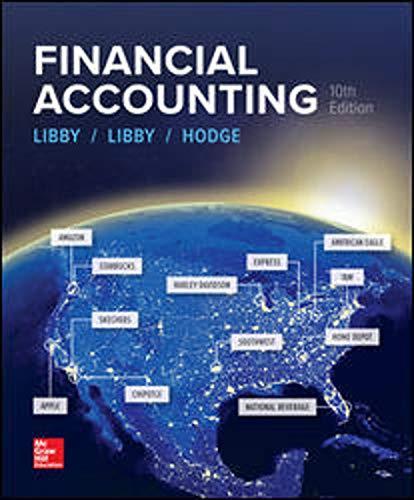
FINANCIAL ACCOUNTING
10th Edition
ISBN: 9781259964947
Author: Libby
Publisher: MCG
expand_more
expand_more
format_list_bulleted
Question
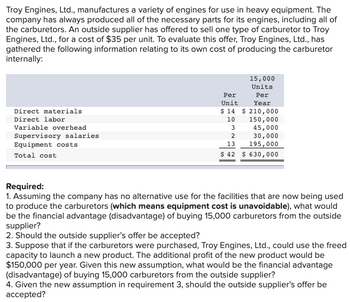
Transcribed Image Text:Troy Engines, Ltd., manufactures a variety of engines for use in heavy equipment. The
company has always produced all of the necessary parts for its engines, including all of
the carburetors. An outside supplier has offered to sell one type of carburetor to Troy
Engines, Ltd., for a cost of $35 per unit. To evaluate this offer, Troy Engines, Ltd., has
gathered the following information relating to its own cost of producing the carburetor
internally:
Direct materials
Direct labor
Variable overhead
Supervisory salaries
Equipment costs
Total cost
15,000
Units
Per
Per
Unit
Year
$ 14 $ 210,000
10
150,000
3
45,000
30,000
195,000
$630,000
2
13
$ 42
Required:
1. Assuming the company has no alternative use for the facilities that are now being used
to produce the carburetors (which means equipment cost is unavoidable), what would
be the financial advantage (disadvantage) of buying 15,000 carburetors from the outside
supplier?
2. Should the outside supplier's offer be accepted?
3. Suppose that if the carburetors were purchased, Troy Engines, Ltd., could use the freed
capacity to launch a new product. The additional profit of the new product would be
$150,000 per year. Given this new assumption, what would be the financial advantage
(disadvantage) of buying 15,000 carburetors from the outside supplier?
4. Given the new assumption in requirement 3, should the outside supplier's offer be
accepted?
Expert Solution

This question has been solved!
Explore an expertly crafted, step-by-step solution for a thorough understanding of key concepts.
This is a popular solution
Trending nowThis is a popular solution!
Step by stepSolved in 3 steps

Knowledge Booster
Similar questions
- Riverbed Company manufactures equipment. Riverbed's products range from simple automated machinery to complex systems containing numerous components. Unit selling prices range from $ 200,000 to $ 1,500,000 and are quoted inclusive of installation. The installation process does not involve changes to the features of the equipment and does not require proprietary information about the equipment in order for the installed equipment to perform to specifications. Riverbed has the following arrangement with Winkerbean Inc. Winkerbean purchases equipment from Riverbed fora price of $ 1,100,000 and contracts with Riverbed to install the equipment. Riverbed charges the same price for the equipment irrespective of whether it does the installation or not. Using market data, Riverbed determines installation service is estimated to have a standalone selling price of $ 46,000. The cost of the equipment is $ 580,000. Winkerbean is obligated to pay Riverbed the $ 1,100,000 upon the delivery and…arrow_forwardTroy Engines, Limited, manufactures a variety of engines for use in heavy equipment. The company has always produced all of the necessary parts for its engines, including all of the carburetors. An outside supplier has offered to sell one type of carburetor to Troy Engines, Limited, for a cost of $30 per unit. To evaluate this offer, Troy Engines, Limited, has gathered the following information relating to its own cost of producing the carburetor internally: Direct materials Direct labor Variable manufacturing overhead Fixed manufacturing overhead, traceable Fixed manufacturing overhead, allocated Total cost Per 12,000 Units Unit Per Year $ 12 $ 144,000 8 96,000 2 24,000 9* 12 108,000 144,000 $ 43 $ 516,000 *One-third supervisory salaries; two-thirds depreciation of special equipment (no resale value). Required: 1. Assuming the company has no alternative use for the facilities that are now being used to produce the carburetors, what would be the financial advantage (disadvantage) of…arrow_forwardThe Compressor Division and the Fabrication Division of Plash Company, which exclusively produces one type of washing machine, respectively, are