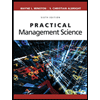
Practical Management Science
6th Edition
ISBN: 9781337406659
Author: WINSTON, Wayne L.
Publisher: Cengage,
expand_more
expand_more
format_list_bulleted
Concept explainers
Topic Video
Question
Kris Lee, the owner and manager of the Quality Hardware Store, is reassessing his inventory policy for hammers. He sells an average of 50 hammers per month, so he has been placing an order to purchase 50 hammers from a wholesaler at a cost of $20 per hammer at the end of each month. However, Kris does all the ordering for the store himself and finds that this is taking a great deal of his time. He estimates that the value of his time spent in placing each order for hammers is $75.
- What would the unit holding cost for hammers need to be for Kris' current inventory policy to be optimal according to the basic EOQ model? What is this unit holding cost as a percentage of the unit acquisition cost?
- What is the optimal order quantity if the unit holding cost actually is 20 percent of the unit acquisition cost? What is the corresponding value of TVC? What is TVC for the current inventory policy?
- If the wholesaler typically delivers an order of hammers in 5 working days (out of 25 working days in an average month), what should the reorder point be (according to the basic EOQ model)?
- Kris doesn't like to incur inventory shortages of important items. Therefore, he has decided to add a safety stock of 5 hammers to safeguard against late deliveries and larger-than-usual sales. What is his new reorder point? How much does this safety stock add to TVC?
Expert Solution

This question has been solved!
Explore an expertly crafted, step-by-step solution for a thorough understanding of key concepts.
This is a popular solution
Trending nowThis is a popular solution!
Step by stepSolved in 2 steps

Knowledge Booster
Learn more about
Need a deep-dive on the concept behind this application? Look no further. Learn more about this topic, operations-management and related others by exploring similar questions and additional content below.Similar questions
- Ray wishes to determine the optimal order quantity for its best-selling bike in his bike store. Ray pays the supplier a wholesale price of $118 each for this bike. Ray has estimated the average daily demand for this bike is 23 units. The store opens 304 days a year. The cost to carry one bike in the store for a whole year is 8% of the unit bike cost. Ray has estimated that, on average, the order processing cost, i.e., ordering cost, with the bike supplier each time is $152, and it roughly takes 20 working days to receive the order from the supplier. Ray wishes to avoid the stock-out situation with a probability of 95%, and this requires Ray to carry a safety stock of 30 bikes in the store. What is the optimal order quantity (EOQ value) that Ray should order each time from the bike supplier to minimize his long-run inventory cost?arrow_forwardA company orders 100 units of a raw material every time its inventory level drops to 50 units. The lead time for the delivery of the raw material is 5 days. Currently, the inventory level is at 80 units. Assuming constant demand, calculate the reorder point for the raw material.arrow_forwardESTRELLA is a bike retailer located in the outskirts of Bacolod City. ESTRELLA purchases bikes from STORAGEHUB in orders of 250 bikes which is the current economic order quantity. STORAGEHUB is now offering the following bulk discounts to its customers: Price 0% discount on orders less than 499 P3,500 10% discount on orders above 500 units - 999 3,150 15% discount on orders above 1,000 units 2,975 ESTRELLA is wondering if the EOQ model is still the most economical and whether increasing the order size would actually be more beneficial. Following information is relevant to forming the decision: Annual demand is 5000 units Ordering cost is $100 per order Annual holding cost is 25% How much is the EOQ for each quantity discount? How much should be the EOQ?arrow_forward
- Algro Inc. keeps a wide range of parts and materials on hand for use in its production processes. Management has recently had difficulty managing parts inventory as demand for its finished goods has increased; they frequently run out of some critical parts while having an endless supply of others. They would like to classify their parts inventory according to the ABC approach to better control inventory. The following is a list of parts, along with their annual usage and unit value: Item Annual Unit Item Annual Unit Number Usage Cost Number Usage Cost 1 36 $350 2 510 30 3 50 23 4 300 45 5 18 1900 6 500 8 7 710 4 8 80 26 9 344 28 10 67 440 11 510 2 12 682 35 13 1216 95 50 14 10 3 15 820 1 KARAN2222222222 16 60 $610 17 120 20 18 270 15 19 45 50 20 19 3200 21 910 3 12 4750 23 