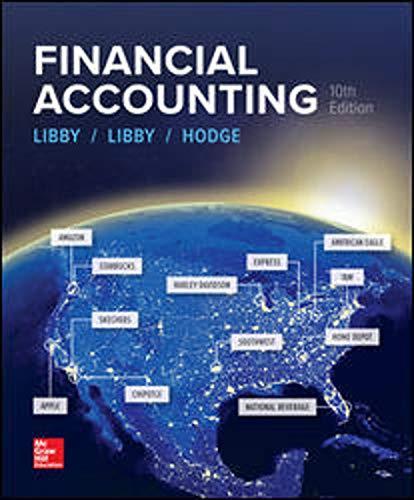
FINANCIAL ACCOUNTING
10th Edition
ISBN: 9781259964947
Author: Libby
Publisher: MCG
expand_more
expand_more
format_list_bulleted
Concept explainers
Topic Video
Question
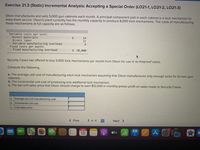
Transcribed Image Text:Exercise 21.3 (Static) Incremental Analysis: Accepting a Special Order (LO21-1, LO21-2, LO21-3)
Olson manufactures and sells 5,000 gun cabinets each month. A principal component part in each cabinet is a lock mechanism to
keep them secure. Olson's plant currently has the monthly capacity to produce 8,000 lock mechanisms. The costs of manufacturing
these mechanisms at full capacity are as follows.
Variable costs per unit:
Direct materials
Direct labor
Variable manufacturing overhead
Fixed costs per month:
Fixed manufacturing overhead
14
12
4
$ 10,000
Security Cases has offered to buy 3,000 lock mechanisms per month from Olson for use in its fireproof cases.
Compute the following.
a. The average unit cost of manufacturing each lock mechanism assuming that Olson manufactures only enough locks for its own gun
cabinets.
b. The incremental unit cost of producing one additional lock mechanism.
c. The per-unit sales price that Olson should charge to earn $12,000 in monthly pretax profit on sales made to Security Cases.
a. Average per-unit manufacturing cost
b. Incremental unit cost
С.
Unit sales price
( Prev
2 of 4
Next >
23
LO
NOV
18
étv l
280
%24
%24
Expert Solution

This question has been solved!
Explore an expertly crafted, step-by-step solution for a thorough understanding of key concepts.
This is a popular solution
Trending nowThis is a popular solution!
Step by stepSolved in 2 steps

Knowledge Booster
Learn more about
Need a deep-dive on the concept behind this application? Look no further. Learn more about this topic, accounting and related others by exploring similar questions and additional content below.Similar questions
- Soul Socket Inc. manufactures socket wrenches. . For next month, the vice president of production plans on producing 4,450 wrenches per day. The company can produce as many as 5,000 wrenches per day, but is more likely to produce 4,500 per day. . The demand for wrenches over the past three years averaged 4,250 wrenches per day. • Fixed manufacturing costs per month total $374,000. . The company works 22 days a month. • Fixed manufacturing overhead is charged on a per-wrench basis. a. What is the overhead rate per wrench based on Theoretical Capacity? [Select] b. What is the overhead rate per wrench based on Practical Capacity? [Select] c. What is the overhead rate per wrench based on Normal Utilization? [Select] d. What is the overhead rate per wrench based on Master Budget Utilization? [Select]arrow_forwardParadise Marine Sails manufactures sails for sailboats. The company’s capacity is 29,000 sails per month. They are currently producing 25,000 sails a month. Current production cost can be found in the chart below: Sales Price $200 Variable Cost Manufacturing Cost $100 Administrative Cost $50 Total Fixed Cost Manufacturing $500,000 Administrative $480,000 Should you accept a special order at a price of $170 for 3000 sails? Fixed cost will increase by $9,000 to produce these sails. Give a numerical justification Would your answer be different if the company was currently producing 28,000 sails?arrow_forwardClone Computers assembles and packages personal computer systems from brand-name components. Its Home Office PC System is assembled from components costing $1400 per system and sells for $2000. Labour costs for assembly are $100 per system. This product line's share of overhead costs is $10,000 per month. a. How many Home Office systems must be sold each month to break even on this product line? b. What will be the profit or loss for a month in which 15 Home Office systems are sold?arrow_forward
- Talbot Industries manufactures two models of wireless headset: TI-12 and TI-28. Each product requires time on a single machine. The machine has a monthly capacity of 540 hours. Total market demand for the two products is limited to 2,000 units of TI-12 and 1,000 units of TI-28 monthly. Talbot is currently producing and selling 1,500 TI-12 models and 780 TI-28 models each month. Cost and machine-usage data for the two products are shown in the following spreadsheet, which analysts at Talbot use for production planning purposes: Price Less variable costs per unit Material Labor Overhead Contribution margin per unit Fixed costs Manufacturing Marketing and administrative Machine hours per unit Machine hours used Machine hours available Quantity produced Maximum demand Profit Required A Required B TI-12 Model TI-28 Model TI-12 $ 80 23 29 8 $ 20 units units 0.1arrow_forwardHot Dog Express (HDE) is currently buying their buns from Buns-For-All for $. 