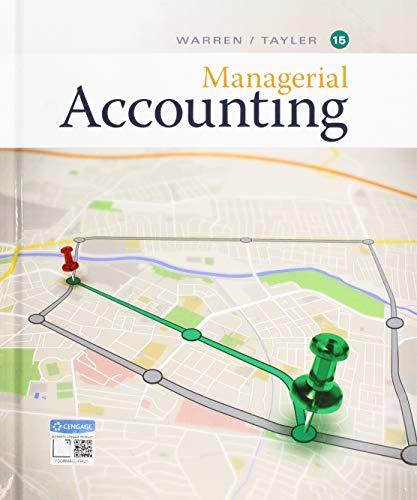
Perfumes Ltd has two divisions: The Perfume Division and the Bottle Division. The company is decentralised, and each division is evaluated as a profit centre. The Bottle Division produces bottles that can be used by the Perfume Division. The Bottle Division's variable
Required
When is it more appropriate to use market-based transfer price rather than cost-based transfer price?

Step by stepSolved in 2 steps

- Perfumes Ltd has two divisions: the Perfume Division and the Bottle Division. The company is decentralised and each division is evaluated as a profit centre. The Bottle Division produces bottles that can be used by the Perfume Division. The Bottle Division's variable manufacturing cost per unit is $3.00 and shipping costs are $0.20 per unit. The Bottle Division's external salesprice is $4.00 per unit. No shipping costs are incurred on sales to the Perfume Division. The Perfume Division can purchase similar bottles in the external market for $3.50.The Bottle Division has sufficient capacity to meet all external market demands in addition to meeting the demands of the Perfume Division. a) Assume the Bottle Division has no excess capacity and can sell everything produced externally. What is the maximum amount Perfume Division would be willing to pay for the bottles? b) When is it more appropriate to use market-based transfer price rather than cost-based transfer price?arrow_forwardFragrance Pty Ltd has two (2) divisions: the Cologne Division and the Bottle Division. The company is de-centralised and each division is evaluated as a profit centre. The Bottle Division produces bottles that can be used by the Cologne Division. The Bottle Division's variable manufacturing cost per unit is $2.00 and shipping costs are $0.10 per unit. The Bottle Division's external sales price is $3.00 per unit. No shipping costs are incurred on sales to the Cologne Division. The Cologne Division can purchase similar bottles in the external market for $2.50. The Bottle Division has sufficient capacity to meet all external market demands in addition to meeting the demands of the Cologne Division. Using the general rule, calculate the minimum transfer price from the Bottle Division to the Cologne Division. Explain your answerarrow_forwardPerfumesLtd has two divisions: the Perfume Division and the Bottle Division. The company is decentralised and each division is evaluated as a profit centre. The Bottle Division produces bottles that can be used by the Perfume Division. The Bottle Division's variable manufacturing cost per unit is $3.00 and shipping costs are $0.20 per unit. The Bottle Division's external sales price is $4.00 per unit. No shipping costs are incurred on sales to the Perfume Division. The Perfume Division can purchase similar bottles in the external market for $3.50.The Bottle Division has sufficient capacity to meet all external market demands in addition to meeting the demands of the Perfume Division. Required: a) Using the general rule, determine the minimum transfer price. b) Assume the Bottle Division has no excess capacity and can sell everything produced externally. Would the transfer price change? c) Assume the Bottle Division has no excess capacity and can sell everything produced externally.…arrow_forward
- Bath Bath Co is a company specialising in the manufacture and sale of baths. Each bath consists of a main unit plus a set of bath fittings. The company is split into two divisions, A and B. Division B manufactures the bath and Division A manufactures sets of bath fittings, which are both sold externally and transferred to Division B. Both of the divisions are treated as profit centres. The following data is available for both divisions: Division A Division B External selling price of items £80 £450 Transfer price £75 Internal standard variable costs per item £20 £245 Annual fixed costs £4,400,000 £7,440,000 Annual production capacity 200,000 80,000 Maximum external demand 180,000 80,000 The transfer price charged by Division A to Division B was negotiated some years ago between the previous divisional managers, who have both now been replaced by new managers. Head Office only allows Division B to purchase its fittings…arrow_forwardThe Sunland Company is a multidivisional company. Its managers have full responsibility for profits and complete autonomy to accept or reject transfers from other divisions. Division A produces a sub-assembly part for which there is a competitive market. Division B currently uses this sub-assembly for a final product that is sold outside at $1,392. Division A charges Division B the market price of $812 per unit of the part. Unit variable costs are $604 and $696 for Divisions A and B, respectively. The manager of Division B feels that Division A should transfer the part at a lower price than market because at market, Division B is unable to make a profit. (a) Your answer has been saved. See score details after the due date. Calculate Division B's contribution margin if transfers are made at the market price, and calculate the company's total contribution margin. (Enter negative amounts using either a negative sign preceding the number e.g.-45 or parentheses e.g. (45).) Division B's…arrow_forwardWeller Industries is a decentralized organization with six divisions. The company’s Electrical Division produces a variety of electrical items, including an X52 electrical fitting. The Electrical Division (which is operating at capacity) sells this fitting to its regular customers for $8.00 each; the fitting has a variable manufacturing cost of $4.47. The company’s Brake Division has asked the Electrical Division to supply it with a large quantity of X52 fittings for only $6.00 each. The Brake Division, which is operating at 50% of capacity, will put the fitting into a brake unit that it will produce and sell to a large commercial airline manufacturer. The cost of the brake unit being built by the Brake Division follows: Purchased parts (from outside vendors) $ 22.80 Electrical fitting X52 6.00 Other variable costs 14.21 Fixed overhead and administration 8.20 Total cost per brake unit $ 51.21 Although the $6.00 price for the X52 fitting represents…arrow_forward
