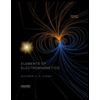
The turbocharger of an internal combustion engine consists of a turbine and a compressor. Hot exhaust gases flow through the turbine to produce work, and the work output from the turbine is used as the work input to the compressor. The pressure of ambient air is increased as it flows through the compressor before it enters the engine cylinders. Thus, the purpose of a turbocharger is to increase the pressure of air so that more air gets into the cylinder. Consequently, more fuel can be burned and more power can be produced by the engine. In a turbocharger, exhaust gases enter the turbine at 400°C and 120 kPa at a rate of 0.02 kg/s and leave at 350°C. Air entersthe compressor at 50°C and 100 kPa and leaves at 130 kPa at a rate of 0.018 kg/s. The compressor increases the air pressure with a side effect: It also increases the air temperature, which increases the possibility that a gasoline engine will experience an engine knock. To avoid this, an aftercooler is placed after the compressor to cool the warm air with cold ambient air before it enters the engine cylinders. It is estimated that the aftercooler must decrease the air temperature below 80°C if knock is to be avoided. The cold ambient air enters the aftercooler at 30°C and leaves at 40°C. Disregarding any frictional losses in the turbine and the compressor and treating the exhaust gases as air, determine the minimum volume flow rate of ambient air required to avoid knock.

Trending nowThis is a popular solution!
Step by stepSolved in 5 steps with 4 images

- 1. The heat produced in a boiler is transferred from the combustion products to the water. While the temperature of the combustion products decreases from 1100 °C to 550 °C, the pressure remains constant at 0.1 MPa. The average specific heat at constant pressure of the combustion products is 1.09 kJ/kg.K. The water enters the system at 0.8 MPa and 150 °C, and leaves at 0.8 MPa and 250 °C. Determine the second law efficiency and the irreversibility for each kilogram of water vaporized for this process. Note: This is a thermodynamics course question. Please provide a solution that is clear and quick.arrow_forwardQuestion 3 Consider the turbocharger of an internal combustion engine. The exhaust gases enter the turbine at 450°C at a rate of 0.02 kg/s and leave at 400°C. Air enters the compressor at70°C and 95 kPa at a rate of 0.018 kg/s and leaves at 135 kPa. The mechanical efficiency between the turbine and the compressor is 95 percent (5 percent of turbine work is lost duringits transmission to the compressor). Using air properties for the exhaust gases, determine:(a).The turbine power output, compressor power input, air temperature at the compressor exit,(b).The air temperature at the compressor for the case of isentropic process and isentropic efficiency of the compressor.arrow_forwardA nozzle is placed horizontally and a working fluid is passing through steadily. At the nozzle’s inlet, the velocity of fluid is 30 m/s and specific enthalpy is 2500 kJ/kg. At the exit from nozzle, its specific enthalpy is 2000 kJ/kg. Calculate: The velocity of the fluid at exitarrow_forward
- Elements Of ElectromagneticsMechanical EngineeringISBN:9780190698614Author:Sadiku, Matthew N. O.Publisher:Oxford University PressMechanics of Materials (10th Edition)Mechanical EngineeringISBN:9780134319650Author:Russell C. HibbelerPublisher:PEARSONThermodynamics: An Engineering ApproachMechanical EngineeringISBN:9781259822674Author:Yunus A. Cengel Dr., Michael A. BolesPublisher:McGraw-Hill Education
- Control Systems EngineeringMechanical EngineeringISBN:9781118170519Author:Norman S. NisePublisher:WILEYMechanics of Materials (MindTap Course List)Mechanical EngineeringISBN:9781337093347Author:Barry J. Goodno, James M. GerePublisher:Cengage LearningEngineering Mechanics: StaticsMechanical EngineeringISBN:9781118807330Author:James L. Meriam, L. G. Kraige, J. N. BoltonPublisher:WILEY
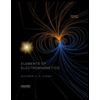
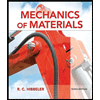
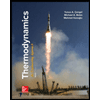
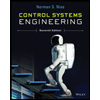
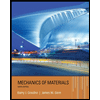
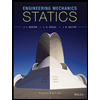