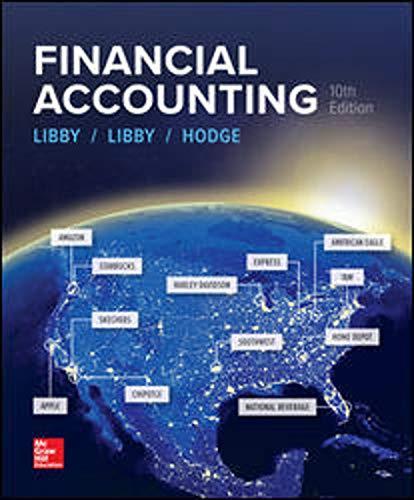
Concept explainers
JFI Foods produces processed foods. Its basic ingredient is a feedstock that is mixed with other ingredients to produce the final packaged product. JFI purchases the feedstock from two suppliers, Rex Materials and Red Oak Chemicals. The quality of the final product depends directly on the quality of the feedstock. If the feedstock is not correct, JFI has to dispose of the entire batch. All feedstock in this business is occasionally "bad," so JFI measures what it calls the "yield," which is measured as,
Yield = Good output ÷ Input
where the output and inputs are both measured in tons. As a benchmark, JFI expects to get 11 tons of good output for every 20 tons of feedstock purchased for a yield of 55 percent (= 11 tons of output ÷ 20 tons of feedstock).
Data on the two suppliers for the past year follow:
Rex Materials | Red Oak Chemicals | Total | |||||||
Total inputs purchased (tons) | 1,380 | 2,280 | 3,660 | ||||||
Good output (tons) | 1,311 | 1,578 | 2,889 | ||||||
Average price (per ton) | $ | 195 | $ | 155 | $ | 170 | |||
Required:
Assume that the average quality, measured by the yield, and prices from the two companies will continue as in the past. What is the effective price for feedstock from the two companies when quality is considered? (Round intermediate calculations and final answers to 2 decimal places.)

Trending nowThis is a popular solution!
Step by stepSolved in 2 steps

- Watko Entertainment Systems (WES) buys audio and video components for assembling home entertainment systems from two suppliers, Bacon Electronics and Hessel Audio and Video. The components are delivered in cartons. If the cartons are delivered late, the installation for the customer is delayed. Delayed installations lead to contractual penalties that call for WES to reimburse a portion of the purchase price to the customer. During the past quarter, the purchasing and delivery data for the two suppliers showed the following: Bacon 5,000 $ 182 40 Total purchases (cartons) Average purchase price (per carton) Number of deliveries Percentage of cartons delivered late. 30% Bacon Hessel Hessel 3,000 $198 20 15% The Accounting Department recorded $255,450 as the cost of late deliveries to customers. Effective Cost Per Carton Total 8,000 $ 188 60 25% Exercise 10-38 (Algo) Activity-Based Costing of Suppliers (LO 10-3, 4) Required: Assume that the average quality, measured by the percentage of…arrow_forwardFeinan Sports, Inc., manufactures sporting equipment, including weight-lifting gloves. Anational sporting goods chain recently submitted a special order for 4,000 pairs of weight-liftinggloves. Feinan Sports was not operating at capacity and could use the extra business.Unfortunately, the order’s offering price of $12.70 per pair was below the cost to produce them.The controller was opposed to taking a loss on the deal. However, the personnel manager arguedin favor of accepting the order even though a loss would be incurred; it would avoid the problemof layoffs and would help maintain the community image of the company. The full cost toproduce a pair of weight-lifting gloves is presented below.Direct materials $ 7.40Direct labor 3.80Variable overhead 1.60Fixed overhead 3.10 Total $15.90No variable selling or administrative expenses would be associated with the order. Non-unitlevel activity costs are a small percentage of total costs and are therefore not considered.Required:1. Assume…arrow_forwardIs Dave behaving unethically by trying to force the Semiconductor Division into a price break? Comment on Howard's reactions.arrow_forward
