What are control systems?
A control system in the field of operational management is a system that manages all the organizational resources. A few organizational resources are human resources, physical resources, and financial resources. Control systems work as a controller of all the organizations which collect the necessary information related to the resources and properly analyze the same. The control systems help any organization achieve its goal and maximize its advantages. The proper control of the management systems and the proper implementation of the strategies are responsibilities of the operations manager.
Management control
Management control is an interdisciplinary subject and an important feature of control systems. It involves extensive measurements, resource allocation, and communication. The extensive measurement is responsible for the management of accounting, and a proper contribution is required from the accounting sector. Similarly, the component of resource allocation is responsible for the economic management of a system, and a proper contribution is required from the economic sector. Communication, along with coordination and motivation is responsible for the psychological behavior of the organization, and a proper contribution is required from the organizational behavior. Therefore, for proper management, it is required that all the resources should be properly coordinated with the respective sectors and other departments.
Techniques involved in control systems
The following are some of the most important techniques involved in control systems:
- Activity-based costing
- Balanced scorecard
- Benchtrending and benchmarking
- Budgeting
- Continuous Improvement
- Lean Manufacturing
- Program management
- Target costing
- TQM
Activity-based costing
Activity-based costing (ABC) is a costing method in any organization. The ABC technique analyzes all the activities in an organization and then calculates the consumption of each activity. The ABC technique then assigns the required costs to each activity as per the requirement. The concept of activity-based costing was introduced so that the unprofitable services can be diminished from the organization and the cost of overpriced essential services can be reduced. The technique also helps for eliminating inefficient services and provides a better yield to the organization.
Balanced scorecard
A balanced scorecard is a mathematical tool used by the operations managers of an organization for the proper management of the operations system. A balanced scorecard is a performance management report prepared and used by the operations management team. A balanced scorecard is a detailed report used by the operations management department to keep an eye on all the departments and properly handle them and face the consequences if any, and provide the proper solution.
Benchtrending and benchmarking
Benchtrending is the process of continuously tracking the performances of an organization. Benchmarking is the process of comparing the business processes with their performances in the terms of quality, cost, and time. Benchtrending and benchmarking processes are the basic processes used by the operations management team of any organization to make the organization work more efficiently.
Budgeting
Budgeting is the process of preparing a detailed plan of the finances required by the organization by analyzing the past trends, present conditions, and future requirements. The budget is usually prepared for one year.
Continuous improvement
Continuous improvement is one of the most important features of any organization. For any organization to work and grow properly, continuous improvement is required in all the employees along with the processes such as logistics and purchases of an organization.
Lean manufacturing
Lean manufacturing is a technique that focuses on developing the production method of a company. The main motive of lean manufacturing is to reduce the response time from the suppliers and customers, and also decrease the design and production time of a specific product.
Program management
Program management is the key skill utilized by all industries to improve the performance of an organization. Program management includes the management of all the projects by being closely associated with all the engineering and management services.
Target costing
Target costing is the method used for determining the total cost of any product which will be adequate for the product to be fully functional and to meet the required quality. Target cost is the maximum amount that can be incurred on any project.
Total Quality Management
Total Quality Management (TQM) is also one of the important features used by the controllers of any organization for improving the ability of an organization to provide the demanded products and services to the consumers. The TQM focuses on the overall improvement and stability of an organization in all respects, which includes, sales, design, engineering, finance, and so on.
Supply Chain Management
Supply chain management is an important concept in the control system. Supply chain management is the management of the proper flow of goods and services between various services and locations. Supply chain management includes the movement and storage of both raw and finished goods from point to point. Supply chain management includes design, planning, execution, and overall control of the various activities in a supply chain. Proper management skills are required for the supply chain management. Various organizations such as Association for Supply Chain Management (APICS) are taking initiative for providing programs for increasing and advancing supply chain management. The figure below shows an example of supply chain management.
