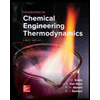
Methanol is produced by reacting carbon monoxide and hydrogen at 644 K over a ZnO–Cr2O3 catalyst. A mixture of CO and H 2 in a ratio 2 mol H 2/mol CO is compressed and fed to the catalyst bed at 644 K and 34.5 MPa absolute. A single-pass conversion of 25% is obtained. The space velocity, or ratio of thevolumetric flow rate of the feed gas to the volume of the catalyst bed, is (25;000 m3/h)/(1 m3 catalyst bed). The product gases are passed through a condenser, in which the methanol is liquefied.
(a) You are designing a reactor to produce 54.5 kmol CH 3OH/h. Estimate (i) the volumetric flow rate that the compressor must be capable of delivering if no gases are recycled, and (ii) the required volume of the catalyst bed. (Use Kay’s rule for pressure–volume calculations.)
(b) If (as is done in practice) the gases from the condenser are recycled to the reactor, the compressor is then required to deliver only the fresh feed. What volumetric flow rate must it deliver assuming that the methanol produced is completely recovered in the condenser? (In practice it is not;
moreover, a purge stream must be taken off to prevent the buildup of impurities in the system.)

Trending nowThis is a popular solution!
Step by stepSolved in 5 steps with 2 images

- A simple batch distillation without reflux is ran until 30% of the initial feed is taken off as overhead. The feed is equimolar mixture of heptane (C7H16, mw 100 g/mol, bp 98 °C) and chloroheptane (C7H15Cl, mw 135 g/mol, bp 150 °C). The system can be considered as ideal, with an average relative volatility of 4.2. What are the mass compositions of the overhead and remaining liquid?arrow_forwardA mixture of 10 mol% methane, 20 mol% ethane, and 70% mol% propane with the flow rare of 150 mol/min is fed to a separator working at 100 psig pressure and 50 °F temperature. Calculate the flow rates and compositions of the outlet streams from this separator. Present your concluding remarks on your solution.arrow_forward1. Based on the following figure, answer the following questions : (a) How many actual trays are present if there is a partial condenser and reboiler? Are the top and bottom products a liquid or vapor? (b) What is the vapor and liquid molar fractions at the third tray? (c) At what tray is the feed placed? Is it above or below that tray? 1 0.9 0.8 0.7 0.6 0.5 0.4 0.3 0.2 0.1 0 0 0.1 0.2 1-Pentene/1-Hexene 0.3 0.4 0.5 14.7 psia 0.6 0.7 0.8 ||||||||||| 0.9 1arrow_forward
- A 7 cm-thick beef steak is being frozen in a -40°C room. The product has 73% moisture content, density of 970 kg/m 3, and thermal conductivity (frozen) of 1.1 W/(m K). Estimate the freezing time using Plank’s equation. The product has an initial freezing temperature of -1.75°C, and the movement of air in the freezing room provides a convective heat-transfer coefficient of 10 W/(m2 K).arrow_forwardSteel surface can be hardened by carburization. Such process is done at 1000°C and the concentration gradient (dc/dx) is -8.23x1029 atoms/m4. The coefficient of diffusion (D0) for Fe is 20x10-6 m2/s (See table 1). Estimate the flux of carbon atoms into the steel in this process.arrow_forwardF2 gas and excess iodine solid are heated together at high temperatures. The iodine sublimes and gaseous iodine heptafluoride forms. A 2.50L reaction vessel contains 350 torr of F2 gas and 2.50g of solid iodine at 250K which is then heated to 550K. What is the number of moles of excess iodine that would be left over once all the fluorine is used up? What is the total pressure at the end of the reaction? What is the partial pressure of the left over iodine gas as the end of the reaction? What is the balanced chemical equation for this reaction?arrow_forward
- A spherical container is used to store reacting chemicals, which results in a uniform heat flux (qi”) applied to the inner surface of the container. The initial temperature of the inner wall of the container, Ti, is 500K. The container has an inner radius of 0.4 m and an outer radius of 0.5 m, the density of the container’s walls are 8055 kg/m3, and its heat capacity is 535 J/(kg-K). The container is then suddenly submerged in a liquid bath with a temperature T∞=300K. The convective heat transfer coefficient for the bath: h= 450 W/(m2 K).(a) Assume that there is a negligible thermal gradient in the wall of the container (dT/dr is negligible) and that the heat flux qi” is constant, write an equation that expresses how the temperature of the wall of the container changes with time (dT/dt) and evaluate the initial rate of change of wall temperature (dT/dt ) when qi”=106 W/m2.