Breathe Better (“BB”) manufactures diffusers for essential oils. Its main product is a diffuser that also functions as a night light called Moon Beam. BB uses First-in-First-out (FIFO) process costing. Moon beam units are produced in a two-step process in two departments: moulding and electrical. Plastic diffuser moulds are made in the moulding department and transferred to the electrical department at the beginning of each month. In the electrical department, all other components are added at the start of the manufacturing process. Conversion costs are incurred evenly throughout the manufacturing process. Inspection takes place when the production is 100% complete. All spoiled products are discarded. Currently normal spoilage cost is charged to COGS at the end of each month and abnormal spoilage treated as a loss. The completed diffusers that passed the inspection are transferred to storage till they are sold and shipped to customers. In the electrical department, there were 2,000 units of moon beam diffusers in the beginning work-in-process (WIP) at the beginning of April 2021. These diffusers were 60% complete. At the end of April 2021, there were 3,000 units of moon beam diffusers in WIP that were 30% complete. During April 2021, 44,000 moon beam units were started. At the end of April, 39,480 completed units of moon beam were transferred to storage. Normal spoilage is set at 3% of inspected products. The following table summarises the cost of beginning WIP and new costs incurred in electrical department for April 2021: Beginning WIP @ 1 Apr 2021 Electrical Dept. Current cost incurred for Apr 2021 Electrical Dept. Transferred in cost (TIC) $14,000 $352,000 Direct material 10,000 220,000 Conversion cost 3,600 170,800 Total $27,600 $742,800 Questions 1. Use FIFO process costing to calculate cost for completed, spoiled, end WIP units of moon beam diffusers in electrical department and cost per moon beam diffuser (nearest cent) for April 2021 (clearly show the costs per equivalent unit to the nearest 2 decimal place for each cost category). 2. Based on information for April 2021, prepare necessary journal entries to record the costs related to material, conversion costs, transferred in material, completed diffusers and abnormal loss (if any) incurred (show workings where relevant; narrations are not required).
Process Costing
Process costing is a sort of operation costing which is employed to determine the value of a product at each process or stage of producing process, applicable where goods produced from a series of continuous operations or procedure.
Job Costing
Job costing is adhesive costs of each and every job involved in the production processes. It is an accounting measure. It is a method which determines the cost of specific jobs, which are performed according to the consumer’s specifications. Job costing is possible only in businesses where the production is done as per the customer’s requirement. For example, some customers order to manufacture furniture as per their needs.
ABC Costing
Cost Accounting is a form of managerial accounting that helps the company in assessing the total variable cost so as to compute the cost of production. Cost accounting is generally used by the management so as to ensure better decision-making. In comparison to financial accounting, cost accounting has to follow a set standard ad can be used flexibly by the management as per their needs. The types of Cost Accounting include – Lean Accounting, Standard Costing, Marginal Costing and Activity Based Costing.
Breathe Better (“BB”) manufactures diffusers for essential oils. Its main product is a diffuser that also functions as a night light called Moon Beam. BB uses First-in-First-out (FIFO)
Moon beam units are produced in a two-step process in two departments: moulding and electrical. Plastic diffuser moulds are made in the moulding department and transferred to the electrical department at the beginning of each month.
In the electrical department, all other components are added at the start of the manufacturing process. Conversion costs are incurred evenly throughout the manufacturing process. Inspection takes place when the production is 100% complete. All spoiled products are discarded. Currently normal spoilage cost is charged to COGS
at the end of each month and abnormal spoilage treated as a loss. The completed diffusers that passed the inspection are transferred to storage till they are sold and shipped to customers.
In the electrical department, there were 2,000 units of moon beam diffusers in the beginning work-in-process (WIP) at the beginning of April 2021. These diffusers were 60% complete. At the end of April 2021, there were 3,000 units of moon beam diffusers in WIP that were 30% complete. During April 2021, 44,000 moon beam units were started. At the end of April, 39,480 completed units of moon beam were transferred to storage. Normal spoilage is set at 3% of inspected products. The following table summarises the cost of beginning WIP and new costs incurred in electrical department
for April 2021:
Beginning WIP @ 1 Apr 2021 Electrical Dept. |
Current cost incurred for Apr 2021 Electrical Dept. |
|
Transferred in cost (TIC) | $14,000 | $352,000 |
Direct material | 10,000 | 220,000 |
Conversion cost | 3,600 | 170,800 |
Total | $27,600 | $742,800 |
Questions
1. Use FIFO process costing to calculate cost for completed, spoiled, end WIP units of moon beam diffusers in electrical department and cost per moon beam diffuser (nearest cent) for April 2021 (clearly show the costs per equivalent unit to the nearest 2 decimal place for each cost category).
2. Based on information for April 2021, prepare necessary

Step by step
Solved in 2 steps

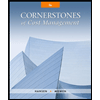
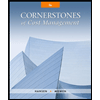