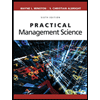
Practical Management Science
6th Edition
ISBN: 9781337406659
Author: WINSTON, Wayne L.
Publisher: Cengage,
expand_more
expand_more
format_list_bulleted
Question
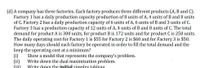
Transcribed Image Text:(d) A company has three factories. Each factory produces three different products (A, B and C).
Factory 1 has a daily production capacity production of 8 units of A, 4 units of B and 8 units
of C. Factory 2 has a daily production capacity of 6 units of A, 6 units of B and 3 units of C.
Factory 3 has a production capacity of 12 units of A, 4 units of B and 8 units of C. The total
demand for product A is 300 units, for product B is 172 units and for product C is 250 units.
The daily operating cost for Factory 1 is $55 for Factory 2 is $60 and for Factory 3
How many days should each factory be operated in order to fill the total demand and the
keep the operating cost at a minimum?
(i)
(ii)
(iii)
$50.
Show a model that represents the company's problem.
Write down the dual maximization problem.
Write down the initial simplex tableau.
Expert Solution

This question has been solved!
Explore an expertly crafted, step-by-step solution for a thorough understanding of key concepts.
This is a popular solution
Trending nowThis is a popular solution!
Step by stepSolved in 3 steps

Knowledge Booster
Similar questions
- paresharrow_forward13. The Bi-Product Company produces two products (A and B) that are similar in terms of labor con- tent and skills required. Company management wishes to "level" the number of employees needed each day so no hiring or layoffs will be required during the year. A complication to this problem is that the number of working days in each quarter varies. Demand Quarter Product A Product B Working Days 1 9,800 14,500 68 2 12,000 30,000 56 3 14,000 19,500 62 4 31,000 25,000 58 Beginning inventory: 2,400 units of Product A 900 units of Product B Inventory holding cost: $10 per unit per quarter (either product) No back orders allowed No variations in size of workforce allowed Output rate=25 units of either product per day per employee a. What daily production rate will be required to meet the demand forecast and yield zero in- ventory at the end of quarter 4? b. How many employees will be required each day? What are the inventory levels each quarter?arrow_forwardA company has the following demand data for the last three years of sales for their popular product B. There are currently 5 workers assigned to the production line, each capable of producing approximately 8 units per month. It is assumed that each month has the same number of production days. They can hire more workers at a hiring and training cost of $800 per worker. If they layoff any workers, the unemployment cost is $2,000 per worker. The product has a standard production cost (labor, material, and overhead) of $300 per unit. The extra cost to produce one unit on overtime is $50 and the maximum overtime is two units per month per worker. They can use inventory but it will cost them $25 per unit per month for any unit in inventory at the end of the month. Failure to meet market demand typically will imply the customer will buy from another supplier, and therefore cost the company $100 in profit. They currently have 0 units in inventory. a. Use the demand data to develop a forecast…arrow_forward
- A local semiconductor firm, Superchip, is planning its workforce and productionlevels over the next year. The firm makes a variety of microprocessors and usessales dollars as its aggregate production measure. Based on orders received and sales forecasts provided by the marketing department, the estimate of dollarsales for the next year by month is as follows:Production Predicted DemandMonth Days (in $10,000)January 22 340February 16 380March 21 220April 19 100May 23 490June 20 625July 24 375August 12 310September 19 175October 22 145November 20 120December 16 165Inventory holding costs are based on a 25 percent annual interest charge. It is anticipatedthat there will be 675 workers on the payroll at the end of the current year and inventorieswill amount to $120,000. The firm would like to have at least $100,000 of inventory at theend of December next year. It is estimated that each worker accounts for an average of$60,000 of production per year (assume that one year consists of 250…arrow_forwardValencia Products makes automobile radar detectors and assembles two models: LaserStop and SpeedBuster. The firm can sell all it produces. Both models use the same electronic components. Two of these can be obtained only from a single supplier. For the next month, the supply of these is limited to 4,000 of component A and 3,500 of component B. The number of each component required for each product and the profit per unit are in the table below. This question is interested in maximizing the profit). a) Identify the decision variables, objective function, and constraints in simple verbal statements. b) Mathematically formulate a linear optimization model. Components Required/Unit A B Profit/Unit LaserStop 18 6 $124 SpeedBuster 12 8 $136 Solve this question in Excel by using SOLVER. Please clearly explain what is the optimal solution? What is the resulting output of the objective function at the optimal solution? P.S. please solve in Excel.arrow_forwardA shop is planning an order for a popular Christmas festive season product. Demand for the product usually starts from first week of December till first week of January and reduces sharply thereafter. For this reason, and to stimulate sales for leftovers, the product is sold at a significantly reduced price from the second week of January to the fourth week of January. Any leftover after the fourth week of January goes waste. The table below gives past data on total demand for the period from first week of December to first week of January, and from second week of January to fourth week of January, together with their respective chances of occurrence. The product can be purchased at a wholesale price of GHS60 per unit for a pack containing 600 products, GHS57 per unit for a pack containing 800 products, and GHS52 per unit for a pack containing 1000 products. The shop plans to sell the product for GHS80 per unit from first week of December to first week of January, and at a reduced…arrow_forward
