What are fabrication techniques?
Fabrication is a technique of manufacturing the desired product with the use of raw materials. It is the combination of small parts to generate a larger product.
It is the involvement of various processes for product manufacturing. There are different fabrication techniques, namely shearing, punching, fastening, welding, machining, and many more.
What are the types of fabrication techniques?
Some of the fabrication techniques include welding, metal stamping, sheet metal fabrication, etc.
The fabrication processes are listed below:
Welding
In this technique, two parts like metal sheets will be combined by applying heat and pressure, and then two metals will be fabricated together after cooling. The joining of two pieces takes place through this process.
Types of welding process
Solid state
- Cold welding like pressure, explosion, ultrasonic weldings
- Friction welding
- Forge welding
- Diffusion welding
Liquid state
- Arc welding like flux cored, shielded gas like tungsten inert gas, metal inert gas, plasma arc welding, submerged arc welding.
- Resistance welding like spot, seam, projection welding.
- Chemical reaction welding like gas and thermit welding.
Solid or liquid welding
- Soldering
- Brazing
The welding can be shown as,
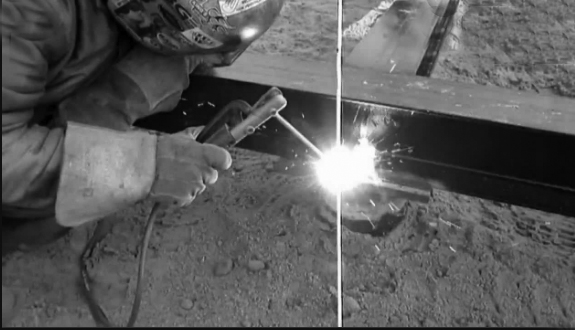
Metal Stamping
It includes various processes like punching, coining, blanking, etc. It is similar to the pressing process. It usually transforms sheet metals into different forms with the help of a stamping press. Stamping is a complex type of process which consists of various techniques like blanking, bending, piercing, punching, etc.
Cutting
In this process, the product is usually cut into small pieces. This step is common in most of the fabrication processes. Various cutting machines like die-cutting machines, drill machines, CNC machines, etc. Many cutting tools like hobber, grinding wheel, reamer, planar, shaper, drilling tool, etc.
CNC machining
It is the computer numerical control. In this machining, the pre-programmed software is used for the movement of various tools and machines. The CNC machines run the program for the processes like drilling, milling, grinding etc. There are many CNC machines like lathe machines, electric discharge machines, water jet cutters etc.
Shearing
In this process, the unwanted part of the workpiece is removed. The workpiece is held between two blades for the introduction of a straight cut. The basic types of shearing fabrication techniques are blanking, punching, trimming etc. Shearing tools like electric shears.
Sheet metal fabrication processes
It is a process of forming different metal structures with the help of other manufacturing techniques. The technique includes cutting, welding, stretching, shrinking, finishing. It is process in which the flat sheet metal (steel) are fabricated into large metal structures. The various processes performed on the sheet metal like cutting, bending, punching and assembling.
Rolling
The rolling process is a type of metal forming or fabrication process. In this process, the slabs obtained from ingots will be deformed by applying biaxial compression with the help of same sized rolls. In this type, the deformation of the slabs is due to compression as well as shear. In this process, the mechanical property of the workpiece changes.
The rolling process can be shown as,
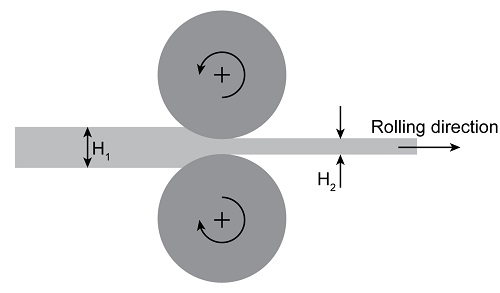
Here, is the initial thickness of the slab, is the final thickness of the slab.
The draft in the rolling process can be expressed as,
The maximum reduction in one pass can be expressed as,
Here, is the coefficient of friction, R is the radius of the roll.
The bite angle in the cold rolling process can be represented as,
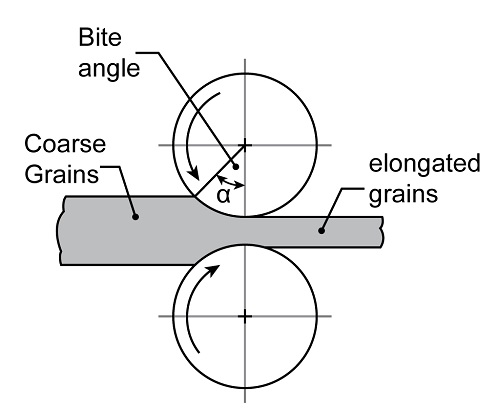
The bite angle is represented by .
