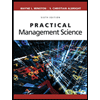
Practical Management Science
6th Edition
ISBN: 9781337406659
Author: WINSTON, Wayne L.
Publisher: Cengage,
expand_more
expand_more
format_list_bulleted
Question
PROBLEM 8
Jim Huang and Roderick Wheeler were sales representatives in a computer store at a shopping mall in
Arlington, Virginia, when they got the idea of going into business in the burgeoning and highly
competitive microcomputer market. Jim went to Taiwan over the summer to visit relatives and made
a contact with a new firm producing display monitors for microcomputers, which was looking for an East Coast distributor in America. Jim made a tentative deal with the firm to supply a maximum of 500
monitors per month and called Rod to see if he could find a building they could operate out of and
some potential customers.
Rod went to work. The first thing he did was send bids to several universities in Maryland, Virginia,
and Pennsylvania for contracts as an authorized vendor for monitors at the schools. Next, he started
looking for a facility to operate from. Jim and his operation would provide minor physical modifications
to the monitors, including some labeling, testing, packaging, and then storage in preparation for
shipping. He knew he needed a building with good security, air-conditioning, and a loading dock.
However, his search proved to be more difficult than he anticipated. Building space of the type and
size he needed was very limited in the area and very expensive. Rod began to worry that he would not
be able to find a suitable facility at all. He decided to look for space in the Virginia and Maryland
suburbs and countryside; and although he found some good locations, the shipping costs out to those
locations were extremely high.
Disheartened by his lack of success, Rod sought help from his sister-in-law Miriam, a local real estate
agent. Rod poured out the details of his plight to Miriam over dinner at Rod’s mother’s house, and she
was sympathetic. She told Rod that she owned a building in Arlington that might be just what he was
looking for, and she would show it to him the next day. As promised, she showed him the ground floor
of the building, and it was perfect. It had plenty of space, good security, and a nice office; furthermore,
it was in an upscale shopping area with lots of good restaurants. Rod was elated; it was just the type
of environment he had envisioned for them to set up their business in. However, his joy soured when
he asked Miriam what the rent was. She said she had not worked out the details, but the rent would
be around $100,000 per year. Rod was shocked, so Miriam said she would offer him an alternative: a
storage fee of $10 per monitor for every monitor purchased and in stock the first month of operation,
with an increase of $2 per month per unit for the remainder of the year. Miriam explained that based
on what he told her about the business, they would not have any sales until the universities opened
around the end of August or the first of September, and that their sales would fall off to nothing in
May or June. She said her offer meant that she would share in their success or failure. If they ended
up with some university contracts, she would reap a reward along with them; if they did not sell many
monitors, she would lose on the deal. But in the summer months after school ended, if they had no
monitors in stock, they would pay her nothing.
Rod mulled this over, and it sounded fair. He loved the building. Also, he liked the idea that they would
not be indebted for a flat lease payment and that the rent was essentially on a per-unit basis. If they
failed, at least they would not be stuck with a huge lease. So he agreed to Miriam’s offer.
When Jim returned from Taiwan, he was skeptical about Rod’s lease arrangement with Miriam. He
was chagrined that Rod hadn’t performed a more thorough analysis of the costs, but Rod explained
that it was pretty hard to do an analysis when he did not know their costs, potential sales, or selling
price. Jim said he had a point, and his concern was somewhat offset by the fact that Rod had gotten
contracts with five universities as an authorized vendor for monitors at a selling price of $180 per unit.
So the two sat down to begin planning their operation.
First, Jim said he had thought of a name for their enterprise, Hawk Systems, Inc., which he said stood
for Huang and Wheeler Computers. When Rod asked how Jim got a k out of computers, Jim cited
poetic license.
Jim said that he had figured that the total cost of the units for them—including the purchase of the
units, shipping, and their own material, labor, and administrative costs—would be $100 per unit
during the first 4 months but would then drop to $90 per month for the following 4 months and, finally,
to $85 per month for the remainder of the year. Jim said that the Taiwan firm was anticipating being
able to lower the purchase price because its production costs would go down as it gained experience.
