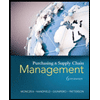
Purchasing and Supply Chain Management
6th Edition
ISBN: 9781285869681
Author: Robert M. Monczka, Robert B. Handfield, Larry C. Giunipero, James L. Patterson
Publisher: Cengage Learning
expand_more
expand_more
format_list_bulleted
Question
Given the projected changes in America’s
demographics, name five products that will face
increasing demand and five that will face declining
demand
Expert Solution

This question has been solved!
Explore an expertly crafted, step-by-step solution for a thorough understanding of key concepts.
This is a popular solution
Trending nowThis is a popular solution!
Step by stepSolved in 2 steps

Knowledge Booster
Learn more about
Need a deep-dive on the concept behind this application? Look no further. Learn more about this topic, marketing and related others by exploring similar questions and additional content below.Similar questions
- Look at the Acer case at the beginning of the chapter and respond to the following items. 2. What goals did they accomplish?arrow_forwardWhat can McDonalds do to address Bakshis concerns?arrow_forwardThe case focuses on U.S. markets. How are European markets affected by holiday shopping?arrow_forward
- What other uses and functions does Input Accel serve, and how will this be useful to Novartis over the long term? (You may want to visit the EMC/Captiva website. https://www.emc.com. for more information on Input Accels capabilities.)arrow_forwardInside Teslas Strategy for Growth Tesla has been pursuing a strategy of aggressive growth since its founding in 2003. The companys mission is to accelerate the move to vehicles that will save energy while saving the planet. The key word here is accelerate. Teslas strategy combines a long-term vision of a world fueled by renewable energy with a sense of urgency about creating Earth-friendly vehicles that customers will want to drive now. Because it relies heavily on technology, its not surprising that Tesla is based in Palo Alto, California, home to tech giants like Hewlett Packard and Facebook. The firm operates a single, highly automated manufacturing plant in Fremont, California. It also built its own massive production facility to supply lithium-ion batteries for its vehicles and developed a network of charging stations from coast to coast. Instead of selling through dealers, Teslas strategy is to sell directly to consumers. This unusual arrangement allows more control over the sales process and yields a higher profit margin per vehicle, because dealers arent part of the distribution channel. In planning its products, Tesla has gone beyond the green appeal to showcase the style, speed, and status of its vehicles, marketing to people who want a special driving experience. Consider the Roadster, a snappy, low-slung sports car introduced in 2008. The attractive and sporty Roadster broke the mold for traditional electric cars and rocketed Tesla into the public eye. The company stopped selling the Roadster in 2011 as it focused on launching the Model S, a stylish, high-end, high-performance sedan with self-driving capabilities. The head designer knew he had to create an all-electric sedan that would stand out in a crowded field of competing vehicles made by international giants such as Audi, BMW, and Mercedes. His design blends the best of today and tomorrow, creating a classically elegant yet forward-looking exterior. Just as important, the Model S has an extended driving range, thanks to the companys advanced battery technology. Next, Tesla introduced the head-turning Model X, a luxury SUV with unique falcon wing passenger doors that open upward for access to rear seating. Thousands of consumers rushed to put down a deposit for this new product, eager to be among the first owners. Despite strong demand, the company struggled to increase production output because of the complexities of manufacturing the unique vehicle and because of parts shortages. Tesla delayed deliveries for months while it ironed out these problems. Expanding the product line and targeting a new customer segment, Tesla then introduced the Model 3. This sedan is more affordably priced than the firms previous vehicles, part of the strategy to enter the mainstream of high-volume, all-electric car marketing. The Model 3 has a modern, uncluttered look with curb appeal. The dashboard is similarly uncluttered, replacing the usual gaggle of gadgets and buttons with one touch-screen control panel. Enhancing Teslas reputation for technology, the Model 3s autopilot feature allows for some driverless operations. More than 450,000 people have already submitted a deposit of 1,000 each to reserve a Model 3. Still, Tesla has had difficulty bringing production to full throttle and, as a result, has been forced to delay some deliveries. Looking ahead to the long-term goal of producing 500,000 vehicles per year and profiting from economies of scale, Tesla is hiring thousands of employees and revamping facilities for higher output. It is preparing for several product introductions, including a new Roadster sports car, a Model Y crossover vehicle, and a Semi truck. Can Tesla achieve sustained profitability as it races to meet its ambitious goals, tries to outpace competitors, and seeks to accelerate the transition to renewable energy?30 What are Teslas core competencies, and how do they help the company compete with long-established car companies?arrow_forwardScenario 4 Sharon