The maximum bite angle can be expressed as,
Casting
In this method, the molten metal is poured into the mold cavity and then left to solidify to form a required structure. For casting any structure, various types of pattern structures can be used. The pattern structures like a solid piece, split piece pattern, loose piece pattern, gated pattern, etc. In this process, a high volume of production takes place.
Semi-finished casting products
These are the products obtained in the intermediate casting products. They are three basic types of products namely bloom, ingot, and billets.
Ingots are very large size casting products. Bloom are in rectangular-shaped structures. Billets have same cross-sectional area across their length.
The semi-finished shapes of a product can be shown as,
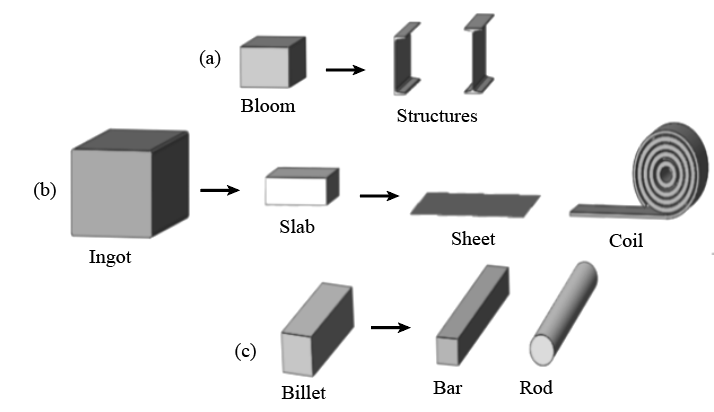
Types of Castings
There are various types of casting processes like sand molding, shell molding, investment molding, injection molding, full molding, centrifugal molding, slush molding, squeeze molding, etc.
Injection molding
Injection molding is the technique in which the plastic molten metal (molted with the help of heat) is poured into the mold and then left for cooling and then solidified it to obtain the required molded parts or the end products.
The injection molding can be shown as,
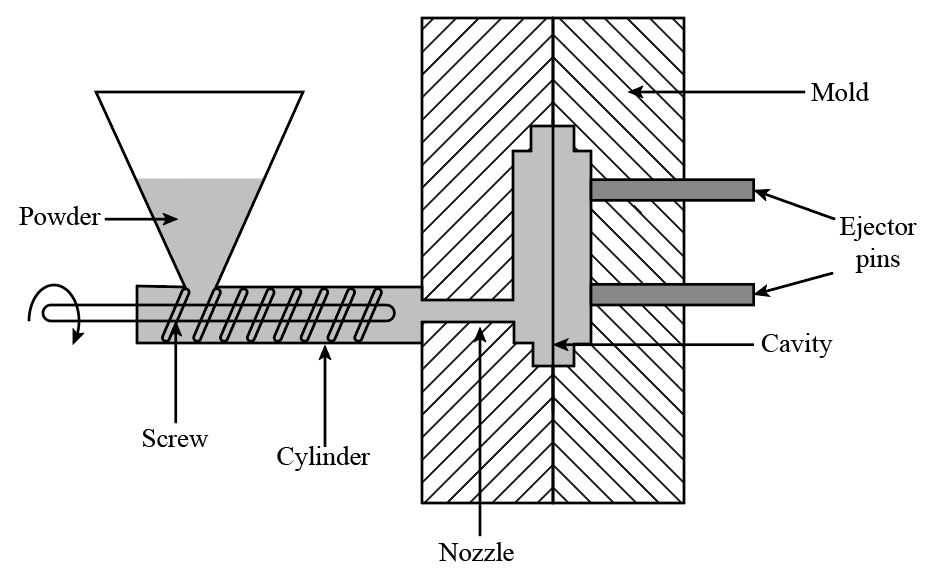
In this diagram, the cylindrical system consists of heating elements due to which the material is heated. The mould consists of a cooling system for the cooling of molten material, and then it is left for solidification into the mold and then mould is then opened, and the structure is removed with the help of ejector pins.
Common materials used in the fabrication technique
Various materials are used in the fabrication processes. Some are gold, silver, stainless steel, aluminum, copper, iron, magnesium, etc. The most commonly used metal is steel.
Stainless steel is commonly used in the fabrication process, and it involves various methods like cutting, bending to make a large structure. Stainless steel is very easy to cut, weld, and machined. These steel materials can be easily fabricated. Stainless steel has high corrosion resistance properties.
Titanium is a corrosion-resistant alloy that can be used in fabrication techniques.
