ME 140L Lab 7 Instruction
docx
keyboard_arrow_up
School
University of Texas *
*We aren’t endorsed by this school
Course
340
Subject
Mechanical Engineering
Date
Apr 3, 2024
Type
docx
Pages
9
Uploaded by DoctorPower13466
page
1
ME 140 L: Mechatronics Lab
Lab 7: DC Motor Characterization, Digital Encoders, and Speed Control
Required Components
permanent-magnet DC motor with digital encoder
1 x N-MOSFET P24NF10 transistor
1 x 1.8 kΩ resistor
1 x 1 μF capacitor (ceramic)
1 x 1N4002
diode
Laboratory Equipment Featured in this Lab
benchtop function generator
oscilloscope
benchtop digital multimeter
DC voltage supply
Pre-Laboratory Readings (sections 7.1 through 7.3)
7.1 Learning Objectives
To learn how to experimentally determine specific properties of DC motors, such as the resistance of the field windings, motor constant, and torque-speed curves.
To understand the relationship between input voltage, motor current, and speed of a DC motor for “no load” conditions.
To understand the relationship between the load placed on a DC motor and the current that it draws.
To understand and apply the concept of pulse-width modulation and its application in the speed control of a DC motor.
7.2 Basic Principles of DC Motors
DC motors generally contain two sets of windings, i.e., wires wrapped around core materials with high magnetic permeability. The field windings in the stator provide a magnetic field that interacts with the magnetic field generated by the armature windings on the rotor. The interaction between the poles of these magnetic fields causes the motor to spin. The figure below shows the schematic of the electrical and mechanical sides of a DC motor.
i
V
in
E
A
k
m
ω
, T
R
A
L
A
page
2
ME 140 L: Mechatronics Lab
Where:
V
in
= input voltage to the motor
i = motor current
R
A
= effective resistance of the field windings
L
A
= effective inductance of the field windings
k
m
= motor constant
E
A
= back EMF (voltage) of the motor
ω = motor speed
T
= torque (load) placed on the motor
Performing a KVL analysis of the electrical side of the motor, we have
V
L
+
V
R
+
E
A
=
V
¿
which yields the following differential equation
L
A
di
dt
+
R
A
i
+
E
A
=
V
¿
For this lab, we will be investigating the motor operating in steady-state mode, i.e., after the transient phase. During the
transient phase, the motor current increases, which energizes the inductor. Once the inductor is fully energized, the motor current reaches a constant value, i.e., the motor is operating in steady-state conditions. This means that the time rate of change of the motor current is equal to zero
di
dt
=
0
which reduces the differential equation above to an algebraic equation
R
A
i
+
E
A
=
V
¿
Note that a motor is an energy transformation device, i.e., it transforms electrical energy into mechanical energy. This energy transformation is represented by the following relationships between the back emf, motor current, motor speed,
and load torque.
E
A
=
k
m
ω
i
=
T
k
m
Qualitatively, this means that the back emf of the motor, E
A
, is proportional to the motor speed, ω
, by the proportionality constant, k
m
(motor constant). Additionally, the current drawn by the motor, i
, is proportional to the torque (load) placed on the motor by the proportionality constant, 1/
k
m
.
Substituting the first proportional relationship, E
A
=
k
m
ω
, into the algebraic equation above, results in
R
A
i
+
E
A
=
V
¿
R
A
i
+
k
m
ω
=
V
¿
Dividing both sides of the equation by the motor current, i
, yields
V
¿
i
=
k
m
ω
i
+
R
A
Thus, there is a linear relationship between V
in /
i
and ω
/
i
. If we obtain a dataset of V
in /
i
and ω
/
i
, we can graphically determine the motor constant, k
m
and the winding resistance, R
A
.
7.3 Measuring Motor Speed: Digital Rotary Encoders
page
3
ME 140 L: Mechatronics Lab
A digital rotary encoder is a device used to measure
the angular velocity of an object that is rotating
about an axis, such as the rotor of a DC motor. A
schematic of such a device is shown to the right.
