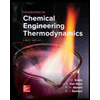
Chemical Engineering Calc.
1. A material containing 75% water and 25% solid is fed to a granulator at a rate of 4000 kg/hr. The feed is premixed in the granulator with recycled product from a dryer which follows the granulator (to reduce the water concentration of the overall material in the granulator to 50% water. 50% solid). The product that leaves the dryer contains 16.7% water. In the dryer, air is passed over the solid being dried. The air entering the dryer contains 3% water by weight (mass) .and the air leaving the dryer contains 6% water by weight (mass).
a) What is the recycle ratio to the granulator?
b) What is the rate of air flow to the dryer?
*note: please do not forget to draw the flow chart diagram. please do not copy from any other sites such do not take any answers from other sites. Please provide easy to understand solution (detailed with given, required, and solutions) in orderly manner.
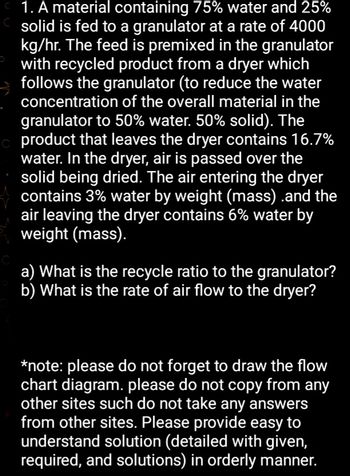

Trending nowThis is a popular solution!
Step by stepSolved in 3 steps with 4 images

- Troubleshooting.Corrosion of high-nickel stainless steel plates was found to occur in a distillation column used at DuPont to separate HCN and water. Sulfuric acid is always added at the top of the column to prevent polymerization of HCN. Water collects at the bottom of the column and HCN collectsat the top. The amount of corrosion on each tray is shown in Figure P3-5Bas a function of plate location in the column.The bottom-most temperature of the column is approximately 125C and the topmost is 100C.The corrosion rate is a function of temperature and the concentration of an HCN–H2SO4 complex.Suggest an explanation for the observed corrosion-plate profile in the column. What effect would the column operating conditions have on the corrosion-plate profile?arrow_forwardSteel surface can be hardened by carburization. Such process is done at 1000°C and the concentration gradient (dc/dx) is -8.23x1029 atoms/m4. The coefficient of diffusion (D0) for Fe is 20x10-6 m2/s (See table 1). Estimate the flux of carbon atoms into the steel in this process.arrow_forward10. The following figure shows an example of physically separating a recycle stream from a product. The process vessel in this case is making iron powder from input ingot by a process called atomization, which generated particles in a variety of sizes. Metal powder customers usually specify a narrower particle size range than the atomizer produces, so the process includes two screens, one to separate out the oversize material and a second that only allows undersize particles to pass through. The powder that doesn't pass through the second screen is what gets shipped to customers. The oversize and under-size powder streams are mixed together and fed back into the powdermaking unit. Fresh Atomizer feed Oversize 1 Recycle Product 2 Undersize One hundred twenty tons per day of "fresh" iron are fed to the powdermaking unit shown in the figure. Ten percent of the powder product fails to pass through the first screen; 26% of the powder fed to the second screen passes through it. If both the…arrow_forward
- I need a labeled process flow chart and a DOF analysis for this problem: One way to make coal “cleaner” is to gasify the coal into “city gas”. In a proposed molten-iron coal gasification process pulverized coal of up to 3 mm size is blown into a molten iron bath and oxygen and steam are blown in from the bottom of the vessel. Materials such as lime for settling the slag, or steam for batch cooling and hydrogen generation can be injected at the same time. The sulfur in the coal reacts with lime to form calcium sulfide, which dissolves into the slag. The process operates at atmospheric pressure and 1400 to 1500°C. Under these conditions, coal volatiles escape immediately and are cracked. The carbon conversion rate is said to be above 98% and the gas is typically 65 to 70% CO, 25 to 35% hydrogen, and less than 2% carbon dioxide. Sulfur