Problem 2. You are supplied with a monthly demand forecast, an organizational policy of requiring 10% of a month's forecast as safety stock, and the number of operating days available each month. There is no inventory available at the beginning of the first month, January. The following table contains the demand requirements. 1. Beginning inventory 2. Forecasted demand 3. Safety Stock 4. 56 5. Production requirements (2+3-1) Operating days 6. Cumulative forecasted demand 7. 8. January 0 10,000 1,000 11,000 22 10,000 Cumulative production 11,000 requirements Cumulative operating days 22 February 1,000 15,000 1,500 3,000 2,700 3,000 March April May June 2,700 3,000 1,500 3,000 30,000 27,000 30,000 16,000 1,600 15,500 31,500 19 21 25,000 55,000 26,500 58,000 41 62 26,700 21 82,000 112,000 84,000 115,000 129,600 30,300 22 83 105 14,600 20 128,000 125
Problem 2. You are supplied with a monthly demand forecast, an organizational policy of requiring 10% of a month's forecast as safety stock, and the number of operating days available each month. There is no inventory available at the beginning of the first month, January. The following table contains the demand requirements. 1. Beginning inventory 2. Forecasted demand 3. Safety Stock 4. 56 5. Production requirements (2+3-1) Operating days 6. Cumulative forecasted demand 7. 8. January 0 10,000 1,000 11,000 22 10,000 Cumulative production 11,000 requirements Cumulative operating days 22 February 1,000 15,000 1,500 3,000 2,700 3,000 March April May June 2,700 3,000 1,500 3,000 30,000 27,000 30,000 16,000 1,600 15,500 31,500 19 21 25,000 55,000 26,500 58,000 41 62 26,700 21 82,000 112,000 84,000 115,000 129,600 30,300 22 83 105 14,600 20 128,000 125
Practical Management Science
6th Edition
ISBN:9781337406659
Author:WINSTON, Wayne L.
Publisher:WINSTON, Wayne L.
Chapter2: Introduction To Spreadsheet Modeling
Section: Chapter Questions
Problem 20P: Julie James is opening a lemonade stand. She believes the fixed cost per week of running the stand...
Related questions
Question

Transcribed Image Text:Problem 2.
You are supplied with a monthly demand forecast, an organizational policy of requiring 10% of a
month's forecast as safety stock, and the number of operating days available each month. There is
no inventory available at the beginning of the first month, January. The following table contains
the demand requirements.
2.
3.
4.
5.
6.
7.
8.
Beginning inventory
Forecasted demand
January
0
10,000
1,000
Safety Stock
Production
requirements (2+3-1)
Operating days
Cumulative forecasted
demand
Cumulative production 11,000
requirements
Cumulative operating
days
11,000
22
10,000
22
February March April May
1,000
1,500
3,000 2,700
15,000
30,000
27,000
30,000
1,500
3,000
2,700
3,000
15,500
19
25,000
31,500 26,700 30,300
21
22
21
82,000 112,000
55,000
26,500 58,000
84,000 115,000 129,600
41
62
83
June
3,000
16,000
1,600
105
14,600
20
128,000
125

Transcribed Image Text:The costs for the organization are as follows:
Manufacturing cost/unit
Inventory holding costª
Hourly wage rate
Stockout cost per unit
Hourly overtime wage rate
Subcontracting cost/unit
Labour hours/unit
Layoff cost/worker
Hiring and training cost/worker
22% of manufacturing cost per month.
Rs.100
Rs.2.00/unit-month
Rs.8.00
Rs.5.00
150%, or Rs.12.00
Rs.104
4 hours
Rs.500
Rs.400
Three potential plans for the production are:
1. Produce to exact production requirements by varying the size of the work force on
regular hours. Assume there are 250 workers available in January.
2. Maintain a constant work force of 518 workers. Assume no subcontracting is available
and inventory will fluctuate with stockouts filled from the following month's production.
3. Produce with a fixed work force of 500 on regular time and subcontract all excess
demand over the period of production. Inventory will increase when production exceeds
demand; no stockouts are permitted.
Expert Solution

This question has been solved!
Explore an expertly crafted, step-by-step solution for a thorough understanding of key concepts.
Step by step
Solved in 5 steps with 6 images

Recommended textbooks for you
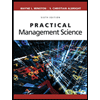
Practical Management Science
Operations Management
ISBN:
9781337406659
Author:
WINSTON, Wayne L.
Publisher:
Cengage,
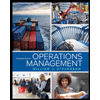
Operations Management
Operations Management
ISBN:
9781259667473
Author:
William J Stevenson
Publisher:
McGraw-Hill Education
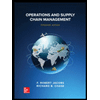
Operations and Supply Chain Management (Mcgraw-hi…
Operations Management
ISBN:
9781259666100
Author:
F. Robert Jacobs, Richard B Chase
Publisher:
McGraw-Hill Education
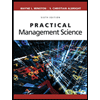
Practical Management Science
Operations Management
ISBN:
9781337406659
Author:
WINSTON, Wayne L.
Publisher:
Cengage,
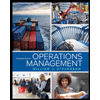
Operations Management
Operations Management
ISBN:
9781259667473
Author:
William J Stevenson
Publisher:
McGraw-Hill Education
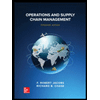
Operations and Supply Chain Management (Mcgraw-hi…
Operations Management
ISBN:
9781259666100
Author:
F. Robert Jacobs, Richard B Chase
Publisher:
McGraw-Hill Education
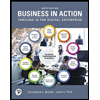
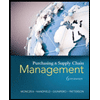
Purchasing and Supply Chain Management
Operations Management
ISBN:
9781285869681
Author:
Robert M. Monczka, Robert B. Handfield, Larry C. Giunipero, James L. Patterson
Publisher:
Cengage Learning
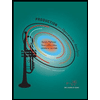
Production and Operations Analysis, Seventh Editi…
Operations Management
ISBN:
9781478623069
Author:
Steven Nahmias, Tava Lennon Olsen
Publisher:
Waveland Press, Inc.