacted.
TABLE OF CONTENTS
Page
ABSTRACT
...........................................................................................................
ii
TABLE OF CONTENTS
.......................................................................................
iii
LIST OF TABLES
.................................................................................................
iv
LIST OF FIGURES
.................................................................................................
v
INTRODUCTION
...................................................................................................
1
RESULTS AND DISCUSSION
..............................................................................
2
CONCLUSIONS
.....................................................................................................
7
REFERENCES
........................................................................................................
8
APPENDIX A: RAW DATA
...................................................................................
9
Your preview ends here
Eager to read complete document? Join bartleby learn and gain access to the full version
- Access to all documents
- Unlimited textbook solutions
- 24/7 expert homework help
LIST OF TABLES
Page
Table 1 Determination of Normal Stress on Soil Specimens During Testing
.....................
2
Table 2 Direct Shear Experimental Data for Specimen 1 – Normal Load = 2.5 psi
...........
2
Table 3 Direct Shear Experimental Data for Specimen 2 – Normal Load = 5 psi
..............
3
Table 4 Direct Shear Experimental Data for Specimen 3 – Normal Load = 10 psi
............
4
Table 5 Typical Values of Drained Angle of Friction for Sand and Silts (after Das 2006)
.............................................................................................................................
5
LIST OF FIGURES
Page
Figure 1 Shear stress vs. displacement for each specimen
.................................................
5
Figure 2 Mohr-Coulomb failure envelope for tested soil
...................................................
6
Figure 3 Contraction and expansion of each specimen during shearing
.............................
6
INTRODUCTION
The shear strength properties of soil, typically defined in terms of the soil’s cohesion (c) and
internal angle of friction (
), represent the soil’s per-unit-area ability to resist sliding along a
ϕ
plane within the soil mass. Quantification of these strength properties and a thorough
understanding of their nature are essential in the design of stable earth structures such as
foundations, slopes, and earth-retaining structures. The test is performed according to ASTM D
3080-04. The test method consists of placing a soil specimen in the direct shear device (Figure
1), applying a pre-determined normal stress, and shearing the specimen at a constant strain rate.
At a given normal stress, the shear strength, which is the maximum shear resistance can be
obtained. The shear strengths (τ) are plotted against the normal stress (σ) to obtain the Mohr-
Coulomb failure envelope, which is assumed to be linear (Figure 2).
Figure 1: Picture (left) and schematics of direct shear test setup
Figure 2: Typical results obtained from direct shear test
Your preview ends here
Eager to read complete document? Join bartleby learn and gain access to the full version
- Access to all documents
- Unlimited textbook solutions
- 24/7 expert homework help
RESULTS AND DISCUSSION
Table 1 presents the measurements and calculated values used to determine the normal stress on
each of the three specimens.
Table 1 Determination of Normal Stress on Soil Specimens During Testing
Property
Specimen
1
2
3
Cross-sectional area, A (in
2
)
4.3
4.3
4.3
Normal load (lb)
44
88
132
Normal stress (psi)
10
20
30
Table 2 through Table 4 present the experimental data acquired during the direct shear testing of
the three specimens as well as the calculated shear stress.
Table 2 Direct Shear Experimental Data for Specimen 1 – Normal Load = 2.5 psi
Horizontal
Displacement
(in)
Vertical
Displacement
(in)
Proving Ring
Dial Gauge
Reading, L (in)
Shear Force,
T = 199.71L + 2.5562 (lb)
(L in mm)
Shear Stress,
τ = T/A (psi)
0.0000
0.0000
0.0000
2.6
0.6
0.0198
