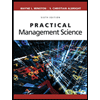
Practical Management Science
6th Edition
ISBN: 9781337406659
Author: WINSTON, Wayne L.
Publisher: Cengage,
expand_more
expand_more
format_list_bulleted
Concept explainers
Topic Video
Question
Henrique Correa’s bakery prepares all its cakes
between 4 a.m. and 6 a.m. so they will be fresh when customers arrive. Day-old cakes are virtually always sold, but at a
50% discount off the regular $10 price. The cost of baking a
cake is $6, and demand is estimated to be
is the optimal stocking level?
Expert Solution

This question has been solved!
Explore an expertly crafted, step-by-step solution for a thorough understanding of key concepts.
This is a popular solution
Trending nowThis is a popular solution!
Step by stepSolved in 2 steps

Knowledge Booster
Learn more about
Need a deep-dive on the concept behind this application? Look no further. Learn more about this topic, operations-management and related others by exploring similar questions and additional content below.Similar questions
- Kooyman hardware sells 31 different types of drills. They had demand for 25 of the drills and satisfied 78 percent of the demand. What was their fill rate for drills? % ( Do not round intermediate calculations.arrow_forwardDavid's Delicatessen flies in Hebrew National salamis regularly to satisfy a growing demand for the salamis in Silicon Valley. The owner, David Gold, estimates that the demand for the salamis is pretty steady at 175 per month. The salamis cost Gold $1.85 each. The fixed cost of calling his brother in New York and having the salamis flown in is $200. It takes three weeks to receive an order. Gold's accountant, Irving Wu, recommendsan annual cost of capital of 22 percent, a cost of shelf space of 3 percent of the value of the item, and a cost of 2 percent of the value for taxes and insurance. How many salamis should Gold have on hand when he phones his brother to send another shipment?arrow_forwardXYZ company has determined that the annual demand for type A material is 20,000 pounds. Salma, who works in her brother's factory, is in charge of purchasing. She estimates that it costs $15 every time an order is placed. This cost includes her wages, the cost of the forms used in placing the order, and so on. Furthermore, she estimates that the cost of carrying one pound in inventory for a year is 0.05 $. Assume that the demand is constant throughout the year. (Note: $ is a dollar sign) a) If we are going to use the EOQ inventory model, mention all the assumptions that are made to validate that model. b) How many pounds of type A material should Huda order (i.e. Q*) at a time if she wishes to minimize total inventory cost? c) How many orders per year would be placed? d) What would the annual ordering cost be? e) What would the average inventory be? f) What would the annual holding cost be? See equations below if needed: Annual Ordering cost Annual hdding: Number of orders placed per…arrow_forward
- 1. HP produces printers for sale in Europe in its Vancouver, Canada factory. Printers sold in different countries differ in terms of the power outlet as well as the language manuals. Currently HP assembles and packs printers for sale in individual countries. The distribution of weekly demand in different countries is normally distributed with mean an standard deviation as shown in the Table below. Assume demand in different countries to be independent. Given that the lead time from the Vancouver factory is six weeks, how much total safety inventory does HP require in Europe if it targets a cycle service level of 95 percent? Country France/Benelux UK/Ireland Germany Italy/Spain/Portugal Demand Forecast 3000 4000 4000 2500 Standard Deviation 2000 2200 1250 800 EAMO2 ad of el how A utarase sit themsi What if HP decides to build a central distribution center (DC) in Europe. It will ship base printers (without power supply) to the new DC. When an order is received, the DC will assemble…arrow_forwardMancuso's Music Store is a small business that sells instruments, books, stands, and other music-related products. The owner always likes to have extra music stands in storage in case a large order arrives suddenly - typically 2 weeks' worth of sales. When an order is placed, the delivery takes 5 business days to arrive. The owner has studied working capital management and estimates that the economic order quantity for music stands is 1500 for each time an order is placed. The fixed cost of an order is $210 and the carrying cost per stand per year is $1.70. How many music stands will the store