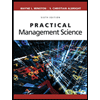
Practical Management Science
6th Edition
ISBN: 9781337406659
Author: WINSTON, Wayne L.
Publisher: Cengage,
expand_more
expand_more
format_list_bulleted
Question
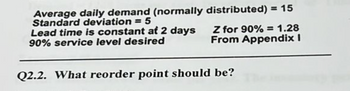
Transcribed Image Text:Average daily demand (normally distributed) = 15
Standard deviation = 5
Lead time is constant at 2 days
90% service level desired
Z for 90% = 1.28
From Appendix I
Q2.2. What reorder point should be?
Expert Solution

This question has been solved!
Explore an expertly crafted, step-by-step solution for a thorough understanding of key concepts.
Step by stepSolved in 3 steps

Knowledge Booster
Similar questions
- Question 3The weekly demand for a product, which is held in stock is always 90 units.When an order for new stock is placed, it is delivered almost instantaneously by an ordering cost of 50,000 is incurred. The product costs 3,000 per unit,and it costs 15 percent of this amount to hold a unit in stock for a year.Currently, orders are placed for 2000 units. There are 50 working weeks in ayear and lead time is one week. a) As a management science student, the MD of the company seeks yourexpert advice on ways in which to determine the economic order quantity,optimal order cycle time, re-order level and total annual inventory cost.Advise the MD, providing detailed explanation using your answer. Writeyour answer in a form of a report to the MD. b) Advise the MD about savings, if any, could be made by changing fromcurrent order quantity of GH¢ 2000 units to the one obtained in (a) above. c) Describe the order policy followed by the firm based on your calculationsarrow_forwardQ 12.30: Alvin's Apple Orchard manages inventory closely to maintain freshness. In the past four years, its current assets have fluctuated with demand and supply of fresh fruits. The following table reproduces selected balance sheet items: 2020 2019 2018 2017 Accounts 10.1% 11.9% 12.1% 12.4% receivable Raw material 7.0% 7.6% 7.8% 8.0% inventory Finished goods 5.2% inventory 4.6% 5.3% 5.4% Alvin's common size analysis shows that A inventory management improved over the period as a result of better control over raw material inventory. В inventory management deteriorated over the five years as a result of poor control over finished raw material inventory. C receivables are becoming easier to collect. inventory management improved over the period as a result of better control over finished goods inventory. Darrow_forwardb. Question 4 Fortis Utility Company uses 2,000 units per year which it stores at $0.50 per unit per annum. The cost to place an order is $100. Calculate: If the company decides to make the items on its own machine with a potential capacity of 4,000 units per year, calculate: i. the batch order quantity (BOQ) the annual ordering cost the annual carrying cost ii. the economic order quantity (EOQ) the number of orders. iii.arrow_forward
- Questions in red 10-12arrow_forwardquestion 3 Sam's Cat Hotel operates 52weeks per year, 5 days per week, and uses a continuous review inventory system. It purchases kitty litter for $10.50 per bag. The following information is available about these bags. Refer to the standard normal table AT END for z-values. ≻Demand= 92 bags/week ≻Order cost =$58/order ≻Annual holding cost =26 percent of cost ≻Desired cycle-service level=99 percent ≻Lead time = 1 week(s) (5 working days) ≻Standard deviation of weekly demand = 20 bags ≻Current on-hand inventory is 310 bags, with no open orders or backorders. a. What is the EOQ? Sam's optimal order quantity is__________ bags. (Enter your response rounded to the nearest whole number.) What would be the average time between orders (in weeks)? The average time between orders is _________weeks. (Enter your response rounded to one decimal place.) b. What should R be? The reorder point is _________ bags. (Enter your response rounded to the…arrow_forwardQUESTION 15 ID-planned order release using EOQ technique Clancy's Motors has the following demand to meet for custom manufactured fuel injector parts. The holding cost for that item is $2 per month and each setup costs $80. Lead time is 0 months. Calculate the planned order releases using: the EOQ technique including the holding cost of any inventory left over after month 7? Month Requirement 1 400 What is the total cost? 2016 2509 1405 1536 2 150 3 200 150 100 150 250arrow_forward