- 1. A major supermarket chain has decided to sub-contract production of ready-to-eat sandwiches to your production plant. Your plant can make three kinds of sand- wiches, each of which take the following amounts of raw ingredients (measured in grams) to produce: Sandwich | Chicken Cheese Lettuce Tomato Bread 45 15 25 10 13 Chicken Salad Chicken Club Cheese and salad 920 0 20 30 Chicken Salad Chicken Club Cheese and Salad 15 10 20 The total amount of time (measured in minutes) to make one of each sandwich is listed below, together with the price that the supermarket will pay to purchase one of each: Sandwich | Time to Make Price 2.8 4.8 1.3 60 90 60 £1.25 £1.65 £0.95 For the sake of this problem you can treat ingredients used and number of sandwiches made as continuous quantities we could perhaps think of this as the average made per day over a longer period, in which case making 100.43 sandwiches per day would still make sense. (a) Suppose that you have 5000g of chicken, 2500g of…arrow_forward"A chipboard company has 4 factories, Mazatenango, Retalhuleu, Escuintla and Xela. It has four major distributors of its chipboards, which are distributor 1, distributor 2, distributor 3 and distributor 4: Mazatenango Retalhuleu Escuintla Xela DEMAND D1 10 16 19 12 350 D2 12 10 18 15 300 D3 15 22 10 10 250 D4 20 10 12 20 200 SUPPLY 150 150 350 250 1) Formulate the problem as a transportation problem, solve it with the three methods and find the optimal cost for this problem. methods and find the optimal cost for this transportation problem. (remember to go through all possible routes). IN THIS CASE USE MINIMUM TRANSPORTATION COST - LEAST COST METHODarrow_forwardA plant manager of a chemical plant must determine the lot size for a particular chemical that has a steadydemand of 30 barrels per day. The production rate is 190 barrels per day, annual demand is 10,500 barrels,setup cost is $200, annual holding cost is $0.21 per barrel, and the plant operates 350 days per year.a. Determine the economic production lot size (ELS).b. Determine the total annual setup and inventory holding cost for this item.c. Determine the time between orders (TBO), or cycle length, for the ELS.d. Determine the production time per lot.What are the advantages of reducing the setup time by 10 percent?arrow_forward
- Develop a lot-for-lot solution and calculate total relevant costs for the gross requirements in the following table*. Period Gross requirements Develop a lot-for-lot solution (enter your responses as whole numbers). Period Gross requirements On-hand at beginning of period On-hand at end of period 1 Order receipt Order release 30 2 3 30 1 30 40 || 4 5 2 6 7 40 70 20 *Holding cost = $3.50/unit/week; setup cost = $150; lead time = 1 week; beginning inventory = 40. 3 4 30 8 9 10 11 12 5 6 7 40 70 20 20 80 8 60 9 10 20 80 11 12 60arrow_forwardQ: The Morton Supply Company produces clothing, footwear, and accessories for dancing and gymnastics. They produce three models of pointe shoes used by ballerinas to balance on the tips of their toes. The shoes are produced from four materials: cardstock, satin, plain fabric, and leather. The number of square inches of each type of material used in each model of shoe, the amount of material available, and the profit/model are shown below: Material (measured in square inches) Model 1 Model 2 Model 3 Material Available Cardstock 12 10 14 1200 Satin 24 20 15 2000 Plain fabric 40 40 30 7500 Leather 11 11 10 1000 Profit per model $50 $44 $40 a) Generate the Sensitivity Report in EXCEL for the model that you built. Interpret, in context, the Shadow Price for the Leather and the Satin constraints. Include units in your interpretations.arrow_forwardsniparrow_forward
arrow_back_ios
SEE MORE QUESTIONS
arrow_forward_ios
Recommended textbooks for you
- Practical Management ScienceOperations ManagementISBN:9781337406659Author:WINSTON, Wayne L.Publisher:Cengage,Operations ManagementOperations ManagementISBN:9781259667473Author:William J StevensonPublisher:McGraw-Hill EducationOperations and Supply Chain Management (Mcgraw-hi...Operations ManagementISBN:9781259666100Author:F. Robert Jacobs, Richard B ChasePublisher:McGraw-Hill Education
- Purchasing and Supply Chain ManagementOperations ManagementISBN:9781285869681Author:Robert M. Monczka, Robert B. Handfield, Larry C. Giunipero, James L. PattersonPublisher:Cengage LearningProduction and Operations Analysis, Seventh Editi...Operations ManagementISBN:9781478623069Author:Steven Nahmias, Tava Lennon OlsenPublisher:Waveland Press, Inc.
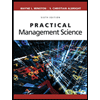
Practical Management Science
Operations Management
ISBN:9781337406659
Author:WINSTON, Wayne L.
Publisher:Cengage,
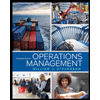
Operations Management
Operations Management
ISBN:9781259667473
Author:William J Stevenson
Publisher:McGraw-Hill Education
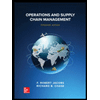
Operations and Supply Chain Management (Mcgraw-hi...
Operations Management
ISBN:9781259666100
Author:F. Robert Jacobs, Richard B Chase
Publisher:McGraw-Hill Education
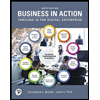
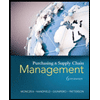
Purchasing and Supply Chain Management
Operations Management
ISBN:9781285869681
Author:Robert M. Monczka, Robert B. Handfield, Larry C. Giunipero, James L. Patterson
Publisher:Cengage Learning
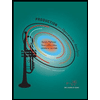
Production and Operations Analysis, Seventh Editi...
Operations Management
ISBN:9781478623069
Author:Steven Nahmias, Tava Lennon Olsen
Publisher:Waveland Press, Inc.