30 2710 24 24 1800 25 870 105 26 244 30 27 750 15 28 45 110 29 46 160 30 165 25 a. Classify the inventory items according to the ABC approach using the dollar value of annual demand. b. Clearly explain why you…arrow_forwardYou are a newsvendor selling the New York Times every morning. Before you get to work, you buy the day’s newspaper for $0.90 a copy. You sell a copy of the New York Times for $4.0. Daily demand is distributed normally with a mean of 130 and a standard deviation of 20. At the end of each morning, any leftover copies can be sold to a recycling center for $0.10. How many copies of the New Yorkarrow_forwardKGU company sells shoes whose daily demand is 100 units. The inventory holding cost is $2 per unit per year. The company also spends $20 per unit to process order. It takes 6 days from the time of reorder to the stocking of the inventory. The company keeps a safety stock that can cover twice the inventory. What is the ideal order quantity for KGU to purchase to minimize inventory costs? What is the ideal level of inventory at which KGU should pace a purchase order?arrow_forward
- Becky Shelton, a teacher at kemp middle school is in charge of ordering the T-shirts to be sold for the school's annual fund-raising project the t-shirts are printed with a special kemp school logo. In some years the supply of T-shirts has been insufficient to satisfy the number of sales orders. In other years, T-shirts have been left over. excess T-shirts are normally donated to some charitable organization. T-shirts cost the school $7 each and are normally sold for $14 each. Ms Shelton has decided to order 790 shirts. Required 1) if the school receives actual sales orders for 715 shirts, what amount of profit will the school earn?what is the cost of waste due to excess inventory? 2) If the school receives actual sales orders for 830 shits, what amount of profit will the school earn? What amount of opportunity cost will the school incur? a) Profit $1,050 waste due to excess inventory b) Profit opportunity costarrow_forwardJill's Job Shop buys two parts (Tegdiws and Widgets) for use in its production system from two different suppliers. The parts are needed throughout the entire 52-week year. Tegdiws are used at a relatively constant rate and are ordered whenever the remaining quantity drops to the reorder level. Widgets are ordered from a supplier who stops by every two weeks. Data for both products are as follows: ITEM TEGDIW WIDGET Annual demand 7,000 10,000 Holding cost (% of item cost) 30 % 30 % Setup or order cost $ 190.00 $ 10.00 Lead time 7 weeks 2 week Safety stock 45 units 9 units Item cost $ 5 $ 6 a. What is the reorder quantity and reorder point for Tegdiws? (Round your answers to the nearest whole number.) b. What is the inventory control system for Widgets? (Round your answer to the nearest whole number.) Note:- Do not provide handwritten solution. Maintain accuracy and quality in your answer. Take care of plagiarism. Answer…arrow_forward
arrow_back_ios
arrow_forward_ios
Recommended textbooks for you
- Practical Management ScienceOperations ManagementISBN:9781337406659Author:WINSTON, Wayne L.Publisher:Cengage,Operations ManagementOperations ManagementISBN:9781259667473Author:William J StevensonPublisher:McGraw-Hill EducationOperations and Supply Chain Management (Mcgraw-hi...Operations ManagementISBN:9781259666100Author:F. Robert Jacobs, Richard B ChasePublisher:McGraw-Hill Education
- Purchasing and Supply Chain ManagementOperations ManagementISBN:9781285869681Author:Robert M. Monczka, Robert B. Handfield, Larry C. Giunipero, James L. PattersonPublisher:Cengage LearningProduction and Operations Analysis, Seventh Editi...Operations ManagementISBN:9781478623069Author:Steven Nahmias, Tava Lennon OlsenPublisher:Waveland Press, Inc.
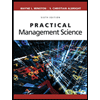
Practical Management Science
Operations Management
ISBN:9781337406659
Author:WINSTON, Wayne L.
Publisher:Cengage,
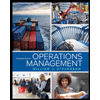
Operations Management
Operations Management
ISBN:9781259667473
Author:William J Stevenson
Publisher:McGraw-Hill Education
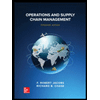
Operations and Supply Chain Management (Mcgraw-hi...
Operations Management
ISBN:9781259666100
Author:F. Robert Jacobs, Richard B Chase
Publisher:McGraw-Hill Education
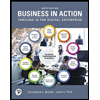
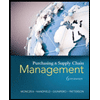
Purchasing and Supply Chain Management
Operations Management
ISBN:9781285869681
Author:Robert M. Monczka, Robert B. Handfield, Larry C. Giunipero, James L. Patterson
Publisher:Cengage Learning
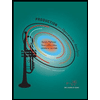
Production and Operations Analysis, Seventh Editi...
Operations Management
ISBN:9781478623069
Author:Steven Nahmias, Tava Lennon Olsen
Publisher:Waveland Press, Inc.