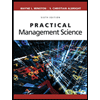
K65.
The Talbot Company uses electrical assemblies to produce an array of small appliances. One of its high cost / high volume assemblies, the XO-01, has an estimated annual demand of 8,000 units. Talbot estimates the cost to place an order is $50, and the holding cost for each assembly is $10 per year. The company operates 250 days per year.
What is the Total Annual Cost (that is, Annual Holding Cost plus Annual Ordering Cost) if Talbot orders using the Economic Order Quantity (EOQ)? (choose the range below which contains the correct answer)
Group of answer choices:
greater than $6,000
greater than $5,000 but less than or equal to $6,000
greater than $4,000 but less than or equal to $5,000
greater than $3,000 but less than or equal to $4,000
less than or equal to $3,000

Trending nowThis is a popular solution!
Step by stepSolved in 2 steps

- Johnson Tire Plaza (JTP) is a large chain of tire shops, who sells various brand of automobile tires. The yearly demand of a particular brand of time is about 8,888 units per year. JTP purchases these tires from a supplier. The ordering cost is $124 per order and the holding cost is $19 per tire per year. The supplier always deliver the shipment within 6 days after receiving a replenishment order from JTP. The company operates 250 days per year. Assume EOQ model is applicable. What is the optimal annual inventory cost for JTP? Use at least 4 decimal places.arrow_forwardSoutheastern Bell stocks a certain switch connector at its central warehouse for supplying field service offices. The yearly demand for these connectors is 15,200 units. Southeastern estimates its annual holding cost for this item to be 323 per unit. The cost to place and process an order from the supplier is $73. The company operates 300 days per year, and the lead time to receive an order from the supplier is 2 working days. a) What is the economic order quantity? units (round your response to the nearest whole number). b) What are the annual holding costs? $ (round your response to the nearest whole number) c) What are the annual ordering costs? S (round your response to the nearest whole number). d) What is the reorder point? units (round your response to the nearest whole number).arrow_forwardList the major assumptions of the EOQ modelarrow_forward
- Matthew Liotine's Dream Store sells water beds and assorted supplies. His best-selling bed has an annual demand of 405 units. Ordering cost is $38; holding cost is $5 per unit per year. a) To minimize the total cost, how many units should be ordered each time an order is placed? EOQ = units (round your response to the nearest whole number). b) If the holding cost per unit was $6.00 instead of $5, what would the optimal order quantity be? New EOQ = units (round your response to the nearest whole number). Aarrow_forwardAnnual demand (D) is 49,000 units. Ordering Cost (S) is $1,000 per order. Holding cost (H) is $2 per unit per year. Find economic order quantity (Q*). 7,000 units 49,000,000 units 4,950 units 3,500 units 4,083 unitsarrow_forwardIf annual demand is 12,000 units, annual holding cost is $15 per unit, and setup cost per order is $25, what is the EOQ lot size?arrow_forward
- Southeastern Bell stocks a certain switch connector at its central warehouse for supplying field service offices. The yearly demand for these connectors is 15,500 units. Southeastern estimates its annual holding cost for this item to be $23 per unit. The cost to place and process an order from the supplier is $78. The company operates 300 days per year, and the lead time to receive an order from the supplier is 3 working days. a) What is the economic order quantity? units (round your response to the nearest whole number). (round your response to the nearest whole number). b) What are the annual holding costs? $ c) What are the annual ordering costs? $ (round your response to the nearest whole number). d) What is the reorder point? units (round your response to the nearest whole number).arrow_forwardAaBbCc AaBbCc AaBbCc No Spacing Normal Reuse Heading 1 Replace Files Paragraph Styles Editing Reuse Files Item SKU A3378 has a demand that is normally distributed during the lead time, with a mean of 360 units and standard deviation of 12. If Hinsdale cannot have stockouts in more than 10% of the time in any order, how much safety stock should be maintained and at what reorder point? 1. SKU F5402: daily demand is normally distributed with a mean of 16, standard deviation of 4, lead time is 4 days, and must operate at a 95% service level. 2. SKU B7319: daily demand is constant at 24 units per day, lead time is normally with a mean of 6 days and standard deviation of 2 days, and must operate at a 95% service level. 3. SKU F9004: daily demand is normally distributed with a mean of 21 units and a standard deviation of 3 days. The lead time is also normally distributed with a mean of 4 days, standard deviation of 2 days, and a service level of 90% is required. dictions: On acer %24 4. % &…arrow_forwardCape Fear Hospital consumed 400 boxes of bandages per week last year. The price of bandages was $80 per box, and the hospital operates 52 weeks per year. The cost of processing an order was $64, and the cost of holding one box throughout a full year was 20% of the value of the material. What is the EOQ? 407 boxes 102 boxes O 408 boxes O 57 boxesarrow_forward
- Practical Management ScienceOperations ManagementISBN:9781337406659Author:WINSTON, Wayne L.Publisher:Cengage,Operations ManagementOperations ManagementISBN:9781259667473Author:William J StevensonPublisher:McGraw-Hill EducationOperations and Supply Chain Management (Mcgraw-hi...Operations ManagementISBN:9781259666100Author:F. Robert Jacobs, Richard B ChasePublisher:McGraw-Hill Education
- Purchasing and Supply Chain ManagementOperations ManagementISBN:9781285869681Author:Robert M. Monczka, Robert B. Handfield, Larry C. Giunipero, James L. PattersonPublisher:Cengage LearningProduction and Operations Analysis, Seventh Editi...Operations ManagementISBN:9781478623069Author:Steven Nahmias, Tava Lennon OlsenPublisher:Waveland Press, Inc.
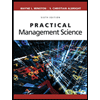
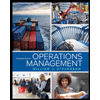
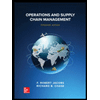
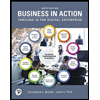
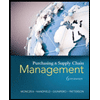
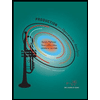