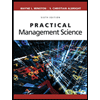
Practical Management Science
6th Edition
ISBN: 9781337406659
Author: WINSTON, Wayne L.
Publisher: Cengage,
expand_more
expand_more
format_list_bulleted
Concept explainers
Topic Video
Question
CYCLE COUNTING AT COLE’S TRUCKS, INC.
Cole’s Trucks, Inc., a builder of high-quality refuse trucks, has about 5,000 items in its inventory. It
wants to determine how many items to cycle count each day.
APPROACH c After hiring Matt Clark, a bright young OM student, for the summer, the firm deter-
mined that it has 500 A items, 1,750 B items, and 2,750 C items. Company policy is to count all A items
every month (every 20 working days), all B items every quarter (every 60 working days), and all C items
every 6 months (every 120 working days). The firm then allocates some items to be counted each day.
Expert Solution

This question has been solved!
Explore an expertly crafted, step-by-step solution for a thorough understanding of key concepts.
This is a popular solution
Trending nowThis is a popular solution!
Step by stepSolved in 2 steps with 1 images

Knowledge Booster
Learn more about
Need a deep-dive on the concept behind this application? Look no further. Learn more about this topic, operations-management and related others by exploring similar questions and additional content below.Similar questions
- Master Company has obtained the following costs and other information pertaining to one of its materials: Working days per year Normal use per day (units) Maximum use per day (units) 250 Lead time ( in days) 500 Cost of placing one order Р36 600 Carrying cost per unit per year P4 Required: a. Calculate the economic order quantity b. Determinethe safety stock c. Compute the order pointarrow_forwardAssume you are the manager of a shop that assembles power tools. You have just received an order for 55 chain saws, which are to be shipped at the start of week 8. Pertinent information on the saws follows: Item Lead Time (weeks) On Hand Saw A B C D E F 2 1 2 2 1 1 2 Gross requirements Scheduled receipts Projected on hand Net requirements Planned order receipt Planned order release Ĉ E(3) & E(2) LT = 1 week Lot size: Lot-for-Lot 15 10 5 65 20 10 30 Skip Extension Tip: Double click to open in new tab Show Transcribed Text Develop the material requirements plan for component E using lot-for-lot ordering for all items. (Leave no cells blank - be certain to enter "0" wherever required.) Components A(2), B(1), C(4) E(3), D(1) D (2), F(3) E(2), D (2) Beg. Inv. 1 2 3 190 5 210 6arrow_forwardWhich of the following is not an acceptable method of applying the LCNRV? Select one: a. Group inventory items b. Individual item c. Total of the inventory d. Inventory locationarrow_forward
- hello please answer number 2 only thank youarrow_forwardPlease do not give solution in image format thanku What are order cycle costs if annual demand is 8,000 units, with the following order quantities and annual order cost is $97? a. Order quantity of 1,000 = b. Order quantity of 500 = C. Order qty of 8,000 =arrow_forwarda) The average monthly demand requirement = ____units (round to nearest whole number.) B) The total stockout cost = $____(nearest whole number) C) The total inventory carrying cost = $____(nearest whole number) D) The total cost, excluding normal time labor costs, is = $_____(nearest whole number)arrow_forward
- Find MPS start as wellarrow_forwardRick Jerz is attempting to perform an inventory analysis on one of his most popular products. Annual demand for this product is 5,000 units; carrying cost is $50 per unit per year; order costs for his company typically run nearly $30 per order; and lead time averages 10 days. (Assume 250 working days per year.) a) The economic order quantity is 77 units (round your response to the nearest whole number). b) The average inventory is units (round your response to the nearest whole number). c) The optimal number of orders per year is orders (round your response to the nearest whole number). d) The optimal number of working days between orders is days (round your response to two decimal places). e) The total annual inventory cost (carrying cost + ordering cost) is $ (round your response to two decimal places). f) The reorder point is units (enter your response as a whole number).arrow_forwardBhatti Company produces plastic photo frames. Two departments, molding and finishing, are involved in the manufacturing. The molding department fills the molds with hot liquid plastic that is left to cool and then opens them. The finishing department removes the plastic frame from the mold and strips the edges of the frames of extra plastic. The following information is available for the month of January: January 1 Quantity (pounds) January 31 Quantity (pounds) Work-in-Process Inventory Cost Cost Molding department Finishing department None None 5,000 $ 15,000 2,000 The WIP Inventory in the finishing department is estimated to be 40% complete for conversion both at the beginning and end of January. Costs of production for January follow: Direct Costs of Production Materials Conversion Molding department Finishing department $ 450,000 $ 90,000 80,290 The molding department started 50,000 pounds of product in January. The firm uses the FIFO method of process costing. Required: 1. Prepare…arrow_forward
- A what is the inventory turnover for the hamburger patties? B. On average, how many days of supply are on hand?arrow_forwardExplore the role and implications of safety stock within the framework of the Wilson approach for effective inventory control.arrow_forwardExplain Planning and Replenishment concepts related to Independent demand inventory?arrow_forward
arrow_back_ios
arrow_forward_ios
Recommended textbooks for you
- Practical Management ScienceOperations ManagementISBN:9781337406659Author:WINSTON, Wayne L.Publisher:Cengage,Operations ManagementOperations ManagementISBN:9781259667473Author:William J StevensonPublisher:McGraw-Hill EducationOperations and Supply Chain Management (Mcgraw-hi...Operations ManagementISBN:9781259666100Author:F. Robert Jacobs, Richard B ChasePublisher:McGraw-Hill Education
- Purchasing and Supply Chain ManagementOperations ManagementISBN:9781285869681Author:Robert M. Monczka, Robert B. Handfield, Larry C. Giunipero, James L. PattersonPublisher:Cengage LearningProduction and Operations Analysis, Seventh Editi...Operations ManagementISBN:9781478623069Author:Steven Nahmias, Tava Lennon OlsenPublisher:Waveland Press, Inc.
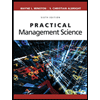
Practical Management Science
Operations Management
ISBN:9781337406659
Author:WINSTON, Wayne L.
Publisher:Cengage,
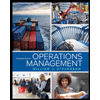
Operations Management
Operations Management
ISBN:9781259667473
Author:William J Stevenson
Publisher:McGraw-Hill Education
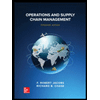
Operations and Supply Chain Management (Mcgraw-hi...
Operations Management
ISBN:9781259666100
Author:F. Robert Jacobs, Richard B Chase
Publisher:McGraw-Hill Education
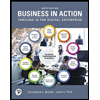
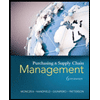
Purchasing and Supply Chain Management
Operations Management
ISBN:9781285869681
Author:Robert M. Monczka, Robert B. Handfield, Larry C. Giunipero, James L. Patterson
Publisher:Cengage Learning
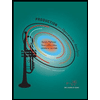
Production and Operations Analysis, Seventh Editi...
Operations Management
ISBN:9781478623069
Author:Steven Nahmias, Tava Lennon Olsen
Publisher:Waveland Press, Inc.