Jim thought their own costs would go down, too. He also explained that they would not be able to
return any items, so it was important that they develop a good order plan that would minimize costs. This was now much more important than Jim had originally thought because of their peculiar lease
arrangement based on their inventory level. Rod said that he had done some research on past
computer sales at the universities they had contracted with and had come up with the following sales
forecast for the next 9 months of the academic year (from September through May):
September 340
October 650
November 420
December 200
January 660
February 550
March 390
April 580
May 120
Rod explained to Jim that computer equipment purchases at universities go up in the fall, then drop
until January, and then peak again in April, just before university budgets are exhausted at the end of
the academic year.
Jim then asked Rod what kind of monthly ordering schedule from Taiwan they should develop to meet
demand while minimizing their costs. Rod said that it was a difficult question, but he remembered that
when he was in college in a management science course, he had seen a production schedule
developed using a transportation model. Jim suggested he get out his old textbook and get busy, or
they would be turning over all their profits to Miriam.
However, before Rod was able to develop a schedule, Jim got a call from the Taiwan firm, saying that
it had gotten some more business later in the year and it could no longer supply up to 500 units per
month. Instead, it could supply 700 monitors for the first 4 months and 300 for the next 5. Jim and
Rod worried about what this would do to their inventory costs.
Required:
A. Formulate and solve a transportation model to determine an optimal monthly ordering and
distribution schedule for Hawk Systems that will minimize costs.
B. If Hawk Systems has to borrow approximately $200,000 to start up the business, will it end up
making anything the first year?
C. What will the change in the supply pattern from the Taiwan firm cost Hawk Systems?
D. How did Miriam fare with her alternative lease arrangement? Would she have been better off
with a flat $100,000 lease payment?
Expert Solution

This question has been solved!
Explore an expertly crafted, step-by-step solution for a thorough understanding of key concepts.
This is a popular solution
Trending nowThis is a popular solution!
Step by stepSolved in 6 steps

Knowledge Booster
Similar questions
- Answer the given question with a proper explanation and step-by-step solution. Monczka-Trent Shipping is the logistics vendor for Handfield Manufacturing Co. in Ohio. Handfield has daily shipments of a power-steering pump from its Ohio plant to an auto assembly line in Alabama. The value of the standard shipment is $255.930. Monczka-Trent has two options: (1) its standard 2-dav shipment or (2) a subcontractor who will team drive overnight with an effective deliverv of ' dav. The extra driver costs $190. Handfied's holding cost is 35% annuallv for this kind of inventorv. Part A: Alternative 2 is more economical, with a daily cost of $_____ . (Enter your response as a whole number.)arrow_forwardYou are a Supply Chain Procurement Manager working for a large manufacturing company located in North America. Recently, you have found out that one of your suppliers is in contravention of your company’s standards of engagement because they are employing persons aged 14 to 16 years of age. Whilst you would prefer to end the business relationship with this supplier immediately, you have to weigh up the ethical issues with the commercial considerations including; the low cost of the supplies and the history of reliability of delivery from this supplier. Required: Based on your knowledge of corporate social responsibility, as well as supply chain logistics, what is the best course of action in this situation? Discuss.arrow_forwardA cattle producer purchased an insurance contract form the USDA Risk Management Agency. The contract pays a fixed dollar amount if and only if the rainfall in the 10 by 10 miles grid surrounding the producer’s land falls below 90 percent of the historical average rainfall. According to the lecture, this is a type of _____ insurance A cattle producer purchased an insurance contract form the USDA Risk Management Agency. The contract pays a fixed dollar amount if and only if the rainfall in the 10 by 10 miles grid surrounding the producer’s land falls below 90 percent of the historical average rainfall. According to the lecture, this is a type of _____ insurance weather pure parametric aggregate loss index parametric indexarrow_forward
