ACCT 406 Wk2 Q7
.pdf
keyboard_arrow_up
School
American Military University *
*We aren’t endorsed by this school
Course
406
Subject
Accounting
Date
Jun 27, 2024
Type
Pages
1
Uploaded by rentont7
v Part4 of 4 0/10 points awarded eBook References I Required information [The following information applies to the questions displayed below.] Black Diamond Company produces snowboards. Each snowboard requires 2 pounds of carbon fiber. Management reports that 5,000 snowboards and 6,000 pounds of carbon fiber are in inventory at the beginning of the third quarter, and that 150,000 snowboards are budgeted to be sold during the third quarter. Management wants to end the third quarter with 3,500 snowboards and 4,000 pounds of carbon fiber in inventory. Carbon fiber costs $15 per pound. Each snowboard requires 0.5 hour of direct labor at $20 per hour. Variable overhead is budgeted at the rate of $8 per direct labor hour. The company budgets fixed overhead of $1,782,000 for the quarter. 4. Prepare the factory overhead budget for the third quarter. [ BLACK DIAMOND COMPANY ] = Factory Overhead Budget = % Third Quarter—‘ Direct labor hours needed 74,250 ariable overhead rate per direct labor hour l o R 8 Budgeted variable overhead $ 594 000 udgeted fixed overhead | v 1,782,000 Budgeted total factory overhead $ 2,376,000
Discover more documents: Sign up today!
Unlock a world of knowledge! Explore tailored content for a richer learning experience. Here's what you'll get:
- Access to all documents
- Unlimited textbook solutions
- 24/7 expert homework help
Related Questions
Please do not give solution in image format thanku
arrow_forward
please can someone help me with working thanks answer in text not image
Greener Grass Fertilizer Company plans to sell 200,000 units of finished product in July and anticipates a growth rate in sales of 5 percent per month. The desired monthly ending inventory in units of finished product is 80 percent of the next month’s estimated sales. There were 160,000 finished units in inventory on June 30. Each unit of the finished product requires four pounds of raw material at a cost of $1.15 per pound. There are 700,000 pounds of raw material in inventory on June 30.
Compute the company’s total required production in units of finished product for the entire three-month period ending September 30.
Independent of your answer to requirement 1, assume the company plans to produce 600,000 units of finished product in the three-month period ending September 30, and to have raw-material inventory on hand at the end of the three-month period equal to 25 percent of the use in that period. Compute…
arrow_forward
Part 3 (20 minutes)
Global Colors manufactures a special line of graphic tubing items. For the next coming
year, the company estimates it will sell 150,000 units of this item. The beginning finished
goods inventory contains 40,000 units. The target for next year's ending inventory is
20,000 units.
Each unit requires 5 feet of plastic tubing. The tubing inventory currently includes
100,000 feet of the required tubing. Materials on hand are targeted to equal three month's
production. Any shortage in materials will be made up by the immediate purchase of
materials.
Required:
Compute the production target and the materials requirements for the coming period.
arrow_forward
2.
arrow_forward
lk
arrow_forward
A7
arrow_forward
Q.3.1 Gill Enterprises produces a number of consumer items, including a stove. A key
component of the stove is purchased from an outside supplier. In total, the company
purchases 2 500 components each year. It costs approximately R12 to place an order
and it costs R0.25 to carry one part in inventory for a year. The company is
operational for 50 weeks in a year.
Required:
Q.3.1.2
It takes about four weeks to receive an order of parts from the supplier.
The company normally uses 52 parts each week in production. However,
usage can be as high as 70 parts per week. Calculate the safety stock.
Calculate the reorder point with safety stock included.
arrow_forward
Please do not give solution in image format thanku
arrow_forward
Student question
MBI is a manufacturer of personal computers. All its personal computers use a 3.5-inch high-density floppy disk drive which it purchases from Ynos. MBI operates its factory 52 weeks per year, which requires assembling 100 of these floppy disk drives into computers per week. MBI’s annual holding cost rate is 20 percent of the value (based on purchase cost) of the inventory. Regardless of order size, the administrative cost of placing an order with Ynos has been estimated to be $50. A quantity discount is offered by Ynos for large orders as shown below, where the price for each category applies to every disk drive purchased.