its two divisions. For the Fabrication Division, which completes the washing machine and sells it to retailers, the Compressor Division makes compressors. The Fabrication Division buys compressors from the Compressor Division. The Fabrication Division will spend $40.00 on a compressor, which is the market price. (Skip updates to the inventory.) It is expected that the fixed costs for the Compressor Division remain constant for orders between 5,000 and 10,000 units. The Fabrication Division's fixed expenses are estimated to be $7.50 per unit at 10,000 units. Compressor's costs per compressor are: Direct materials $15.00 Direct labor $7.25 Variable overhead $3.00 Division fixed costs $7.50 Fabrication's costs per completed air conditioner are: Direct materials $150.00 Direct labor $62.50 Variable overhead $20.00 Division fixed costs $7.50 Assume…arrow_forward
- The Pixels Corporation produces a component used in the manufacture of one of its best-selling products. The costs associated with the production of 10,000 units of this component are presented in the table above. The PCAOB Corp. offered to sell Pixels 10,000 units of the same part at a price of $36 per unit. Assume that Pixels has no alternative use for the factory facilities that would be released. Based on all of the information above, should Pixels manufacture their own part or outsource to PCAOB? Note that if you agree to outsource, you would save $60,000 in indirect fixed costs. Direct Materials $90,000 Direct Manufacturing Labor $130,000 Variable Manufacturing Overhead $60,000 Fixed Manufacturing Overhead $140,000 Total Costs $420,000 a. Buy the part from PCAOB because you save $6 per unit b. Manufacture the part because it saves $6 per unit c. Make the part because you save $2 per unit d. Buy the part from PCAOB because you save $60,000arrow_forwardStan Fawcett's company currently purchases a gear assembly from Salt Lake Supply, Inc., at $3.80 per unit with a minimum order of 3,000 units. Stan is considering instead producing the gear assembly himself. He estimates that producing it himself will cost $12,000 to set up the process and then $1.82 per unit for labor and materials. a) Using the line drawing tool, add the total cost graph for Stan to produce the assembly instead of purchasing from Salt Lake Supply. Total cost for the purchase option is already plotted. Properly label your line. Note: Carefully follow the instructions above and only draw the required object. Cost 40,000- ¡Minimum Order 36,000 32,000- 28,000- 24,000 20,000- 16,000 12,000 - 8,000- 4,000- 0+ 0 2,000 4,000 Quantity 6,000 8,000arrow_forwardEach year, Basu Company produces 24,000 units of a component used in microwave ovens. An outside supplier has offered to supply the part for $1.17. The unit cost is: Direct materials $0.72 Direct labor 0.25 Variable overhead 0.13 Fixed overhead 2.95 Total unit cost $4.05 Required: 1. What are the alternatives for Basu Company? 2. Assume that none of the fixed cost is avoidable. List the relevant cost(s) of internal production. List the relevant cost(s) of external purchase. 3. Which alternative is more cost effective and by how much? _____ by $___ 4. What if $18,560 of fixed overhead is rental of equipment used only in production of the component that can be avoided if the component is purchased? Which alternative is more cost effective and by how much? ____ by $____arrow_forward
- ! Required information [The following information applies to the questions displayed below.] Kinnear Plastics manufactures various components for the aircraft and marine industry. Kinnear buys plastic from two vendors: Tappan Corporation and Hill Enterprises. Kinnear chooses the vendor based on price. Once the plastic is received, it is inspected to ensure that it is suitable for production. Plastic that is deemed unsuitable is disposed of. The controller at Kinnear collected the following information on purchases for the past year: Total purchases (tons) Plastic discarded Tappan 5,000 200 The purchasing manager has just received bids on an order for 