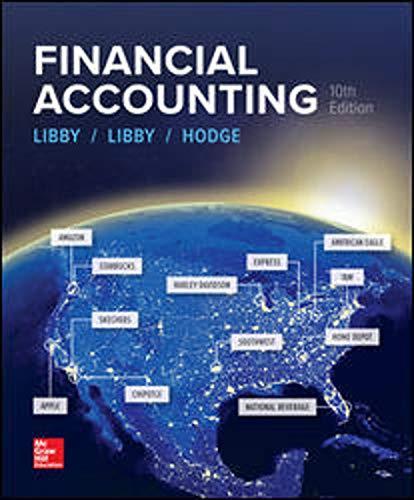
Concept explainers
Krazy Kayaks manufactures kayaks. The company has automated production, so it allocates manufacturing
Raw Materials Inventory $20,000
Work-in-Process Inventory $17,000
Finished Goods Inventory $11,000
During January 2015, Krazy used 300 machine hours and recorded the following transactions:
- Purchased materials on account, $31,000
- Used direct materials, $39,000
- Manufacturing wages incurred totaled $40,000, of which 90% was direct labor and 10% was indirect labor.
- Used indirect materials, $3,000
- Incurred other manufacturing overhead for January 2015, $13,000
- Allocated manufacturing overhead for January 2015
- Cost of completed motor scooters, $100,000
- Sold scooters on account, $175,000; cost of scooters sold, $95,000
Requirements:
Compute Krazy Kayak’s predetermined overhead allocation rate for 2015
Journalize the transactions in the general journal.
Adjust the Manufacturing overhead for the overallocated or under-allocated overhead.

Trending nowThis is a popular solution!
Step by stepSolved in 4 steps with 3 images

- Campbell Manufacturing Company produced 1,400 units of inventory in January Year 2. It expects to produce an additional 9,000 units during the remaining 11 months of the year. In other words, total production for Year 2 is estimated to be 10,400 units. Direct materials and direct labor costs are $74 and $71 per unit, respectively. Campbell expects to incur the following manufacturing overhead costs during the Year 2 accounting period. Production supplies Supervisor salary Depreciation on equipment Utilities Rental fee on manufacturing facilities Required a. Combine the individual overhead costs into a cost pool and calculate a predetermined overhead rate assuming the cost driver is number of units. b. Determine the cost of the 1,400 units of product made in January. Complete this question by entering your answers in the tabs below. Required A Required B $6,500 186,000 126,000 17,000 223,500 Determine the cost of the 1,400 units of product made in January. Allocated Cost Indirect…arrow_forwardWachowski Company reported the following cost data for the year 2017. Factory maintenance costs $90,000 Direct labor, wages 352,000 Direct labor, health insurance 32,000 Indirect labor, health insurance 16,000 Health insurance for production supervisor 6,500 Administrative costs 54,000 Rental of office space for administrative staff 18,500 Sales commissions 52,000 Direct material 1,220,000 Indirect materials 633,000 Advertising expense 39,000 Depreciation on factory building 62,000 Indirect labor, wages 70,000 Production supervisor's salary 33,000 Use the above cost data to complete the table below. Total prime costs $4 Total manufacturing overhead costs $ Total product costs Total period costsarrow_forwardWachowski Company reported the following cost data for the year 2017. Factory maintenance costs $90,000 Direct labor, wages 352,000 Direct labor, health insurance 32,000 Indirect labor, health insurance 16,000 Health insurance for production supervisor 6,500 Administrative costs 54,000 Rental of office space for administrative staff 18,500 Sales commissions 52,000 Direct material 1,220,000 Indirect materials 633,000 Advertising expense 39,000 Depreciation on factory building 62,000 Indirect labor, wages 70,000 Production supervisor's salary 33,000 Use the above cost data to complete the table below. Total prime costs Total manufacturing overhead costs $ Total product costs $ Total period costsarrow_forward
- I want to answer this questionarrow_forwardLakeside Company estimated manufacturing overhead costs for 2014 at $390,000, based on 160,000 estimated direct labor hours. Actual direct labor hours for 2014 totaled 195,000. The manufacturing overhead account contains debit entries totaling $391,500. The manufacturing overhead for 2014 was: (Round your intermediate calculations to one decimal place)arrow_forwardVelshi Printers has contracts to complete weekly supplements required by forty - six customers. For the year 2018, manufacturing overhead cost estimates total $2,080,000 for an annual production capacity of 16 million pages. For 2018 Velshi Printers has decided to evaluate the use of additional cost pools. After analyzing manufacturing overhead costs, it was determined that number of design changes, setups, and inspections are the primary manufacturing overhead cost drivers. The following information was gathered during the analysis: Cost pool Design changes Manufacturing overhead costs Activity level 100 design changes $160,000 Setups 1,850,000 6,000 setups Inspections 70,000 9,000 inspections Total manufacturing overhead costs $2,080,000 During 2018, two customers, Money Managers and Hospital Systems, are expected to use the following printing services: Activity Money Managers Hospital Systems Pages 90,000 106,000 Design changes Setups Inspections 12 17 26 34 Assuming activity - cost…arrow_forward
- AccountingAccountingISBN:9781337272094Author:WARREN, Carl S., Reeve, James M., Duchac, Jonathan E.Publisher:Cengage Learning,Accounting Information SystemsAccountingISBN:9781337619202Author:Hall, James A.Publisher:Cengage Learning,
- Horngren's Cost Accounting: A Managerial Emphasis...AccountingISBN:9780134475585Author:Srikant M. Datar, Madhav V. RajanPublisher:PEARSONIntermediate AccountingAccountingISBN:9781259722660Author:J. David Spiceland, Mark W. Nelson, Wayne M ThomasPublisher:McGraw-Hill EducationFinancial and Managerial AccountingAccountingISBN:9781259726705Author:John J Wild, Ken W. Shaw, Barbara Chiappetta Fundamental Accounting PrinciplesPublisher:McGraw-Hill Education
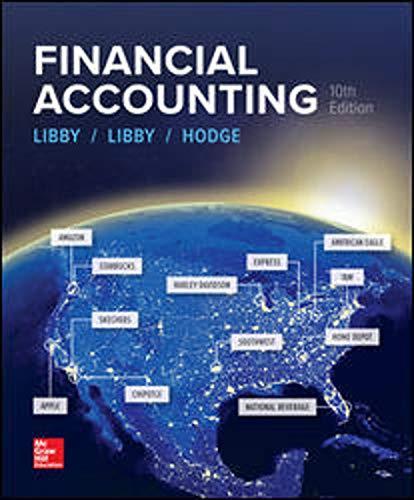
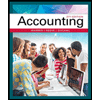
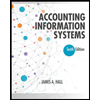
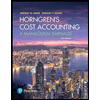
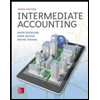
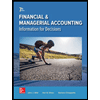