- The Cook Company operates a simple chemical process to convert a single material into three separate items, referred to here as X, Y, and Z. All three end products are separated simultaneously at a single splitoff point. Products X and Y are ready for sale immediately upon splitoff without further processing or any other additional costs. Product Z, however, is processed further before being sold. There is no available market price for Z at the splitoff point. The selling prices quoted here are expected to remain the same in the coming year. During 2017, the selling prices of the items and the total amounts sold were as follows: ■ X—68 tons sold for $1,200 per ton ■ Y—480 tons sold for $900 per ton ■ Z—672 tons sold for $600 per ton The total joint manufacturing costs for the year were $580,000. Cook spent an additional $200,000 to finish product Z. There were no beginning inventories of X, Y, or Z. At the end of the year, the following inventories of completed units were on hand: X,…arrow_forwardZodiac Sound Company manufactures audio systems, both made-to-order and mass-produced systems that are typically sold to large- scale manufacturers of electronics equipment. For competitive reasons, the company is trying to increase its manufacturing cycle efficiency (MCE) measure. As a strategy for improving its MCE performance, the company is considering a switch to JIT manufacturing. While the company managers have a fairly good feel for the costs of implementing JIT, they are unsure about the benefits of such a move, both in financial and nonfinancial terms. To help inform the ultimate decision regarding a move to a JIT system, you've been asked to provide some input. Fortunately, you've recently attended a continuing professional education (CPE) workshop on the costs and benefits of moving to JIT and therefore feel comfortable responding to management's request. Required: 3. Given the estimated data below, calculate the MCE for both the current manufacturing process and the…arrow_forwardHaving trouble with some questions from the last chapter.arrow_forward
- Branded Shoe Company manufactures only one type of shoe and has two divisions, the Stitching Division and the Polishing Division. The Stitching Division manufactures shoes for the Polishing Division, which completes the shoes and sells them to retailers. The Stitching Division "sells" shoes to the Polishing Division. The market price for the Polishing Division to purchase a pair of shoes is $42.00.(Ignore changes in inventory.) The fixed costs for the Stitching Division are assumed to be the same over the range of 40,000−101,000units. The fixed costs for the Polishing Division are assumed to be $19.00per pair at 101,000 units. Stitching's costs per pair of shoes are: Direct materials $15.00 Direct labor $13.00 Variable overhead $11.00 Division fixed costs $9.00 Polishing's costs per completed pair of shoes are: Direct materials $16.00 Direct labor $10.00 Variable overhead $7.00 Division fixed costs $18.00 What is the market−based transfer price per pair of shoes from…arrow_forwardBoney Corporation processes sugar beets that it purchases from farmers. Sugar beets are processed in batches. A batch of sugar beets costs $53 to buy from farmers and $18 to crush in the company's plant. Two intermediate products, beet fiber and beet juice, emerge from the crushing process. The beet fiber can be sold as is for $25 or processed further for $18 to make the end product industrial fiber that is sold for $39. The beet juice can be sold as is for $32 or processed further for $28 to make the end product refined sugar that is sold for $79. What is the financial advantage (disadvantage) for the company from processing the intermediate product beet juice into refined sugar rather than selling it as is?arrow_forwardWatko Entertainment Systems (WES) buys audio and video components for assembling home entertainment systems from two suppliers, Bacon Electronics and Hessel Audio and Video. The components are delivered in cartons. If the