-0.0009
0.0004
4.5
1.1
0.0396
-0.0016
0.0004
4.5
1.1
0.0594
-0.0022
0.0005
5.0
1.2
0.0792
-0.0027
0.0008
6.8
1.6
0.0991
-0.0040
0.0023
14.1
3.3
0.1189
-0.0082
0.0034
20.1
4.7
0.1387
-0.0111
0.0047
26.5
6.2
0.1585
-0.0126
0.0059
32.7
7.6
0.1783
-0.0133
0.0073
40.0
9.3
0.1981
-0.0128
0.0085
46.3
10.8
0.2179
-0.0111
0.0096
51.5
12.0
0.2377
-0.0092
0.0101
54.5
12.7
0.2576
-0.0083
0.0107
57.3
13.4
0.2774
-0.0079
0.0109
58.6
13.7
0.2972
-0.0075
0.0112
59.7
13.9
0.3170
-0.0066
0.0105
56.3
13.1
0.3368
-0.0051
0.0102
54.8
12.8
0.3566
-0.0031
0.0100
53.8
12.6
0.3764
-0.0017
0.0099
53.1
12.4
0.3962
-0.0012
0.0094
50.5
11.8
Table 3 Direct Shear Experimental Data for Specimen 2 – Normal Load = 5 psi
Horizontal
Displacement
(in)
Vertical
Displacement
(in)
Proving Ring
Dial Gauge
Reading, L (in)
Shear Force
T = 199.71L + 2.5562 (lb)
(L in mm)
Shear Stress
τ = T/A (psi)
0.0000
0.0000
0.0000
2.6
0.6
0.0198
0.0000
0.0005
5.0
1.2
0.0396
0.0000
0.0005
5.0
1.2
0.0594
0.0000
0.0008
6.6
1.5
0.0792
-0.0002
0.0012
8.5
2.0
0.0991
-0.0005
0.0037
21.3
5.0
0.1189
-0.0037
0.0069
38.1
8.9
0.1387
-0.0063
0.0102
54.9
12.8
0.1585
-0.0071
0.0127
67.7
15.8
0.1783
-0.0072
0.0144
76.4
17.8
0.1981
-0.0066
0.0161
85.2
19.9
0.2179
-0.0049
0.0172
90.4
21.1
0.2377
-0.0034
0.0186
98.0
22.9
0.2576
-0.0018
0.0194
102.0
23.8
0.2774
0.0004
0.0197
103.6
24.2
0.2972
0.0024
0.0200
104.8
24.4
0.3170
0.0046
0.0195
102.4
23.9
0.3368
0.0061
0.0187
98.4
23.0
0.3566
0.0066
0.0179
94.0
21.9
0.3764
0.0067
0.0169
89.2
20.8
Table 4 Direct Shear Experimental Data for Specimen 3 – Normal Load = 10 psi
Horizontal
Displacement
(in)
Vertical
Displacement
(in)
Proving Ring
Dial Gauge
Reading, L (in)
Shear Force,
T = 199.71L + 2.5562 (lb)
(L in mm)
Shear Stress,
τ = T/A (psi)
0.0000
0.0000
0.0000
2.6
0.6
0.0198
-0.0009
0.0039
22.7
5.3
0.0396
-0.0015
0.0039
22.7
5.3
0.0594
-0.0017
0.0039
22.7
5.3
0.0792
-0.0021
0.0044
24.9
5.8
0.0991
-0.0024
0.0050
28.1
6.6
0.1189
-0.0037
0.0125
66.5
15.5
0.1387
-0.0046
0.0176
92.8
21.7
0.1585
-0.0053
0.0226
118.4
27.6
0.1783
-0.0052
0.0262
136.8
31.9
0.1981
-0.0049
0.0296
154.3
36.0
0.2179
-0.0042
0.0322
167.5
39.1
0.2377
-0.0034
0.0338
175.5
40.9
0.2576
-0.0017
0.0344
178.7
41.7
0.2774
-0.0005
0.0340
176.7
41.2
0.2972
0.0003
0.0330
171.5
40.0
0.3170
0.0009
0.0304
158.3
36.9
0.3368
0.0012
0.0282
146.7
34.2
0.3566
0.0012
0.0275
143.2
33.4
0.3764
0.0015
0.0262
136.8
31.9
From this experimental data, Figure 3 was created to show the relationship between the shear
stress (the specimen’s resistance to shearing) and displacement during shearing for each
specimen. The peak value represents the specimen’s shear strength and can be taken from the
plots or directly from the experimental data. When plotted against the corresponding normal
stress, three failure points are generated as in Figure 4. A best-fit line is applied to these points
(shown in Figure 4) and compared with Equation 1 to determine the soil’s cohesion and internal
angle of friction. The resulting value of internal angle of friction (54
) far exceeds the expected
values for any of the materials outlined in Table 5 from Das (2006).
Your preview ends here
Eager to read complete document? Join bartleby learn and gain access to the full version
- Access to all documents
- Unlimited textbook solutions
- 24/7 expert homework help
Table 5 Typical Values of Drained Angle of Friction for Sand and Silts (after Das 2006)
Soil Type
φ
(deg)
Sand: Rounded grains
Loose
27-30
Medium
30-35
Dense
35-38
Sand: Angular grains
Loose
30-35
Medium
35-40
Dense
40-45
Gravel with some sand
34-48
Silts
26-35
Upon further investigation after making this observation, the authors discovered that the data
acquired from the proving ring were erroneous. When the machine is in operation, the proving
ring can be subjected to either compressive or tensile forces, depending on the direction of
displacement of the shear box. Correct usage of the equipment requires that the proving ring be
compressed. However, in the experiment presented here, data was acquired while the proving
ring was in tension. This error essentially invalidates all results aside from the
contraction/dilation data, which does not rely on the direction of shear. Figure 3 Shear stress vs. displacement for each specimen.