50 a dozen. Each month they purchase 14,000 dozen. HDE is considering making their own buns for cost cutting and quality reasons. They have determined the following costs: materials, $. 20; direct labor, $. 10; variable factory overhead cost, $. 04; and total (existing) fixed costs, $3,000 per month. From an accounting point of view only, should HDE make or buy their buns?arrow_forwardGreener Garden Group produces and sells 21,200 litres of organic lawn and garden fertilizer. The fertilizer, GoGrow, is a favourite among landscaping companies in southern Manitoba. The selling price of GoGrow is $16 per litre, variable costs are $9 per litre, fixed manufacturing overhead costs in the plant total $121,900 per month, and the fixed selling costs total $164,300 per month. Recent supply chain problems have made it difficult for the Greener Garden Group to get the quantity of chemicals needed to produce the fertilizer. Because of this, sales have dropped to 6,360 litres per month and will most likely stay at this level until the supply of chemicals is back to normal. Management expects that the supply chain issues will ease up soon with business returning to normal in two months. However, the CEO of Greener Garden Group thinks the company should fully shut down operations for two months until the supply chain issues are resolved. If the Greener Garden Group does close the…arrow_forward
- Sheridan Ranch Inc. has been manufacturing its own finials for its curtain rods. The company is currently operating at 100% of capacity, and variable manufacturing overhead is charged to production at the rate of 66% of direct labor cost. The direct materials and direct labor cost per unit to make a pair of finials are $4 and $5, respectively. Normal production is 34,300 curtain rods per year. A supplier offers to make a pair of finials at a price of $13.05 per unit. If Sheridan Ranch accepts the supplier's offer, all variable manufacturing costs will be eliminated, but the $45,700 of fixed manufacturing overhead currently being charged to the finials will have to be absorbed by other products. (a) Prepare the incremental analysis for the decision to make or buy the finials. (Enter negative amounts using either a negative sign preceding the number e.g. -45 or parentheses e.g. (45).) Direct materials. Direct labor Variable overhead costs Fixed manufacturing costs Purchase price Total…arrow_forwardSheridan Inc. has been manufacturing its own shades for its table lamps. The company is currently operating at 100% of capacity, and variable manufacturing overhead is charged to production at the rate of 50% of direct labour costs. The direct materials and direct labour costs per unit to make the lampshades are $4.50 and $5.50, respectively. Normal production is 48,000 table lamps per year. A supplier offers to make the lampshades at a price of $13.20 per unit. If Sheridan Inc. accepts the supplier's offer, all variable manufacturing costs will be eliminated, but the $40,000 of fixed manufacturing overhead currently being charged to the lampshades will have to be absorbed by other products. Prepare the incremental analysis for the decision to make or buy the lampshades. (Round answers to O decimal places, e.g. 5,275. If an amount reduces the net income then enter with a negative sign preceding the number e.g. -15,000 or parenthesis, e.g. (15,000). While alternate approaches are…arrow_forwardChristine's Chronographs makes two models of a high-end watch-the model 94 and the model 101. Both models go through a special polishing step that requires the use of the single polishing machine at the company. The price and costs of the two models appear as follows. Price per watch Variable cost per watch Polishing hours per watch The polishing machine used for both models has a capacity of 48,000 hours annually. Fixed manufacturing costs are $8,200,000 annually. Required: a. Suppose that the maximum annual unit sales that Christine's can achieve is 18,000 units of the Model 94 and 17,000 of the Model 101. How many units of each watch model should Christine's produce annually? b. Suppose that the maximum annual unit sales that Christine's achieve make is 16,000 units of the Model 94 and 13,000 of the Model 101. How many units of each watch model should Christine's produce annually? Model 94 Model 101 $4,300 $10,500 $ 6,600 $2,200 2 3 Complete this question by entering your answers in…arrow_forward
