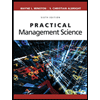
Problem 4 WORKFORCE
Davis Instruments has two manufacturing plants located in Atlanta, Georgia. Product demand varies considerably from month to month, causing Davis extreme difficulty in workforce scheduling. Recently Davis started hiring temporary workers supplied by WorkForce Unlimited, a company that specializes in providing temporary employees for firms in the greater Atlanta area. WorkForce Unlimited offered to provide temporary employees under three contract options that differ in terms of the length of employment and the cost. The three options are summarized:
Option Length of Employment
|
One month |
$2000 |
2 |
Two months |
S4800 |
3 |
Three months |
$7500 |
The longer contract periods are more expensive because WorkForce Unlimited experiences greater difficulty finding temporary workers who are willing to commit to longer work assignments.
Over the next six months, Davis projects the following needs for additional employees:
Month |
January |
February |
March |
April |
May |
June |
Employees Needed |
10 |
23 |
19 |
26 |
20 |
14 |
Each month, Davis can hire as many temporary employees as needed under each of the three options. For instance, if Davis hires five employees in January under Option 2, WorkForce Unlimited will supply Davis with five temporary workers who will work for two months: January and February. For these workers, Davis will have to pay 5($4800) = $24,000. Because of some merger negotiations under way, Davis does not want to commit to any contractual obligations for temporary employees that extend beyond June.
Davis's quality control program requires each temporary employee to receive training at the time Of hire. The training program is required even if the person worked for Davis Instruments in the past. Davis estimates that the cost of training is $875 each time a temporary employee is hired. Thus, if a temporary employee is hired for one month, Davis will incur a training cost of $875, but will incur no additional training cost if the employee is on a two- or three-month contract.
Simply develop and solve a model that can be used to determine the number of temporary employees Davis should hire each month under each contract plan in order to meet the projected needs at a minimum total cost.

Trending nowThis is a popular solution!
Step by stepSolved in 3 steps with 4 images

- STOOGE ENTERPRISES Stooge Enterprises (Stooges) manufactures wooden mallets for commercial and residential applications. Stooges landed a major contract as a supplier to Slapsticks, Inc., a leading retailer in several major cities throughout the upper Midwest. Because of the large volume of demand, Stooges has to expand its manufacturing operation to three shifts and hire additional workers. Not long after Stooges began mallets to Slapsticks, it began receiving some complaints about mallet head diameters. This problem was somewhat alarming to Stooges, because its reputation as a high quality manufacturer was the principal reason that it was selected as a supplier to Slapsticks. Stooges placed a great deal of confidence in its manufacturing capability because of its well trained and dedicated employees, and it never felt the need to consider formal process control approaches. In view of the recent complaints, the company president suspected that the expansion to a three-shift…arrow_forwardAIP 6.9 Transfer Prices and Changing from a Cost to a Profit Center LO 2, 5Northern Blue Company has manufacturing plants and retail shops. The retail shops purchase products from the manufacturing plants. Currently, the manufacturing plants are operated as cost centers and only supply the company’s retail shops. The transfer price is cost-based and the retail shops operate as profit centers. The company presidentis considering an increase in manufacturing capacity that will allow sales to customers outside the organization. The president plans to make the manufacturing plants profit centers. Questionsa. Why are the managers of the retail shops unhappy with these new plans?arrow_forwardThe industry in which Morton Company operates is quite sensitive to cyclical movements in the economy. Thus, profits vary considerably from year to year according to general economic conditions. The company has a large amount of unused capacity and is studying ways of improving profits. Required: 1. New equipment has come onto the market that would allow Morton Company to automate a portion of its operations. Variable expenses would be reduced by $8.70 per unit. However, fixed expenses would increase to a total of $642,060 each month. Prepare two contribution format income statements, one showing present operations and one showing how operations would appear if the new equipment is purchased. 2. Refer to the income statements in (1). For the present operations and the proposed new operations, compute (a) the degree of operating leverage, (b) the break-even point in dollar sales, and (c) the margin of safety in dollars and the margin of safety percentage. 3. Refer again to the data in…arrow_forward
