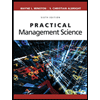
Concept explainers
Product Cost under Full vs. Variable Costing Kate’s Kale Chips produces a healthy snack
made primarily of kale. Each bag of the product sells for $5. The company computes the manufacturing overhead rate on a quarterly basis based upon the planned number of units to be produced that
quarter. The following data are from the projections of Kate’s Kale Chips for the upcoming quarter:
[LO 18-4]
Projections
Sales 20,000 bags
Production 22,000 bags
Variable
Sales and distribution costs per bag $0.15
Total fixed manufacturing overhead $33,000
Fixed administrative overhead $18,000
Required
1. Compute the projected product cost per bag produced under full costing.
2. Compute the projected product cost per bag under variable costing

Trending nowThis is a popular solution!
Step by stepSolved in 3 steps

- If January’s ending inventory is negative 300 or -300, with the cost information shown below, select the correct value for January’s inventory shortage cost. 300 450 -300 150 1,500arrow_forwardDont give me handwritten answer thankuarrow_forwardPLEASE ANSWER BOTH QUESTIONS without excel a) Using a weighted moving average with three periods, determine the demand for period 13. Use 3, 2, and 1 for the weights of the most recent, second most recent, and third most recent periods, respectively b) Find the MAD, MSE and MAPEarrow_forward
- Navajo Company's year-end financial statements show the following. The company recently discovered that in making physical counts of inventory, it had made the following errors: Year 1 ending inventory is understated by $69,000 and Year 2 ending inventory is overstated by $39,000. For Year Ended December 31 (a) Cost of goods sold (b) Net income (c) Total current assets (d) Total equity Year 1 $ 744,000 Year 2 $ 974,000 287,000 1,266,000 1,406,000 294,000 1,379,000 1,599,000 Year 3 $ 809,000 269,000 1,249,000 1,264,000 Required: 1. For each key financial statement figure-(a), (b), (c), and (d) above-prepare a table to show the adjustments necessary to correct the reported amounts. 2. What is the total error in combined net income for the three-year period resulting from the inventory errors? Complete this question by entering your answers in the tabs below. Required 1 Required 2 For each key financial statement figure-(a), (b), (c), and (d) above-prepare a table to show the adjustments…arrow_forwardPlease do not give solution in image format thankuarrow_forwardGive typed full explanationarrow_forward
- Given that: Sales = $300,000,000 Transportation cost = $15,000,000 Warehousing cost = $4,000,000 Inventory carrying cost rate (W) = 30% Cost of goods sold = $95,000,000 Other operating costs = $55,000,000 Average Inventory (AI) = $15,000,000 Accounts receivable = $35,000,000 What is the total operating cost? Group of answer choices 56,500,000 48,500,000 75,500,000 78,500,000 68,500,000arrow_forwardConsider the following information. PART X Gross Requirements Scheduled Receipts Projected On-Hand Inventory 100 Q = 60, LT= 3 weeks, Safety Stock = 5 1 70 70 PART X Gross Requirements Scheduled Receipts Projected On-Hand Inventory 100 Planned Order Releases 1 70 70 100 2 0 > X WEEK 3 40 Compute the planned order releases and projected on-hand inventory for component part X. Round your answers to the nearest whole number. If your answer is zero, enter "0". 2 0 4 0 100 WEEK 3 40 5 160 60 4 0 40 0 X 5 160 Check My Work -60 0arrow_forwardIn your own words, describe how you will use STAR reports to make decisions about room pricing and revenue management.arrow_forward
- Saché, Incorporated, expects to sell 2,030 of its designer suits every week. The store is open seven days a week and expects to sell the same number of suits every day. The company has an EOQ of 1,450 suits and a safety stock of 290 suits. Once an order is placed, it takes three days for Saché to get the suits in. How many orders does the company place per year? (Do not round intermediate calculations and round your answer to 2 decimal places, e.g., 32.16.) Assume that it is Monday morning before the store opens, and a shipment of suits has just arrived. When will Saché place its next order? multiple choice Monday Tuesday Wednesday Thursday Friday Saturday Sundayarrow_forwardFisk Corporation is trying to improve its inventory control system and has installed an online system at its retail stores. Fisk anticipates sales of 58,800 units per year, an ordering cost of $4 per order, and carrying costs of $1.50 per unit. In the second year, Fisk Corporation finds that it can reduce ordering costs to $1 per order, but carrying costs will stay the same at $1.50 per unit. a-1. What is the economic ordering quantity for the second year? Economic ordering quantity (EOQ) a-2. How many orders will be placed during the second year? Number of orders a-3. What will the average inventory be for the second year? Average inventory Total costs units units a-4. What is the total cost of ordering and carrying inventory for second year? LAarrow_forwardInventory Management You are the store manager at a local branch of DigiLife, a large electronics retail chain. A new version of a popular consumer electronics device called the Amulet is coming out this year. It is your job to sell as many Amulets as you can while minimizing your costs in order to maximize your store's profits. Your Goal Earn $1,000,000 in net profits of Amulet sales.arrow_forward
- Practical Management ScienceOperations ManagementISBN:9781337406659Author:WINSTON, Wayne L.Publisher:Cengage,Operations ManagementOperations ManagementISBN:9781259667473Author:William J StevensonPublisher:McGraw-Hill EducationOperations and Supply Chain Management (Mcgraw-hi...Operations ManagementISBN:9781259666100Author:F. Robert Jacobs, Richard B ChasePublisher:McGraw-Hill Education
- Purchasing and Supply Chain ManagementOperations ManagementISBN:9781285869681Author:Robert M. Monczka, Robert B. Handfield, Larry C. Giunipero, James L. PattersonPublisher:Cengage LearningProduction and Operations Analysis, Seventh Editi...Operations ManagementISBN:9781478623069Author:Steven Nahmias, Tava Lennon OlsenPublisher:Waveland Press, Inc.
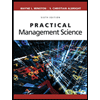
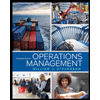
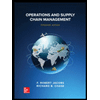
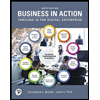
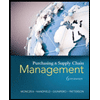
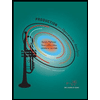