Which total quality management principles does Toyota use
Which total

One of the fundamental TQM implementation concepts that ensure an organization's success is the dedication of business executives. In actuality, senior organizational staff members from top to lower administration exhibit a commitment to the organization. These come about as a result of employee empowerment, motivation, and self-driven goals. Within Toyota, Total Quality Management is made attainable by establishing company objectives, goals, and mission and vision statements. Additionally, TQM may be attained by actively taking part in organizational follow-up activities. These acts signify all of the tasks required and concerned with carrying out the organization's stated principles. According to research by Toyota Corporation, the organizational personnel and top management's dedication to TQM have made it successful. The TMS (Toyota Management System) customers are permitted to make twice as much as the standard production via inventory and reduce bottlenecks by half at a cost and time reduction. The Toyota Production System includes several modernisms such as strategy or kanri Hoshin usage, total value supervision, and just-in-time assembly to control the quality in all organizational management systems. Despite not having created all of these inventions, the combination of them gives Toyota a significant competitive edge. Henry Ford used a just-in-time production strategy for his innovation from 1914. From a broad viewpoint, the Ford manufacturing system calls for high volume and, consequently, quality.
Step by step
Solved in 2 steps

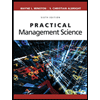
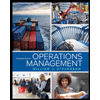
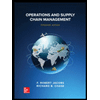
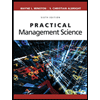
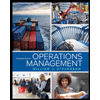
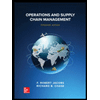
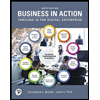
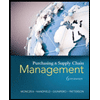
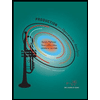