content of the gas is less than 20 ppm. Assume that the product gas is 68% Co, 30% H2, and 2% CO2. Calculate the enthalpy change that occurs on the…arrow_forwardSome cold milk (temperature 10.2 degrees C) is added to 231g of hot milk (86.9 degrees C). Once mixed, all of the milk will reach a final temperature of 72.4 degrees C. What mass of cold milk was used? The specific heat capacity of the milk is 3930 J/kg degrees Carrow_forwardair at dry ball temperature 90 ° C and RH 8% is passed over the cooling coil so that the air dry ball temperature becomes 45 ° C. How much heat is released from the air in the process? = answer (kJ / kg)arrow_forward
- An evaporation-crystallization process of the type described in Example 4.5-2 is used to obtain solid potassium sulfate from an aqueous solution of this salt. The fresh feed to the process contains 19.6 wt % K2SO4. The wet filter cake consists of solid K2SO4 crystals and a 40.0 wt % K2SO4 solution, in a ratio 10 kg crystals/kg solution. The filtrate, also a 40.0% solution, is recycled to join the fresh feed. Of the water fed to the evaporator, 45.0% is evaporated. The evaporator has a maximum capacity of 175 kg water evaporated/s. (a) Assume the process is operating at maximum capacity. Draw and label a flowchart and do the degree-of-freedom analysis for the overall system, the recycle-fresh feed mixing point, the evap- orator, and the crystallizer. Then write in an efficient order (minimizing simultaneous equations) the equations you would solve to determine all unknown stream variables. In each equation, cir- cle the variable for which you would solve, but don't do the calculations.…arrow_forwardL-serine is produced by fermentation and recovered and purified by crystallization at 10oC. To increase the yield of the crystallization step, methanol is added to the system. An aqueous solution containing 27wt% L-serine is added with methanol to a batch crystallizer and cooled to 10oC. The crystals are then recovered by filtration. Draw a flowchart for this process showing the key unit operations with appropriate stream labels and composition.arrow_forward4arrow_forward
- 2) Filtration involves the separation of solid particles from fluid through a filtering medium and ranges from simple straining to more complex operations. Depending on the objective of the filtration process, the fluid, solid or both may be useful outputs of the overall process(a)Describe the basic principles offiltration as applied in the chemical industry. Using a suitable example, explain with clear illustrationshow filtration technique can be used to separate solids from filtrates at industrial scalearrow_forwardMaterial Science please helparrow_forwardIf Equimolar mixture of A and B is mixed, 200 kgmol/hr of water (component C) is used to extract B into aqueous phase. The product flow rates is 350 kgmol/hr. Find the Feed flowrate and the product composition.arrow_forward
- Introduction to Chemical Engineering Thermodynami...Chemical EngineeringISBN:9781259696527Author:J.M. Smith Termodinamica en ingenieria quimica, Hendrick C Van Ness, Michael Abbott, Mark SwihartPublisher:McGraw-Hill EducationElementary Principles of Chemical Processes, Bind...Chemical EngineeringISBN:9781118431221Author:Richard M. Felder, Ronald W. Rousseau, Lisa G. BullardPublisher:WILEYElements of Chemical Reaction Engineering (5th Ed...Chemical EngineeringISBN:9780133887518Author:H. Scott FoglerPublisher:Prentice Hall
- Industrial Plastics: Theory and ApplicationsChemical EngineeringISBN:9781285061238Author:Lokensgard, ErikPublisher:Delmar Cengage LearningUnit Operations of Chemical EngineeringChemical EngineeringISBN:9780072848236Author:Warren McCabe, Julian C. Smith, Peter HarriottPublisher:McGraw-Hill Companies, The
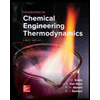
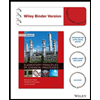
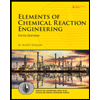
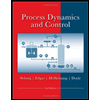
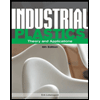
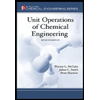