Determine the optimal order quantity according to the EOQ model with quantity discounts. What is the resulting total cost per year?
What is the resulting total cost per year?
arrow_forward
Required information
[The following information applies to the questions displayed below.]
Black Diamond Company produces snow skis. Each ski requires 2 pounds of carbon fiber. The company's management
predicts that 5,000 skis and 6,000 pounds of carbon fiber will be in inventory on June 30 of the current year and that
150,000 skis will be sold during the next (third) quarter. A set of two skis sells for $300. Management wants to end the
third quarter with 3,500 skis and 4,000 pounds of carbon fiber in inventory. Carbon fiber can be purchased for $15 per
pound. Each ski requires 0.5 hours of direct labor at $20 per hour. Variable overhead is applied at the rate of $8 per
direct labor hour. The company budgets fixed overhead of $1,782,000 for the quarter.
4. Prepare the factory overhead budget for the third quarter.
BLACK DIAMOND COMPANY
Factory Overhead Budget
Third Quarter
Total labor hours needed
arrow_forward
Required information
[The following information applies to the questions displayed below.]
Black Diamond Company produces snow skis. Each ski requires 2 pounds of carbon fiber. The company's management
predicts that 5,000 skis and 6,000 pounds of carbon fiber will be in inventory on June 30 of the current year and that
150,000 skis will be sold during the next (third) quarter. A set of two skis sells for $300. Management wants to end the
third quarter with 3,500 skis and 4,000 pounds of carbon fiber in inventory. Carbon fiber can be purchased for $15 per
pound. Each ski requires 0.5 hours of direct labor at $20 per hour. Variable overhead is applied at the rate of $8 per
direct labor hour. The company budgets fixed overhead of $1,782,000 for the quarter.
Required:
1. Prepare the third-quarter production budget for skis.
BLACK DIAMOND COMPANY
Production Budget (in units)
Third Quarter
Required units of available production
Units to be manufactured
arrow_forward
Please do not give solution in image format thanku
arrow_forward
Please do not give solution in image format thanku
arrow_forward
Sagar
Dot's upload image please
arrow_forward
Sagar
arrow_forward
1. Question Content Area
Sales Budget
FlashKick Company manufactures and sells soccer balls for teams of children in elementary and high school. FlashKick’s best-selling lines are the practice ball line (durable soccer balls for training and practice) and the match ball line (high-performance soccer balls used in games). In the first four months of next year, FlashKick expects to sell the following:
Practice Balls
Match Balls
Units
Selling Price
Units
Selling Price
January
50,000
$8.25
7,000
$16.00
February
58,000
$8.25
8,000
$16.00
March
80,000
$8.25
13,000
$16.00
April
100,000
$8.25
18,000
$16.00
Required:
Question Content Area
1. Construct a sales budget for FlashKick for the first three months of the coming year. Show total sales for each product line by month and in total for the first quarter. If required, round your answers to the nearest cent.
FlashKick CompanySales BudgetFor the First Quarter of Next Year…
arrow_forward
Vishnu
arrow_forward
Please do not give solution in image format thanku
arrow_forward
Please do not give solution in image format thanku
arrow_forward
both image are same please pull information and answer asap thanks
arrow_forward
Please do not give solution in image format thanku
arrow_forward
Don't give answer in image format
arrow_forward
Itranscript
Required information
[The following information applies to the questions displayed below)
Iguana, Incorporated, manufactures bamboo picture frames that sell for $20 each. Each frame requires 4 linear feet of
bamboo, which costs $1.50 per foot. Each frame takes approximately 30 minutes to build, and the labor rate averages $13
per hour. Iguana has the following inventory policies
Ending finished goods inventory should be 40 percent of next month's sales.
Ending direct materials inventory should be 30 percent of next month's production.
Expected unit sales (frames) for the upcoming months follow:
.