(b) What is the steady state temperature of the wall?arrow_forwardNormal butane is catalytically isomerized to isobutane. A fresh feed stream containing pure n-butane at temperature T, is mixed adiabatically with a recycle stream containing n-butane and isobutane, and the combined stream is fed to the reactor, where some but not all of the n-butane in the feed is converted. The reactor effluent is pumped to a distillation column. The overhead distillation product contains primarily isobutane and a small amount of n-butane. The bottoms product, which also contains both species, is the stream recycled to the reactor. The streams leaving the distillation column are at different temperatures. a) Determine the number of degrees of freedom associated with the feed mixer, the reactor, the distillation column, and the entire process. Include all unknown process stream temperatures and process unit heat duties in your analysis. b) Suppose a single-pass conversion of 35.0% is attained in the reactor, the overhead distillation column product contains 88.5 mole…arrow_forwardSteam distillation can be run more efficiently in some cases using super-heated steam at 1 atm pressure rather than boiling water. By increasing the temperature of the steam beyond the boiling point of water in a controlled fashion, the oil may still be protected from degradation while increasing its contribution to the vapor composition, making the process more efficient. At 150 °C, linalyl acetate exerts a vapor pressure of 93 torr. If a steam still were run using steam heated to this temperature in place of boiling water, how much water must co-distill to collect 1.0 grams of linalyl acetate?arrow_forward
- The following stream is at 100 psia and 190F. Perform and isothermal flash calculation to determine the vapor fraction, liquid fraction, vapor composition and liquid composition at this temperature and pressure.arrow_forwardDistillation is used to separate pentane from hexane. The feed amounts 700 mol/s and has amole ratio pentane/hexane = 0.5. The bottom and top products have the compositions xB=0.05 andxD= 0.98. The reflux ratio is 2.25. The column pressure is 1 bar. The feed, at the bubbling point, enters the column exactly on the feed tray. The tray temperature is equal to the feed temperature. The pentane vapor pressure is given by: lnP=11T-3410/T The vapor pressure of hexane is 1/3 of the pentane vapor pressure over the whole temperature range. The heat of vaporization amounts to 30 kJ/mol. The distance between the trays amounts to 0.50 m. A.The vapor stream from the reboiler=693.100 mole/s B.The required energy in the reboiler=20793.01887 kJ/s c. number of equilibrium stages d.height of columnarrow_forwarda) Consider a pressure of 15.75 kPa for the evaporation of the 50% NaOH solution. Determine the boiling temperature of the NaOH solution, determine the elevation of the boiling point of the solution with respect to the boiling point of water at the same pressure. b) Consider a pressure of 15.75 kPa for the evaporation of the 40% NaOH solution. Determine the boiling temperature of the NaOH solution, determine the elevation of the boiling point of the solution with respect to the boiling point of water at the same pressure. Based on your results, answer the following questions. Do you think what is an important parameter in the design of an evaporator? Why?arrow_forward
- Introduction to Chemical Engineering Thermodynami...Chemical EngineeringISBN:9781259696527Author:J.M. Smith Termodinamica en ingenieria quimica, Hendrick C Van Ness, Michael Abbott, Mark SwihartPublisher:McGraw-Hill EducationElementary Principles of Chemical Processes, Bind...Chemical EngineeringISBN:9781118431221Author:Richard M. Felder, Ronald W. Rousseau, Lisa G. BullardPublisher:WILEYElements of Chemical Reaction Engineering (5th Ed...Chemical EngineeringISBN:9780133887518Author:H. Scott FoglerPublisher:Prentice Hall
- Industrial Plastics: Theory and ApplicationsChemical EngineeringISBN:9781285061238Author:Lokensgard, ErikPublisher:Delmar Cengage LearningUnit Operations of Chemical EngineeringChemical EngineeringISBN:9780072848236Author:Warren McCabe, Julian C. Smith, Peter HarriottPublisher:McGraw-Hill Companies, The
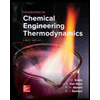
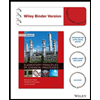
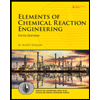
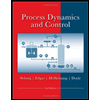
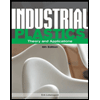
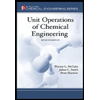