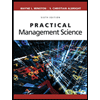
Concept explainers
The sales of Whole Care mouthwash at Tom's of Maine over the past six months have averaged 2,000 cases per month, which is the current order quantity. Tom's of Maine's cost is $12.00 per case, and ordering cost is $38. The company estimates its cost of capital to be 12 percent. Insurance, taxes, breakage, handling, and pilferage are estimated to be approximately 6 percent of the item cost. Lead time is 3 days, and considering weekends and holidays, Tom's of Maine operates 250 days per year.
Based on the above information please answer the following questions
a) What is EOQ?
b) What is the cost reduction?
c) What is the reorder point?
d) What is Time between Orders (TBO)?

Trending nowThis is a popular solution!
Step by stepSolved in 2 steps with 3 images

- All the statements concerning reasons to hold inventory are true Except: To meet variations in demand To allow inflexible production schedules To take advantage of price discounts As a safeguard against variations in delivery timearrow_forwardA billiard ball maker must place orders for resin, a raw material for billiard balls. It uses resin at a rate of 120 kilograms each day, and incurs a cost of $0.4 per kilogram per day to hold inventory. The ordering cost is $150 per order. Lead time for delivery is 4 days. Assume 365 day in a year.What is the optimal length of the order cycle associated with the minimum total cost of ordering and inventory holding? [Round your final number with two decimals] 0.13 days 1.10 days 2.50 days 47.76 days None of the above PLEASE SHOW CALCULATIONS NOT JUST ANSWERarrow_forwarda) What is the economic order quantity? b) Find the annual holding costs.c) Find the annual ordering costs.d) What is the reorder point?arrow_forward
- You have an annual demand of 800 units of your product which you sell for $90 a unit. It costs you $20 to place an order and carrying costs for the item are 14%. What is your EOQ?arrow_forwardA company that markets hypodermic needles to hospitals. The company purchases the needles from a supplier. The annual demand is 7,641 needles. The annual setup (or ordering) cost is $20 per order and the inventory holding cost per unit per year is $6.05. The company operates 258 days a year. Calculate the optimal number of orders per year for the company.arrow_forwardA toy manufacturer uses approximately 32,000 silicon chips annually. The chips are used at a steady rate during the 240 days a year that the plant operates. Annual holding cost is $3 per chip, and ordering cost is $120. Determine the following: What is the reorder point, if the lead time is 7 days?arrow_forward
- A certain successful entrepreneur purchases high-quality term papers ("guaranteed A") from an even bigger entrepreneur for resale to unethical students. Annual demand is 34000 papers, carrying cost is $3 per paper per year, and ordering cost is $90 per order. Students, being as desperate as they are, never backorder. The purchase price is stiff $35 per paper. What is the optimal order quantity (round your final answer to the nearest integer) ?MY answer 1428Correct answer 1565arrow_forwardA components manufacturer uses approximately 20,000 units annually of an item. They are used at a steady rate during the 250 workdays that the plant operates. The cost of each item is $7.00, and the annual carrying cost is $0.50 per unit per year. The ordering cost is $50. What is the economic order quantity?arrow_forwardDelaney Co. uses 12,000 of an item per year. They are open 300 days per year. The item takes 8 days from the time they place an order until they receive it. They like to maintain a safety stock of 200. What is Delaney's reorder point for this item?arrow_forward
- www.www A toy manufacturer uses approximately 40000 silicon chips annually. The chips are used at a steady rate during 350 working days per year. The annual holding cost is $4 per chip, ordering cost is $145, and lead time is 5 days. Determine the annual cost saving if company uses optimal EOQ (part a) instead of current order quantity of 3000 units (Round your answer to 1 decimal places)arrow_forwardPotter Machine Company expects total sales of $60,000. The price per unit is $10. The firm estimates an ordering cost of $25 per order, with an inventory carrying cost of $0.70 per unit. What is the optimal order size?arrow_forwardUse the inventory table and the gross profit inventory method to estimate the ending inventory and cost of goods sold if a 40% gross profit is realized on sales and net sales are $115,990. Date of purchase Units Cost per Total Retail price Total retail purchased unit cost per unit value Beginning inventory 41 $830 $34,030 $985 $40,385 February 5 20 $1,750 $35,000 $2,115 $42,300 February 19 15 $975 $14,625 $1,996 $29,940 March 3 28 $470 $13,160 $610 $17,080 Goods available for sale 104 $129,705 Units sold 81 Ending inventory 23 The estimated cost of goods sold is $arrow_forward
- Practical Management ScienceOperations ManagementISBN:9781337406659Author:WINSTON, Wayne L.Publisher:Cengage,Operations ManagementOperations ManagementISBN:9781259667473Author:William J StevensonPublisher:McGraw-Hill EducationOperations and Supply Chain Management (Mcgraw-hi...Operations ManagementISBN:9781259666100Author:F. Robert Jacobs, Richard B ChasePublisher:McGraw-Hill Education
- Purchasing and Supply Chain ManagementOperations ManagementISBN:9781285869681Author:Robert M. Monczka, Robert B. Handfield, Larry C. Giunipero, James L. PattersonPublisher:Cengage LearningProduction and Operations Analysis, Seventh Editi...Operations ManagementISBN:9781478623069Author:Steven Nahmias, Tava Lennon OlsenPublisher:Waveland Press, Inc.
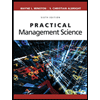
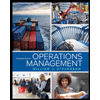
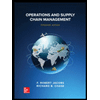
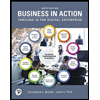
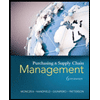
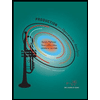