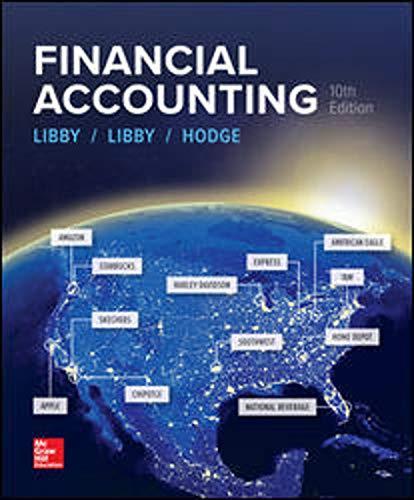
Intercontinental Chemical Company, located in Buenos Aires, Argentina, recently received an order for a product it does not normally produce. Since the company has excess production capacity, management is considering accepting the order. In analyzing the decision, the assistant controller is compiling the relevant costs of producing the order. Production of the special order would require 8,000 kilograms of theolite. Intercontinental does not use theolite for its regular product, but the firm has 8,000 kilograms of the chemical on hand from the days when it used theolite regularly. The theolite could be sold to a chemical wholesaler for 14,500 p. The book value of the theolite is 2.00 p per kilogram. Intercontinental could buy theolite for 2.40 p per kilogram. ( p denotes the peso, Argentina’s national monetary unit. Many countries use the peso as their unit of currency. On the day this exercise was written, Argentina’s
peso was worth .104 U.S. dollar.)
Required:
1. What is the relevant cost of theolite for the purpose of analyzing the special-order decision? (Remember to express your answer in terms of Argentina’s peso.)
2. Discuss each of the numbers given in the exercise with regard to its relevance in making the decision.

Trending nowThis is a popular solution!
Step by stepSolved in 3 steps

- Johnson Limited is contemplating the installation of a new system that would allow for automated handling of customer inquiries about their order status, account balances, etc. Currently all such inquiries are handled manually by customer service representatives. The software for the new system would cost $214,000. An additional $169,000 would be required for one-time installation costs. Management estimates that the new system would result in costs of $10,300 per year related to addressing software issues and other technological problems that may arise. However, the new system is expected to reduce labour costs by $65,000 per year. Management estimates that the system would be used for five years. Severance costs related to the employees that would be laid off after implementing the new system would be $22,600. Johnson Limited requires a return of at least 15% on investments of this type. Required: Ignore income taxes. 1. Compute the net annual cost savings promised by the new system.…arrow_forwardYardwork Tools Corp manufactures garden tools in a factory in Taneytown, Maryland. Recently, the company designed a collection of tools for professional use rather than consumer use. Management needs to make a good decision about whether to produce this line in their existing space in Maryland, where space is available or to accept an offer from a manufacturer in Taiwan. Data concerning the decision are as follows: Expected annual sales of tools (in units) 660,000 Average selling price of tools $11 Price quoted by Taiwanese company, in New Taiwanese Dollars (NTD) 27,300 Current exchange rate 9,100 NTD = $1 Variable manufacturing costs $2.85 per unit Incremental annual fixed manufacturing costs associated with the new product line $310,000 Variable selling and distribution costsª $0.50 per unit Annual fixed selling and distribution costsª $250,000 ªSelling and distribution costs are the same regardless of whether the tools…arrow_forwardGrant Industries, a manufacturer of electronic parts, has recently received an invitation to bid on a special order for 20,500 units of one of its most popular products. Grant currently manufactures 41,000 units of this product in its Loveland, Ohio, plant. The plant is operating at 50% capacity. There will be no marketing costs on the special order. The sales manager of Grant wants to set the bid at $15 because she is sure that Grant will get the business at that price. Others on the executive committee of the firm object, saying that Grant would lose money on the special order at that price. Units Manufacturing costs: Direct materials Direct labor Factory overhead 41,000 61,500 $ 164,000 205,000 328,000 $ 246,000 307,500 430,500 $ 984,000 Total manufacturing costs $ 697,000 $ 17 Unit cost $ 16 Required: 2. What is the relevant cost per unit? What do you think the minimum short-term bid price per unit should be? What would be the impact on short-term operating income if the order is…arrow_forward