0
10
20
30
40
50
0.00
0.05
0.10
0.15
0.20
0.25
0.30
0.35
0.40
Shearstress(psi)
Horizontaldisplacement(in)
Normal stress = 10 psi
Normal stress = 20 psi
Normal stress = 30 psi
41.7
24.4
13.9
10, 13.9
20, 24.4
30, 41.7
y = 1.39x - 1.1333
0
5
10
15
20
25
30
35
40
45
0
5
10
15
20
25
30
35
Shearstress,τ(psi)
Normalstress,σ(psi)
Figure 4 Mohr-Coulomb failure envelope for tested soil.
Despite the experimental error just described, the variation in specimen volume caused by
particle rearrangement during shearing is still valid. Figure 5 presents this behavior for each
specimen, and was generated from the data in Table 2 through Table 4. The initial contraction
followed by expansion exhibited by each specimen indicates each was densely compacted.
-0.015
-0.010
-0.005
0.000
0.005
0.010
0.00
0.05
0.10
0.15
0.20
0.25
0.30
0.35
0.40
Ver
caldisplacement(in)
Horizontaldisplacement(in)
Normal stress = 10 psi
Normal stress = 20 psi
Normal stress = 30 psi
Figure 5 Contraction and expansion of each specimen during shearing.
CONCLUSIONS The main objectives of this exercise were to determine the shear strength properties – cohesion
and internal angle of friction – for a soil sample. A secondary objective was to observe volume
change behavior during shearing. Each objective was pursued via standard direct shear testing.
Upon analysis of the experimental data, it was discovered that an error was made during testing.
This error led to invalid results and as a consequence, the soil sample’s shear strength properties
were unable to be determined. However, this testing error did not affect the volume change
results, which indicated that the soil specimens were densely compacted. In the future, the
authors suggest that tests performed using the correct mode of shearing (i.e. with the proving
ring in compression).
Your preview ends here
Eager to read complete document? Join bartleby learn and gain access to the full version
- Access to all documents
- Unlimited textbook solutions
- 24/7 expert homework help
REFERENCES
Das, B. M. (2006). “Shear Strength of Soil.” Principles of Geotechnical Engineering, Sixth
Edition
, Thomson Learning, Toronto, Ontario, Canada
APPENDIX A: RAW DATA
Raw data was collected electronically during testing (i.e. no hand-written data sheets exist) and
was presented in Table 1 through Table 4.
Related Documents
Related Questions
Please check if it’s correct
arrow_forward
Please don't provide handwitten solution ....
arrow_forward
As the tempering temperature of a heat-treated steel increases, the associated values of Brinell hardness also increases, while the values of tensile strength and yield strength decrease.
True
False
The correct definition of Dimensional Analysis is:
A procedure to find the yield point of a material when no definitive yield point can be determined graphically.
A procedure to calculate the Elastic Modulus.
A procedure to verify the size of a mass of material.
A methodical process of converting from one set of units to another set of units.
arrow_forward
i need the answer quickly
arrow_forward
10. Measure the diameter of impression using the profile projector and compute for the
hardness number using the formula:
Where:
2P
P – Applied Load
D - Diameter of steel ball (8.0 mm)
BHN
«D(D- /D²
– d²
d - Ave. diameter of indentation
|
Raw data:
Diameter
Specimen (carbon steel)
d1
d2
Air cooled
5.13
5.22
Oil quenched
Water quenched
4.12
4.36
3.74
3.81
Note: All dimensions are in mm.
arrow_forward
Please help with all, and desbribe how the table is used, thank you in advance! Will give thumbs up
arrow_forward
Submit correct and complete solutions.
Please provide Explanation.
Provide step-by-step detailed explanations.
arrow_forward
Don’t use ai pls
arrow_forward
Note:-
• Do not provide handwritten solution. Maintain accuracy and quality in your answer. Take care of plagiarism.
• Answer completely.
• You will get up vote for sure.
arrow_forward
Note:
Please provide a clear, step-by-step simplified handwritten working out (no explanations!), ensuring it is done without any AI involvement. I require an expert-level answer, and I will assess and rate based on the quality and accuracy of your work and refer to the provided image for more clarity. Make sure to double-check everything for correctness before submitting appreciate your time and effort!.