The encoder consists of a disk with two sets of
concentric slits that allow light to pass through. As
the disk rotates, the number of light pulses that
reach the detector in a given period of time is
proportional to the angular velocity of the disk. If
we know the number of slits for a complete
revolution of the disk, we can calculate the angular
velocity. The encoder that you will be using in the lab has 500 slits
– once the light sensor counts 500 light pulses, that means the disk has completed one revolution. In general, we have
¿
of pulses
/
sec
❑
×
1
revolution
500
pulses
=
revolutions
sec
For example, if the light sensor detects 16,798 pulses per second, the angular velocity of the rotating object connected to the encoder is
16798
pulses
/
sec
❑
×
1
revolution
500
pulses
=
33.596
rev
sec
rev
min
We can use the oscilloscope to measure the number of pulses per second output by the encoder, i.e., the frequency, which is often measured in Hz. On the oscilloscope screen, these pulses appear as a square wave. The encoder outputs two channels of pulses, which are
slightly out of phase with each other. If the pulse train
from channel A leads the pulse train from channel B,
then the encoder is detecting a clockwise rotation, as
shown below. If the channel B leads channel A, then
the encoder is detecting a counterclockwise rotation.
light sources
light sensors
Your preview ends here
Eager to read complete document? Join bartleby learn and gain access to the full version
- Access to all documents
- Unlimited textbook solutions
- 24/7 expert homework help
page
4
ME 140 L: Mechatronics Lab
7.4 Speed Control of DC Motors Using Pulse-Width Modulation (PWM)
In section 7.2, we determined that there is a linear relationship between the input voltage, V
in , and the speed of the motor, ω
. Since the motor constant (slope of the linear relationship) is positive, as the motor input voltage, V
in , increases, the speed of the motor, ω
, increases. Varying the input voltage is easy if you have a benchtop DC power supply whose voltage can be easily adjusted. Suppose that you only have a constant voltage source available, such as a battery, which can only output a single voltage. A quick solution for varying the voltage would be to create a voltage divider using a potentiometer, but this may be impractical if the motor current is high, which would result in a large amount of power dissipation through the resistor.
A more novel approach to controlling the speed of a motor is the use of “pulse-width modulation” or PWM. This essentially involves “pulsing” the motor input voltage on and off at a high frequency such that the motor maintains a constant angular velocity. By pulsing the motor on and off, and controlling the length of the “on” portion, we control the amount of electrical power input to the motor. The portion of time the input voltage is on during a given pulsing cycle is called the “duty cycle”, as illustrated in the following figure. For more information on PWM control of DC motors, see the following references:
https://en.wikipedia.org/wiki/Pulse-width_modulation
https://www.arduino.cc/en/Tutorial/PWM
page
5
ME 140 L: Mechatronics Lab
7.5
Laboratory Procedures and Experimental Summary Sheet WARNING: During all exercises, you should not allow the motor to “draw” more than 1 A (one amp) of current. Going
above this limit may result in burnt-out circuits, etc.
Exercise 1: Measuring the motor speed using a digital encoder
(1)
Connect the motor to the DC power supply as shown below.
(2)
Connect the digital encoder to a 5V DC power supply and the outputs of the encoder to channels A and B of the oscilloscope, as shown below.
DC Power Supply
Oscilloscope
5V DC
+ Vin
GND
+ 5V
GND
Encoder
DC Motor
Channel A
Channel B
GND
page
6
ME 140 L: Mechatronics Lab
(3)
For the motor input voltages indicated in the table below, record the frequency output of the encoder (from the oscilloscope) and indicate whether the pulse train of channel A is leading or lagging the pulse train of channel B. You can
calculate the motor speed post-lab. Note that the encoder we’re using in the lab has 500 pulses per revolution.
DC motor input
voltage (V)
encoder
frequency (Hz)
motor speed, ω
rpm
channel A leading or
lagging channel B?
3
4
5
6
7
8
-3
-4
-5
-6
-7
-8
(4)
On the axes below, sketch both cases that show the pulse train of channel A leading the pulse train of channel B and the pulse train of channel A lagging the pulse train of channel B.
