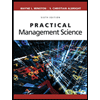
Concept explainers
Johnson Peters holds the position of operations manager for a small container and bottle manufacturing company. His job description includes managing inventory levels, supervision of operation, leading his team etc. Annually there is usually a quick turn over of inventory items. One of the main items (bottle caps) have a demand of 8,000 units per day. The actual cost of each unit is $150, and the inventory holding cost per years is 15% of the unit price. The average setup cost is $17.85. There are 300 working days per year, and it takes an order about 5 days to arrive by boat.
D.What is the optimal number of days in between any two orders?
E.What is the annual cost of ordering?
F.What is the annual cost of holding inventory?
PLEASE DO NOT WRITE RESPONSES IT IS HARD TO UNDERSTAND

Trending nowThis is a popular solution!
Step by stepSolved in 5 steps

- A company orders 100 units of a raw material every time its inventory level drops to 50 units. The lead time for the delivery of the raw material is 5 days. Currently, the inventory level is at 80 units. Assuming constant demand, calculate the reorder point for the raw material.arrow_forwardSubject: Logistic management The following information is given to you D = 19,000 units/yr; H = $4/unit/year; S=$25/order. Calculate the EOQ, Annual holding cost and annual ordering cost.arrow_forwardFirst Printing has contracts with legal firms in San Francisco to copy their court documents. Daily demand is almost constant at 11,100 pages of documents. The lead time for paper delivery is normally distributed with a mean of 1 day and a standard deviation of 1 day. A 95% service level is expected. Compute First's ROP. Refer to the standard normal table for z-values. The reorder point is documents (round your response to the nearest whole number). Z-Table Z 0.38 0.50 0.67 0.84 1.04 1.28 1.41 1.56 1.65 1.75 1.88 2.06 2.33 Print Pr(Z) 65 69 75 80 85 90 92 94 95 96 97 98 99 Done - Xarrow_forward
- The fixed quantity version of EOQ compares and contrasts with the fixed interval version. Where will each of the scenarios be used?arrow_forwardThe daily demand for printer paper at the School of Business is approximately normal with a mean of 15.2 boxes and a standard deviation of 1.6 per day. The Administrative Assistant reviews the inventory every 30 days, and the lead time is 5 days. The division set a policy of satisfying 96% of the demand for paper. If there are 125 boxes of printer paper in inventory at the beginning of this review period, how many boxes of printer paper should be ordered? What is the variance of demand during the review period plus the lead-time period? What is the standard deviation of demand during the review period plus the lead-time period? A. Variance = 76.80 Standard deviation = 8.76 B. Variance = 89.60 Standard deviation = 9.47 C. Variance = 9.47 Standard deviation = 89.60 D. Variance = 12.8 Standard deviation = 3.58arrow_forward
- Practical Management ScienceOperations ManagementISBN:9781337406659Author:WINSTON, Wayne L.Publisher:Cengage,Operations ManagementOperations ManagementISBN:9781259667473Author:William J StevensonPublisher:McGraw-Hill EducationOperations and Supply Chain Management (Mcgraw-hi...Operations ManagementISBN:9781259666100Author:F. Robert Jacobs, Richard B ChasePublisher:McGraw-Hill Education
- Purchasing and Supply Chain ManagementOperations ManagementISBN:9781285869681Author:Robert M. Monczka, Robert B. Handfield, Larry C. Giunipero, James L. PattersonPublisher:Cengage LearningProduction and Operations Analysis, Seventh Editi...Operations ManagementISBN:9781478623069Author:Steven Nahmias, Tava Lennon OlsenPublisher:Waveland Press, Inc.
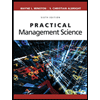
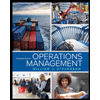
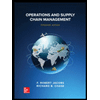
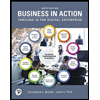
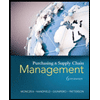
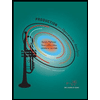