330 tons of plastic from both Tappan and Hill. Tappan bid $2,112 and Hill bid $2,109 per ton. Effective cost per ton Hill 7,500 375 Required: 1-a. Assume that the average quality, measured by the amounts discarded from the two companies, will continue as in the past. What is the effective cost per ton for both Tappan and Hill? (Do not…arrow_forwardRenke Inc. is in the corn-milling industry but to date has had only enough manufacturing space for one joint process. Renke refers to its two products as prime products and by-products. There is a market for both products, but, as the names imply, the prime products are what Renke got into business to sell, as the prime products' sales price far exceeds that of the by-products. In a typical production run, which costs $60,000, Renke Inc. produces the following products, which can be sold at the prices shown. Prime products By-products Quantity Produced 1,625 tons 875 tons Sales Price per Ton $50 $5 Because Renke's customers (the corn processors) count on purchasing top-quality raw material from Renke, it is important that the company maintains a steady amount of inventory. For this reason, Renke never completely sells out of its products. For the current production run, managers plan to sell 80% of each product immediately, holding 20% in inventory to carry into the next period.arrow_forwardTroy Engines, Limited, manufactures a variety of engines for use in heavy equipment. The company has always produced all of the necessary parts for its engines, including all of the carburetors. An outside supplier has offered to sell one type of carburetor to Troy Engines, Limited, for a cost of $36 per unit. To evaluate this offer, Troy Engines, Limited, has gathered the following information relathng to its own cost of producing the carburetor internally:. Per 20,000 Units Per Unit Year $ 340,000 200,000 40,000 180, 000 240,000 Direct materials $ 17 Direct labor 10 2 Variable manufacturing overhead Fixed manufacturing overhead, traceable Fixed manufacturing overhead, allocated 9* 12 $ 50 $ 1,000,000 Total cost *One-third supervisory salaries; two-thirds depreciation of special equipment (no resale value). Required: 1. Assuming the company has no alternative use for the facilities that are now being used to produce the carburetors, what would be the financial advantage (disadvantage)…arrow_forward
arrow_back_ios
arrow_forward_ios
Recommended textbooks for you
- AccountingAccountingISBN:9781337272094Author:WARREN, Carl S., Reeve, James M., Duchac, Jonathan E.Publisher:Cengage Learning,Accounting Information SystemsAccountingISBN:9781337619202Author:Hall, James A.Publisher:Cengage Learning,
- Horngren's Cost Accounting: A Managerial Emphasis...AccountingISBN:9780134475585Author:Srikant M. Datar, Madhav V. RajanPublisher:PEARSONIntermediate AccountingAccountingISBN:9781259722660Author:J. David Spiceland, Mark W. Nelson, Wayne M ThomasPublisher:McGraw-Hill EducationFinancial and Managerial AccountingAccountingISBN:9781259726705Author:John J Wild, Ken W. Shaw, Barbara Chiappetta Fundamental Accounting PrinciplesPublisher:McGraw-Hill Education
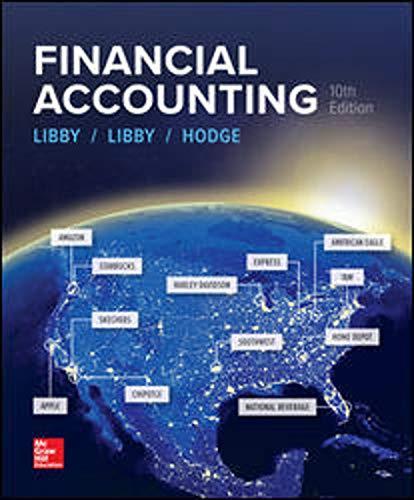
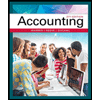
Accounting
Accounting
ISBN:9781337272094
Author:WARREN, Carl S., Reeve, James M., Duchac, Jonathan E.
Publisher:Cengage Learning,
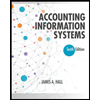
Accounting Information Systems
Accounting
ISBN:9781337619202
Author:Hall, James A.
Publisher:Cengage Learning,
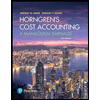
Horngren's Cost Accounting: A Managerial Emphasis...
Accounting
ISBN:9780134475585
Author:Srikant M. Datar, Madhav V. Rajan
Publisher:PEARSON
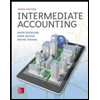
Intermediate Accounting
Accounting
ISBN:9781259722660
Author:J. David Spiceland, Mark W. Nelson, Wayne M Thomas
Publisher:McGraw-Hill Education
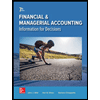
Financial and Managerial Accounting
Accounting
ISBN:9781259726705
Author:John J Wild, Ken W. Shaw, Barbara Chiappetta Fundamental Accounting Principles
Publisher:McGraw-Hill Education