March
April
May
June
July
August
Skip to question
325
350
400
5:00
475
525
Variable manufacturing overhead is incurred at a rate of $0.30 per unit produced. Annual fixed manufacturing overhead is
estimated to be $6.000 ($500 per month) for expected production of 5,000 units for the year. Selling and administrative
expenses are estimated at $550 per month plus $0.60 per unit sold.…
arrow_forward
Please do not give solution in image format thanku
arrow_forward
Figure 1
Mrs. Brown's Bagel Company manufactures specialty bagels. The company buys flour in
50-pound bags that cost GHS25 each. The company uses 10,000 bags per year, and usage occurs
evenly throughout the year.
The average cost to carry a 50-pound bag in inventory per year is GHS4, and the cost to place an
order is GHS10.
The company works 250 days per year.
20. Refer to Figure 1. If Brown's lead time is four working days, the average rate of usage is 40 bags
per day, and the company carries a safety stock of 20 bags, the reorder point would be
a. 180 bags.
b. 140 bags.
c. 160 bags.
d. 100 bags.
arrow_forward
Please do not give solution in image format thanku
arrow_forward
Required information
[The following information applies to the questions displayed below.]
Iguana, Incorporated, manufactures bamboo picture frames that sell for $25 each. Each frame requires 4 linear feet of
bamboo, which costs $2.00 per foot. Each frame takes approximately 30 minutes to build, and the labor rate averages $13
per hour. Iguana has the following inventory policies:
⚫ Ending finished goods inventory should be 40 percent of next month's sales.
• Ending direct materials inventory should be 30 percent of next month's production.
Expected unit sales (frames) for the upcoming months follow:
March
April
May
June
July
August
310
320
370
470
445
495
Variable manufacturing overhead is incurred at a rate of $0.50 per unit produced. Annual fixed manufacturing overhead is
estimated to be $4,800 ($400 per month) for expected production of 4,800 units for the year. Selling and administrative
expenses are estimated at $500 per month plus $0.50 per unit sold.
Iguana, Incorporated, had…
arrow_forward
second requirement fast please
arrow_forward
please need true help with all working and steps thanks
arrow_forward
FlashKick Company manufactures and sells soccer balls for teams of children in elementary and high school. FlashKick’s best-selling lines are the practice ball line (durable soccer balls for training and practice) and the match ball line (high-performance soccer balls used in games). In the first four months of next year, FlashKick expects to sell the following:
Practice Balls
Match Balls
Units
Selling Price
Units
Selling Price
January
46,000
$8.50
6,700
$17.50
February
55,000
$8.50
8,300
$17.50
March
86,000
$8.50
13,500
$17.50
April
115,000
$8.50
16,500
$17.50
FlashKick requires ending inventory of product to equal 20 percent of the next month’s unit sales. Beginning inventory in January was 9,200 practice soccer balls and 1,340 match soccer balls.
Every practice ball requires 0.7 square yard of polyvinyl chloride panels, one bladder with valve (to fill with air), and 2 ounces of glue. FlashKick’s policy is that 20 percent of the…
arrow_forward
H1.
Account
arrow_forward
Please do not give solution in image format thanku
arrow_forward
SEE MORE QUESTIONS
Recommended textbooks for you
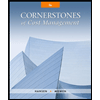
Cornerstones of Cost Management (Cornerstones Ser...
