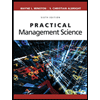
Practical Management Science
6th Edition
ISBN: 9781337406659
Author: WINSTON, Wayne L.
Publisher: Cengage,
expand_more
expand_more
format_list_bulleted
Question
Statement 1 – For providing higher service levels an organization must hold higher levels of inventory. Statement 2 – A perfect order is a key measure of supply chain performance
a.
True, True
b.
False, True
c.
True, False
d.
False, False
Expert Solution

This question has been solved!
Explore an expertly crafted, step-by-step solution for a thorough understanding of key concepts.
Step by stepSolved in 3 steps

Knowledge Booster
Similar questions
- What are order cycle costs if annual demand is 9,600 units, the order quantity is 2,000 units, and annual order cost is $45? What if the order size changes to 1,000 units or 9,600 units? Round your answers to the nearest cent. If the order quantity is 2,000 units, the order cycle costs are $ . If the order quantity is 1,000 units, the order cycle costs are $ . If the order quantity is 9,600 units, the order cycle costs are $ .arrow_forwardWhich of the following are true as the order decoupling point moves toward the source? I. Inventory investment decreases. II. Customer lead time gets longer. III. Inventory investment increases. IV. Customer lead time is unchanged. Options I and II Options II and III Option III Option III and IV Option IVarrow_forwardTransactional relationships are most appropriate for suppliers of ________ inventory types. Group of answer choices Critical Leverage Routine None of these answersarrow_forward
- Unaiki manages the inventory for Hine's kids collection. She's had too many stockouts lately and is worried about poor customer service. Therefore, she is considering a change to the current inventory control system for kids track pants. She gathers the following information: average demand: 250 pairs/week lead time: 2 weeks order cost = $75 per/order unit cost: $21.50 carrying charge rate = 18% desired service level = 95% standard deviation of weekly demand: 40 number of weeks per year: 52 Unaiki decides to use a fixed order quantity system. a. What is the Economic Order Quantity? b. What are the total annual order and inventory-holding costs for the EOQ? c. What should the reorder point be to have a 95% service level? d. Help Unaoiki understand her new order logic: In order to stay in stock 95% of the time. she should place an order for ________ pairs when ____________.arrow_forwardThe extra inventory we keep just in case the replenishment is delayed is referred to as Group of answer choices a)customer service inventory b)unanticipated excess inventory c)safety stock d) unexplained inventoryarrow_forwardPlease do not give solution in image format thankuarrow_forward
- Please do not give solution in image formate thanku Which of the following is a method to improve cash-to-cash conversion (CCC)?Increasing payment terms from customersIncreasing inventory safety stockDecreasing payment terms from customersDecreasing payment terms from suppliersarrow_forwardExplain the following based on Demand Management Demand Management Independent Demand Dependent Demand Random Variations Safety Stocksarrow_forwardA plastic canister manufacturing company maintains an annual safety stock of 500 units of plastic caps. If the company places an annual purchase order for 1,800 units of these caps, its average annual inventory, in units, is between: ( )1,500 and 1,300 ( )3,200 and 3,000 ( )2,400 and 2,200 ( )1,200 and 1,000 ( )1,900 and 1,700arrow_forward