Gillespie, a new buyer at Visionex, Inc., was reviewing quotations for a tooling contract submitted by four suppliers. She was evaluating the quotes based on price, target quality levels, and delivery lead time promises. As she was working, her manager, Dave Cox, entered her office. He asked how everything was progressing and if she needed any help. She mentioned she was reviewing quotations from suppliers for a tooling contract. Dave asked who the interested suppliers were and if she had made a decision. Sharon indicated that one supplier, Apex, appeared to fit exactly the requirements Visionex had specified in the proposal. Dave told her to keep up the good work. Later that day Dave again visited Sharons office. He stated that he had done some research on the suppliers and felt that another supplier, Micron, appeared to have the best track record with Visionex. He pointed out that Sharons first choice was a new supplier to Visionex and there was some risk involved with that choice. Dave indicated that it would please him greatly if she selected Micron for the contract. The next day Sharon was having lunch with another buyer, Mark Smith. She mentioned the conversation with Dave and said she honestly felt that Apex was the best choice. When Mark asked Sharon who Dave preferred, she answered, Micron. At that point Mark rolled his eyes and shook his head. Sharon asked what the body language was all about. Mark replied, Look, I know youre new but you should know this. I heard last week that Daves brother-in-law is a new part owner of Micron. I was wondering how soon it would be before he started steering business to that company. He is not the straightest character. Sharon was shocked. After a few moments, she announced that her original choice was still the best selection. At that point Mark reminded Sharon that she was replacing a terminated buyer who did not go along with one of Daves previous preferred suppliers. What does the Institute of Supply Management code of ethics say about financial conflicts of interest?arrow_forward
- Scenario 4 Sharon Gillespie, a new buyer at Visionex, Inc., was reviewing quotations for a tooling contract submitted by four suppliers. She was evaluating the quotes based on price, target quality levels, and delivery lead time promises. As she was working, her manager, Dave Cox, entered her office. He asked how everything was progressing and if she needed any help. She mentioned she was reviewing quotations from suppliers for a tooling contract. Dave asked who the interested suppliers were and if she had made a decision. Sharon indicated that one supplier, Apex, appeared to fit exactly the requirements Visionex had specified in the proposal. Dave told her to keep up the good work. Later that day Dave again visited Sharons office. He stated that he had done some research on the suppliers and felt that another supplier, Micron, appeared to have the best track record with Visionex. He pointed out that Sharons first choice was a new supplier to Visionex and there was some risk involved with that choice. Dave indicated that it would please him greatly if she selected Micron for the contract. The next day Sharon was having lunch with another buyer, Mark Smith. She mentioned the conversation with Dave and said she honestly felt that Apex was the best choice. When Mark asked Sharon who Dave preferred, she answered, Micron. At that point Mark rolled his eyes and shook his head. Sharon asked what the body language was all about. Mark replied, Look, I know youre new but you should know this. I heard last week that Daves brother-in-law is a new part owner of Micron. I was wondering how soon it would be before he started steering business to that company. He is not the straightest character. Sharon was shocked. After a few moments, she announced that her original choice was still the best selection. At that point Mark reminded Sharon that she was replacing a terminated buyer who did not go along with one of Daves previous preferred suppliers. Ethical decisions that affect a buyers ethical perspective usually involve the organizational environment, cultural environment, personal environment, and industry environment. Analyze this scenario using these four variables.arrow_forwardScenario 4 Sharon Gillespie, a new buyer at Visionex, Inc., was reviewing quotations for a tooling contract submitted by four suppliers. She was evaluating the quotes based on price, target quality levels, and delivery lead time promises. As she was working, her manager, Dave Cox, entered her office. He asked how everything was progressing and if she needed any help. She mentioned she was reviewing quotations from suppliers for a tooling contract. Dave asked who the interested suppliers were and if she had made a decision. Sharon indicated that one supplier, Apex, appeared to fit exactly the requirements Visionex had specified in the proposal. Dave told her to keep up the good work. Later that day Dave again visited Sharons office. He stated that he had done some research on the suppliers and felt that another supplier, Micron, appeared to have the best track record with Visionex. He pointed out that Sharons first choice was a new supplier to Visionex and there was some risk involved with that choice. Dave indicated that it would please him greatly if she selected Micron for the contract. The next day Sharon was having lunch with another buyer, Mark Smith. She mentioned the