A
B
A
B
Your preview ends here
Eager to read complete document? Join bartleby learn and gain access to the full version
- Access to all documents
- Unlimited textbook solutions
- 24/7 expert homework help
page
7
ME 140 L: Mechatronics Lab
Exercise 2: Relationship between motor input voltage, current, and speed
(1) No-load test: Connect the DC motor to the input voltage source and construct an experimental setup in which you can monitor the motor input voltage and the motor speed for “no load” conditions. Note: we are intentionally withholding the schematic of the experimental setup – at this point in the course, you should try to figure this out yourself.
motor input voltage,
V
in
(volts)
motor current, i
,
(amps)
encoder frequency
(Hz)
motor speed, ω
(rpm)
4
6
8
10
12
14
(2) Loading the motor:
Using V
in
= 5V, and keeping it constant, touch the rotor with your finger to create a load on the motor – what do you think will change? Refer back to the equations that describe the electrical to mechanical energy transformation for the motor in Section 7.2. Record your observations using the table below.
pressure exerted on
rotor by finger
motor input voltage,
V
in
(volts)
motor current, i
,
(amps)
encoder frequency
(Hz)
motor speed, ω
(rpm)
light
medium
hard
(3) Blocked-rotor test:
Lastly, conduct a “blocked rotor” test by using a pliers to block the rotor such that it does not spin. Do this for input voltage values V
in
= 4, 6, and 8 V and measure the current drawn by the motor.
page
8
ME 140 L: Mechatronics Lab
Exercise 3: PWM speed control of a DC motor
The experimental setup for PWM control of a DC motor is shown below. A MOSFET (
M
etal–
O
xide–
S
emiconductor F
ield-
E
ffect T
ransistor), as shown in the photo, is used as a switch to turn the 12V
source voltage to the motor on and off, according to the duty cycle setting on the function
generator. This transistor is represented in the schematic by a blue circle that is labeled P24NF10,
which indicates the specific type of transistor.
Why don’t we just connect the function generator directly to the motor?
The function generator cannot provide the 12V amplitude of the on-off pulses that are needed to effectively drive the motor (the function generator can only go up to 5V.) Thus, the function generator is connected to a constant 12V source through the transistor. The function generator controls the a smaller voltage to the gate of the transistor (G terminal) which acts like a switch that turns on and off the 12V supply to the motor.
A “freewheel” or “flyback” diode (1N4002G) is connected across the motor to prevent transient voltage spikes in the inductive coils (field winding inductance) as the voltage is turned on and off according to the duty cycle set by the function generator. Build the circuit as shown, using indicated the function generator settings. Once this is set up properly, set the duty cycle for the 100 Hz, 5 Vpp square wave from the function generator (your TA will show you how to do this.) For each duty cycle indicated in the table below, record the corresponding motor speed. Start with an 80% duty cycle and go down from there.
+
-
D
G
S
page
9
ME 140 L: Mechatronics Lab
WARNING: Ensure that the MOSFET is correctly oriented and connected within the circuit. If the MOSFET begins to heat
up, something is wrong – shut off the power to the circuit and check the connections.
duty cycle V
G
(V)
voltage at
transistor gate
frequency from motor
encoder (Hz)
motor speed, ω
(rpm)
80%
70%
60%
50%
40%
30%
20%
7.5
Post-Lab Activities
(1)
For your data from exercise 1, calculate the angular velocity (along with its sign) for each of the input voltages, assuming that the encoder attached to the motor has 500 slits per revolution. Use Excel to create a plot of the input voltage vs. the motor speed.
(2)
For your data from exercise 2, plot the V
in /
i
vs. ω
/
i data and do a linear curve fit. From this curve fit, you can determine the motor constant, k
m
, and the winding resistance, R
A
, of the motor. Attach your Excel file and paste the graph into the PDF file that you submit on Canvas.
(3)
For your data from exercise 2, plot the torque-speed curves for the motor: one for each of the three voltage input values.
