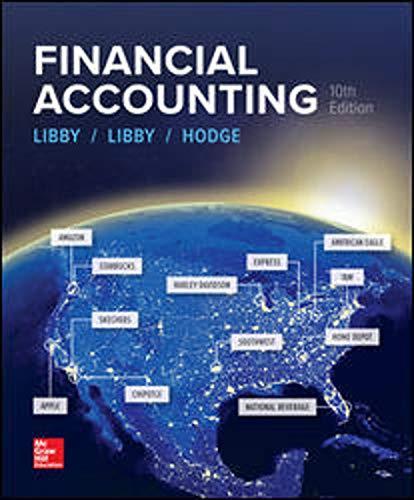
FINANCIAL ACCOUNTING
10th Edition
ISBN: 9781259964947
Author: Libby
Publisher: MCG
expand_more
expand_more
format_list_bulleted
Question
The Colin Division of Sunland Company sells its product for $32 per unit. Variable costs per unit include: manufacturing, $14; and selling and administrative, $3. Fixed costs are: $200000 manufacturing
What would the net income be under variable costing for each alternative?
40000 units 60000 units
$380000 $340000
$340000 $392000
$340000 $340000
$340000 $500000
Expert Solution

This question has been solved!
Explore an expertly crafted, step-by-step solution for a thorough understanding of key concepts.
This is a popular solution
Trending nowThis is a popular solution!
Step by stepSolved in 2 steps with 1 images

Knowledge Booster
Learn more about
Need a deep-dive on the concept behind this application? Look no further. Learn more about this topic, accounting and related others by exploring similar questions and additional content below.Similar questions
- Artisan Metalworks has a bottleneck in their production that occurs within the engraving department. Jamal Moore, the COO, is considering hiring an extra worker, whose salary will be $54,000 per year, to solve the problem. With this extra worker, the company could produce and sell 3,000 more units per year. Currently, the selling price per unit is $26.00 and the cost per unit is $7.75. Direct materials $3.40 Direct labor 1.10 Variable overhead 0.45 Fixed overhead (primarily depreciation of equipment) 2.80 Total $7.75 Using the information provided, calculate the annual financial impact of hiring the extra worker. Profit $fill in the blank 1arrow_forwardIn the last 6 months, demand for one of Appleby Company's products has dropped off considerably, due mainly to it becoming obsolescent as a result of technological change. Knowing that the equipment used in the manufacture of this product may not be easy to sell, Appleby spent $50,000 on consultants to determine whether it could use the equipment to produce a new product under license by another company. The consultant has determined that this product would have variable production costs of $65 per unit and should sell at a price of $90/unit. The licensing royalty is 5% of gross product revenue. Estimated annual demand is 20,000 units per year. Additional annual operating costs related to this product are $30,000/year (excluding depreciation). Depreciation on the equipment is $15,000. Annual depreciation expense is a: O a. Sunk cost O b. Relevant cost O c. Both sunk and Irrelevant cost Od. Irrelevant costarrow_forwardA company makes 36,000 motors to be used in the production of its blender. The average cost per motor at this level of activity is: Direct materials Direct labor Variable manufacturing overhead Fixed manufacturing overhead An outside supplier recently began producing a comparable motor that could be used in the blender. The price offered to the company for this motor is $23.95. There would be no other use for the production facilities and none of the fixed manufacturing overhead cost could be avoided. The annual financial advantage (disadvantage) for the company as a result of making the motors rather than buying them from the outside supplier would be: Multiple Choice O O O ($68,400) $214,200 $9.50 $ 8.50 $ 3.45 $ 4.40 90,000 $158,400arrow_forward
- Artisan Metalworks has a bottleneck in their production that occurs within the engraving department. Jamal Moore, the COO, is considering hiring an extra worker, whose salary will be $54,000 per year, to solve the problem. With this extra worker, the company could produce and sell 3,000 more units per year. Currently, the selling price per unit is $25.00 and the cost per unit is $7.80. Direct materials $3.50 Direct labor 1.10 Variable overhead 0.40 Fixed overhead (primarily depreciation of equipment) 2.80 Total $7.80 Using the information provided, calculate the annual financial impact of hiring the extra worker. Profit $_____ ______arrow_forwardZycon has produced 10,000 units of partially finished Product A. These units cost $15,000 to produce, and they can be