conversation with Dave and said she honestly felt that Apex was the best choice. When Mark asked Sharon who Dave preferred, she answered, Micron. At that point Mark rolled his eyes and shook his head. Sharon asked what the body language was all about. Mark replied, Look, I know youre new but you should know this. I heard last week that Daves brother-in-law is a new part owner of Micron. I was wondering how soon it would be before he started steering business to that company. He is not the straightest character. Sharon was shocked. After a few moments, she announced that her original choice was still the best selection. At that point Mark reminded Sharon that she was replacing a terminated buyer who did not go along with one of Daves previous preferred suppliers. What should Sharon do in this situation?arrow_forwardWhat is the difference between goal, domain, and hybrid planning?arrow_forward
- The Global Sourcing Wire Harness Decision Sheila Austin, a buyer at Autolink, a Detroit-based producer of subassemblies for the automotive market, has sent out requests for quotations for a wiring harness to four prospective suppliers. Only two of the four suppliers indicated an interest in quoting the business: Original Wire (Auburn Hills, MI) and Happy Lucky Assemblies (HLA) of Guangdong Province, China. The estimated demand for the harnesses is 5,000 units a month. Both suppliers will incur some costs to retool for this particular harness. The harnesses will be prepackaged in 24 12 6-inch cartons. Each packaged unit weighs approximately 10 pounds. Quote 1 The first quote received is from Original Wire. Auburn Hills is about 20 miles from Autolinks corporate headquarters, so the quote was delivered in person. When Sheila went down to the lobby, she was greeted by the sales agent and an engineering representative. After the quote was handed over, the sales agent noted that engineering would be happy to work closely with Autolink in developing the unit and would also be interested in future business that might involve finding ways to reduce costs. The sales agent also noted that they were hungry for business, as they were losing a lot of customers to companies from China. The quote included unit price, tooling, and packaging. The quoted unit price does not include shipping costs. Original Wire requires no special warehousing of inventory, and daily deliveries from its manufacturing site directly to Autolinks assembly operations are possible. Original Wire Quote: Unit price = 30 Packing costs = 0.75 per unit Tooling = 6,000 one-time fixed charge Freight cost = 5.20 per hundred pounds Quote 2 The second quote received is from Happy Lucky Assemblies of Guangdong Province, China. The supplier must pack the harnesses in a container and ship via inland transportation to the port of Shanghai in China, have the shipment transferred to a container ship, ship material to Seattle, and then have material transported inland to Detroit. The quoted unit price does not include international shipping costs, which the buyer will assume. HLA Quote: Unit price = 19.50 Shipping lead time = Eight weeks Tooling = 3,000 In addition to the suppliers quote, Sheila must consider additional costs and information before preparing a comparison of the Chinese suppliers quotation: Each monthly shipment requires three 40-foot containers. Packing costs for containerization = 2 per unit. Cost of inland transportation to port of export = 200 per container. Freight forwarders fee = 100 per shipment (letter of credit, documentation, etc.). Cost of ocean transport = 4,000 per container. This has risen significantly in recent years due to a shortage of ocean freight capacity. Marine insurance = 0.50 per 100 of shipment. U.S. port handling charges = 1,200 per container. This fee has also risen considerably this year, due to increased security. Ports have also been complaining that the charges may increase in the future. Customs duty = 5% of unit cost. Customs broker fees per shipment = 300. Transportation from Seattle to Detroit = 18.60 per hundred pounds. Need to warehouse at least four weeks of inventory in Detroit at a warehousing cost of 1.00 per cubic foot per month, to compensate for lead time uncertainty. Sheila must also figure the costs associated with committing corporate capital for holding inventory. She has spoken to some accountants, who typically use a corporate cost of capital rate of 15%. Cost of hedging currencybroker fees = 400 per shipment Additional administrative time due to international shipping = 4 hours per shipment 25 per hour (estimated) At least two five-day visits per year to travel to China to meet with supplier and provide updates on performance and shipping = 20,000 per year (estimated) The international sourcing costs must be absorbed by Sheila, as the supplier does not assume any of the additional estimated costs and invoice Sheila later, or build the costs into a revised unit price. Sheila feels that the U.S. supplier is probably less expensive, even though it quoted a higher price. Sheila also knows that this is a standard technology that is unlikely to change during the next three years, but which could be a contract that extends multiple years out. There is also a lot of hall talk amongst the engineers on her floor about next-generation automotive electronics, which will completely eliminate the need for wire harnesses, which will be replaced by electronic components that are