(4)
For your data from exercise 3, plot the motor speed vs. duty cycle and determine the nature of the functional relationship between the speed and the duty cycle. Attach your Excel file and paste the graph into the PDF file that you submit on Canvas.
Your preview ends here
Eager to read complete document? Join bartleby learn and gain access to the full version
- Access to all documents
- Unlimited textbook solutions
- 24/7 expert homework help
Related Documents
Related Questions
2.
[5 points]
(a)
Vs
(b)
R Rx
IG
contact
Ammeter
A
A potentiometer is to be used to measure the voltage Vm as shown
above.
L is the length of the potentiometer and x is the length of resistance to the contact point when the
measurement is ready to be taken.
VmRm
What conditions are required for a measurement to be taken?
Does this place the system in null or deflection mode for the measurement?
How is Vm calculated from the measured length x? Provide a mathematical expression.
No written explanation required.
arrow_forward
3.29. For each state of an n-channel enhancement-mode MOSFET that follows, determine
what operating region the MOSFET is in if the threshold voltage V, is 3 V.
a. V = 2 V, Vds=5 V
b. Vas = 4 V, Vas = 5 V
c. Vg = 6 V, V4s = 5 V
gs
с.
%3D
d. Ve = - 2.5 V
gs
arrow_forward
A
X₁
RA
P₁
X₂
P₂
2
X3
X
L
10
C
ХА
B
RB
22
Z
P₁ = 30kN; P₂ = 50kN; w= 10kN/m; L = 6m
x₁ = 1m; x₂ = 2m; x3 = 3m; x = 5m
Find RA and Rg, and draw SFD and BMD
arrow_forward
MECT361
Mechatronics Components and Instrumentation
PLEASE GIVE ME THE short answer and wite it by keyword
thanks
arrow_forward
magnitudes F₁
A scissors truss supports three forces at joints B, C, and D as shown in the figure below. The forces have
35 kip, F₂ = 10 kip, and F3 = 25 kip. The truss is held in equilibrium by a pin at point A
and a roller at point E. Note that sides ABC, CDE, AFD, and BFE are straight lines, and member CF is vertical.
Joint F lies s = 12 ft to the right and h = 4 ft above joint A, and joint C lies h = 4 ft above joint F. Use the
method of joints to determine the force in each member of the truss, and indicate whether they are in
tension or compression.
Note: Express tension forces as positive (+) and compression forces as negative (-).
=
A.
HA
B
S
F₁
F₂
2
F
C
F3
D
S
E
A
h
h
arrow_forward
The mechanism shown is a modified
Geneva drive, a constant velocity input
produces a varying velocity output with
periods of dwell. The input torque is
135NM. For the position shown, compute
the contact force at B and the magnitude
of the reaction at A. Neglect friction and
the weights of the components.
arrow_forward
1.Equivalent resisitance through entire system
2.Current being drawn from battery
3.Current flowing through R2
4.Voltage drop across R2
5.Power dissipated by R2
arrow_forward
Please Solution Step by Step
arrow_forward
Action Potentials
Graded (Locl)
Atential
All or none
Chemically or mechanically gated
Involve gated channels
Voltage gated channels
channels
Do not reach threshold
Involve K+ diffusion
Local signalling
Decreases in intensity
Change in RMP
Involve Na+ diffusion
Long distance signaling
Found in axon
Size depends on size of stimulus
Self-propagating
Found in dendrites
Has a threshold
hrane potential 0
arrow_forward
Don't Use Chat GPT Will Upvote And Give Handwritten Solution Please
arrow_forward
Subject : engineering design - DFMA
arrow_forward
I am struggling with this question
arrow_forward
3) If two forces of 10,000 N are continuously rotating 1,000,000 shafts, the ball bearings and shaft
thickness must be selected. The system should be drawn in 3D and proven to work safely. Please
note that you must determine the dimensions of the system and the shaft material and code
yourself. This question should only be answered if you are between 61 and 90 in the student list
(#61-90).
