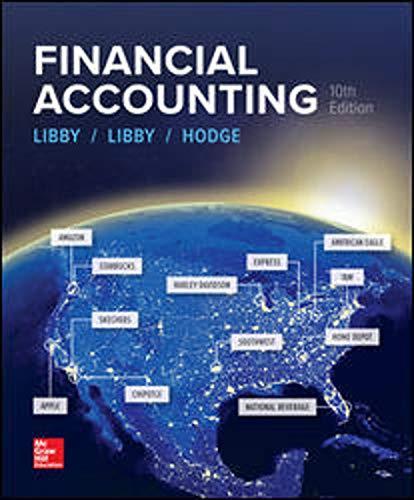
FINANCIAL ACCOUNTING
10th Edition
ISBN: 9781259964947
Author: Libby
Publisher: MCG
expand_more
expand_more
format_list_bulleted
Question
Samantha Ross is the procurement manager for the headquarters of a large Financial company chain with a central inventory operation. Ross’ quick-moving inventory item has a demand of 7,000 units per year. Each unit cost $120, and the inventory holding cost is $15 per unit per year. The average ordering cost is $31 per order. It takes about 6 days for an order to arrive. (This is a corporate operation, and there are 250 working days per year.)
a) What is the annual cost of ordering and holding inventory?
b) Including the cost of the 7,000 units. What is the total annual inventory cost?
c) What is the total annual cost?
Expert Solution

This question has been solved!
Explore an expertly crafted, step-by-step solution for a thorough understanding of key concepts.
This is a popular solution
Trending nowThis is a popular solution!
Step by stepSolved in 4 steps

Knowledge Booster
Learn more about
Need a deep-dive on the concept behind this application? Look no further. Learn more about this topic, accounting and related others by exploring similar questions and additional content below.Similar questions
- Elliott, Inc., has four salaried clerks to process purchase orders. Each clerk is paid a salary of $25,750 and is capable of processing as many as 6,500 purchase orders per year. Each clerk uses a PC and laser printer in processing orders. Time available on each PC system is sufficient to process 6,500 orders per year. The cost of each PC system is $1,100 per year. In addition to the salaries, Elliott spends $27,560 for forms, postage, and other supplies (assuming 26,000 purchase orders are processed). During the year, 25,350 orders were processed. REQUIRED: 1. Classify the resources associated with purchasing as (1) flexible or (2) committed. 2. Compute the total activity availability, and break this into activity usage and unused activity. 3. Calculate the total cost of resources supplied (activity cost), and break this into the cost of activity used and the cost of unused activity. (a) Suppose that a large special order will cause an additional 500 purchase orders. What purchasing…arrow_forwardNet Steels is a steel manufacturing company. It currently orders 180 metric tons of raw material per order. It was observed that the company often faces stockout. To tackle this issue, the company incorporated a fixed-quantity system (FQS) and collected the following data. The lead time is 2 weeks. Demand Order Cost Item Cost Inventory-Holding Cost 10000 metric tons per year $17000 per order $38000 per year 20 percent per year Assuming there are 50 weeks a year, determine the reorder point. Only for non-integer results, round your answer UP to the nearest integer. For example, if your answer is 5.05, type 6; if your answer is 5, type 5. 2DCO Economic Order Quantity (EOQ), Q* = Cn Reorder point, r = demand rate x lead time Your Answer: Answerarrow_forwardYou work for a firm of management consultants that offers assistance to new businesses. One of your clients is Blossom Manufacturing, a company that manufactures a small, but vital, component for the specialized lighting industry. Blossom is a new company (and a new client for your employer) and you have been assigned the task of advising it of its options for financing its inventory during the first few months. The marketing experts have told you that Blossom should have at least three months of inventory on hand so it can meet all demands from its customers. The annual production of the Blossom component is projected to be 140,400 units. Annual direct labour and direct material costs together are estimated at $351,000 per year. Variable manufacturing costs are estimated to be $210,600 per year; fixed manufacturing costs are projected to be $585,000 per year. Fixed marketing and administration costs are estimated at $819,000 per year. These projections are all for the company's first…arrow_forward
