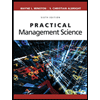
Practical Management Science
6th Edition
ISBN: 9781337406659
Author: WINSTON, Wayne L.
Publisher: Cengage,
expand_more
expand_more
format_list_bulleted
Question
A company has a factory that is designed so that it is most efficient (average unit cost is minimized) when producing 28,500 units of output each month. However, it has an absolute maximum output capability of 35,000 units per month, and can produce as little as 7,000 units per month without corporate headquarters shifting production to another plant. If the factory produces 22,120 units in October, what is the capacity utilization rate in October for this factory? (Round your answer to 1 decimal place.)
Expert Solution

This question has been solved!
Explore an expertly crafted, step-by-step solution for a thorough understanding of key concepts.
This is a popular solution
Trending nowThis is a popular solution!
Step by stepSolved in 3 steps with 1 images

Knowledge Booster
Similar questions
- Explain the figures and mention the disadvantages and advantages of the following figures based on the operation management perspective: leading demand with an incremental expansion, leading demand with one-step expansion, lagging demand with incremental expansion, attempts to have an average capacity that straddles demand with incremental expansionarrow_forwardCalculate Capacity utilization whereas: Design Capacity per hr is 11,080 Units Effective Capacity per minute is 138 Units Actual Output per min is 109 Units Daily working hrs is 12 hrs per Shift with 300 working days annuallyarrow_forwardA manager must decide between two machines. The manager will take into account each machine's operating costs and initial costs, and its breakdown and repair times. Machine A has a projected average operating time of 140 hours and a projected average repair time of 7 hours. Projected times for machine B are an average operating time of 70 hours and a repair time of 6 hours. What are the projected availabilities of each machine? (Round your answer to 3 decimal places). I don't want the answer. I just want to know HOW to do it.arrow_forward
- Please do not give solution in image format thanku Bob's candle factory is considering three different manufacturing options. Option A uses hand labor with fixed costs of $10,000 and variable costs of $2.75/candle. Option B uses a combination of hand and automation with fixed costs of $15,000 and variable costs of $1.10/candle. Option C is highly automated with fixed costs of $20,000 and variable costs of $0.75/candle. a. If demand for Bob's candles is 2500, which option should he pick, and what is the cost? b. If demand for Bob's candles is 4500 which option should he pick, and what is the cost?arrow_forwardA manufacturer of printed circuit boards has a design capacity of 1,000 boards per day. The effective capacity, however, is 693 boards per day. Recently, the production facility has been producing 964 boards per day. Compute the design and effective capacity utilization measures. (Round your answers to 1 decimal place, e.g. 3.5%.) Utilization Effective = enter utilization in percentages rounded to 1 decimal place %, Utilization Design = enter utilization in percentages rounded to 1 decimal place %arrow_forwardYou are the operations manager for Louisiana Oysters, Inc. The company has designed new "Oyster shucking" knife that is expected to reduce risk of injury to the user. Your firm plans to begin production of these knives soon. Either of two machines, A or B could be used for in-house production. Machine A would have a fixed cost of $6000 and a variable cost of $5 per knife produced, and machine B would have a fixed cost of $9600 but a variable cost of $3 per knife. Each knife is expected to sell for $15. Determine the Range of annual “Volume of Business“[Q], for which each of the two alternative machines would be optimal i.e. best. Hint: Compute various break-even points for your evaluationarrow_forward