have in stock immediately after a shipment arrives? Assume the store is closed on Sundays (a 6-day business week), holidays, and a few vacation days, so that the store has 300 business days per year. Give your answer rounded to the nearest whole number of music stands. Do not include comma separators in your answer.arrow_forwardUnited Airlines has an agreement to buy jet fuel from Exxon. The goal is to minimize total cost (i.e., ordering cost + holding cost). The annual demand for fuel is 201,000 barrels. Exxon charges United $3740 to process each order. United incurs a holding cost of $20 per barrel. When purchasing using the EOQ (from last question), what is the order cycle time (days between orders) for United? Note: round your answer to the nearest 1 decimal place. For example, answer like 12.3 Answer: Checkarrow_forward
- The local supermarket buys lettuce each day to ensure really fresh produce. Each morning, any lettuce that is left from the previous day is sold to a dealer that resells it to farmers who use it to feed their animals. This week, the supermarket can buy fresh lettuce for $8.00 a box. The lettuce is sold for $16.00 a box and the dealer that sells old lettuce is willing to pay $1.80 a box. Past history says that tomorrow's demand for lettuce averages 245 boxes with a standard deviation of 38 boxes. How many boxes of lettuce should the supermarket purchase tomorrow? (Use Excel's NORMSINV() function to find the correct critical value for the given a-level. Do not round intermediate calculations. Round your answer to the nearest whole number.) Number of boxesarrow_forward1. Demand for walnut fudge ice cream at the Sweet Cream Dairy can be approximated by a normal distribution with a mean of 21 gallons per week and a standard deviation of 5 gallons per week. The new manager desires a service level of 90 percent. Lead time is 8 days, and the dairy is open seven days a week. (Hint: Work in terms of weeks.) If the ROP model is used, what is the appropriate safety stock level to achieve the desired service level? Round to two decimal places. Answer: _________arrow_forwardNEED ALL THREE QUESTIONS Item X is a standard item stocked in a company's inventory of component parts. Each year the firm, on a random basis, uses about 2,700 of item X, which costs $25 each. Storage costs, which include insurance and cost of capital, amount to $9 per unit of average inventory. Every time an order is placed for more item X, it costs $6. a. Whenever item X is ordered, what should the order size be? (Round your answer to the nearest whole number.) b. What is the annual cost for ordering item X? (Round your answer to 2 decimal places.) c. What is the annual cost for storing item X? (Round your answer to 2 decimal places.)arrow_forward
arrow_back_ios
arrow_forward_ios
Recommended textbooks for you
- Practical Management ScienceOperations ManagementISBN:9781337406659Author:WINSTON, Wayne L.Publisher:Cengage,Operations ManagementOperations ManagementISBN:9781259667473Author:William J StevensonPublisher:McGraw-Hill EducationOperations and Supply Chain Management (Mcgraw-hi...Operations ManagementISBN:9781259666100Author:F. Robert Jacobs, Richard B ChasePublisher:McGraw-Hill Education
- Purchasing and Supply Chain ManagementOperations ManagementISBN:9781285869681Author:Robert M. Monczka, Robert B. Handfield, Larry C. Giunipero, James L. PattersonPublisher:Cengage LearningProduction and Operations Analysis, Seventh Editi...Operations ManagementISBN:9781478623069Author:Steven Nahmias, Tava Lennon OlsenPublisher:Waveland Press, Inc.
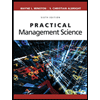
Practical Management Science
Operations Management
ISBN:9781337406659
Author:WINSTON, Wayne L.
Publisher:Cengage,
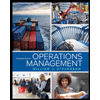
Operations Management
Operations Management
ISBN:9781259667473
Author:William J Stevenson
Publisher:McGraw-Hill Education
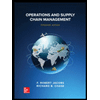
Operations and Supply Chain Management (Mcgraw-hi...
Operations Management
ISBN:9781259666100
Author:F. Robert Jacobs, Richard B Chase
Publisher:McGraw-Hill Education
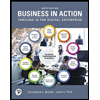
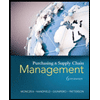
Purchasing and Supply Chain Management
Operations Management
ISBN:9781285869681
Author:Robert M. Monczka, Robert B. Handfield, Larry C. Giunipero, James L. Patterson
Publisher:Cengage Learning
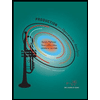
Production and Operations Analysis, Seventh Editi...
Operations Management
ISBN:9781478623069
Author:Steven Nahmias, Tava Lennon Olsen
Publisher:Waveland Press, Inc.