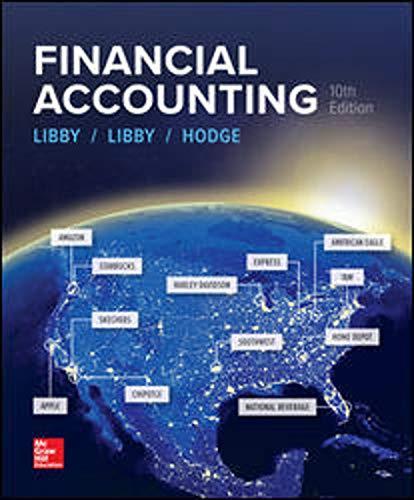
Steps in Preparing a Production Report
Recently, Stillwater Designs expanded its market by becoming an original equipment supplier to Jeep Wrangler. Stillwater Designs produces factory upgraded speakers specifically for Jeep Wrangler. The Kicker components and speaker cabinets are outsourced with assembly remaining in house. Stillwater Designs assembles the product by placing the speakers and other components in cabinets that define an audio package upgrade and that can be placed into the Jeep Wrangler, producing the desired factory-installed appearance. Speaker cabinets and associated Kicker components are added at the beginning of the assembly process.
Assume that Stillwater Designs uses the weighted average method to cost out the audio package. The following are cost and production data for the assembly process for April:
Production: | |||
Units in process, April 1, 60% complete | 60,000 | ||
Units completed and transferred out | 150,000 | ||
Units in process, April 30, 20% complete | 30,000 | ||
Costs: | |||
WIP, April 1: | |||
Cabinets | $1,200,000 | ||
Kicker components | 12,600,000 | ||
Conversion costs | 5,400,000 | ||
Costs added during April: | |||
Cabinets | $2,400,000 | ||
Kicker components | 25,200,000 | ||
Conversion costs | 8,640,000 |
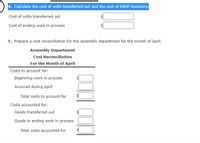
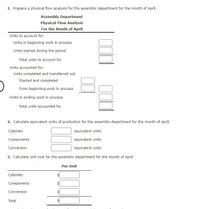

Trending nowThis is a popular solution!
Step by stepSolved in 2 steps with 1 images

- Coastal Cycles makes three models of electric bicycles: E20, E35, and E60. The models differ by the size of the battery and the quality of the components. The bicycles are produced in two departments. The Assembly Department purchases components from vendors and assembles them into bicycles. The models E20 and E35 are complete and ready for sale after completing the assembly process. The model E60 undergoes further process in Customization Department, which is actually just a small area in the same building as the Assembly Department. Conversion costs in both the Assembly Department and Customization Department are based on the number of units produced. There are never any work-in-process inventories. Data for production in November are shown in the following table. Total E20 E35 E60 Units produced 11,500 4,500 4,000 3,000 Materials cost $ 8,590,000 $ 2,250,000 $ 3,040,000 $ 3,300,000 Conversion costs Assembly…arrow_forwardVishnuarrow_forwardShow the solution in good accounting formarrow_forward
- Trivor, Inc., produces a special line of toy racing cars. Trivor produces the cars in batches. To manufacture each batch of cars, Trivor must set up the machines and molds. Setup costs are fixed batch-level costs. In the long run, number of setup-hours is the cost driver of set up costs. A separate Setup Department is responsible for setting up machines and molds for each style of car. The following information pertains to 2020: (Click the icon to view the information.) Read the requirements. Requirement a. Calculate the spending variance for fixed setup overhead costs. (Label the variance as favorable (F) or unfavorable (U).) The spending variance for fixed setup overhead costs is Requirements Calculate the following: a. The spending variance for fixed setup overhead costs b. The budgeted fixed setup overhead rate c. The production-volume variance for fixed overhead setup costs Print Done U < Data table Units produced and sold Batch size (number of units per batch) Setup-hours per…arrow_forwardNote:- Do not provide handwritten solution. Maintain accuracy and quality in your answer. Take care of plagiarism. Answer completely. You will get up vote for sure.arrow_forwardIndicate how to present and analyze liabilities and contingencies.arrow_forward