- Question 21 C&A sells T-shirts for $20 that cost $5 to produce. The annual holding cost percentage is 20% and the T-shirts turn 25 times a year. What holding cost does C&A incur for each T-shirt? Group of answer choices $0.50 $0.08 $0.04 $0.02arrow_forward8arrow_forwardInventory is not a property that is acquired for the purpose of resale in a business activity. Question 4 options: True Falsearrow_forward
- Question: How do you use the Silver-Meal ordering policy to find the Total annual Cost for the damand and parameters listed below? Month Period Demand Jan. 1 110 Feb. 2 40 Mar. 3 150 Apr. 4 130 May 5 60 Jun. 6 30 Jul. 7 20 Aug. 8 30 Sep. 9 80 Oct. 10 120 Nov. 11 130 Dec. 12 100 Total 1000 Given cost parameter: Value Order cost $25 Unit cost $8 Holding cost rate (monthly) 5%arrow_forwardQuestion 3 Which of the following Inventory Holding Costs refers to the cost associated with return on the investment in inventory? Service Capital Cost Space Riskarrow_forwardQuestion 5 A company sales product A to its customer. The company forecasts the monthly demand of product A d=11107 units, sa-3099 units. The cost of A is UC=0.11 $/unit, the reorder cost RC = 10 $/order, the holding cost of product A is 20% yearly of its value. The leading time of ordering is constant, LT=1.5 month. The company wants the service level to achieve 75%. Please give the optimal inventory policy for the company. (The reorder quantity and ROL, we have Z=0.67 for SL>=75%)arrow_forward
arrow_back_ios
SEE MORE QUESTIONS
arrow_forward_ios
Recommended textbooks for you
- Practical Management ScienceOperations ManagementISBN:9781337406659Author:WINSTON, Wayne L.Publisher:Cengage,Operations ManagementOperations ManagementISBN:9781259667473Author:William J StevensonPublisher:McGraw-Hill EducationOperations and Supply Chain Management (Mcgraw-hi...Operations ManagementISBN:9781259666100Author:F. Robert Jacobs, Richard B ChasePublisher:McGraw-Hill Education
- Purchasing and Supply Chain ManagementOperations ManagementISBN:9781285869681Author:Robert M. Monczka, Robert B. Handfield, Larry C. Giunipero, James L. PattersonPublisher:Cengage LearningProduction and Operations Analysis, Seventh Editi...Operations ManagementISBN:9781478623069Author:Steven Nahmias, Tava Lennon OlsenPublisher:Waveland Press, Inc.
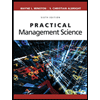
Practical Management Science
Operations Management
ISBN:9781337406659
Author:WINSTON, Wayne L.
Publisher:Cengage,
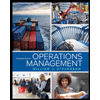
Operations Management
Operations Management
ISBN:9781259667473
Author:William J Stevenson
Publisher:McGraw-Hill Education
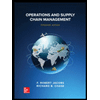
Operations and Supply Chain Management (Mcgraw-hi...
Operations Management
ISBN:9781259666100
Author:F. Robert Jacobs, Richard B Chase
Publisher:McGraw-Hill Education
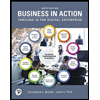
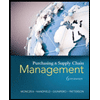
Purchasing and Supply Chain Management
Operations Management
ISBN:9781285869681
Author:Robert M. Monczka, Robert B. Handfield, Larry C. Giunipero, James L. Patterson
Publisher:Cengage Learning
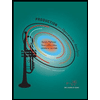
Production and Operations Analysis, Seventh Editi...
Operations Management
ISBN:9781478623069
Author:Steven Nahmias, Tava Lennon Olsen
Publisher:Waveland Press, Inc.