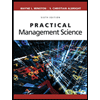
Practical Management Science
6th Edition
ISBN: 9781337406659
Author: WINSTON, Wayne L.
Publisher: Cengage,
expand_more
expand_more
format_list_bulleted
Question
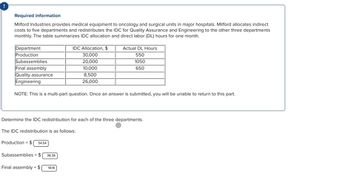
Transcribed Image Text:Required information
Milford Industries provides medical equipment to oncology and surgical units in major hospitals. Milford allocates indirect
costs to five departments and redistributes the IDC for Quality Assurance and Engineering to the other three departments
monthly. The table summarizes IDC allocation and direct labor (DL) hours for one month.
Department
Production
Subassemblies
Final assembly
Quality assurance
Engineering
NOTE: This is a multi-part question. Once an answer is submitted, you will be unable to return to this part.
Determine the IDC redistribution for each of the three departments.
The IDC redistribution is as follows:
Production = $ 54.54
Subassemblies = $
IDC Allocation, $
30,000
20,000
10,000
8,500
26,000
Final assembly = $
36.36
Actual DL Hours
550
1050
650
18.18
Expert Solution

This question has been solved!
Explore an expertly crafted, step-by-step solution for a thorough understanding of key concepts.
This is a popular solution
Trending nowThis is a popular solution!
Step by stepSolved in 3 steps

Follow-up Questions
Read through expert solutions to related follow-up questions below.
Follow-up Question
54.54 is not correct
Solution
by Bartleby Expert
Follow-up Questions
Read through expert solutions to related follow-up questions below.
Follow-up Question
54.54 is not correct
Solution
by Bartleby Expert
Knowledge Booster
Similar questions
- Requirements: • Find Current R1 and R2 And find the voltage in R3 Apply this theorem to find above 4. Norton’sarrow_forwardFanning Company and Finch Company both apply overhead to the Work in Process Inventory account using direct labor hours. The following information is available for both companies for the year. Actual manufacturing overhead Actual direct labor hours Underapplied overhead Overapplied overhead) Required Fanning Company Finch Company $ 145,750 $ 261,600 23,000 27,000 10,500 $ 21,000 a. Compute the predetermined overhead rate for each company. b. Using T-accounts, record the entry to close the overapplied or underapplied overhead at the end of the accounting period for each company, assuming the amounts are immaterial.arrow_forwardQ4 Costs: LayoffHiringInventory Totals: 246 246 30,000 Costs: $246,000 $492,000 $30,000 Cost of plan:$768,000 Planning values Starting inventory: 2,500 Starting and ending workforce: 200 Hours worked per month per hour: 360 Hours per unit: 40 Hiring cost per worker: $2,000 Layoff cost per worker: $1,000 Monthly per-unit holding cost: $1 Forecasted sales:Month Forecasted salesMarch 1,827April 1,620May 1,440June 1,179July 1,611August 2,115September 2,637October 2,502November 3,150December 3,231January 2,826February 2,331arrow_forward
- If 10 pallets are received each 8-hour day, what is the average number of pallets in the system on any given day? Stocking 9 persons 1. 5 hpp S/R Cycle Count person 0.5 hrs/pallet (hpp) Pricing 2 persons 1.25 hpp 1 person 0.25 hpp Spotting 1 persons 0.2 hpp O 10 pallets O 4.713 pallets O 4.375 pallets O125 pallets O Impossible to determinearrow_forward• 1An advantage of a make-to-stock process is which of the following? o It responds directly to customer orderso It allows the firm to avoid inventory costso Rapid delivery of a standard producto All units of output are uniqueCorrect• 2According to Little’s law, which of the following can be used to estimate inventory?o Set up time times throughput rateo Process time times cycle timeo Process velocity times flow timeo Throughput rate times flow timeCorrect• 3Which of the following is a principle of reengineering? o Integrate the outcomes of parallel activitieso Organize around the taskso Treat geographically dispersed resources as though they were centralizedo Capture information many times, at the source and where it is interpretedCorrect• 4Which of the following is one of the major types of stakeholders impacted by most consulting projects?o International government regulatorso Other consultantso…arrow_forward• What is the Reorder Point (ROP)? • What is the fill rate? What is the average inventory? • What is the average flow time? Given Data: Coefficient of variation (CV) = 0.24 Average weekly demand = 540 units Standard deviation = 130 units Lead time=2 Lot size = 1641 Safety inventory: NORMSINV(0.95) = 1.64 Standard deviation * sqrt(2) * 1.64 130*√√2*1.64 301.51 301 = 301 unitsarrow_forward