Accounting
ISBN:9781305970663
Author:Don R. Hansen, Maryanne M. Mowen
Publisher:Cengage Learning
Related Questions
- Please do not give solution in image format thankuarrow_forwardplease can someone help me with working thanks answer in text not image Greener Grass Fertilizer Company plans to sell 200,000 units of finished product in July and anticipates a growth rate in sales of 5 percent per month. The desired monthly ending inventory in units of finished product is 80 percent of the next month’s estimated sales. There were 160,000 finished units in inventory on June 30. Each unit of the finished product requires four pounds of raw material at a cost of $1.15 per pound. There are 700,000 pounds of raw material in inventory on June 30. Compute the company’s total required production in units of finished product for the entire three-month period ending September 30. Independent of your answer to requirement 1, assume the company plans to produce 600,000 units of finished product in the three-month period ending September 30, and to have raw-material inventory on hand at the end of the three-month period equal to 25 percent of the use in that period. Compute…arrow_forwardPart 3 (20 minutes) Global Colors manufactures a special line of graphic tubing items. For the next coming year, the company estimates it will sell 150,000 units of this item. The beginning finished goods inventory contains 40,000 units. The target for next year's ending inventory is 20,000 units. Each unit requires 5 feet of plastic tubing. The tubing inventory currently includes 100,000 feet of the required tubing. Materials on hand are targeted to equal three month's production. Any shortage in materials will be made up by the immediate purchase of materials. Required: Compute the production target and the materials requirements for the coming period.arrow_forward
- Q.3.1 Gill Enterprises produces a number of consumer items, including a stove. A key component of the stove is purchased from an outside supplier. In total, the company purchases 2 500 components each year. It costs approximately R12 to place an order and it costs R0.25 to carry one part in inventory for a year. The company is operational for 50 weeks in a year. Required: Q.3.1.2 It takes about four weeks to receive an order of parts from the supplier. The company normally uses 52 parts each week in production. However, usage can be as high as 70 parts per week. Calculate the safety stock. Calculate the reorder point with safety stock included.arrow_forwardPlease do not give solution in image format thankuarrow_forwardStudent question MBI is a manufacturer of personal computers. All its personal computers use a 3.5-inch high-density floppy disk drive which it purchases from Ynos. MBI operates its factory 52 weeks per year, which requires assembling 100 of these floppy disk drives into computers per week. MBI’s annual holding cost rate is 20 percent of the value (based on purchase cost) of the inventory. Regardless of order size, the administrative cost of placing an order with Ynos has been estimated to be $50. A quantity discount is offered by Ynos for large orders as shown below, where the price for each category applies to every disk drive purchased. Determine the optimal order quantity according to the EOQ model with quantity discounts. What is the resulting total cost per year? What is the resulting total cost per year?arrow_forward
- Required information [The following information applies to the questions displayed below.] Black Diamond Company produces snow skis. Each ski requires 2 pounds of carbon fiber. The company's management predicts that 5,000 skis and 6,000 pounds of carbon fiber will be in inventory on June 30 of the current year and that 150,000 skis will be sold during the next (third) quarter. A set of two skis sells for $300. Management wants to end the third quarter with 3,500 skis and 4,000 pounds of carbon fiber in inventory. Carbon fiber can be purchased for $15 per pound. Each ski requires 0.5 hours of direct labor at $20 per hour. Variable overhead is applied at the rate of $8 per direct labor hour. The company budgets fixed overhead of $1,782,000 for the quarter. 4. Prepare the factory overhead budget for the third quarter. BLACK DIAMOND COMPANY Factory Overhead Budget Third Quarter Total labor hours neededarrow_forwardRequired information [The following information applies to the questions displayed below.] Black Diamond Company produces snow skis. Each ski requires 2 pounds of carbon fiber. The company's management predicts that 5,000 skis and 6,000 pounds of carbon fiber will be in inventory on June 30 of the current year and that 150,000 skis will be sold during the next (third) quarter. A set of two skis sells for $300. Management wants to end the third quarter with 3,500 skis and 4,000 pounds of carbon fiber in inventory. Carbon fiber can be purchased for $15 per pound. Each ski requires 0.5 hours of direct labor at $20 per hour. Variable overhead is applied at the rate of $8 per direct labor hour. The company budgets fixed overhead of $1,782,000 for the quarter. Required: 1. Prepare the third-quarter production budget for skis. BLACK DIAMOND COMPANY Production Budget (in units) Third Quarter Required units of available production Units to be manufacturedarrow_forwardPlease do not give solution in image format thankuarrow_forward
arrow_back_ios
SEE MORE QUESTIONS
arrow_forward_ios
Recommended textbooks for you
- Cornerstones of Cost Management (Cornerstones Ser...AccountingISBN:9781305970663Author:Don R. Hansen, Maryanne M. MowenPublisher:Cengage Learning
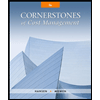
Cornerstones of Cost Management (Cornerstones Ser...
Accounting
ISBN:9781305970663
Author:Don R. Hansen, Maryanne M. Mowen
Publisher:Cengage Learning