sold to another manufacturer for $20,000. Instead, Zycon can process the units further and produce finished Products X, Y, and Z. Processing further will cost an additional $22,000 and will yield total revenues of $35,000. Place an X in the appropriate column to identify whether the item is relevant or irrelevant to the sell or process further decision.arrow_forwardHH Co. uses corrugated cardboard to ship its product to customers. Currently, the company’s returns department incurs annual overhead costs of $126,000 and forecasts 6,000 returns per year. Management believes it has found a better way to package its products. As a result, the company expects to reduce the number of shipments that are returned due to damage by 3%. In addition, the initiative is expected to reduce the department’s annual overhead by $14,000.Compute the returns department’s standard overhead rate per return (a) before the sustainability improvement and (b) after the sustainability improvement.arrow_forward
- Edidas Company needs 20,000 units of Part GX to use in producing one of its products. If Edidas buys the Part GX from McMillan Company for $79 instead of making it, Edidas will not use the released facilities in another manufacturing activity. Twenty percent of the fixed overhead will continue irrespective of CEO Donald Mickey's decision. The cost per unit data are as follows: Cost to make the part Direct Materials Direct Labor (S) 30 15 Variable Overhead 20 Fixed Overhead 20 85 Required : 1. Explain which alternative is more attractive to Edidas, make or buy Part GX. 2. Assume there is new information that Edidas is negotiating to purchase cheaper raw materials from supplier (Twenty percent lower price). Is this information relevant or irrelevant? On the basis of financial considerations alone, should Edidas make or buy Part GX? Show your calculations 3. Based on requirement 2, what are relevant qualitative factors that Edidas should consider to decide whether to make or buy Part GX?…arrow_forwardGrey Inc. has been purchasing a component, Z for $85 a unit. The company is currently operating at 75% of full capacity, and no significant increase in production is anticipated in the near future. The cost of manufacturing a unit of Z, determined by absorption costing method, is estimated as follows: Direct materials $30 Direct labor 15 Variable factory overhead 26 Fixed factory overhead 10 Total $81 Prepare a differential analysis report, dated March 12 of the current year, on the decision to make or buy Part Z. Grey Inc. Proposal to Manufacture Part Z March 12, 20XX Purchase price of Part Z Differential cost to manufacture Z: Direct materials X Direct labor X Variable factory overhead X Cost savings from manufacturing Part Zarrow_forwardSteven oversees the production department for a factory that makes plastic outdoor chairs. department sells all of its production to external parties, and the department has an overall production capacity of 150,000 chairs. Their sales data is as follows: Sales (90,000 chairs) a $460,000, Variable Costs are $206,200, and Fixed Costs are $194,350. The internal Resale would like to purchase 26,700 chairs from the Production Department. They will be selling external retailers for $15.49 per chair. If the Resale Division negotiates a deal with the Pro Department to purchase each chair for its absorption cost plus a 2.4% markup, then what amount of Operating Income the Resale Division would report for their sale of 26,700 cha per unit cost to nearest cents. O $291,831 O $351,105 O $198,235 O $3,612arrow_forward