cartons are delivered late, the installation for the customer is delayed. Delayed installations lead to contractual penalties that call for WES to reimburse a portion of the purchase price to the customer. During the past quarter, the purchasing and delivery data for the two suppliers showed the following: Bacon 5,000 $ 192 40 30% Bacon Hessel Hessel 3,000 $ 208 Total purchases (cartons) Average purchase price (per carton) Number of deliveries Percentage of cartons delivered late. The Accounting Department recorded $265,200 as the cost of late deliveries to customers. Effective Cost Per Carton Total 8,000 $ 198 20 15% Required: Assume that the average quality, measured by the percentage of late deliveries, and prices from the two companies will continue as in the…arrow_forward
- Maglie Company manufactures two video game consoles: handheld and home. The handheld consoles are smaller and less expensive than the home consoles. The company only recently began producing the home model. Since the introduction of the new product, profits have been steadily declining. Management believes that the accounting system is not accurately allocating costs to products, particularly because sales of the new product have been increasing. Management has asked you to investigate the cost allocation problem. You find that manufacturing overhead is currently assigned to products based on their direct labor costs. For your investigation, you have data from last year. Manufacturing overhead was $1,237,000 based on production of 290,000 handheld consoles and 100,000 home consoles. Direct labor and direct materials costs were as follows. Handheld Home Total Direct labor $ 1,135,250 $ 411,000 $ 1,546,250 Materials 700,000 671,000 1,371,000…arrow_forwardJFI Foods produces processed foods. Its basic ingredient is a feedstock that is mixed with other ingredients to produce the final packaged product. JFI purchases the feedstock from two suppliers, Rex Materials and Red Oak Chemicals. The quality of the final product depends directly on the quality of the feedstock. If the feedstock is not correct, JFI has to dispose of the entire batch. All feedstock in this business is occasionally "bad," so JFI measures what it calls the "yield," which is measured as, Yield = Good output ÷ Input where the output and inputs are both measured in tons. As a benchmark, JFI expects to get 11 tons of good output for every 20 tons of feedstock purchased for a yield of 55 percent (= 11 tons of output ÷ 20 tons of feedstock). Data on the two suppliers for the past year follow: Rex Materials Red Oak Chemicals Total Total inputs purchased (tons) 1,380 2,280 3,660 Good output (tons) 1,311 1,578 2,889 Average price…arrow_forwardNote:- Do not provide handwritten solution. Maintain accuracy and quality in your answer. Take care of plagiarism. Answer completely. You will get up vote for sure.arrow_forward
- AccountingAccountingISBN:9781337272094Author:WARREN, Carl S., Reeve, James M., Duchac, Jonathan E.Publisher:Cengage Learning,Accounting Information SystemsAccountingISBN:9781337619202Author:Hall, James A.Publisher:Cengage Learning,
- Horngren's Cost Accounting: A Managerial Emphasis...AccountingISBN:9780134475585Author:Srikant M. Datar, Madhav V. RajanPublisher:PEARSONIntermediate AccountingAccountingISBN:9781259722660Author:J. David Spiceland, Mark W. Nelson, Wayne M ThomasPublisher:McGraw-Hill EducationFinancial and Managerial AccountingAccountingISBN:9781259726705Author:John J Wild, Ken W. Shaw, Barbara Chiappetta Fundamental Accounting PrinciplesPublisher:McGraw-Hill Education
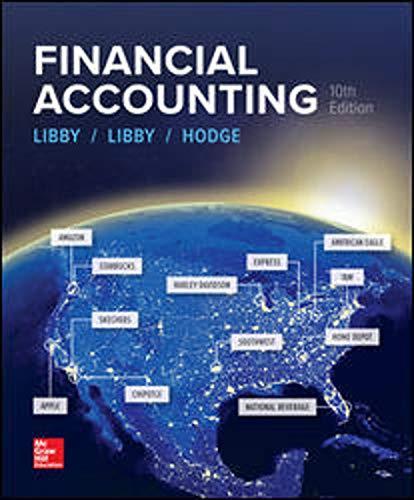
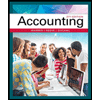
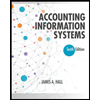
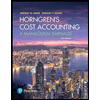
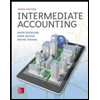
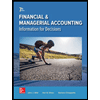