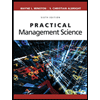
Formulate the LP model for each of the problem identified below. Clearly define the decision variables and the objective function
The Burroughs Garment Company manufactures men’s shirts and women’s blouses for Walmark Discount Stores. Walmark will accept all the products supplied by Burroughs. The production process includes cutting, sewing, and packaging. Burroughs employs 25 workers in the cutting department, 35 in the sewing department, and 5 in the packaging department. The factory works one 8-hr shift, 5 days a week. Determine the optimal weekly production

Trending nowThis is a popular solution!
Step by stepSolved in 2 steps with 4 images

- I need typing clear urjent no chatgpt use i will give 5 upvotesarrow_forwardAn operations manager is deciding on the level of automation for a new process. The fixed cost for automation includes the equipment purchase price, installation, and initial spare parts. The variable costs per unit for each level of automation are primarily labor related. Each unit can be sold for $84. As in many cases, you have the default alternative of doing nothing ($0 fixed cost, $0 variable costs). What is the break-even point for option C? DO NOT INCLUDE A COMMA. Round your answer to the nearest whole number and do not include units or a comma. For example, submit 12450 and NOT 12,450. Alternative Fixed Costs A B C $100,000 $282,000 $560,000 Variable Costs per Unit $54 $37 $20 Round your answer to the nearest whole number and do not include units.arrow_forwardHickory Manufacturing Company forecasts the following demand for a product (in thousands of units) over the next five years. Year 1 2 3 4 5 Forecast demand 62 84 86 90 90 Currently the manufacturer has seven machines that operate on a two-shift (eight hours each) basis. Thirty days per year are available for scheduled maintenance of equipment with no process output. Assume there are 250 workdays in a year. Each manufactured good takes 20 minutes to produce. What is the effective capacity of the factory? Round your answer down to the nearest whole number. units/year Given the five-year forecast, how much extra capacity is needed each year? Use a minus sign to enter an answer, if there is excess capacity. Round your answers to the nearest whole number. Year 1 2 3 4 5 Extra capacity needed (units) Does the firm need to buy more machines? If so, how many? When? If your answer is zero, enter "0". Round your answers up to the nearest whole number.…arrow_forward
- Deforrest Marine Motors manufactures engines for the speedboat racing circuit. As part of their annual planning cycle, they forecasted demand for the next four quarters. The number of available days of production and the anticipated demand are given below. Employees Production Rate Production Cost Backorder Cost Overtime Cost Overtime Limit Demand Q1 2,400 6,019,000 They also estimated many of the costs required to conduct operations planning. Some of these key figures are listed below. 30 70 units/employee/quarter Q2 2,200 $1,000/unit $200/unit/quarter $1,500/unit <= 25% of Reg. Production Q3 1,700 Q4 1,800 Hire Cost Fire Cost Subcontracting Cost Subcontracting Limit Inventory Cost Initial Inventory $1,200/employee $800/employee $1,800/unit 400 units maximum $100/unit/quarter 280 units Deforrest Marine Motors wishes to maintain the current number of employees for the entire year to follow a level strategy balanced with inventory and backorders as needed. What is the total cost of this…arrow_forwardUse the following for the next 2 questions: A company forecasts that it will ship 120,000 boxes of product in June. The product has a monthly turnover of 3. The company plans to use its facility to ship 80,000 boxes and the balance of the 40,000 boxes will ship from a rented facility. Space may be rented for a charge of $7 per box per month with an in-and-out handling charge of $0.45 per box shipped. 1. What is the rented (fixed) storage cost for June? - $280,000 - $180,000 - $42,500 - $250,000 - $93,333 - $153,333 - $173,333 2. What is the rented variable cost for June? - $33,333 - $43,333 - $6,000 - $38,000 - $18,000 - $28,000 - $23,333arrow_forwardThe company Customer First A-to-Z uses a make to stock strategy. Product A is thecompany’s main product. The forecast for Product A, the accepted customer ordersand the master production schedule is shown below. The company presently has150 units on hand and a fixed master production schedule quantity of 80 units isused. Product A Forecast Customer Orders MPS Week Quantity Week Quantity Week Quantity 1 60 1 45 1 2 60 2 66 2 80 3 60 3 55 3 4 60 4 65 4 5 60 5 40 5 6 60 6 22 6 7 60 7 10 7 8 60 8 5 8 9 60 9 4 9 10 60 10 2 10 Required:A. Help the master production scheduler to fill in the master schedule calculationtable shown below, by using the forecast, the customer orders and the plannedproduction of product A. 1 2 3 4 5 6 7 8 9 10 Ft Dt EIt-1 Pt EIt ATPt B. The marketing department has accepted an…arrow_forward
- A Company currently has 230 units of a product on-hand that it orders every three weeks when the salesperson visits the premises. Average demand for the product is 20 units per day with a standard deviation of 5 units. Lead time for the product to arrive is seven days. Management has a goal of 95 percent probability of not stocking out for this product. The salesperson is due to come in late this afternoon when 210 units are left in stock. How many units should be ordered?arrow_forwardAn operations manager is deciding on the level of automation for a new process. The fixed cost for automation includes the equipment purchase price, installation, and initial spare parts. The variable costs per unit for each level of automation are primarily labor related. Each unit can be sold for $86. As in many cases, you have the default alternative of doing nothing ($0 fixed cost, $0 variable costs). When comparing Alternative A to Alternative B, B is more attractive than A above DO NOT INCLUDE A COMMA. Round your answer to the nearest whole number and do not include units or a comma. For example, submit 12450 and NOT 12,450. Alternative Fixed Costs A B с units. $100,000 $284,000 $560,000 Variable Costs per Unit $54 $44 $20 Hint: For these questions, also consider the "Do Nothing" option as a viable option when making your decision.arrow_forward
- Practical Management ScienceOperations ManagementISBN:9781337406659Author:WINSTON, Wayne L.Publisher:Cengage,Operations ManagementOperations ManagementISBN:9781259667473Author:William J StevensonPublisher:McGraw-Hill EducationOperations and Supply Chain Management (Mcgraw-hi...Operations ManagementISBN:9781259666100Author:F. Robert Jacobs, Richard B ChasePublisher:McGraw-Hill Education
- Purchasing and Supply Chain ManagementOperations ManagementISBN:9781285869681Author:Robert M. Monczka, Robert B. Handfield, Larry C. Giunipero, James L. PattersonPublisher:Cengage LearningProduction and Operations Analysis, Seventh Editi...Operations ManagementISBN:9781478623069Author:Steven Nahmias, Tava Lennon OlsenPublisher:Waveland Press, Inc.
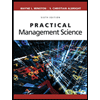
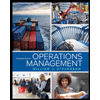
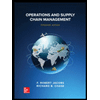
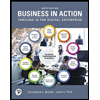
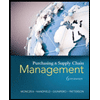
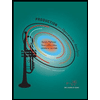