Prefabrication technique
It is the practice of collecting and assembling various parts of a large structure, and then they are transported to the large structural sites. It is a type of manufacturing of smaller pieces of a large structure. These parts are transportable from one place to another. The pre-made components are manufactured and then assembled for the fabrication of the large structures.
The fabrication technique includes pre-fabricated materials like aluminum steels, concrete, steel frames, modular structures, etc.
Uses of fabrication techniques
The uses of fabrication techniques can be listed below as,
Hardware and tools
- Hand tool production
- Nut and bolt manufacturing
Construction
- Heating, ventilation and air conditioning industries
Manufacturing
- Boiler manufacturing
- Metal parts manufacturing
- Architectural structures manufacturing
- Spring manufacturing
Daily usable products
Daily usable products like fan, lamps, appliances, lamps, sinks, chairs, fasteners, pots etc.
Common Mistakes
- Students get confused that the surface finish is also a fabrication process. But actually, the surface finish comes under the machining process.
- Students sometimes get confused that the heat treatment is a fabrication process. But heat treatment processes are not fabrication processes. Heat treatment involves the improvement of metal properties.
- Students generally thought that everything could be fabricated easily. But fabrication process is restricted to limited designs of structures. These processes will not be helpful in geometrical shapes and the advanced design of structures.
- It is a misconception that fabrication results in the production of the products. Metal fabrication does not mean that the product or structure is finalized. It needed machining process, finishing, and painting process for the finalization of any structure.
- Students get confused that steel is a non-corrosive material. It will never rust easily. But the steel structures are generally susceptible to the corrosion because it forms rust while reacting with oxygen.
- Another misconception is that fabrication is a hurry or rush process, and less care is needed while operating. But fabrication process needs safety and precautions while performing the process. It takes time, and safety precautions are always required.
- Common misconception is that less care is needed in welding. But actually, proper care is needed while striking the arc in the arc welding process. Due to misplace of arc position, the metal will damage as a result.
- One of the misconceptions is that the filler material is not susceptible to corrosion. But actually, they will develop rust while interacting with moist air. And the end product will be defective.
- Students sometimes get confused that the rails can be welded with the help of friction welding. But they are welded by the thermit welding process.
Context and Applications
The topic fabrication techniques and practices is significant in several professional exams, under graduation courses, graduation, post graduation, PhD level and many more. For example:
Related Concepts
- Metal fabrication processes
- Types of Fabrication
- Fabrication methods
- Fabrication materials
- Sheet metal fabrication
- Manufacturing and fabrication
Practice Problems
Q1: Which of the following is not the type of pattern in the casting process?
- Solid piece
- Split piece
- Loose piece
- Spherical piece
Correct option: (d)
Explanation: Spherical piece type of pattern cannot be seen in the casting process.
Q2: Which of the following is correct for the metal forming process like rolling?
- Compression and tensile stress
- Axial compression
- Compression and shear
- Bi-axial compression and shear
Correct option: (c)
Explanation: In the metal forming or fabrication process of rolling, the deformation of the slabs is due to compression as well as shear.
Q3: The coefficient of friction between the roll and plate is 0.15. What is the maximum angle of bite in the metal forming process rolling?
- 8.02
- 8.53
- 9.23
- 7.50
Correct option: (b)
Explanation: The maximum bite angle in the rolling process is obtained by substituting the value of coefficient of friction between the roll and the plate in the expression for the maximum bite angle as follows:
Q4: The diameter of the copper roll is 600 mm. The friction coefficient between the roll and the steel plate is 0.13. Evaluate the maximum draft in the rolling metal forming process.
- 5.07 mm
- 6.08 mm
- 7.23 mm
- 5.59 mm
Correct option: (a)
Explanation: The expression for the maximum draft in the rolling metal forming process is given by
Q5: Which of the following varies with the variation in electrode diameter in the arc welding process?
- Arc length
- Welding speed
- Wire feed speed
- Current
Correct option: (d)
Explanation: With the variation in electrode diameter in the arc welding process, the current will vary.
Want more help with your mechanical engineering homework?
*Response times may vary by subject and question complexity. Median response time is 34 minutes for paid subscribers and may be longer for promotional offers.
Search. Solve. Succeed!
Study smarter access to millions of step-by step textbook solutions, our Q&A library, and AI powered Math Solver. Plus, you get 30 questions to ask an expert each month.
Manufacturing Engineering and Technology
Micro Manufacturing
Fabrication of Micro Electromechanical Devices
Fabricating techniques and practices Homework Questions from Fellow Students
Browse our recently answered Fabricating techniques and practices homework questions.
Search. Solve. Succeed!
Study smarter access to millions of step-by step textbook solutions, our Q&A library, and AI powered Math Solver. Plus, you get 30 questions to ask an expert each month.