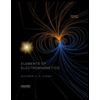
What does the region of strain hardening cause?

The working of the metals below their recrystallisation temperature is known as cold working process. Due to cold working the strength and hardness of the metal increases. Due to this process, the dislocations inside the ,metal crystals become entangled with each other and hence it become tough for the dislocations to move, hence hardening of the material atoms takes place .Example of cold working processes-cold rolling, cold forging, cold extrusion etc.
Strain hardening (also called work-hardening or cold-working) is the process of making a metal harder and stronger through permanent plastic deformation. When a metal is plastically deformed, dislocations move and additional dislocations are generated continuously. The more dislocations within a material, the more they will interact and get tangled. This will result in a decrease in the mobility of the dislocations and a strengthening of the material of the metal. This type of strengthening is commonly called cold-working. The plastic deformation must occurs at a temperature low enough that atoms cannot rearrange themselves, hence cold working is preferred for strain hardening. In strain hardening region less amount of deformation or strain occurs even if high amount of stress is developed.
Step by stepSolved in 3 steps

- Question 4 Save Answer You do a series of tensile tests on plates of a magnesium alloy that have been subjected to prior cold rolling to true plastic strains of 0.1, 0.2 and 0.3. The resulting true stress-true strain curves are shown below (including a zoomed in version expanding on the small strain region). It is reasonable to approximate the the 0.2% offset yield strength of the magnesium as ✓ MPa for 0.2 and ✓ MPa for 0.3. Assuming the yield strength is ✓ MPa for 0.1 plastic strain, proportional to the square root of the prior true plastic strain results in a hardening coefficient of approximately k= MPa. Hence, we can predict that we need a prior plastic strain of approximately True Stress (MPa) True Stress (MPa) True Stress (MPa) 250 200 150 100 50 0 0.00 250 200 150 100 50 0 0.00 250 200 150 100 50 0 0.00 Ep = 0.1 0.01 Ep=0.2 0.01 Ep=0.3 0.01 0.02 True Strain 0.02 0.03 0.02 0.03 True Strain 0.03 0.04 0.04 0.04 True Stress (MPa) 0.05 0.000 0.001 True Stress (MPa) Ep=0.1 True…arrow_forwardWhy does the tensile fracture occur suddenly?arrow_forwardCan we determine the relationship between the average normal stress and average normal strain by performing the tension test?arrow_forward
- Elements Of ElectromagneticsMechanical EngineeringISBN:9780190698614Author:Sadiku, Matthew N. O.Publisher:Oxford University PressMechanics of Materials (10th Edition)Mechanical EngineeringISBN:9780134319650Author:Russell C. HibbelerPublisher:PEARSONThermodynamics: An Engineering ApproachMechanical EngineeringISBN:9781259822674Author:Yunus A. Cengel Dr., Michael A. BolesPublisher:McGraw-Hill Education
- Control Systems EngineeringMechanical EngineeringISBN:9781118170519Author:Norman S. NisePublisher:WILEYMechanics of Materials (MindTap Course List)Mechanical EngineeringISBN:9781337093347Author:Barry J. Goodno, James M. GerePublisher:Cengage LearningEngineering Mechanics: StaticsMechanical EngineeringISBN:9781118807330Author:James L. Meriam, L. G. Kraige, J. N. BoltonPublisher:WILEY
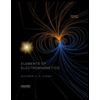
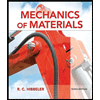
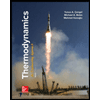
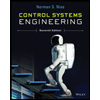
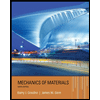
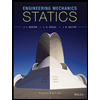