- Complete the master production schedule (enter your responses as whole numbers). On-hand inventory at end of week 1: 190 Week Forecasted demand Booked orders Projected ending inventory Master production schedule Available to promise 2 280 125 680 770 3 400 170 280 4 290 265 640 650 5 250 150 390 6 260 265 965 840 7 250 240 715 8 290 125 1295 870 555 9 310 190 985arrow_forwardpls some assistance :((arrow_forwardII. Financial information of the business which produces and sells three types of electronical motors is given below: Production Sale Direct Model Quantity (U) Price ($) Material($) Norm 5.000 800 120 Pluger 4.000 1.500 450 Elevator 1.000 2.500 700 Direct Production Labor ($) Time (DLH/U) 80 250 300 4 5 8 Total fixed costs are only 1.750.000$. a. Calculate the BEP for each model, b. Choose the model to prioritize with reasons, c. Compute the common BEP of all models, d. Compute the profit if all the capacity is sold, e. Compute the sale price of each model to get a profit of 5.150.000$.arrow_forward
- When evaluating sales revenue which critical factor(s) must be considered? a) Number of operating meal periods or days b) Changes in menu prices, guest counts, and check averages c) Special events d) All of the abovearrow_forwardwhat is the purpose of the class diagram?arrow_forwardA bagel store orders cream cheese from three suppliers, Cheesy Cream Corp. (CCC), Super Smooth & Sons (SSS), and Bagel's Best Friend Co. (BBF). One month, the total order of cheese came to 100 tons. (The store does do a booming trade.) The costs were $80, $50 and $65 per ton from the three suppliers respectively, with the total cost amounting to $6,710. Given that the store ordered the same amount from CCC and BBF, how many tons of cream cheese were ordered from each supplier? Cheesy Cream Corp.____ tons Super Smooth & Sons ____tons Bagel's Best Friend Co. _____tonsarrow_forward
arrow_back_ios
SEE MORE QUESTIONS
arrow_forward_ios
Recommended textbooks for you
- Practical Management ScienceOperations ManagementISBN:9781337406659Author:WINSTON, Wayne L.Publisher:Cengage,Operations ManagementOperations ManagementISBN:9781259667473Author:William J StevensonPublisher:McGraw-Hill EducationOperations and Supply Chain Management (Mcgraw-hi...Operations ManagementISBN:9781259666100Author:F. Robert Jacobs, Richard B ChasePublisher:McGraw-Hill Education
- Purchasing and Supply Chain ManagementOperations ManagementISBN:9781285869681Author:Robert M. Monczka, Robert B. Handfield, Larry C. Giunipero, James L. PattersonPublisher:Cengage LearningProduction and Operations Analysis, Seventh Editi...Operations ManagementISBN:9781478623069Author:Steven Nahmias, Tava Lennon OlsenPublisher:Waveland Press, Inc.
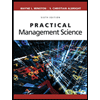
Practical Management Science
Operations Management
ISBN:9781337406659
Author:WINSTON, Wayne L.
Publisher:Cengage,
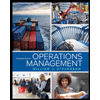
Operations Management
Operations Management
ISBN:9781259667473
Author:William J Stevenson
Publisher:McGraw-Hill Education
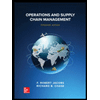
Operations and Supply Chain Management (Mcgraw-hi...
Operations Management
ISBN:9781259666100
Author:F. Robert Jacobs, Richard B Chase
Publisher:McGraw-Hill Education
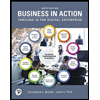
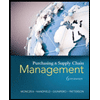
Purchasing and Supply Chain Management
Operations Management
ISBN:9781285869681
Author:Robert M. Monczka, Robert B. Handfield, Larry C. Giunipero, James L. Patterson
Publisher:Cengage Learning
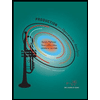
Production and Operations Analysis, Seventh Editi...
Operations Management
ISBN:9781478623069
Author:Steven Nahmias, Tava Lennon Olsen
Publisher:Waveland Press, Inc.