- Race Cars, Inc., produces model cars made from aluminum. It operates two production departments, Molding and Painting, and has three service departments, Administration, Accounting, and Maintenance. The accumulated costs in the three service departments were $250,000, $400,000 and $200,000, respectively. Management is concerned that the costs of its service departments are getting too high. In particular, managers would like to keep the costs of service departments under $3.50 per unit on average. You have been asked to allocate service department costs to the two production departments and compute the unit costs. The company decided that Administration costs should be allocated on the basis of square footage used by each production and service department. Accounting costs are allocated on the basis of number of employees. Maintenance cost are allocated on the basis of the dollar value of the equipment in each department. The use of each base by all departments during the current…arrow_forward(Note: This type of decision is similar to dropping a product line.) Nicholas Company manufactures a fast-bonding glue, normally producing and selling 64,000 litres of the glue each month. This glue, which is known as MJ-7, is used in the wood industry to manufacture plywood. The selling price of MJ-7 is $50 per litre, variable costs are $30 per litre, fixed manufacturing overhead costs in the plant total $368,000 per month, and the fixed selling costs total $492,800 per month. Strikes in the mills that purchase the bulk of the MJ-7 glue have caused Nicholas Company's sales to temporarily drop to only 16,000 litres per month. Nicholas Company's management estimates that the strikes will last for two months, after which sales of MJ-7 should return to normal. Due to the current low level of sales, Nicholas Company's management is thinking about closing down the plant during the strike. If Nicholas Company does close down the plant, fixed manufacturing overhead costs can be reduced by…arrow_forwardScholes Systems supplies a particular type of office chair to large retailers such as Target, Costco, and Office Max. Scholes is concerned about the possible effects of inflation on its operations. Presently, the company sells 81,000 units for $65 per unit. The variable production costs are $35, and fixed costs amount to $1,410,000. Production engineers have advised management that they expect unit labor costs to rise by 15 percent and unit materials costs to rise by 10 percent in the coming year. Of the $35 variable costs, 40 percent are from labor and 20 percent are from materials. Variable overhead costs are expected to increase by 20 percent. Sales prices cannot increase more than 10 percent. It is also expected that fixed costs will rise by 5 percent as a result of increased taxes and other miscellaneous fixed charges. The company wishes to maintain the same level of profit in real dollar terms. It is expected that to accomplish this objective, profits must increase by 7 percent…arrow_forward
arrow_back_ios
SEE MORE QUESTIONS
arrow_forward_ios
Recommended textbooks for you
- AccountingAccountingISBN:9781337272094Author:WARREN, Carl S., Reeve, James M., Duchac, Jonathan E.Publisher:Cengage Learning,Accounting Information SystemsAccountingISBN:9781337619202Author:Hall, James A.Publisher:Cengage Learning,
- Horngren's Cost Accounting: A Managerial Emphasis...AccountingISBN:9780134475585Author:Srikant M. Datar, Madhav V. RajanPublisher:PEARSONIntermediate AccountingAccountingISBN:9781259722660Author:J. David Spiceland, Mark W. Nelson, Wayne M ThomasPublisher:McGraw-Hill EducationFinancial and Managerial AccountingAccountingISBN:9781259726705Author:John J Wild, Ken W. Shaw, Barbara Chiappetta Fundamental Accounting PrinciplesPublisher:McGraw-Hill Education
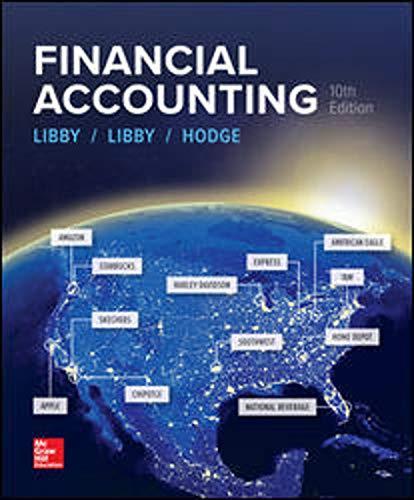
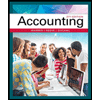
Accounting
Accounting
ISBN:9781337272094
Author:WARREN, Carl S., Reeve, James M., Duchac, Jonathan E.
Publisher:Cengage Learning,
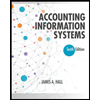
Accounting Information Systems
Accounting
ISBN:9781337619202
Author:Hall, James A.
Publisher:Cengage Learning,
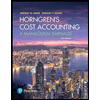
Horngren's Cost Accounting: A Managerial Emphasis...
Accounting
ISBN:9780134475585
Author:Srikant M. Datar, Madhav V. Rajan
Publisher:PEARSON
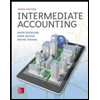
Intermediate Accounting
Accounting
ISBN:9781259722660
Author:J. David Spiceland, Mark W. Nelson, Wayne M Thomas
Publisher:McGraw-Hill Education
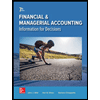
Financial and Managerial Accounting
Accounting
ISBN:9781259726705
Author:John J Wild, Ken W. Shaw, Barbara Chiappetta Fundamental Accounting Principles
Publisher:McGraw-Hill Education