F
Bearing
☑ ☑
☑ ☑
Shaft
F
arrow_forward
What type of CAD software could be used to test the medical scaffold made out of TPU that will be printed using stereolithography (SLA). The medical scaffold will be surgically implanted around the pancreas to enable the infusion of Islet beta cells which are encapsulated within the scaffold to provide diabetic patients with a functional pancreas.
E.g. hydrostatic pressure testing/torsion tests
What other type of physical testings should be taken? E.g. Brunauer–Emmett–Teller (BET) test to check the porosity of the material
arrow_forward
3) The probe in AFM techniques is
4) Nanoscale materials are so interesting, especially in the industry sector due to
5)
and
and------
are considered one of the important metal nanoparticles that are used as vigorous
catalysts in chemical reactions.
6) The synthesis process of nanoparticles that use the liquid phase as bulk materials is process.
7) The process that uses ultrasound frequency greater than 20 kHz is known as
process.
is outside the sphere.
8) The process that depends on using atom by atom to fabricate nanoparticles are called
9) Micelles are called reverse micelles if is inside the sphere and
10) The pressure equal to 50 Torr is normally equal to ------Pa.
arrow_forward
I’m a doing a stiffness compliance matrix. E_1 is 150 GPA; what are the units of E_1 when I do 1/150e9
arrow_forward
Please help me
arrow_forward
What is the difference between OrCad and Comsol multiphysics
arrow_forward
10
arrow_forward
SEE MORE QUESTIONS
Recommended textbooks for you
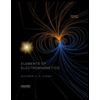
Elements Of Electromagnetics
Mechanical Engineering
ISBN:9780190698614
Author:Sadiku, Matthew N. O.
Publisher:Oxford University Press
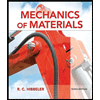
Mechanics of Materials (10th Edition)
Mechanical Engineering
ISBN:9780134319650
Author:Russell C. Hibbeler
Publisher:PEARSON
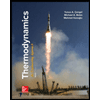
Thermodynamics: An Engineering Approach
Mechanical Engineering
ISBN:9781259822674
Author:Yunus A. Cengel Dr., Michael A. Boles
Publisher:McGraw-Hill Education
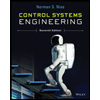
Control Systems Engineering
Mechanical Engineering
ISBN:9781118170519
Author:Norman S. Nise
Publisher:WILEY
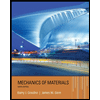
Mechanics of Materials (MindTap Course List)
Mechanical Engineering
ISBN:9781337093347
Author:Barry J. Goodno, James M. Gere
Publisher:Cengage Learning
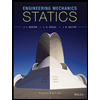
Engineering Mechanics: Statics
Mechanical Engineering
ISBN:9781118807330
Author:James L. Meriam, L. G. Kraige, J. N. Bolton
Publisher:WILEY
Related Questions
- 2. [5 points] (a) Vs (b) R Rx IG contact Ammeter A A potentiometer is to be used to measure the voltage Vm as shown above. L is the length of the potentiometer and x is the length of resistance to the contact point when the measurement is ready to be taken. VmRm What conditions are required for a measurement to be taken? Does this place the system in null or deflection mode for the measurement? How is Vm calculated from the measured length x? Provide a mathematical expression. No written explanation required.arrow_forward3.29. For each state of an n-channel enhancement-mode MOSFET that follows, determine what operating region the MOSFET is in if the threshold voltage V, is 3 V. a. V = 2 V, Vds=5 V b. Vas = 4 V, Vas = 5 V c. Vg = 6 V, V4s = 5 V gs с. %3D d. Ve = - 2.5 V gsarrow_forwardA X₁ RA P₁ X₂ P₂ 2 X3 X L 10 C ХА B RB 22 Z P₁ = 30kN; P₂ = 50kN; w= 10kN/m; L = 6m x₁ = 1m; x₂ = 2m; x3 = 3m; x = 5m Find RA and Rg, and draw SFD and BMDarrow_forward