- Lay's Potato Chips is examining their Wavy Lays chip line. They began the year expecting to produce 500,000 bags of potato chips. They projected that each bag would require 3 pounds of potatos and 1.5 hours of labor to manufacture. They planned to pay $2 per pound for potatos and $20 per hour for labor. They also budgeted $900,000 for variable manufacturing overhead costs and $ 450,000 of fixed manufacturing overhead costs, with both variable and fixed manufacturing overhead costs being allocated based on direct labor hours. At the end of the year, Lay's finds that they produced 880,000 bags of potato chips, using 3.25 pounds of potatos per bag and 1.25 hours of labor per bag. Due to significant inflation, the purchasing department made a deal with the supplier and purchased 3,000,000 pounds of potatos for a per-pound price of $3.25. They also spent $22 per hour for direct labor. The Wavy Lays chip line spent $843,000 on variable manufacturing overhead costs and $562,000 on fixed…arrow_forwardThe Svenson corporation manufactures cell phones. It manufactures its own circuit boards for cell phones, an important part for the cell phone.The unit variable cost of raw materials is $180The variable unit labor cost is $65.The unit variable cost of indirect costs is $13Fixed costs are $6,000The number of parts it manufactures is 700 cell phones in a month.Morly, an electrical parts supplier, offers to sell you the board for $210 plus freight of $8 per unit.• Determine whether it is best for you to continue manufacturing the part or purchase it from the supplier.• Calculate the profit or loss you would have if you accepted the supplier's proposal.arrow_forwardNardin Outfitters has a capacity to produce 12,000 of their special arctic tents per year. The company is currently producing and selling 5,000 tents per year at a selling price of $900 per tent. The cost of producing and selling one tent follows: Variable manufacturing costs $ 440 Fixed manufacturing costs 90 Variable selling and administrative costs 80 Fixed selling and administrative costs 50 Total costs $ 660 The company has received a special order for 500 tents at a price of $600 per tent from Chipman Outdoor Center. It will not have to pay any sales commission on the special order, so the variable selling and administrative costs would be only $45 per tent. The special order would have no effect on total fixed costs. The company has rejected the offer based on the following computations: Selling price per case $ 600 Variable manufacturing costs 440 Fixed manufacturing costs 90 Variable selling and administrative costs 45 Fixed selling and…arrow_forward
arrow_back_ios
SEE MORE QUESTIONS
arrow_forward_ios
Recommended textbooks for you
- AccountingAccountingISBN:9781337272094Author:WARREN, Carl S., Reeve, James M., Duchac, Jonathan E.Publisher:Cengage Learning,Accounting Information SystemsAccountingISBN:9781337619202Author:Hall, James A.Publisher:Cengage Learning,
- Horngren's Cost Accounting: A Managerial Emphasis...AccountingISBN:9780134475585Author:Srikant M. Datar, Madhav V. RajanPublisher:PEARSONIntermediate AccountingAccountingISBN:9781259722660Author:J. David Spiceland, Mark W. Nelson, Wayne M ThomasPublisher:McGraw-Hill EducationFinancial and Managerial AccountingAccountingISBN:9781259726705Author:John J Wild, Ken W. Shaw, Barbara Chiappetta Fundamental Accounting PrinciplesPublisher:McGraw-Hill Education
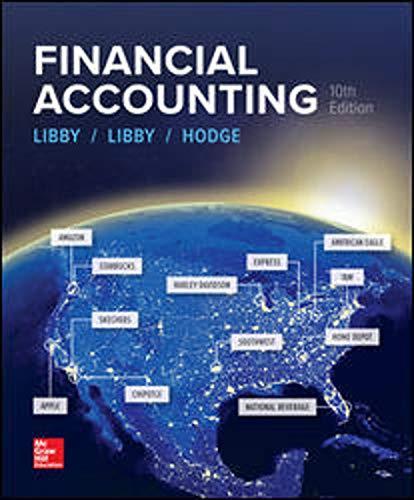
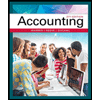
Accounting
Accounting
ISBN:9781337272094
Author:WARREN, Carl S., Reeve, James M., Duchac, Jonathan E.
Publisher:Cengage Learning,
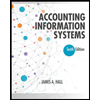
Accounting Information Systems
Accounting
ISBN:9781337619202
Author:Hall, James A.
Publisher:Cengage Learning,
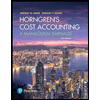
Horngren's Cost Accounting: A Managerial Emphasis...
Accounting
ISBN:9780134475585
Author:Srikant M. Datar, Madhav V. Rajan
Publisher:PEARSON
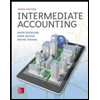
Intermediate Accounting
Accounting
ISBN:9781259722660
Author:J. David Spiceland, Mark W. Nelson, Wayne M Thomas
Publisher:McGraw-Hill Education
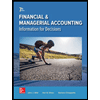
Financial and Managerial Accounting
Accounting
ISBN:9781259726705
Author:John J Wild, Ken W. Shaw, Barbara Chiappetta Fundamental Accounting Principles
Publisher:McGraw-Hill Education