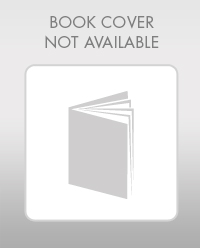
Ross White's machine shop uses 2,500 brackets during the course of a year, and this usage is relatively constant throughout the year. These brackets are purchased from a supplier 100 miles away for $15 each, and the lead time is 2 days. The holding cost per bracket per year is $1.50 (or 10% of the unit cost) and the ordering cost per order is $18.75. There are 250 working days per year.
Required:
(a). What is the EOQ?
( b.) Given the EOQ, what is the average inventory? What is the annual inventory holding costs?
( c). In minimizing cost, how many orders would be made each year? What would be the annual ordering cost?
( d). Given the EOQ, what is the total annual inventory cost, including purchase cost?
( e). What is the time between orders?
( f). What is the reorder point, ROP?

Trending nowThis is a popular solution!
Step by stepSolved in 4 steps with 6 images

- A local toolmaker makes the best hammers on the market. The head of the hammer costs $19.75 and the handle costs $3.52. It takes 1.4 minutes to assemble the hammer and the hourly cost is $73 for assembly time. The company has fixed operating costs of $27746 per month. They sell the hammers for three times their total variable cost. The company wants to make a monthly profit of $14085. How many hammers must they sell? Round to the nearest whole number Answer:arrow_forwardA firm orders on average 400 wheels each month. Demand is normally distributed with standard deviation of the monthly demand being 20 wheels. The ordering cost is $8 per order. The cost to buy one wheel is $4 per wheel. Annual carrying costs are 50% of unit cost. The supplier lead time is 2 operating days. The firm operates 240 days per year, in other word, the firm operates 20 days each month. Each order is received from the supplier in a single delivery. There are no quantity discounts. Write your answer and then Round your answer up to the nearest number for future calculation. (e.g 9.6 => 10). Please clearly write down the formulation and calculation for your answers. Note: Here I make the time measures bolded for you to make you pay the attention to their differences. Please notice the difference in times measure units, so that you do not make mistake by doing calculations with different time measures. You need to convert the data to the same time measures before doing any…arrow_forwardPLEASE MAKE IT IN EXCEL AND SHOW THE FORMULAS Comercial El Alacrán, S.A., purchases 200,000 units per year of the only product it sells. The cost of each order is $35.00. The annual unit maintenance cost is 23% of its cost of $8.00. The supplier currently takes 5.5 days to deliver, and the company sorts and stores it in 3 days. The company makes significant efforts to shorten these lead times. If it manages to reduce, through an agreement with the supplier, its delivery time to 3.5 days and to do the sorting in 1.5 days, how many units does the decrease in the reorder point amount to?arrow_forward
- ABC company uses 8,000 pens every year. For each pen, cach order cost is $30 and the annual holding cost is 10 per cent of unit cost. The unit cost depends on the quantity ordered as follows: Quantity 1-199 Unit Cost (S) 20 200-499 18 500-799 16 800+ 12 > Assume that demand has a constant rate and do not stockout; a) What is the optimal order size? b) Determine the yearly order quantityarrow_forwardABC Corporation resells one type of candle. It has 250 working days. Each day, it sells an average of 500 boxes but may sometimes sell a maximum of 600 boxes. The supplier takes an average of 5 days to deliver the order. During busier times, the supplier may take 7 days.Based on ABC’s records, ordering cost average P400 per order. Storage cost per box average P5 per year. There is also an opportunity cost of 1% per year for every peso invested in inventories. Each box of candles costs P450.If ABC would continue its current inventory management policy, it would keep 10,000 boxes as safety stock and order tendays-worth of inventory.(A) Reorder Point1. What should be the reorder point in boxes?2. How much would the normal lead time usage be?3. How much should ABC keep as safety stock?arrow_forwardAl Khaleej Inc. needs 400 kgs of a material per month. It costs RO 100 to make and receive an order, and it takes 12 workdays to receive it Ihe annual holding cost is 15 % of purchase price. The price RO 1 per kg. The company is operating 6 workdays per week in a 52-week year. At what quantity in kgs you may place a new order? Round-up to the nearest integer Select one: O a. 185 O b. 247 Oc 2// Od. 154 O e. None is correctarrow_forward
- Essentials Of InvestmentsFinanceISBN:9781260013924Author:Bodie, Zvi, Kane, Alex, MARCUS, Alan J.Publisher:Mcgraw-hill Education,
- Foundations Of FinanceFinanceISBN:9780134897264Author:KEOWN, Arthur J., Martin, John D., PETTY, J. WilliamPublisher:Pearson,Fundamentals of Financial Management (MindTap Cou...FinanceISBN:9781337395250Author:Eugene F. Brigham, Joel F. HoustonPublisher:Cengage LearningCorporate Finance (The Mcgraw-hill/Irwin Series i...FinanceISBN:9780077861759Author:Stephen A. Ross Franco Modigliani Professor of Financial Economics Professor, Randolph W Westerfield Robert R. Dockson Deans Chair in Bus. Admin., Jeffrey Jaffe, Bradford D Jordan ProfessorPublisher:McGraw-Hill Education
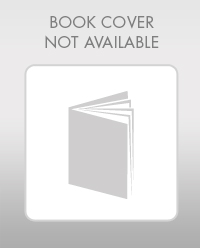
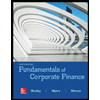
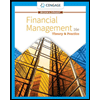
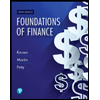
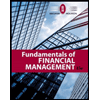
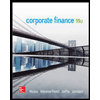