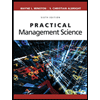
Practical Management Science
6th Edition
ISBN: 9781337406659
Author: WINSTON, Wayne L.
Publisher: Cengage,
expand_more
expand_more
format_list_bulleted
Question
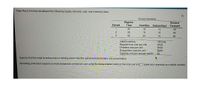
Transcribed Image Text:Ram Roy's firm has developed the following supply, demand, cost, and inventory data.
Supply Available
Regular
Demand
Period
Time
Overtime
Subcontract
Forecast
1.
40
15
10
40
2.
35
15
10
60
3.
30
20
10
50
Initial inventory
Regular-time cost per unit
Overtime cost per unit
Subcontract cost per unit
Carrying cost per unit per month.
20 units
$100
$150
$250
$2
Assume that the initial inventory has no holding cost in the first period and backorders are not permitted.
Allocating production capacity to meet demand at a minimum cost using the transportation method, the total cost is $ (enter your response as a whole number).
Expert Solution

This question has been solved!
Explore an expertly crafted, step-by-step solution for a thorough understanding of key concepts.
Step by stepSolved in 3 steps with 3 images

Knowledge Booster
Similar questions
- Annual demand for squash racquets is 50,000 units, and carrying costs amount to P2 per unit. Order costs for the company amount to P5. The optimum order quantity in units for squash racquets is (rounded to the nearest unit):arrow_forwardObjectives of Inventory Control in Procter & Gamble.arrow_forwardCurrent decision to buy: Ross White's machine shop uses 200 brackets each month during the course of a year. This usage is relatively constant throughout the year. Currently, these brackets are purchased from a supplier 100 miles away for $16 each and the lead time is 2 days. The holding cost per bracket per year is $1.60 (10% of the unit cost) and the annual ordering cost per order is $18.50. There are 240 working days per year. Possible future decision to make in-house: Ross White is reconsidering his decision of buying the brackets and is considering making the brackets in-house. He has determined the set up costs would be $24.50 in machinist time and lost production time. Forty eight brackets could be produced in a day once the machine has been set up. Ross estimates that the cost (including labor and materials) of producing one bracket would be $14.85. The holding cost would be 10% of the cost. a. What is the EOQ given Ross' current decision to buy the brackets? What is the total…arrow_forward
- The maintenance department of a large hospital uses 816 cases of liquid cleaner annually. Ordering costs are $12, carrying costs are $4 per case per year, and the new price schedule indicates that orders of less than 50 cases will cost $20 per case, 50 to 79 cases will cost $18 per case, 80 to 99 cases will cost $17 per case, and larger orders will cost $16 per case. Determine the optimal order quantity and the total costarrow_forwardSuppose that your firm manufactures rubber chickens. Monthly demand for the chickens is 32,000 units. Setup costs per order is $85, and the annual holding cost percentage is 17%. The chickens cost $8 to produce and are sold for $18. a. if you have a warehouse, what is the economic order quantity for the chickens? what is the total of the annual setup and holding cost of this quantity? b. suppose that you have 25 warehouses instead of one, and total demand is equally distributed among the warehouses. If setup and holding costs are the same in the smaller warehouses as they would be for a single large warehousem what is the EOQ for the chickens at each of the 25 warehouses? what is the total of the annual setup and holding costs at each warehouse? what is the total of the company's annual setup and holding costs? c. using centralized warehousing as in part a implies that products must be shipped over longer distances. suppose that shipping costs are $0.80 per unit when using one…arrow_forwardes Garden Variety Flower Shop uses 930 clay pots a month. The pots are purchased at $3.90 each. Annual carrying costs per pot are estimated to be 10 percent of cost, and ordering costs are $10 per order. The manager has been using an order size of 2,000 flower pots. a.What additional annual cost is the shop incurring by staying with this order size? (Round your optimal order quantity to the nearest whole number. Round all other intermediate calculations and your final answer to 2 decimal places.) Additional annual cost b.Other than cost savings, what benefit would using the optimal order quantity yield (relative to the order size of 2,000)? (Use the rounded order quantity from Part a. Round your final answer to the nearest whole percent.) About % of the storage space would be needed. Check myarrow_forward