smaller, lighter, and more reliable. She is unsure about how to calculate the total costs for each option, and she is even more unsure about how to factor these other variables into the decision. Calculate the total cost per unit of purchasing from Original Wire.arrow_forwardThe Global Sourcing Wire Harness Decision Sheila Austin, a buyer at Autolink, a Detroit-based producer of subassemblies for the automotive market, has sent out requests for quotations for a wiring harness to four prospective suppliers. Only two of the four suppliers indicated an interest in quoting the business: Original Wire (Auburn Hills, MI) and Happy Lucky Assemblies (HLA) of Guangdong Province, China. The estimated demand for the harnesses is 5,000 units a month. Both suppliers will incur some costs to retool for this particular harness. The harnesses will be prepackaged in 24 12 6-inch cartons. Each packaged unit weighs approximately 10 pounds. Quote 1 The first quote received is from Original Wire. Auburn Hills is about 20 miles from Autolinks corporate headquarters, so the quote was delivered in person. When Sheila went down to the lobby, she was greeted by the sales agent and an engineering representative. After the quote was handed over, the sales agent noted that engineering would be happy to work closely with Autolink in developing the unit and would also be interested in future business that might involve finding ways to reduce costs. The sales agent also noted that they were hungry for business, as they were losing a lot of customers to companies from China. The quote included unit price, tooling, and packaging. The quoted unit price does not include shipping costs. Original Wire requires no special warehousing of inventory, and daily deliveries from its manufacturing site directly to Autolinks assembly operations are possible. Original Wire Quote: Unit price = 30 Packing costs = 0.75 per unit Tooling = 6,000 one-time fixed charge Freight cost = 5.20 per hundred pounds Quote 2 The second quote received is from Happy Lucky Assemblies of Guangdong Province, China. The supplier must pack the harnesses in a container and ship via inland transportation to the port of Shanghai in China, have the shipment transferred to a container ship, ship material to Seattle, and then have material transported inland to Detroit. The quoted unit price does not include international shipping costs, which the buyer will assume. HLA Quote: Unit price = 19.50 Shipping lead time = Eight weeks Tooling = 3,000 In addition to the suppliers quote, Sheila must consider additional costs and information before preparing a comparison of the Chinese suppliers quotation: Each monthly shipment requires three 40-foot containers. Packing costs for containerization = 2 per unit. Cost of inland transportation to port of export = 200 per container. Freight forwarders fee = 100 per shipment (letter of credit, documentation, etc.). Cost of ocean transport = 4,000 per container. This has risen significantly in recent years due to a shortage of ocean freight capacity. Marine insurance = 0.50 per 100 of shipment. U.S. port handling charges = 1,200 per container. This fee has also risen considerably this year, due to increased security. Ports have also been complaining that the charges may increase in the future. Customs duty = 5% of unit cost. Customs broker fees per shipment = 300. Transportation from Seattle to Detroit = 18.60 per hundred pounds. Need to warehouse at least four weeks of inventory in Detroit at a warehousing cost of 1.00 per cubic foot per month, to compensate for lead time uncertainty. Sheila must also figure the costs associated with committing corporate capital for holding inventory. She has spoken to some accountants, who typically use a corporate cost of capital rate of 15%. Cost of hedging currencybroker fees = 400 per shipment Additional administrative time due to international shipping = 4 hours per shipment 25 per hour (estimated) At least two five-day visits per year to travel to China to meet with supplier and provide updates on performance and shipping = 20,000 per year (estimated) The international sourcing costs must be absorbed by Sheila, as the supplier does not assume any of the additional estimated costs and invoice Sheila later, or build the costs into a revised unit price. Sheila feels that the U.S. supplier is probably less expensive, even though it quoted a higher price. Sheila also knows that this is a standard technology that is unlikely to change during the next three years, but which could be a contract that extends multiple years out. There is also a lot of hall talk amongst the engineers on her floor about next-generation automotive electronics, which will completely eliminate the need for wire harnesses, which will be replaced by electronic components that are smaller, lighter, and more reliable. She is unsure about how to calculate the total costs for each option, and she is even more unsure about how to factor these other variables into the decision. Calculate the total cost per unit of purchasing from Happy Lucky Assemblies.arrow_forwardThe Global Sourcing Wire Harness Decision Sheila Austin, a buyer at Autolink, a Detroit-based producer of subassemblies for the automotive market, has sent out requests for quotations for a wiring harness to four prospective suppliers. Only two of the four suppliers indicated an interest in quoting the business: Original Wire (Auburn Hills, MI) and Happy Lucky