- A manager must decide which type of machine to buy, A, B, or C. Machine costs (per individual machine) are as follows: Machine Cost $50,000 A B $40,000 C $70,000 Product forecasts and processing times on the machines are as follows: PROCCESSING TIME PER UNIT (minutes) Annual Product Demand 1 2 3 4 18,000 25,000 15,000 9,000 A 1 5 4 5 A B C B Click here for the Excel Data File 6531 Total processing time in minutes per machine: a. Assume that only purchasing costs are being considered. Compute the total processing time required for each machine type to meet demand, how many of each machine type would be needed, and the resulting total purchasing cost for each machine type. The machines will operate 8 hours a day, 220 days a year. (Enter total processing times as whole numbers. Round up machine quantities to the next higher whole number. Compute total purchasing costs using these rounded machine quantities. Enter the resulting total purchasing cost as a whole number.) C 2 1 2 6arrow_forwardHoosier Manufacturing operates a production shop that is designed to have the lowest unit production cost at an output rate of 100 units per hour. In the month of July, the company operated the production line for a total of 175 hours and produced 16,900 units of output. What was its capacity utilization rate for the month?arrow_forwardTrue or False: Capacity planning in operations management involves ensuring that a company's resources, including equipment, labor, and facilities, are able to meet current and future demand levels efficiently.arrow_forward
- How many workers are needed at each stage if management wants a utilization of at least 85 percent? Round your answers up to the nearest whole number. Stage A: __ workers Stage B: __ workers Stage C: __ workers Stage D: __ workers Stage E: __ workers Suppose that the number of workers at each stage are as follows: Stage Number of Workers A 5 B 3 C 7 D 5 E 2 What is the output rate at each stage? Round your answers to the nearest whole number. Stage A: __ units/hour Stage B: __ units/hour Stage C: __ units/hour Stage D: __ units/hour Stage E: __ units/hour Where is the bottleneck in this process? The bottleneck is (Stage A, B, C, D, or E).arrow_forwardThe measure of production that considers historical and estimated future production levels and cyclical fluctuations is referred to as: Group of answer choices expected capacity normal capacity theoretical capacity practical capacityarrow_forwardWestern Wheels produces industrial-grade wheels for local and international markets. Their factory can produce at most 1800 wheels per week. If the factory wants to achieve an utilization 89%, what should be the output of the factory next week? Please round final answer to nearest integerarrow_forward
arrow_back_ios
SEE MORE QUESTIONS
arrow_forward_ios
Recommended textbooks for you
- Practical Management ScienceOperations ManagementISBN:9781337406659Author:WINSTON, Wayne L.Publisher:Cengage,Operations ManagementOperations ManagementISBN:9781259667473Author:William J StevensonPublisher:McGraw-Hill EducationOperations and Supply Chain Management (Mcgraw-hi...Operations ManagementISBN:9781259666100Author:F. Robert Jacobs, Richard B ChasePublisher:McGraw-Hill Education
- Purchasing and Supply Chain ManagementOperations ManagementISBN:9781285869681Author:Robert M. Monczka, Robert B. Handfield, Larry C. Giunipero, James L. PattersonPublisher:Cengage LearningProduction and Operations Analysis, Seventh Editi...Operations ManagementISBN:9781478623069Author:Steven Nahmias, Tava Lennon OlsenPublisher:Waveland Press, Inc.
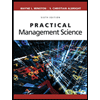
Practical Management Science
Operations Management
ISBN:9781337406659
Author:WINSTON, Wayne L.
Publisher:Cengage,
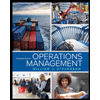
Operations Management
Operations Management
ISBN:9781259667473
Author:William J Stevenson
Publisher:McGraw-Hill Education
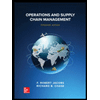
Operations and Supply Chain Management (Mcgraw-hi...
Operations Management
ISBN:9781259666100
Author:F. Robert Jacobs, Richard B Chase
Publisher:McGraw-Hill Education
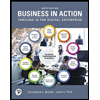
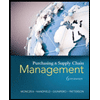
Purchasing and Supply Chain Management
Operations Management
ISBN:9781285869681
Author:Robert M. Monczka, Robert B. Handfield, Larry C. Giunipero, James L. Patterson
Publisher:Cengage Learning
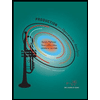
Production and Operations Analysis, Seventh Editi...
Operations Management
ISBN:9781478623069
Author:Steven Nahmias, Tava Lennon Olsen
Publisher:Waveland Press, Inc.