Question:
arrow_forward
Question 8. The following figure represents three hardness-testing techniques of materials.
Describe their specifications, how there are conducted and their potential applications?
8 -
Shape of Indentation
Test
Indenter
Side View
Top View
Load
Brinell
10-mm sphere
P
of steel or
tungsten carbide
Vickers
Diamond
136°
microhardness
ругamid
Rockwell and
60 kg)
100 kg } Rockwell
150 kg)
Diamond
120°
superficial
cone:
s - in.-
diameter
Rockwell
15 kg
30 kg } Superficial Rockwell
45 kg)
steel spheres
arrow_forward
Viscosity (Pa-s)
400
1016
1014
1012
1010
108
105
104
10²
1
200
800
Borosilicate
glass
Temperature (°F)
1200 1600 2000
96% silica
glass
Working range
Melting point
400 600
Fused
silica
2400 2800 3:200
Strain point
Annealing point
Softening point
Working point
Soda-lime glass
1018
1016
1014
1012
1010
108
106
104
10²
800 1000 1200 1400 1600 1800
Temperature (°C)
Viscosity (P)
arrow_forward
Calculate the young’s modulus from one of these two graphs?
arrow_forward
Pls don’t use ai and fast :)
arrow_forward
Question 4
You do a series of tensile tests on plates of a magnesium alloy that have been subjected to prior cold rolling to true plastic strains of 0.1, 0.2 and 0.3. The resulting true stress-true strain curves are shown below (including a zoomed in version expanding on the small strain region). It is reasonable to approximate the the 0.2% offset yield strength
of the magnesium as ✓ MPa for 0.1 plastic strain, ✓ MPa for 0.2 and
✓ MPa for 0.3. Assuming the yield strength is proportional to the square root of the prior true plastic strain results in a hardening coefficient of approximately k=
✓ MPa. Hence, we can predict that we need a prior plastic strain of approximately
✓to obtain a
hgth of 120 MPa
True Stress (MPa)
250
200
100
85
95
50
105
115
125
135
145
300
350
0.12
0.14
150 0.16
0.18
155
165
175
200
250
0.1
True Stress (MPa)
Ep = 0.1
Zoomed version of left plot
arrow_forward
I need answers for problems 7, 8, and 9 pertaining to the print provided.
arrow_forward
Cal. the permeability number of a sand specimen if it takes 75s to pass 2000 cm3 of air at a pressure of 6 g/cm2 through the standard sample.
arrow_forward
Please can you plot the Mohr's strain circle using the above inform
arrow_forward
SEE MORE QUESTIONS
Recommended textbooks for you
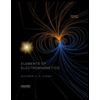
Elements Of Electromagnetics
Mechanical Engineering
ISBN:9780190698614
Author:Sadiku, Matthew N. O.
Publisher:Oxford University Press
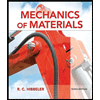
Mechanics of Materials (10th Edition)
Mechanical Engineering
ISBN:9780134319650
Author:Russell C. Hibbeler
Publisher:PEARSON
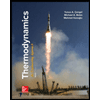
Thermodynamics: An Engineering Approach
Mechanical Engineering
ISBN:9781259822674
Author:Yunus A. Cengel Dr., Michael A. Boles
Publisher:McGraw-Hill Education
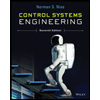
Control Systems Engineering
Mechanical Engineering
ISBN:9781118170519
Author:Norman S. Nise
Publisher:WILEY
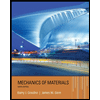
Mechanics of Materials (MindTap Course List)
Mechanical Engineering
ISBN:9781337093347
Author:Barry J. Goodno, James M. Gere
Publisher:Cengage Learning
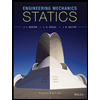
Engineering Mechanics: Statics
Mechanical Engineering
ISBN:9781118807330
Author:James L. Meriam, L. G. Kraige, J. N. Bolton
Publisher:WILEY
Related Questions
- Please check if it’s correctarrow_forwardPlease don't provide handwitten solution ....arrow_forwardAs the tempering temperature of a heat-treated steel increases, the associated values of Brinell hardness also increases, while the values of tensile strength and yield strength decrease. True False The correct definition of Dimensional Analysis is: A procedure to find the yield point of a material when no definitive yield point can be determined graphically. A procedure to calculate the Elastic Modulus. A procedure to verify the size of a mass of material. A methodical process of converting from one set of units to another set of units.arrow_forward