- Feinan Sports, Inc., manufactures sporting equipment, including weight-lifting gloves. Anational sporting goods chain recently submitted a special order for 4,000 pairs of weight-liftinggloves. Feinan Sports was not operating at capacity and could use the extra business.Unfortunately, the order’s offering price of $12.70 per pair was below the cost to produce them.The controller was opposed to taking a loss on the deal. However, the personnel manager arguedin favor of accepting the order even though a loss would be incurred; it would avoid the problemof layoffs and would help maintain the community image of the company. The full cost toproduce a pair of weight-lifting gloves is presented below.Direct materials $ 7.40Direct labor 3.80Variable overhead 1.60Fixed overhead 3.10 Total $15.90No variable selling or administrative expenses would be associated with the order. Non-unitlevel activity costs are a small percentage of total costs and are therefore not considered.Required:1. Assume…arrow_forwardDeli's Fudge Factory currently makes fudge for retail and mail order customers. It also offers a variety of roasted nuts. Fudge sales have increased over the past year, so Deli is considering outsourcing the roasted nuts and using the roasting space to make additional fudge. A reliable supplier has quoted a price of £0.85 per pound for the roasted nuts. The following amounts reflect the in-house manufacturing costs per pound for the roasted nuts: Direct materials Direct labour Unit-related support costs Batch-related support costs Product-sustaining support costs Facility-sustaining support costs Total cost per pound £0.50 0.06 0.10 0.04 0.05 0.15 £0.90 Required: Should Deli's Fudge Factory outsource the roasted nuts? Why or why not? Discuss all items that should be considered. a.arrow_forwardTania Company manufactures watches. A national sporting goods chain recentlysubmitted a special order for 4,000 sport watches. Tania was not operating at capacityand could use the extra business. Unfortunately, the order’s offering price of RM17 perwatch was below the cost to produce the watches. The controller did not agree to take aloss on the deal. However, the personnel manager argued in favor of accepting theorder even though a loss would be incurred: it would avoid the problems of layoff andwould help maintain the community image of the company. The following informationis the full cost to produce a sport watch:Table 6: Production CostsDetails Unit CostRMDirect materials 6.50Direct labor 5.00Variable overhead 3.25Fixed overhead 2.50Total 17.25 List the relevant costs of the two alternatives of the special order. (ii) Propose whether operating income increase or decrease if the order is acceptedarrow_forward
- TufStuff, Inc., sells a wide range of drums, bins, boxes, and other containers that are used in the chemical industry. One of the company’s products is a heavy-duty corrosion-resistant metal drum, called the WVD drum, used to store toxic wastes. Production is constrained by the capacity of an automated welding machine that is used to make precision welds. A total of 2,000 hours of welding time is available annually on the machine. Because each drum requires 0.4 hours of welding machine time, annual production is limited to 5,000 drums. At present, the welding machine is used exclusively to make the WVD drums. The accounting department has provided the following financial data concerning the WVD drums: WVD Drums Selling price per drum $ 149.00 Cost per drum: Direct materials $52.10 Direct labor ($18 per hour) 3.60 Manufacturing overhead 4.50 Selling and administrative expense 29.80 90.00 Margin per drum $ 59.00 Management…arrow_forwardFyodor Corporation has a Parts Division that does work for other Divisions in the company as well as for outside customers. The company's Machine Division has asked the Parts Division to provide it with 6,000 special parts each year. The special parts would require $21 per unit in variable production costs. The Machine Division has a bid from an outside supplier for the special parts at $31.20 per unit. In order to have time and space to produce the special part, the Parts Division would have to cut back production of another part-the QR4 that it presently is producing. The QR4 sells for $40 per unit and requires $20 per unit in variable production costs. Packaging and shipping costs of the QR4 are $2 per unit. Packaging and shipping costs for the new special part would be only $0.50 per unit. The Parts Division is now producing and selling 30,000 units of the QR4 each year. Production and sales of the QR4 would drop by 5% if the new special part is produced for the Machine Division.…arrow_forwardA manager of Burns Sporting Goods Company is considering accepting an order from an overseas customer. This customer has requested an order for 200,000 dozen golf balls at a price of $22 per dozen. The variable cost to manufacture a dozen golf balls is $18 per dozen. The full cost is $25 per dozen. Burns Sporting Goods Company plant has just enough excess capacity on the second shift to make the overseas order. Discuss the considerations in accepting or rejecting the order.arrow_forward