Assemblies (HLA) of Guangdong Province, China. The estimated demand for the harnesses is 5,000 units a month. Both suppliers will incur some costs to retool for this particular harness. The harnesses will be prepackaged in 24 12 6-inch cartons. Each packaged unit weighs approximately 10 pounds. Quote 1 The first quote received is from Original Wire. Auburn Hills is about 20 miles from Autolinks corporate headquarters, so the quote was delivered in person. When Sheila went down to the lobby, she was greeted by the sales agent and an engineering representative. After the quote was handed over, the sales agent noted that engineering would be happy to work closely with Autolink in developing the unit and would also be interested in future business that might involve finding ways to reduce costs. The sales agent also noted that they were hungry for business, as they were losing a lot of customers to companies from China. The quote included unit price, tooling, and packaging. The quoted unit price does not include shipping costs. Original Wire requires no special warehousing of inventory, and daily deliveries from its manufacturing site directly to Autolinks assembly operations are possible. Original Wire Quote: Unit price = 30 Packing costs = 0.75 per unit Tooling = 6,000 one-time fixed charge Freight cost = 5.20 per hundred pounds Quote 2 The second quote received is from Happy Lucky Assemblies of Guangdong Province, China. The supplier must pack the harnesses in a container and ship via inland transportation to the port of Shanghai in China, have the shipment transferred to a container ship, ship material to Seattle, and then have material transported inland to Detroit. The quoted unit price does not include international shipping costs, which the buyer will assume. HLA Quote: Unit price = 19.50 Shipping lead time = Eight weeks Tooling = 3,000 In addition to the suppliers quote, Sheila must consider additional costs and information before preparing a comparison of the Chinese suppliers quotation: Each monthly shipment requires three 40-foot containers. Packing costs for containerization = 2 per unit. Cost of inland transportation to port of export = 200 per container. Freight forwarders fee = 100 per shipment (letter of credit, documentation, etc.). Cost of ocean transport = 4,000 per container. This has risen significantly in recent years due to a shortage of ocean freight capacity. Marine insurance = 0.50 per 100 of shipment. U.S. port handling charges = 1,200 per container. This fee has also risen considerably this year, due to increased security. Ports have also been complaining that the charges may increase in the future. Customs duty = 5% of unit cost. Customs broker fees per shipment = 300. Transportation from Seattle to Detroit = 18.60 per hundred pounds. Need to warehouse at least four weeks of inventory in Detroit at a warehousing cost of 1.00 per cubic foot per month, to compensate for lead time uncertainty. Sheila must also figure the costs associated with committing corporate capital for holding inventory. She has spoken to some accountants, who typically use a corporate cost of capital rate of 15%. Cost of hedging currencybroker fees = 400 per shipment Additional administrative time due to international shipping = 4 hours per shipment 25 per hour (estimated) At least two five-day visits per year to travel to China to meet with supplier and provide updates on performance and shipping = 20,000 per year (estimated) The international sourcing costs must be absorbed by Sheila, as the supplier does not assume any of the additional estimated costs and invoice Sheila later, or build the costs into a revised unit price. Sheila feels that the U.S. supplier is probably less expensive, even though it quoted a higher price. Sheila also knows that this is a standard technology that is unlikely to change during the next three years, but which could be a contract that extends multiple years out. There is also a lot of hall talk amongst the engineers on her floor about next-generation automotive electronics, which will completely eliminate the need for wire harnesses, which will be replaced by electronic components that are smaller, lighter, and more reliable. She is unsure about how to calculate the total costs for each option, and she is even more unsure about how to factor these other variables into the decision. Are there any other issues besides cost that Sheila should evaluate?arrow_forward
arrow_back_ios
SEE MORE QUESTIONS
arrow_forward_ios
Recommended textbooks for you
- Purchasing and Supply Chain ManagementOperations ManagementISBN:9781285869681Author:Robert M. Monczka, Robert B. Handfield, Larry C. Giunipero, James L. PattersonPublisher:Cengage LearningMarketingMarketingISBN:9780357033791Author:Pride, William MPublisher:South Western Educational Publishing
- Contemporary MarketingMarketingISBN:9780357033777Author:Louis E. Boone, David L. KurtzPublisher:Cengage Learning
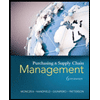
Purchasing and Supply Chain Management
Operations Management
ISBN:9781285869681
Author:Robert M. Monczka, Robert B. Handfield, Larry C. Giunipero, James L. Patterson
Publisher:Cengage Learning
Marketing
Marketing
ISBN:9780357033791
Author:Pride, William M
Publisher:South Western Educational Publishing
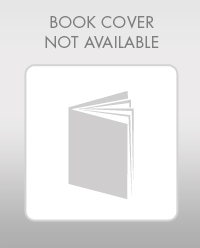
Contemporary Marketing
Marketing
ISBN:9780357033777
Author:Louis E. Boone, David L. Kurtz
Publisher:Cengage Learning