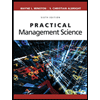
Wheeled Coach, based in Winter Park, Florida, is the world's largest manufacturer of ambulance. Working four 10 hour days each week, 350 employees make only custom-made ambulances. Virtually every vehicle is unique. Wheeled Coach accommodates the marketplace by providing a wide variety of options and an engineering staff accustomed to innovation and custom design. Continuing growth, which now requires that more than 20 ambulances roll off the assembly line each week, makes process design a continuing challenge. Wheeled Coach's response has been to build a focused factory. Wheeled Coach established work cells for every major module feeding an assembly line, including aluminum bodies, electrical wiring harnesses, interior cabinets, windows, painting, and upholstery.
Labor standards drive the
1-Based on case study wheeled coach, why do you think major auto manufacturer do not build ambulance?
2-Based on case study wheeled coach, what is the process strategy that used by Wheeled Coach?
3-Based on case study wheeled coach, wht it is moe efficient for the work cell to prepare "modules" and deliver them to the assembly line than it would be to produce the component on the line?
4-How does Wheeled Coach manage the task to be performed at each work station?

Trending nowThis is a popular solution!
Step by stepSolved in 2 steps

- 1. Practice: Identify the Associated Tasks of Each Business Operations Component Following is a list of business operations components and the associated task of each component. Read each element carefully and select the correct business operations component. 1. Utilize lean manufacturing. multiple choice 1 Business location Equipment Labor Operational processes 2. Minimize production errors. multiple choice 2 Business location Equipment Labor Operational processes 3. Train all employees on new systems. multiple choice 3 Business location Equipment Labor Operational processes 4. Monitor vendor bargaining power. multiple choice 4 Business location Equipment Labor Operational processesarrow_forwardWhat is the relationship between Value Engineering and Zero-defect approach? Can you please elaborate? don't use chatgptarrow_forwardProblem 9-17 Frandec Company manufactures, assembles, and rebuilds material handling equipment used in warehouses and distribution centers. One product, called a Liftmaster, is assembled from four components: a frame, a motor, two supports, and a metal strap. Frandec's production schedule calls for 5000 Liftmasters to be made next month. Frandec purchases the motors from an outside supplier, but the frames, supports, and straps may be either manufactured by the company or purchased from an outside supplier. Manufacturing and purchase costs per unit are shown. Component. Frame Support Strap Component Frame Support Strap Capacity (hours) Three departments are involved in the production of these components. The time (in minutes per unit) required to process each component in each department and the available capacity (in hours) for the three departments are as follows: Department Milling 2.2 1.7 SP number of supports purchased Min s.t. TM number of straps manufactured TP number of straps…arrow_forward
- Practical Management ScienceOperations ManagementISBN:9781337406659Author:WINSTON, Wayne L.Publisher:Cengage,Operations ManagementOperations ManagementISBN:9781259667473Author:William J StevensonPublisher:McGraw-Hill EducationOperations and Supply Chain Management (Mcgraw-hi...Operations ManagementISBN:9781259666100Author:F. Robert Jacobs, Richard B ChasePublisher:McGraw-Hill Education
- Purchasing and Supply Chain ManagementOperations ManagementISBN:9781285869681Author:Robert M. Monczka, Robert B. Handfield, Larry C. Giunipero, James L. PattersonPublisher:Cengage LearningProduction and Operations Analysis, Seventh Editi...Operations ManagementISBN:9781478623069Author:Steven Nahmias, Tava Lennon OlsenPublisher:Waveland Press, Inc.
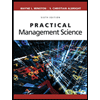
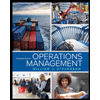
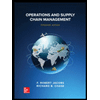
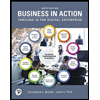
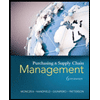
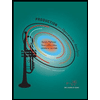