- The Sheridan Company is a multidivisional company. Its managers have full responsibility for profits and complete autonomy to accept or reject transfers from other divisions. Division A produces a sub-assembly part for which there is a competitive market. Division B currently uses this sub-assembly for a final product that is sold outside at $1,368. Division A charges Division B the market price of $798 per unit of the part. Unit variable costs are $594 and $684 for Divisions A and B, respectively. The manager of Division B feels that Division A should transfer the part at a lower price than market because at market, Division B is unable to make a profit. (a) Your answer is correct. Calculate Division B's contribution margin if transfers are made at the market price, and calculate the company's total contribution margin. (Enter negative amounts using either a negative sign preceding the number e.g. -45 or parentheses e.g. (45).) (b) (c) Division B's contribution margin $ Company's…arrow_forwardMorrisons Plastics Division, a profit center, sells its products to external customers as well as to other internal profit centers. Which one of the following circumstances would justify the Plastics Division selling a product internally to another profit center at a price that is below the market-based transfer price? a. The buying unit has excess capacity. b. The selling unit is operating at full capacity. c. Routine sales commissions and collection costs would be avoided. d. The profit centers managers are evaluated on the basis of unit operating income.arrow_forwardCascade Containers is organized into two divisions-Manufacturing and Distribution. Manufacturing produces a product that can be sold immediately or transferred to Distribution for further processing and then sold. Distribution only buys from Manufacturing for quality control reasons. Manufacturing currently sells 2,400 units annually at a price of $600 per unit to outside customers. It sells an additional 1,200 units to Distribution. The unit variable cost in Manufacturing is $300 and annual fixed costs are $300,000. Manufacturing is located in a country with a 20 percent tax rate. Distribution can sell units that have had further processing for $1,200 each. In addition to what it pays Manufacturing, the variable costs in Distribution are $150 per unit. Annual fixed costs in Distribution are $360,000. Distribution is located in a country with a 10 percent tax rate. Required: a. Suppose Manufacturing would have excess capacity even with the demand from Distribution. Ignoring tax…arrow_forward
- The Eastern division sells goods internally to the Western division of the same company. The quoted external price in industry publications from a supplier near Eastern is $200 per ton plus transportation. It costs $20 per ton to transport the goods to Western. Eastern's actual market cost per ton to buy the direct materials to make the transferred product is $100. Actual per ton direct labor is $50. Other actual costs of storage and handling are $40. Assuming there is an excess capcity in the Eastern Division, the minimum and maximum transfer price are:arrow_forwardQuinlan Corporation has two divisions: the Industrial Equipment Division and the Consumer Goods Division. The Industrial Equipment Division's divisional segment margin is $42,500, and the Consumer Goods Division's divisional segment margin is $88,300. The total amount of common fixed expenses not traceable to the individual divisions is $108,400. What is the company's net operating income?helparrow_forwardAxelia Corporation has two divisions, Refining and Extraction. The company's primary product is Luboil Oil. Each division's costs are provided below: Extraction: Variable costs per barrel of oil $13 Fixed costs per barrel of oil $6 Refining: Variable costs per barrel of oil $26 Fixed costs per barrel of oil $36 The Refining Division has been operating at a capacity of 40,800 barrels a day and usually purchases 25,600 barrels of oil from the Extraction Division and 15,100 barrels from other suppliers at $62 per barrel. What is the transfer price per barrel from the Extraction Division to the Refining Division, assuming the method used to place a value on each barrel of oil is 110% of full costs? A. $99.00 B. $20.90 C. $55.00 D. $19.00arrow_forward
- Managerial AccountingAccountingISBN:9781337912020Author:Carl Warren, Ph.d. Cma William B. TaylerPublisher:South-Western College PubFinancial And Managerial AccountingAccountingISBN:9781337902663Author:WARREN, Carl S.Publisher:Cengage Learning,
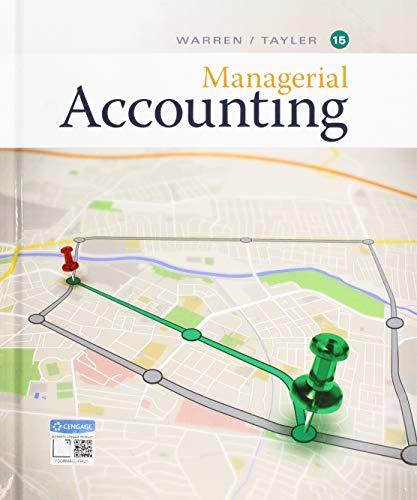
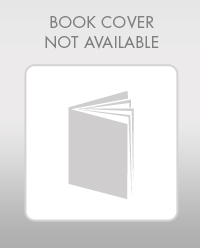