- i need the answer quicklyarrow_forward10. Measure the diameter of impression using the profile projector and compute for the hardness number using the formula: Where: 2P P – Applied Load D - Diameter of steel ball (8.0 mm) BHN «D(D- /D² – d² d - Ave. diameter of indentation | Raw data: Diameter Specimen (carbon steel) d1 d2 Air cooled 5.13 5.22 Oil quenched Water quenched 4.12 4.36 3.74 3.81 Note: All dimensions are in mm.arrow_forwardPlease help with all, and desbribe how the table is used, thank you in advance! Will give thumbs uparrow_forward
- Submit correct and complete solutions. Please provide Explanation. Provide step-by-step detailed explanations.arrow_forwardDon’t use ai plsarrow_forwardNote:- • Do not provide handwritten solution. Maintain accuracy and quality in your answer. Take care of plagiarism. • Answer completely. • You will get up vote for sure.arrow_forward
- Note: Please provide a clear, step-by-step simplified handwritten working out (no explanations!), ensuring it is done without any AI involvement. I require an expert-level answer, and I will assess and rate based on the quality and accuracy of your work and refer to the provided image for more clarity. Make sure to double-check everything for correctness before submitting appreciate your time and effort!. Question:arrow_forwardQuestion 8. The following figure represents three hardness-testing techniques of materials. Describe their specifications, how there are conducted and their potential applications? 8 - Shape of Indentation Test Indenter Side View Top View Load Brinell 10-mm sphere P of steel or tungsten carbide Vickers Diamond 136° microhardness ругamid Rockwell and 60 kg) 100 kg } Rockwell 150 kg) Diamond 120° superficial cone: s - in.- diameter Rockwell 15 kg 30 kg } Superficial Rockwell 45 kg) steel spheresarrow_forwardViscosity (Pa-s) 400 1016 1014 1012 1010 108 105 104 10² 1 200 800 Borosilicate glass Temperature (°F) 1200 1600 2000 96% silica glass Working range Melting point 400 600 Fused silica 2400 2800 3:200 Strain point Annealing point Softening point Working point Soda-lime glass 1018 1016 1014 1012 1010 108 106 104 10² 800 1000 1200 1400 1600 1800 Temperature (°C) Viscosity (P)arrow_forward
arrow_back_ios
SEE MORE QUESTIONS
arrow_forward_ios
Recommended textbooks for you
- Elements Of ElectromagneticsMechanical EngineeringISBN:9780190698614Author:Sadiku, Matthew N. O.Publisher:Oxford University PressMechanics of Materials (10th Edition)Mechanical EngineeringISBN:9780134319650Author:Russell C. HibbelerPublisher:PEARSONThermodynamics: An Engineering ApproachMechanical EngineeringISBN:9781259822674Author:Yunus A. Cengel Dr., Michael A. BolesPublisher:McGraw-Hill Education
- Control Systems EngineeringMechanical EngineeringISBN:9781118170519Author:Norman S. NisePublisher:WILEYMechanics of Materials (MindTap Course List)Mechanical EngineeringISBN:9781337093347Author:Barry J. Goodno, James M. GerePublisher:Cengage LearningEngineering Mechanics: StaticsMechanical EngineeringISBN:9781118807330Author:James L. Meriam, L. G. Kraige, J. N. BoltonPublisher:WILEY
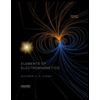
Elements Of Electromagnetics
Mechanical Engineering
ISBN:9780190698614
Author:Sadiku, Matthew N. O.
Publisher:Oxford University Press
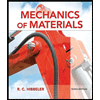
Mechanics of Materials (10th Edition)
Mechanical Engineering
ISBN:9780134319650
Author:Russell C. Hibbeler
Publisher:PEARSON
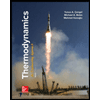
Thermodynamics: An Engineering Approach
Mechanical Engineering
ISBN:9781259822674
Author:Yunus A. Cengel Dr., Michael A. Boles
Publisher:McGraw-Hill Education
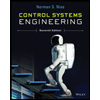
Control Systems Engineering
Mechanical Engineering
ISBN:9781118170519
Author:Norman S. Nise
Publisher:WILEY
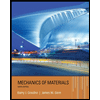
Mechanics of Materials (MindTap Course List)
Mechanical Engineering
ISBN:9781337093347
Author:Barry J. Goodno, James M. Gere
Publisher:Cengage Learning
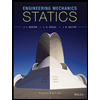
Engineering Mechanics: Statics
Mechanical Engineering
ISBN:9781118807330
Author:James L. Meriam, L. G. Kraige, J. N. Bolton
Publisher:WILEY