- A book publishing company is planning its inventory. The cost to store one book is $4 per month. The cost for a production run is $8 per run and $0.50 per book. The company sells 3,600 books per month. How many should be in a production run to minimize inventory costs?arrow_forwardDiagnostic Supplies has expected sales of 98,000 units per year, carrying costs of $5 per unit, and an ordering cost of $8 per order. a. What is the economic ordering quantity? Economic ordering quantity b-1. What is the average inventory? Average inventory b-2. What is the total carrying cost? Total carrying cost units unitsarrow_forwardIguana, Inc., manufactures bamboo picture frames that sell for $30 each. Each frame requires 4 linear feet of bamboo, which costs $2.50 per foot. Each frame takes approximately 30 minutes to build, and the labor rate averages $12 per hour. Iguana has the following inventory policies: Ending finished goods inventory should be 40 percent of next month’s sales. Ending direct materials inventory should be 30 percent of next month’s production. Expected unit sales (frames) for the upcoming months follow: March 280 April 260 May 310 June 410 July 385 August 435 Variable manufacturing overhead is incurred at a rate of $0.40 per unit produced. Annual fixed manufacturing overhead is estimated to be $7,800 ($650 per month) for expected production of 3,000 units for the year. Selling and administrative expenses are estimated at $700 per month plus $0.50 per unit sold. Iguana, Inc., had $10,900 cash on hand on April 1. Of its sales, 80 percent is in cash. Of the credit…arrow_forward
- Quick-Copy Duplicating Company uses 110,000 reams of standard-size paper a year at its various duplicating centers. Its current paper supplier charges $2.00 per ream. Annual inventory carrying costs are 15 percent of inventory value. The costs of placing and receiving an order of paper are $41.25. Assuming that inventory replenishment occurs virtually instantaneously, determine the following: a. The firm's EOQ b. The total annual inventory costs of this policy c. The optimal ordering frequency d. Compute and plot ordering costs, carrying costs, and total inventory costs for order quantities of 2,000, 4,000, 5,000, 5,500, 6,000, 7,000, and 9,000 reams. Connect the points on each function with a smooth curve, and determine the EOQ from the graph (and the table used in constructing the graph).arrow_forwardIguana, Inc., manufactures bamboo picture frames that sell for $25 each. Each frame requires 4 linear feet of bamboo, which costs $2.50 per foot. Each frame takes approximately 30 minutes to build, and the labor rate averages $14 per hour. Iguana has the following inventory policies: • Ending finished goods inventory should be 40 percent of next month's sales. Ending direct materials inventory should be 30 percent of next month's production. Expected unit sales (frames) for the upcoming months follow: March April May June July August 315 330 380 480 455 505 Variable manufacturing overhead is incurred at a rate of $0.60 per unit produced. Annual fixed manufacturing overhead is estimated to be $7,200 ($600 per month) for expected production of 3,000 units for the year. Selling and administrative expenses are estimated at $650 per month plus $0.50 per unit sold. Iguana, Inc., had $11,000 cash on hand on April 1. Of its sales, 80 percent is in cash. Of the credit sales, 50 percent is…arrow_forward
arrow_back_ios
arrow_forward_ios
Recommended textbooks for you
- AccountingAccountingISBN:9781337272094Author:WARREN, Carl S., Reeve, James M., Duchac, Jonathan E.Publisher:Cengage Learning,Accounting Information SystemsAccountingISBN:9781337619202Author:Hall, James A.Publisher:Cengage Learning,
- Horngren's Cost Accounting: A Managerial Emphasis...AccountingISBN:9780134475585Author:Srikant M. Datar, Madhav V. RajanPublisher:PEARSONIntermediate AccountingAccountingISBN:9781259722660Author:J. David Spiceland, Mark W. Nelson, Wayne M ThomasPublisher:McGraw-Hill EducationFinancial and Managerial AccountingAccountingISBN:9781259726705Author:John J Wild, Ken W. Shaw, Barbara Chiappetta Fundamental Accounting PrinciplesPublisher:McGraw-Hill Education
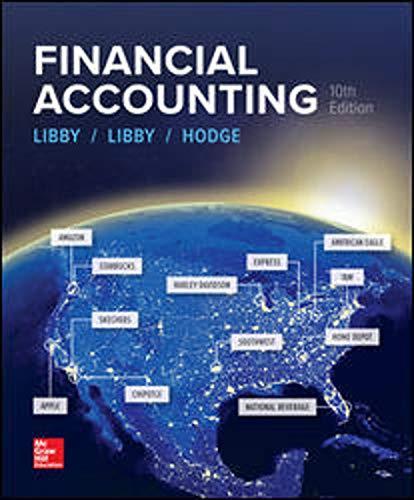
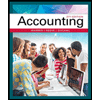
Accounting
Accounting
ISBN:9781337272094
Author:WARREN, Carl S., Reeve, James M., Duchac, Jonathan E.
Publisher:Cengage Learning,
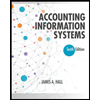
Accounting Information Systems
Accounting
ISBN:9781337619202
Author:Hall, James A.
Publisher:Cengage Learning,
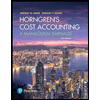
Horngren's Cost Accounting: A Managerial Emphasis...
Accounting
ISBN:9780134475585
Author:Srikant M. Datar, Madhav V. Rajan
Publisher:PEARSON
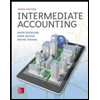
Intermediate Accounting
Accounting
ISBN:9781259722660
Author:J. David Spiceland, Mark W. Nelson, Wayne M Thomas
Publisher:McGraw-Hill Education
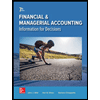
Financial and Managerial Accounting
Accounting
ISBN:9781259726705
Author:John J Wild, Ken W. Shaw, Barbara Chiappetta Fundamental Accounting Principles
Publisher:McGraw-Hill Education