- Edin-Chem Ltd. is a small company that acquires high-grade crude oil from low volume producing wells owned by individuals. The crude oil is processed in a single refinery into Two Oil, Six Oil, and impure distillates. Edin-Chem does not have the technology or capacity to process these products further and sells most of its putput each month to major refineries. There were no beginning finished goods or work-in-process inventories on January 1. The production costs and output of Edin-Chem for January are as follows: 1. Crude oil acquired and placed into production £5,000,000 Direct labour and related costs 2,000,000 Manufacturing overhead 3,000,000 2. Production and sales: Two Oil: Six Oil: Required: 300,000 barrels produced; 80,000 barrels sold at £20 each 240,000 barrels produced; 120,000 barrels sold at £30 each Distillates: 120,000 barrels produced and sold at £15 per barrel Calculate the amount of joint production cost that Edin-Chem would allocate to each of the three joint…arrow_forwardIn the last 6 months, demand for one of Appleby Company's products has dropped off considerably, due mainly to it becoming obsolescent as a result of technological change. Knowing that the equipment used in the manufacture of this product may not be easy to sell, Appleby spent $50,000 on consultants to determine whether it could use the equipment to produce a new product under license by another company. The consultant has determined that this product would have variable production costs of $65 per unit and should sell at a price of $90/unit. The licensing royalty is 5% of gross product revenue. Estimated annual demand is 20,000 units per year. Additional annual operating costs related to this product are $30,000/year (excluding depreciation). Depreciation on the equipment is $15,000. Annual depreciation expense is a: O a. Sunk cost O b. Relevant cost O c. Both sunk and Irrelevant cost Od. Irrelevant costarrow_forwardThompson Industrial Products Inc. (TIPI) is a diversified industrial-cleaner processing company. The company's Dargan plant produces two products: a table cleaner and a floor cleaner from a common set of chemical inputs (CDG). Each week, 945,000 ounces of chemical input are processed at a cost of $213,000 into 630,000 ounces of floor cleaner and 315,000 ounces of table cleaner. The floor cleaner has no market value until it is converted into a polish with the trade name FloorShine. The additional processing costs for this conversion amount to $244,200, Floor Shine sells at $20 per 30-ounce bottle. The table cleaner can be sold for $21 per 25-ounce bottle. However, the table cleaner can be converted into two other products by adding 315,000 ounces of another compound (TCP) to the 315,000 ounces of table cleaner. This joint process will yield 315,000 ounces each of table stain remover (TSR) and table polish (TP). The additional processing costs for this process amount to $102,000. Both…arrow_forward
- AccountingAccountingISBN:9781337272094Author:WARREN, Carl S., Reeve, James M., Duchac, Jonathan E.Publisher:Cengage Learning,Accounting Information SystemsAccountingISBN:9781337619202Author:Hall, James A.Publisher:Cengage Learning,
- Horngren's Cost Accounting: A Managerial Emphasis...AccountingISBN:9780134475585Author:Srikant M. Datar, Madhav V. RajanPublisher:PEARSONIntermediate AccountingAccountingISBN:9781259722660Author:J. David Spiceland, Mark W. Nelson, Wayne M ThomasPublisher:McGraw-Hill EducationFinancial and Managerial AccountingAccountingISBN:9781259726705Author:John J Wild, Ken W. Shaw, Barbara Chiappetta Fundamental Accounting PrinciplesPublisher:McGraw-Hill Education
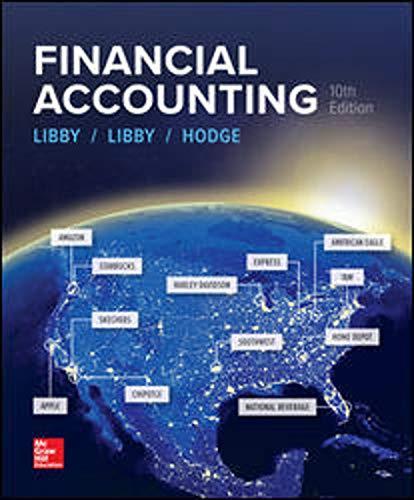
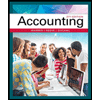
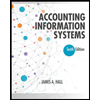
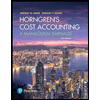
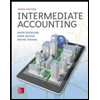
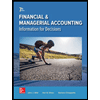