- Need explanation for (a2) and take likearrow_forwardWatertime inc. manufactures old fashioned grandfather clocks. The production utilizes a highly automated assembly line. The firm has identified two cost categories: direct materials and conversion costs. During the production process each clock moves first through the Assembly Department, where materials are added and the clock is assembled, then through the Testing Department, where the clock is inspected for quality control. All direct materials are added at the beginning of the production process but conversion costs are allocated evenly throughout production. Spartans Inc. uses weighted-average costing. Data for Department A for June 2020 are: Beginning WiP Inventory 320 units Direct Materials (100% complete) Conversion (35% complete) Units started during June 750 units Ending WiP Inventory June 30 300 units Direct…arrow_forwardB.E. Kemper, LLC (KEMPER) is a custom parts fabricator supporting the classic auto and recreational marine industries. The company is evaluating a proposal by its Marketing department to develop one-of-a-kind, customize parts for resto-mod professionals and the hobbyist in their desire for that special, unique "new" old car/truck. This approach will require the expertise of design artists and engineers working with the restorer and the need for custom programs, computer-aided design, CNC milling equipment, and both polymer & metal 3D printing equipment Market studies indicate that the restoration market is continuing to grow and is broadening to include the newer 'classic' vehicles of the '80s and '90s. The industry consists of both professional restoration shops and many talented hobbyists. The anticipated demand is incorporated in the forecasts below. Sales Forecast: The estimate of sales revenues for this project is $1,250,000 in year 1. Sales growth of 50% is forecast for year 2,…arrow_forward
- Target costs, effect of process-design changes on service costs. Solar Energy Systems (SES) sells solar heating systems in residential areas of eastern Pennsylvania. A successful sale results in the homeowner purchasing a solar heating system and obtaining rebates, tax credits, and nancing for which SES completes all the paperwork. The company has identied three major activities that drive the cost of selling heating systems: identifying new contacts (varies with the number of new contacts); traveling to and between appointments (varies with the number of miles driven); and preparing and ling rebates and tax forms (varies with the number of solar systems sold). Actual costs for each of these activities in 2016 and 2017 are:arrow_forwardNizam Company produces speaker cabinets. Recently, Nizam switched from a traditional departmental assembly line system to a manufacturing cell in order to produce the cabinets. Sup-pose that the cabinet manufacturing cell is the cost object. Assume that all or a portion of the following costs must be assigned to the cell:a. Depreciation on electric saws, sanders, and drills used to produce the cabinetsb. Power to heat and cool the plant in which the cell is locatedc. Salary of cell supervisord. Wood used to produce the cabinet housingse. Maintenance for the cell’s equipment (provided by the maintenance department)f. Labor used to cut the wood and to assemble the cabinetsg. Replacement sanding beltsh. Cost of janitorial services for the planti. Ordering costs for materials used in productionj. The salary of the industrial engineer (she spends about 20 percent of her time on work forthe cell)k. Cost of maintaining plant and grounds l. Cost of plant’s personnel officem. Depreciation on…arrow_forwardGadubhaiarrow_forward
- AccountingAccountingISBN:9781337272094Author:WARREN, Carl S., Reeve, James M., Duchac, Jonathan E.Publisher:Cengage Learning,Accounting Information SystemsAccountingISBN:9781337619202Author:Hall, James A.Publisher:Cengage Learning,
- Horngren's Cost Accounting: A Managerial Emphasis...AccountingISBN:9780134475585Author:Srikant M. Datar, Madhav V. RajanPublisher:PEARSONIntermediate AccountingAccountingISBN:9781259722660Author:J. David Spiceland, Mark W. Nelson, Wayne M ThomasPublisher:McGraw-Hill EducationFinancial and Managerial AccountingAccountingISBN:9781259726705Author:John J Wild, Ken W. Shaw, Barbara Chiappetta Fundamental Accounting PrinciplesPublisher:McGraw-Hill Education
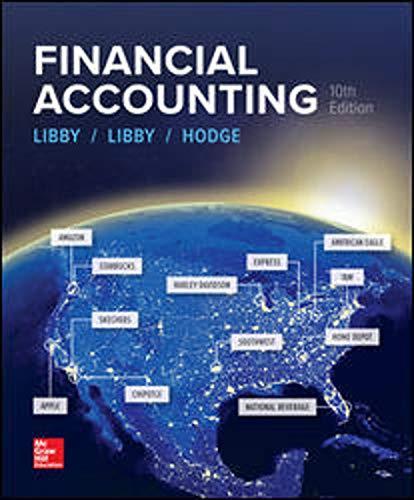
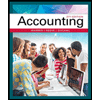
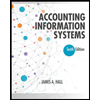
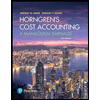
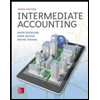
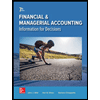