You are in charge of replacing a chiller that is used as part of a distillation process that condenses methanol (boiling point = 65 °C). Your task is to select the most economical type of system. A conventional chiller will have a lower first cost and will have lower maintenance costs than one that involves enhanced heat transfer surfaces, but the chiller with enhanced surfaces will condense the same amount of alcohol with a lower energy consumption. Select the appropriate chiller by considering the net present value of both systems. That value will involve the first cost of the chiller, and the present value of the maintenance and energy costs. Some information for the analysis: ● ● ● ● ● ● ● The chiller uses a standard vapor-compression refrigeration cycle with R-22 (see Figure 1 below). For this analysis, assume that it operates under an ideal refrigeration cycle. Electricity to run the chiller is bought by the facility at a rate of $0.11 per kWh. That rate is expected to increase at a rate of $0.0025 annually. Cycle information: o There is a sensor and controller at the inlet to the compressor that modulates the mass flow rate of refrigerant to ensure that the vapor entering the compressor is saturated. O The compressor has a flat compressor curve, meaning that the pressure increase across the compressor is insensitive to mass flow rate through it. That pressure increase is 1500 kPa. o Assume that the compressor is 90 % efficient in this operating regime. The chiller must condense methanol at a rate of 0.25 kg/s. The heat of vaporization of methanol is 1102 kJ/kg at atmospheric pressure. For any heat transfer analysis, you can assume that the methanol is at the condensation temperature (65 °C) throughout the process. The system runs 10 hours per day, 250 days per year. The chiller is projected to last 20 years, so the economic analysis should consider that time frame. Assume an inflation rate of 3 %. Maintenance costs are expected to increase at a rate of $1000 per year for each chiller. The evaporator's UA values and other characteristics of each chiller are given below (note: The "evaporator" of the chiller will actually be the component on which the alcohol will condense. "Evaporation" refers to the process for the refrigerant inside the tubes, not that outside the tubes).
You are in charge of replacing a chiller that is used as part of a distillation process that condenses methanol (boiling point = 65 °C). Your task is to select the most economical type of system. A conventional chiller will have a lower first cost and will have lower maintenance costs than one that involves enhanced heat transfer surfaces, but the chiller with enhanced surfaces will condense the same amount of alcohol with a lower energy consumption. Select the appropriate chiller by considering the net present value of both systems. That value will involve the first cost of the chiller, and the present value of the maintenance and energy costs. Some information for the analysis: ● ● ● ● ● ● ● The chiller uses a standard vapor-compression refrigeration cycle with R-22 (see Figure 1 below). For this analysis, assume that it operates under an ideal refrigeration cycle. Electricity to run the chiller is bought by the facility at a rate of $0.11 per kWh. That rate is expected to increase at a rate of $0.0025 annually. Cycle information: o There is a sensor and controller at the inlet to the compressor that modulates the mass flow rate of refrigerant to ensure that the vapor entering the compressor is saturated. O The compressor has a flat compressor curve, meaning that the pressure increase across the compressor is insensitive to mass flow rate through it. That pressure increase is 1500 kPa. o Assume that the compressor is 90 % efficient in this operating regime. The chiller must condense methanol at a rate of 0.25 kg/s. The heat of vaporization of methanol is 1102 kJ/kg at atmospheric pressure. For any heat transfer analysis, you can assume that the methanol is at the condensation temperature (65 °C) throughout the process. The system runs 10 hours per day, 250 days per year. The chiller is projected to last 20 years, so the economic analysis should consider that time frame. Assume an inflation rate of 3 %. Maintenance costs are expected to increase at a rate of $1000 per year for each chiller. The evaporator's UA values and other characteristics of each chiller are given below (note: The "evaporator" of the chiller will actually be the component on which the alcohol will condense. "Evaporation" refers to the process for the refrigerant inside the tubes, not that outside the tubes).
Elements Of Electromagnetics
7th Edition
ISBN:9780190698614
Author:Sadiku, Matthew N. O.
Publisher:Sadiku, Matthew N. O.
