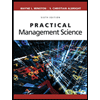
Practical Management Science
6th Edition
ISBN: 9781337406659
Author: WINSTON, Wayne L.
Publisher: Cengage,
expand_more
expand_more
format_list_bulleted
Question
thumb_up100%
can you explain this answer for you? and more explaination for the avaribles.
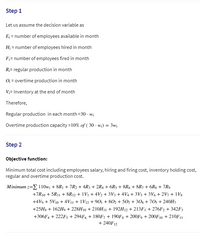
Transcribed Image Text:Step 1
Let us assume the decision variable as
E; = number of employees available in month
H; = number of employees hired in month
F;= number of employees fired in month
R;= regular production in month
0; = overtime production in month
V;= Inventory at the end of month
Therefore,
Regular production in each month =30 - wi
Overtime production capacity =10% of ( 30 · w;) = 3w;
Step 2
Objective function:
Minimum total cost including employees salary, hiring and firing cost, inventory holding cost,
regular and overtime production cost.
Minimum z=E 110w; + 8R1 + 7R2 + 4R3 + 2R4 + 6R5 + 8R6 + 8R7 + 6R8 + 7R9
+7R10 + 5R|1 + 8R12 + 1V1 + 4V2 + 3V3 + 4V4 + 3V5 + 3V6 + 2V + 1V8
+4V9 + 5V10 + 4V11 + 1V12 + 901 + 802 + 503 + 304 + 705 + 240H
+25H8 + 162H9 + 228H10 + 210H|| + 192H12 + 213F¡ + 276F2 + 342F3
+306F4 + 222F5 + 294F6 + 180F, + 190Fg + 200F9 + 200F10 + 210F11
+ 240F12
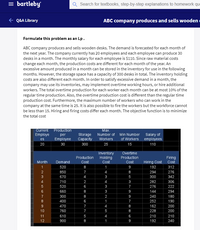
Transcribed Image Text:= bartleby
Q Search for textbooks, step-by-step explanations to homework que
e Q&A Library
ABC company produces and sells wooden «
Formulate this problem as an Lp.
ABC company produces and sells wooden desks. The demand is forecasted for each month of
the next year. The company currently has 20 employees and each employee can produce 30
desks in a month. The monthly salary for each employee is $110. Since raw material costs
change each month, the production costs are different for each month of the year. An
excessive amount produced in a month can be stored in the inventory for use in the following
months. However, the storage space has a capacity of 300 desks in total. The inventory holding
costs are also different each month. In order to satisfy excessive demand in a month, the
company may use its inventories, may implement overtime working hours, or hire additional
workers. The total overtime production for each worker each month can be at most 10% of the
regular time production. Also, the overtime production cost is different than the regular time
production cost. Furthermore, the maximum number of workers who can work in the
company at the same time is 25. It is also possible to fire the workers but the workforce cannot
be less than 15. Hiring and firing costs differ each month. The objective function is to minimize
the total cost
Current Production
Employe
Max.
Storage Number of Min Number Salary of
Сараacity
per
es
Employee
Workers
of Workers employees
20
30
300
25
15
110
Inventory
Holding
Overtime
Production
Production
Firing
Hiring Cost
192
Month
Demand
Cost
Cost
Cost
Cost
1
520
9
312
2
850
4.
8.
294
276
3
670
3
5
300
342
710
4
282
306
5
520
3
7
276
222
6
660
8
3
144
294
7
300
8
2
9
240
180
400
1
252
190
470
162
200
10
760
5
8.
228
200
11
610
4.
6.
210
210
12
900
9
192
240
7.
CO
8. 74
2 60
6677
558
Expert Solution

arrow_forward
Step 1
Linear Programming is an optimization technique used to achieve the best outcome or output by taking various constraints and factors. It is a mathematical model which uses a set of variables to form linear relationships.
Step by stepSolved in 2 steps

Knowledge Booster
Learn more about
Need a deep-dive on the concept behind this application? Look no further. Learn more about this topic, operations-management and related others by exploring similar questions and additional content below.Similar questions
- There are several different ways you can increase participation from customers: give two examples of different names?arrow_forwardWhat is the "free rider" problem and how does it relate to interest group membership? According to sponsorship theory, how might interest groups try to overcome this problem?arrow_forwardHow does the deep web aid IT-dependent businesses?arrow_forward
arrow_back_ios
arrow_forward_ios
Recommended textbooks for you
- Practical Management ScienceOperations ManagementISBN:9781337406659Author:WINSTON, Wayne L.Publisher:Cengage,Operations ManagementOperations ManagementISBN:9781259667473Author:William J StevensonPublisher:McGraw-Hill EducationOperations and Supply Chain Management (Mcgraw-hi...Operations ManagementISBN:9781259666100Author:F. Robert Jacobs, Richard B ChasePublisher:McGraw-Hill Education
- Purchasing and Supply Chain ManagementOperations ManagementISBN:9781285869681Author:Robert M. Monczka, Robert B. Handfield, Larry C. Giunipero, James L. PattersonPublisher:Cengage LearningProduction and Operations Analysis, Seventh Editi...Operations ManagementISBN:9781478623069Author:Steven Nahmias, Tava Lennon OlsenPublisher:Waveland Press, Inc.
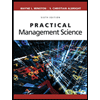
Practical Management Science
Operations Management
ISBN:9781337406659
Author:WINSTON, Wayne L.
Publisher:Cengage,
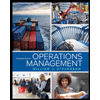
Operations Management
Operations Management
ISBN:9781259667473
Author:William J Stevenson
Publisher:McGraw-Hill Education
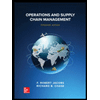
Operations and Supply Chain Management (Mcgraw-hi...
Operations Management
ISBN:9781259666100
Author:F. Robert Jacobs, Richard B Chase
Publisher:McGraw-Hill Education
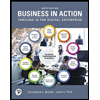
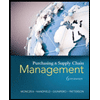
Purchasing and Supply Chain Management
Operations Management
ISBN:9781285869681
Author:Robert M. Monczka, Robert B. Handfield, Larry C. Giunipero, James L. Patterson
Publisher:Cengage Learning
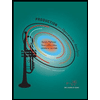
Production and Operations Analysis, Seventh Editi...
Operations Management
ISBN:9781478623069
Author:Steven Nahmias, Tava Lennon Olsen
Publisher:Waveland Press, Inc.