- Suppose you have a newly booming culinary business based in the heart of Johannesburg. As a result, you want to make use of Mr. Delivery’s services to deliver your home‐cooked meals to the surrounding areas. Use the below guidelines for purchasing services and explain how you would use these guidelines to assist you in your use of Mr. Delivery’s services. 1. Have policy on compliance 2. Have a clearly defined scope of work 3. Establishe a suitable organisational struarrow_forwardISO 27002 Supplier Relationships (Section 15) was added in the 2013 version. Discuss your opinion with a real example of why this section was added? Please clear and correct answer. Please don't copy the answer from another student. The subject is IT Security and Policies.arrow_forwardAll of the following are advantages to contracting except: a. Reducing income riskb. Assuring a market for a commodityc. Eliminating default risk of a single buyerd. Ensuring and rewarding for qualityarrow_forward
- Mr. Dan Stockman is the procurement manager for Slicker Image (SI), an upscale retailer of novelty products. It is mid-August, and Mr. Stockman is wondering how many units of a new multi-function smart bracelet to order for the upcoming holiday season (November and December). The Malaysian manufacturer of this item, TechToys, requires orders to be placed in late August for delivery in late October, in time for holiday sales. Based on past experience with similar products, Mr. Stockman believes that the holiday demand (Nov-Dec) for the bracelet is Normally distributed with a mean of 3,000 units and standard deviation of 900. TechToys sells the item to SI at a unit price of $ 145 per unit, and SI has decided to set the retail price at $ 200 during the regular selling season (Nov-Dec). At the end of December, SI will mark down the price by 50% (i.e., sell the item for $ 100) to sell off any left-over items. TechToys incurs a cost of $ 105 per unit to manufacture this bracelet. For…arrow_forward1. Explain 4 reasons why a firm would consider Enterprise Resource Planning System as part of its operations. 2. Information flow in the logistics function is critical. Explain 4 implications of the use of ICT to enhance information flow. 3. Under what circumstance is competitive tendering inappropriate for procuring goods and services?arrow_forwardWhich aspects of IT security would you expect to be incorporating into an IT procurement plan? a. Penetration testing, System hardness, Physical access b. Authorisation, Authentication and Audit expectations c. Anti-virus, Access controls, Password expiry d. You wouldn't consider security in procurement because it is a different issue entirelyarrow_forward
arrow_back_ios
arrow_forward_ios
Recommended textbooks for you
- Practical Management ScienceOperations ManagementISBN:9781337406659Author:WINSTON, Wayne L.Publisher:Cengage,Operations ManagementOperations ManagementISBN:9781259667473Author:William J StevensonPublisher:McGraw-Hill EducationOperations and Supply Chain Management (Mcgraw-hi...Operations ManagementISBN:9781259666100Author:F. Robert Jacobs, Richard B ChasePublisher:McGraw-Hill Education
- Purchasing and Supply Chain ManagementOperations ManagementISBN:9781285869681Author:Robert M. Monczka, Robert B. Handfield, Larry C. Giunipero, James L. PattersonPublisher:Cengage LearningProduction and Operations Analysis, Seventh Editi...Operations ManagementISBN:9781478623069Author:Steven Nahmias, Tava Lennon OlsenPublisher:Waveland Press, Inc.
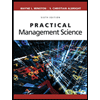
Practical Management Science
Operations Management
ISBN:9781337406659
Author:WINSTON, Wayne L.
Publisher:Cengage,
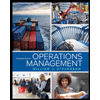
Operations Management
Operations Management
ISBN:9781259667473
Author:William J Stevenson
Publisher:McGraw-Hill Education
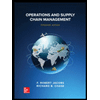
Operations and Supply Chain Management (Mcgraw-hi...
Operations Management
ISBN:9781259666100
Author:F. Robert Jacobs, Richard B Chase
Publisher:McGraw-Hill Education
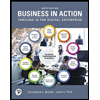
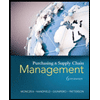
Purchasing and Supply Chain Management
Operations Management
ISBN:9781285869681
Author:Robert M. Monczka, Robert B. Handfield, Larry C. Giunipero, James L. Patterson
Publisher:Cengage Learning
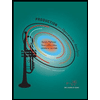
Production and Operations Analysis, Seventh Editi...
Operations Management
ISBN:9781478623069
Author:Steven Nahmias, Tava Lennon Olsen
Publisher:Waveland Press, Inc.