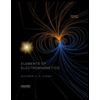
The shafting shown in Figure 2.51 was taken from a mill transfer chain that was frequently
overloaded, causing the shaft (made of low-carbon steel) to fail by torsion shear. It has obviously
been loaded in torsion beyond its elastic limit into the plastic range and has taken a permanent
set. Since the sprocket and bearing bores are bot easily changed to substitute a larger diameter
shaft, what type of replacement shaft will solve the problem? What different
properties must it posses so it will not again fail by torsion shear?

what type of replacement shaft will solve the problem? What different mechanical
properties must it posses so it will not again fail by torsion shear?
Trending nowThis is a popular solution!
Step by stepSolved in 2 steps

- (7) A clutch system is to be designed to transmit 800 ft-lb of torque. A multi-plate clutch in an oil bath is found to be suitable for this application. The outer disk diameter is to be limited to a maximum of 7 inch. Design data for molded friction material and steel disk is Pmax = 160 psi and f = 0.11. Determine inner diameter of disks, clamping force and number of disks. Assume inner diameter of disk = 0.5 * outer diameter. Assume uniform rate of wear at interface (List necessary assumptions, make suitable sketch & label it, write conclusions).arrow_forwardPlease full steps. Big clear Handwriting. Thanksarrow_forwardA car jack uses a single square-thread screw to raise a known load. The major diameter and pitch of the screw and the thrust collar mean diameter are known. Running friction coefficients are estimated. Find: (a) Determine the thread depth and helix angle. (b) Estimate the starting torque for raising and lowering the load. (c) Estimate the efficiency of the jack for raising the load. (d) Estimate the power required to drive the screw at a constant 1 revolution per second. Schematic and Given Data: Load 50 kN NOTE: ANSWER ONLY LETETRS C AND D.arrow_forward
- Describe the failure of a hollow torque tube. Calculate the forces creating the failurearrow_forward(4) An electric motor purchased by your employer surprisingly arrived without a keyway in the shaft. The motor has power rating of 7.5kW & 1,800rpm & has a shaft of Ø17mm. It will be used to drive a centrifugal pump using cast iron sheave. Design the square key to be used in the assembly based on maximum bearing & shearing stresses of 580MPa & 370MPa, respectively, and factor of safety of 5.arrow_forward4 A double-threaded power screw with square threads pushes against a load of 3,641 N at a speed of 15 mm/s. The screw has a major diameter of 20 mm and a pitch of 3 mm. The frictional coefficient of the threads is 0.25, and collar friction is negligible. What is the rotational speed of the screw in units of revolutions per minute? Type your answer 2 pointsarrow_forward
- I have a 52100 steel hollow shaft, that will be threaded into a 1 inch thick plate of aluminum 7075. The shaft is 960 mm in length, 40 mm OD and 20 mm ID. The threaded end of the shaft is M30X3.5. What would be the recommended torque for the shaft, with the dissimilar metals. I’m expecting a range between 100-280 ft-lbs but can justify it.arrow_forwardCompute the contact stress number for the gear fain pair driven directly by an electrical motor. The driven machthe is concrete mixture with moderate shock, the other data are given below. Ks= 1.00, Km 1.21, Vt =1527 St/min, Av-11 Pd= 6, np= 1750rp.m, Np 20, No= 70, F=2.00/n Tp = 900ib, Dp= 3:333 in The material used for pioin an gear is Steelarrow_forward4. A square-threaded power screw has a mean diameter, dm = 1.75 in and a pitch, p = 0.875 in. The coefficient of thread friction is 0.10 and the collar friction is negligible. What horsepower is required to raise a weight of 3000 lbf at a rate of 20 ft/min?arrow_forward
- In a gear set, a 36-tooth spur pinion drives a 60-tooth spur gear. The teeth of these gear are cast iron profile. The diametral pitch is 6-teeth/in, the face width si 0.5 inches, and the pressure angle is 20 degrees. Assume that the pinion transmits 10 hp at a speed of 2000 rpm. Find the tangential load in lbf Find the contact stress in kpsi, assuming CP=1960 psi.arrow_forwardNote: Read the question carefully and give me all a,b and c right solutions. If you don't know the concept please leave it. I want 100% right solutiosarrow_forward(8) An axle (non-rotating) is to be machined from AISI 1144, OQT 1,000°F, to the proportions keyway в shown, with a fillet radius r = 0.2D; F varies 1.SD from 400 lb. to 1,200 lb.; the supports are to the left of B, not shown. Let N = 2 (Soderberg Line). 6" (a) At the fillet, compute D and the 30 maximum tensile stress. (b) Compute D at section B. (c) Specify suitable dimensions. Keeping the given proportions, would a smaller diameter be permissible if the fillet were shot-peened?arrow_forward
- Elements Of ElectromagneticsMechanical EngineeringISBN:9780190698614Author:Sadiku, Matthew N. O.Publisher:Oxford University PressMechanics of Materials (10th Edition)Mechanical EngineeringISBN:9780134319650Author:Russell C. HibbelerPublisher:PEARSONThermodynamics: An Engineering ApproachMechanical EngineeringISBN:9781259822674Author:Yunus A. Cengel Dr., Michael A. BolesPublisher:McGraw-Hill Education
- Control Systems EngineeringMechanical EngineeringISBN:9781118170519Author:Norman S. NisePublisher:WILEYMechanics of Materials (MindTap Course List)Mechanical EngineeringISBN:9781337093347Author:Barry J. Goodno, James M. GerePublisher:Cengage LearningEngineering Mechanics: StaticsMechanical EngineeringISBN:9781118807330Author:James L. Meriam, L. G. Kraige, J. N. BoltonPublisher:WILEY
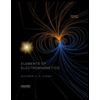
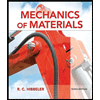
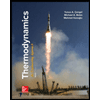
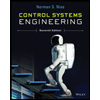
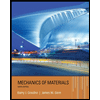
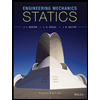