- MECT361 Mechatronics Components and Instrumentation PLEASE GIVE ME THE short answer and wite it by keyword thanksarrow_forwardmagnitudes F₁ A scissors truss supports three forces at joints B, C, and D as shown in the figure below. The forces have 35 kip, F₂ = 10 kip, and F3 = 25 kip. The truss is held in equilibrium by a pin at point A and a roller at point E. Note that sides ABC, CDE, AFD, and BFE are straight lines, and member CF is vertical. Joint F lies s = 12 ft to the right and h = 4 ft above joint A, and joint C lies h = 4 ft above joint F. Use the method of joints to determine the force in each member of the truss, and indicate whether they are in tension or compression. Note: Express tension forces as positive (+) and compression forces as negative (-). = A. HA B S F₁ F₂ 2 F C F3 D S E A h harrow_forwardThe mechanism shown is a modified Geneva drive, a constant velocity input produces a varying velocity output with periods of dwell. The input torque is 135NM. For the position shown, compute the contact force at B and the magnitude of the reaction at A. Neglect friction and the weights of the components.arrow_forward
- 1.Equivalent resisitance through entire system 2.Current being drawn from battery 3.Current flowing through R2 4.Voltage drop across R2 5.Power dissipated by R2arrow_forwardPlease Solution Step by Steparrow_forwardAction Potentials Graded (Locl) Atential All or none Chemically or mechanically gated Involve gated channels Voltage gated channels channels Do not reach threshold Involve K+ diffusion Local signalling Decreases in intensity Change in RMP Involve Na+ diffusion Long distance signaling Found in axon Size depends on size of stimulus Self-propagating Found in dendrites Has a threshold hrane potential 0arrow_forward
arrow_back_ios
SEE MORE QUESTIONS
arrow_forward_ios
Recommended textbooks for you
- Elements Of ElectromagneticsMechanical EngineeringISBN:9780190698614Author:Sadiku, Matthew N. O.Publisher:Oxford University PressMechanics of Materials (10th Edition)Mechanical EngineeringISBN:9780134319650Author:Russell C. HibbelerPublisher:PEARSONThermodynamics: An Engineering ApproachMechanical EngineeringISBN:9781259822674Author:Yunus A. Cengel Dr., Michael A. BolesPublisher:McGraw-Hill Education
- Control Systems EngineeringMechanical EngineeringISBN:9781118170519Author:Norman S. NisePublisher:WILEYMechanics of Materials (MindTap Course List)Mechanical EngineeringISBN:9781337093347Author:Barry J. Goodno, James M. GerePublisher:Cengage LearningEngineering Mechanics: StaticsMechanical EngineeringISBN:9781118807330Author:James L. Meriam, L. G. Kraige, J. N. BoltonPublisher:WILEY
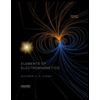
Elements Of Electromagnetics
Mechanical Engineering
ISBN:9780190698614
Author:Sadiku, Matthew N. O.
Publisher:Oxford University Press
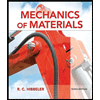
Mechanics of Materials (10th Edition)
Mechanical Engineering
ISBN:9780134319650
Author:Russell C. Hibbeler
Publisher:PEARSON
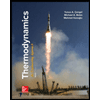
Thermodynamics: An Engineering Approach
Mechanical Engineering
ISBN:9781259822674
Author:Yunus A. Cengel Dr., Michael A. Boles
Publisher:McGraw-Hill Education
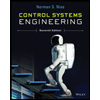
Control Systems Engineering
Mechanical Engineering
ISBN:9781118170519
Author:Norman S. Nise
Publisher:WILEY
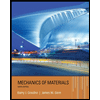
Mechanics of Materials (MindTap Course List)
Mechanical Engineering
ISBN:9781337093347
Author:Barry J. Goodno, James M. Gere
Publisher:Cengage Learning
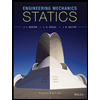
Engineering Mechanics: Statics
Mechanical Engineering
ISBN:9781118807330
Author:James L. Meriam, L. G. Kraige, J. N. Bolton
Publisher:WILEY