ChapterMA: Math Assessment
Section: Chapter Questions
Problem 1.1MA
Related questions
Question
Analyze the condensation process using both chillers. Provide operating temperatures and
pressures entering each component shown in the diagram (at points 1, 2, 3, 4). Indicate which chiller should be chosen based on the economics

Transcribed Image Text:**Title: Selecting the Most Economical Chiller for Methanol Condensation**
**Overview:**
This analysis involves replacing a chiller used in a distillation process to condense methanol (boiling point = 65 °C). The goal is to choose the most economical system based on the net present value, considering first costs, maintenance, and energy expenses. A conventional chiller typically offers lower initial and maintenance costs, while a chiller with enhanced surfaces saves energy by condensing the same amount of alcohol with reduced energy consumption.
**Key Information for Analysis:**
- **Refrigeration Cycle:**
- Uses a standard vapor-compression cycle with R-22 refrigerant.
- Assumes operation under ideal conditions.
- Electricity costs are $0.11 per kWh, increasing annually by $0.0025.
- **Cycle Details:**
- Includes a sensor and controller at the compressor inlet to maintain a saturated vapor state.
- The compressor’s pressure increase is 1500 kPa and is 90% efficient.
- **Methanol Condensation:**
- The rate of condensation is 0.25 kg/s.
- The heat of vaporization of methanol is 1102 kJ/kg.
- Assume methanol remains at condensation temperature (65 °C).
- **System Operation:**
- Operates 10 hours daily, 250 days a year.
- Expected lifespan of 20 years with a 3% inflation rate.
- **Cost Projections:**
- Maintenance costs to rise by $1000 annually for each chiller.
- **Evaporator Characteristics:**
- UA values and other features of each chiller are provided.
- The term "evaporator" refers to the refrigerant process inside tubes while alcohol condenses outside.
**Note:** This document provides specific parameters and financial projections that must be assessed to determine the most suitable chiller, weighing both short-term and long-term financial implications.
![### Chiller Overview
This section provides a comparison between two types of chillers: Conventional and Enhanced.
| Chiller | Price | Evaporator UA Value [kW/(K)] | First Year Maintenance Cost |
|----------------|-----------|-----------------------------|-----------------------------|
| Conventional | $700,000 | 10 | $10,000 |
| Enhanced | $800,000 | 20 | $11,000 |
### Refrigeration Cycle Diagram
The diagram above illustrates a simplified refrigeration cycle, which includes the following key components and stages:
1. **Evaporator**: This component absorbs heat from the environment, causing the refrigerant to evaporate.
2. **Compressor**: The gaseous refrigerant is compressed, increasing its pressure and temperature.
3. **Condenser**: The high-pressure gas releases heat to the surroundings, condensing into a high-pressure liquid.
4. **Throttling Valve**: The high-pressure liquid is expanded through this valve, decreasing its pressure and temperature, before returning to the evaporator.
Arrows indicate the direction of heat transfer and refrigerant flow, and the cycle is shown moving from the evaporator to the condenser, then through the throttling valve back to the evaporator.
### Temperature-Entropy (T-s) Diagram
Below the refrigeration cycle diagram is a Temperature-Entropy (T-s) graph representing the changes in the refrigerant during each phase of the cycle:
- **1-2**: Compression (from evaporator to the compressor), where pressure is constant.
- **2-3**: Condensation (through the condenser) at constant pressure as heat is rejected.
- **3-4**: Expansion (via the throttling valve), where enthalpy (h) is constant.
- **4-1**: Evaporation (back to the evaporator) at constant pressure as heat is absorbed.
This diagram visually depicts the thermal and mechanical processes the refrigerant undergoes through each key component of the cycle.](/v2/_next/image?url=https%3A%2F%2Fcontent.bartleby.com%2Fqna-images%2Fquestion%2Ff0e69105-edad-4e40-a986-7d2af8f1b9bd%2F0c31c0fa-66a2-450c-92f7-c1f19073aa4b%2Fy2qqbzq_processed.jpeg&w=3840&q=75)
Transcribed Image Text:### Chiller Overview
This section provides a comparison between two types of chillers: Conventional and Enhanced.
| Chiller | Price | Evaporator UA Value [kW/(K)] | First Year Maintenance Cost |
|----------------|-----------|-----------------------------|-----------------------------|
| Conventional | $700,000 | 10 | $10,000 |
| Enhanced | $800,000 | 20 | $11,000 |
### Refrigeration Cycle Diagram
The diagram above illustrates a simplified refrigeration cycle, which includes the following key components and stages:
1. **Evaporator**: This component absorbs heat from the environment, causing the refrigerant to evaporate.