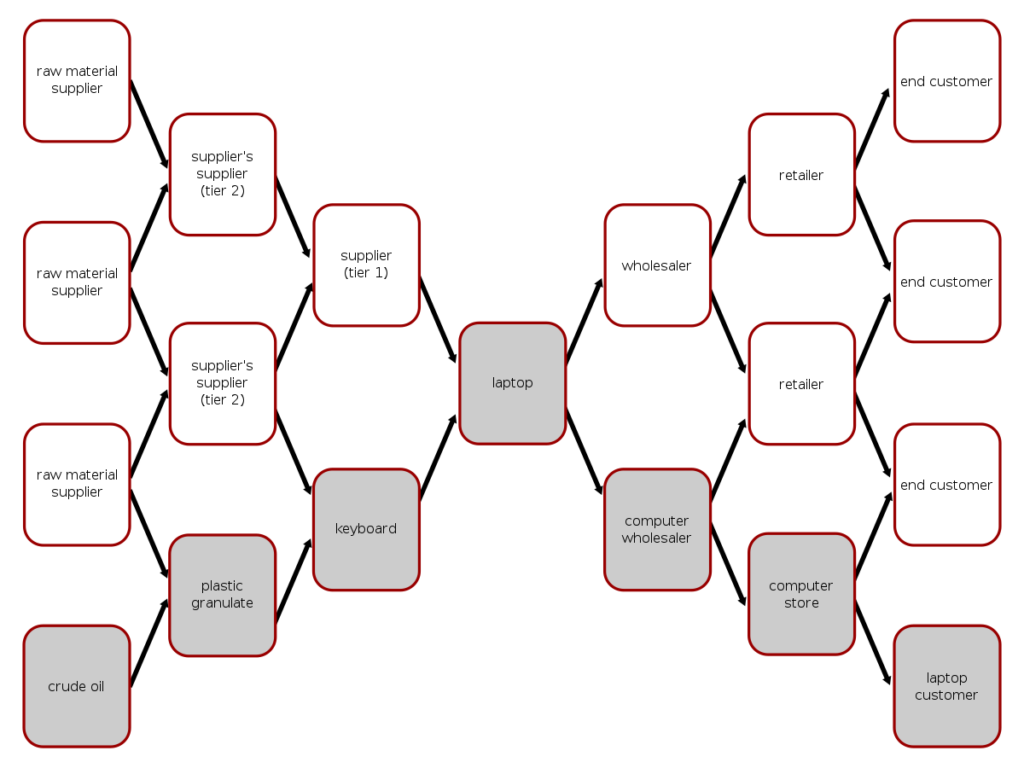
Context and Applications
The control system is used widely in industries and companies that require proper management for all the tasks. The introduction of control systems is useful for the students undergoing the following courses:
- Bachelors in Business Administration
- Master in Business Administration
- Master in Operations Management
Practice Problems
1. Which of the following technique in the control system helps for eliminating inefficient services and provides a better yield to the organization. al resources?
- Activity-based costing
- Balanced scorecard
- Benchtrending and benchmarking
- Budgeting
Answer: Option a
Explanation: The Activity-based costing technique analyzes all the activities in an organization and then calculates the consumption of each activity. It helps for eliminating inefficient services and provides a better yield to the organization. al resources.
2. Which of the following technique in the control system helps to reduce the response time from the suppliers and customers?
- Benchmarking
- Continuous improvement
- Target costing
- Lean manufacturing
Answer: Option d
Explanation: Lean manufacturing focuses on developing the production method of a company. It helps to reduce the response time from the suppliers and customers and also decreases the design and production time of a specific product.
3. Which of the following technique involved in the control system helps an organization to analyze the past trends, present conditions, and future requirements. ?
- Balanced Scorecard
- Activity-Based Costing
- Budgeting
- Target costing
Answer: Option d
Explanation: Budgeting is the process of preparing a detailed plan of the finances required by the organization by analyzing the past trends, present conditions, and future requirements.
4. Which of the following is an activity included in supply chain management?
- Movement of raw and finished goods
- Storage of raw and finished goods
- Design, planning, execution, and overall control of the various activities
- All the above
Answer: Option b
Explanation: Supply chain management includes the movement and storage of both raw and finished goods from point to point. It also includes design, planning, execution, and overall control of the various activities in a supply chain.
5. Which of the following is an organization that is taking initiative in providing programs for increasing and advancing supply chain management?
- Supervisory Control And Data Acquisition (SCADA)
- Association for Supply Chain Management (APICS)
- Detector Control System (DCS)
- Association Of Traders (AOT)
Answer: Option b
Explanation: Association for Supply Chain Management (APICS) is an organization that is taking initiative for providing programs for increasing and advancing supply chain management.
Want more help with your operations management homework?
*Response times may vary by subject and question complexity. Median response time is 34 minutes for paid subscribers and may be longer for promotional offers.
Search. Solve. Succeed!
Study smarter access to millions of step-by step textbook solutions, our Q&A library, and AI powered Math Solver. Plus, you get 30 questions to ask an expert each month.
Introduction to Control systems Homework Questions from Fellow Students
Browse our recently answered Introduction to Control systems homework questions.
Search. Solve. Succeed!
Study smarter access to millions of step-by step textbook solutions, our Q&A library, and AI powered Math Solver. Plus, you get 30 questions to ask an expert each month.