- Subject: calculusarrow_forwardHi, Pls provide answers. thank you.arrow_forwardCurrent decision to buy: Ross White's machine shop uses 300 brackets each month during the course of a year. This usage is relatively constant throughout the year. Currently, these brackets are purchased from a supplier 100 miles away for $25 each and the lead time is 2 days. The holding cost per bracket per year is $3.75 (15% of the unit cost) and the annual ordering cost per order is $18.50. There are 240 working days per year. Possible future decision to make in-house: Ross White is reconsidering his decision of buying the brackets and is considering making the brackets in-house. He has determined the set up costs would be $22.50 in machinist time and lost production time. Forty eight brackets could be produced in a day once the machine has been set up. Ross estimates that the cost (including labor and materials) of producing one bracket would be $22.85. The holding cost would be 12% of the cost. What is the EOQ given Ross' current decision to buy the brackets? What is the…arrow_forward
- Jean-Marie Bourjolly's restaurant has the following inventory items that it orders on a weekly basis. Fill in the blanks in the following table. Remember that annual dollar volume (not weekly) is requested. The restaurant is open 52 weeks a year. (Round dollar volume to the nearest whole number and percentage of dollar volume to two decimal places.) The class of French fries is The class of Oil is ID Item 1 Rib eye steak 2 3 Pasta 4 Salt 5 Napkins 6 Tomato sauce c) What is the total annual dollar volume for all items? $ Lobster tail (enter you 7 8 Pepper 9 Garlic powder 10 Trash can liners 11 Table cloths 12 Fish filets 13 Prime rib roasts 14 Oil 15 Lettuce (case) 16 Chickens 17 Order pads 18 Eggs (case) 19 Bacon 20 Sugar French fries C ♥ B # Ordered per Cost/Case Week ($) 3 140 245 23 3 12 25 A NOENEN was du w w w 8 N N N N w W a whole number). 3 12 2 12 30 3 3 3 5 10 6 3 24 14 7 2 48 3 11 12 32 143 166 21 35 75 12 22 56 4 4 Annual Dollar Volume a) What is the highest annual dollar…arrow_forwardRam Roy's firm has developed the following supply, demand, cost, and inventory data Period 1 2 3 Regular Time 30 30 40 Supply Available Overtime Subcontract 5 15 15 15 5 5 Demand Forecast 40 20 units $100 $150 $200 $6 45 55 Initial inventory Regular-time cost per unit Overtime cost per unit Subcontract cost per unit Carrying cost per unit per month Assume that the initial inventory has no holding cost in the first period and backorders are not permitted Allocating production capacity to meet demand at a minimum cost using the transportation method, the total cost is $ (enter your response as a whole number)arrow_forwardARP Engines is a producer of outboard motors and ships worldwide. The company has recently set up a new distribution centre and wants to decide on an inventory policy for one of its products. It has determined the following pertinent information: expected average weekly demand weekly demand standard deviation holding cost production setup cost delivery lead time 400 motors 50 motors $25/motor $5,000/order 3 weeks The company plans to operate 5 days per week, 50 weeks per year. a. Compute the Economic Order Quantity (ignore the variation in demand) given the informa- tion gathered by the company. What is the time between orders and the total cost of operating the EOQ inventory policy? b. The company is considering using the EOQ as the order quantity in a continuous review system. Compute the reorder point and safety stock to meet a service level of 99%. What is the cost of this Q system inventory policy? c. If the company thinks to use the TBO (computed in part a) as the period for a…arrow_forward
arrow_back_ios
SEE MORE QUESTIONS
arrow_forward_ios
Recommended textbooks for you
- Practical Management ScienceOperations ManagementISBN:9781337406659Author:WINSTON, Wayne L.Publisher:Cengage,Operations ManagementOperations ManagementISBN:9781259667473Author:William J StevensonPublisher:McGraw-Hill EducationOperations and Supply Chain Management (Mcgraw-hi...Operations ManagementISBN:9781259666100Author:F. Robert Jacobs, Richard B ChasePublisher:McGraw-Hill Education
- Purchasing and Supply Chain ManagementOperations ManagementISBN:9781285869681Author:Robert M. Monczka, Robert B. Handfield, Larry C. Giunipero, James L. PattersonPublisher:Cengage LearningProduction and Operations Analysis, Seventh Editi...Operations ManagementISBN:9781478623069Author:Steven Nahmias, Tava Lennon OlsenPublisher:Waveland Press, Inc.
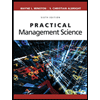
Practical Management Science
Operations Management
ISBN:9781337406659
Author:WINSTON, Wayne L.
Publisher:Cengage,
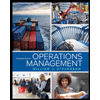
Operations Management
Operations Management
ISBN:9781259667473
Author:William J Stevenson
Publisher:McGraw-Hill Education
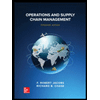
Operations and Supply Chain Management (Mcgraw-hi...
Operations Management
ISBN:9781259666100
Author:F. Robert Jacobs, Richard B Chase
Publisher:McGraw-Hill Education
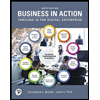
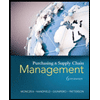
Purchasing and Supply Chain Management
Operations Management
ISBN:9781285869681
Author:Robert M. Monczka, Robert B. Handfield, Larry C. Giunipero, James L. Patterson
Publisher:Cengage Learning
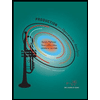
Production and Operations Analysis, Seventh Editi...
Operations Management
ISBN:9781478623069
Author:Steven Nahmias, Tava Lennon Olsen
Publisher:Waveland Press, Inc.