- 13.20. Southwood Furniture Company is a U.S.-based furniture manufacturer that offshored all of its actual manufacturing opera- tions to China about a decade ago. It set up a distribution center in Hong Kong from which the company ships its items to the United States on container ships. The company learned early on that it could not rely on local Chinese freight forwarders to arrange for sufficient containers for the company's shipments, so it contracted to purchase containers from a Taiwanese manufacturer and then sell them to shipping companies at the U.S. ports the containers are shipped to. Southwood needs 715 containers each year. It costs $1200 to hold a container at its distribution center, and it costs $6000 to receive an order for the containers. Determine the optimal order size, min- imum total annual inventory cost, number of annual orders, and time between orders.arrow_forwardThe Northridge Company tends to keep the inventory low. At the same time, it is important to respond to demand quickly, since a customer who wants a product K is very likely to get one from a competitor if Northridge Company doesn’t have one available immediately. Northridge Company’s current policy to produce the product K is to produce 100 per week, which is the average demand. Even this is a problem, as the production manager has pointed out, since the equipment is also used for other products and the lot size of 300 would be much more efficient. He said he is currently set up the production for product K for the next week and states that he has capacity available to produce 300 at a time next week. The following lists the forecasts and actual customer orders for the next 12 weeks. Week 1 2 3 4 5 6 7 8 9 10 11 12 Forecast 90 120 110 80 85 95 100 110 90 90 100 110 Customer Orders 105 97 93 72 98 72 53 21…arrow_forwardBradley Solutions and Alexander Limited are two well-established suppliers of inexpensive tools. Weekend Projects is a national chain of retail outlets that caters to the occasional fixer-upper who would prefer to get the job done fast rather than investing in a well-appointed tool box. Weekend Projects wants to find a supplier for a particular tool set that promises to be a big seller. Expected annual sales are 100,000 units (D). Weekend's warehouses operate 50 weeks a year. Management collected data on the two suppliers, which are contained in the table below: Annual Freight Costs Shipping Quantity (Q) Price/Unit Annual Holding Lead Time (L) (p) $7.15 $7,15 Annual Supplier Bradley Alexander 10,000 25,000 $40.000 $26.000 50,000 $18.000 Cost/Unit (H) (wks) Administrative Cost $15.000 $1.43 $1.43 $30,000 $25,000 $17,000 6 $10,000 a. Which of the two suppliers would provide the lowest annual cost to Weekend Projects? What shipping quantity would you suggest? Using V and a shipping…arrow_forward
arrow_back_ios
SEE MORE QUESTIONS
arrow_forward_ios
Recommended textbooks for you
- Practical Management ScienceOperations ManagementISBN:9781337406659Author:WINSTON, Wayne L.Publisher:Cengage,Operations ManagementOperations ManagementISBN:9781259667473Author:William J StevensonPublisher:McGraw-Hill EducationOperations and Supply Chain Management (Mcgraw-hi...Operations ManagementISBN:9781259666100Author:F. Robert Jacobs, Richard B ChasePublisher:McGraw-Hill Education
- Purchasing and Supply Chain ManagementOperations ManagementISBN:9781285869681Author:Robert M. Monczka, Robert B. Handfield, Larry C. Giunipero, James L. PattersonPublisher:Cengage LearningProduction and Operations Analysis, Seventh Editi...Operations ManagementISBN:9781478623069Author:Steven Nahmias, Tava Lennon OlsenPublisher:Waveland Press, Inc.
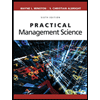
Practical Management Science
Operations Management
ISBN:9781337406659
Author:WINSTON, Wayne L.
Publisher:Cengage,
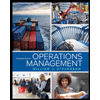
Operations Management
Operations Management
ISBN:9781259667473
Author:William J Stevenson
Publisher:McGraw-Hill Education
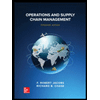
Operations and Supply Chain Management (Mcgraw-hi...
Operations Management
ISBN:9781259666100
Author:F. Robert Jacobs, Richard B Chase
Publisher:McGraw-Hill Education
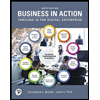
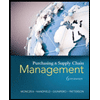
Purchasing and Supply Chain Management
Operations Management
ISBN:9781285869681
Author:Robert M. Monczka, Robert B. Handfield, Larry C. Giunipero, James L. Patterson
Publisher:Cengage Learning
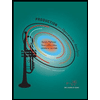
Production and Operations Analysis, Seventh Editi...
Operations Management
ISBN:9781478623069
Author:Steven Nahmias, Tava Lennon Olsen
Publisher:Waveland Press, Inc.