2. **Compressor**: The gaseous refrigerant is compressed, increasing its pressure and temperature.
3. **Condenser**: The high-pressure gas releases heat to the surroundings, condensing into a high-pressure liquid.
4. **Throttling Valve**: The high-pressure liquid is expanded through this valve, decreasing its pressure and temperature, before returning to the evaporator.
Arrows indicate the direction of heat transfer and refrigerant flow, and the cycle is shown moving from the evaporator to the condenser, then through the throttling valve back to the evaporator.
### Temperature-Entropy (T-s) Diagram
Below the refrigeration cycle diagram is a Temperature-Entropy (T-s) graph representing the changes in the refrigerant during each phase of the cycle:
- **1-2**: Compression (from evaporator to the compressor), where pressure is constant.
- **2-3**: Condensation (through the condenser) at constant pressure as heat is rejected.
- **3-4**: Expansion (via the throttling valve), where enthalpy (h) is constant.
- **4-1**: Evaporation (back to the evaporator) at constant pressure as heat is absorbed.
This diagram visually depicts the thermal and mechanical processes the refrigerant undergoes through each key component of the cycle.
Expert Solution

This question has been solved!
Explore an expertly crafted, step-by-step solution for a thorough understanding of key concepts.
This is a popular solution!
Trending now
This is a popular solution!
Step by step
Solved in 4 steps with 16 images

Knowledge Booster
Learn more about
Need a deep-dive on the concept behind this application? Look no further. Learn more about this topic, mechanical-engineering and related others by exploring similar questions and additional content below.Recommended textbooks for you
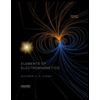
Elements Of Electromagnetics
Mechanical Engineering
ISBN:
9780190698614
Author:
Sadiku, Matthew N. O.
Publisher:
Oxford University Press
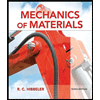
Mechanics of Materials (10th Edition)
Mechanical Engineering
ISBN:
9780134319650
Author:
Russell C. Hibbeler
Publisher:
PEARSON
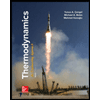
Thermodynamics: An Engineering Approach
Mechanical Engineering
ISBN:
9781259822674
Author:
Yunus A. Cengel Dr., Michael A. Boles
Publisher:
McGraw-Hill Education
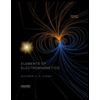
Elements Of Electromagnetics
Mechanical Engineering
ISBN:
9780190698614
Author:
Sadiku, Matthew N. O.
Publisher:
Oxford University Press
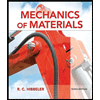
Mechanics of Materials (10th Edition)
Mechanical Engineering
ISBN:
9780134319650
Author:
Russell C. Hibbeler
Publisher:
PEARSON
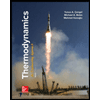
Thermodynamics: An Engineering Approach
Mechanical Engineering
ISBN:
9781259822674
Author:
Yunus A. Cengel Dr., Michael A. Boles
Publisher:
McGraw-Hill Education
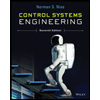
Control Systems Engineering
Mechanical Engineering
ISBN:
9781118170519
Author:
Norman S. Nise
Publisher:
WILEY
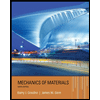
Mechanics of Materials (MindTap Course List)
Mechanical Engineering
ISBN:
9781337093347
Author:
Barry J. Goodno, James M. Gere
Publisher:
Cengage Learning
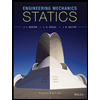
Engineering Mechanics: Statics
Mechanical Engineering
ISBN:
9781118807330
Author:
James L. Meriam, L. G. Kraige, J. N. Bolton
Publisher:
WILEY