- Question: Retail Channel: David can run the business fully online then he does not need to rent the facility. Alternatively, he can run the business in hybrid model (online as well as through traditional brick-and-motor channel). What will be the possible benefits and challenges for Food-Town to take the options (fully online or hybrid)? Can you solve this question for me which is linked with case study? This subject is about RETAIL AND SERVICE LOGISTICS. Please make sure to read the case study. I also provided the case study in image. Please just write in 150 words.arrow_forwardA 126,000 square foot office building in Plano, Texas is fully leased to the Dr. Pepper Snapple Group at a base rent of $2.50 per square foot per month. The building’s expenses total $0.90 per square foot per month and an expense stop in the Dr. Pepper lease is set at $6.00 per square foot per year. What is the annual NOI? a. $3,024,000 b. $3,175,200 c. $3,780,000 d. $2,419,200arrow_forwardRequired information Lyndia Company is a merchandiser that sells a total of 15 products to its customers. The company provided the following information from last year: Selling Price Variable Cost Product 1 Unit Sales per Unit per Unit 9,000 $ 29 $12.95 2 16,500 $ 99 $68.55 3 6,000 $ 85 $42.50 4 19,500 $109 $85.00 5 4,500 $ 19 $ 6.35 6 27,000 $119 7 3,000 $ 39 $92.00 $14.30 8 7,500 $ 79 $33.18 9 9,000 $ 69 $30.36 10 15,000 $.95 $77.60 11 10,500 $ 59 $25.40 12 1,500 $ 65 $29.00 222 13 3,000 $ 44 $12.40 141 6,000 $ 49 $13.48 15 12,000 150,000 $ 89 $61.83 Last year, Lyndia's total fixed expenses and net operating income were $3,000,000 and $1,223,070, respectively. The company would like your assistance in developing some financial projections for this year.arrow_forward
- Describe one of the dimensions of the Big Five Taxonomyarrow_forwardMonth Item 1 Item 2 Item 3 Item 4 1 751 250 666 287 2 741 268 618 352 3 728 289 483 416 4 773 314 375 313 5 718 337 303 359 6 752 367 242 440 7 736 391 210 520 8 768 409 239 391 9 729 433 342 449 10 777 459 396 550 11 748 481 457 650 12 756 500 587 489 Make a demand forecast for the next six periods for each item using any method you wish. What are the differences between qualitative and quantitative types of forecasting methods?arrow_forwardGodaarrow_forward
- STOOGE ENTERPRISES Stooge Enterprises (Stooges) manufactures wooden mallets for commercial and residential applications. Stooges landed a major contract as a supplier to Slapsticks, Inc., a leading retailer in several major cities throughout the upper Midwest. Because of the large volume of demand, Stooges has to expand its manufacturing operation to three shifts and hire additional workers. Not long after Stooges began mallets to Slapsticks, it began receiving some complaints about mallet head diameters. This problem was somewhat alarming to Stooges, because its reputation as a high-quality manufacturer was the principal reason that it was selected as a supplier to Slapsticks. Stooges placed a great deal of confidence in its manufacturing capability because of its well trained and dedicated employees, and it never felt the need to consider formal process control approaches. In view of the recent complaints, the company president suspected that the expansion to a three-shift…arrow_forwardQuestion 3 To keep up with the market demands, Dolphin Technologies allows overtime for each of the two departments. The cost per hour of overtime for the Chip Manufacturing Department is $20, and $12 for Case Fabricating Department. Formulate a linear programming model can be used to determine the optimal production quantities if overtime is made available.arrow_forwardDescribe how the theory of constraints can be used to manage inventory.arrow_forward
- Practical Management ScienceOperations ManagementISBN:9781337406659Author:WINSTON, Wayne L.Publisher:Cengage,Operations ManagementOperations ManagementISBN:9781259667473Author:William J StevensonPublisher:McGraw-Hill EducationOperations and Supply Chain Management (Mcgraw-hi...Operations ManagementISBN:9781259666100Author:F. Robert Jacobs, Richard B ChasePublisher:McGraw-Hill Education
- Purchasing and Supply Chain ManagementOperations ManagementISBN:9781285869681Author:Robert M. Monczka, Robert B. Handfield, Larry C. Giunipero, James L. PattersonPublisher:Cengage LearningProduction and Operations Analysis, Seventh Editi...Operations ManagementISBN:9781478623069Author:Steven Nahmias, Tava Lennon OlsenPublisher:Waveland Press, Inc.
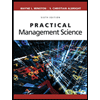
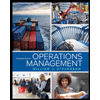
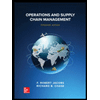
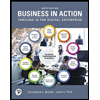
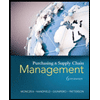
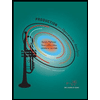