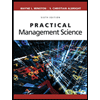
Practical Management Science
6th Edition
ISBN: 9781337406659
Author: WINSTON, Wayne L.
Publisher: Cengage,
expand_more
expand_more
format_list_bulleted
Question
The average days account receiveable/ days of inventory?
![Company Ajax has the following information from its financial statements
in 2021.
The annual sales revenue was $271 million and we assume that the
company operated for 365 days last year. The accounts receivable (AR)
amounted to $31.8 million and the accounts payable (AP) to $33.2
million. Further from the balance sheet, the inventory is valued at $12.6
million. The cost of sales (COGS/Revenue) is 50%.
Part 1: The average days of accounts receivable is
[Select]
Part 2: The average days of inventory is [Select]
Part 3: The average days of accounts payable is
[ Select ]
Part 4: The cash-to-cash cycle time is [Select]](https://content.bartleby.com/qna-images/question/94318975-01ba-4d18-9ca1-9fd38cc18d5f/b3e489ae-4db7-4e5c-8f4f-fd294afc709d/1xobu1_thumbnail.jpeg)
Transcribed Image Text:Company Ajax has the following information from its financial statements
in 2021.
The annual sales revenue was $271 million and we assume that the
company operated for 365 days last year. The accounts receivable (AR)
amounted to $31.8 million and the accounts payable (AP) to $33.2
million. Further from the balance sheet, the inventory is valued at $12.6
million. The cost of sales (COGS/Revenue) is 50%.
Part 1: The average days of accounts receivable is
[Select]
Part 2: The average days of inventory is [Select]
Part 3: The average days of accounts payable is
[ Select ]
Part 4: The cash-to-cash cycle time is [Select]
Expert Solution

arrow_forward
Step 1
Account receivable is the amount that receivable from outstanding at the end of the each business day. Average daily accounts receivable is determined by dividing account receivable by sales revenue.
Formula = Account receivable / Sales revenue *365
Sales revenue = $271 million
Account receivable = $31.8 million
Number of days = 365
Step by stepSolved in 3 steps

Knowledge Booster
Similar questions
- Component Immediate Parent Usage per Parent Lead Time (weeks) Beginning Inventory A none — 1 0 B A 2 2 250 C A 1 6 500 D A 3 3 750 E A 2 2 750 F B 4 2 3000 G B 2 4 1000 H D 3 2 5000 I D 2 4 5000 J E 1 8 1000 K E 5 1 5000 L E 2 4 2500 M F 3 3 250 N F 6 3 2560 O H 2 4 0 P K 1 2 500 Q K 2 3 1000 Using the information given, calculate the replenishment time when no beginning inventory exists.arrow_forwardQuestion 3The weekly demand for a product, which is held in stock is always 90 units.When an order for new stock is placed, it is delivered almost instantaneously by an ordering cost of 50,000 is incurred. The product costs 3,000 per unit,and it costs 15 percent of this amount to hold a unit in stock for a year.Currently, orders are placed for 2000 units. There are 50 working weeks in ayear and lead time is one week. a) As a management science student, the MD of the company seeks yourexpert advice on ways in which to determine the economic order quantity,optimal order cycle time, re-order level and total annual inventory cost.Advise the MD, providing detailed explanation using your answer. Writeyour answer in a form of a report to the MD. b) Advise the MD about savings, if any, could be made by changing fromcurrent order quantity of GH¢ 2000 units to the one obtained in (a) above. c) Describe the order policy followed by the firm based on your calculationsarrow_forwardExplain the difference between a periodic and perpetual inventory system. Would either be necessary or both be essential for a restaurant?arrow_forward
- Please do not give solution in image format thanku 1. Current total inventory level (I E) of a company is 10,000 units, which are held at 4 different facilities (n E). Next year, the company plans to open 12 new facilities. Provide an estimate on the total future inventory level (I F) for the company. a. 60,000 units b. 10,000 units c. 40,000 units d. 20,000 units e. 17,321 unitsarrow_forwardThe president of Hill Enterprises, Terri Hill, projects the firm's aggregate demand requirements over the next 8 months as follows: 2,200 January 1,400 May February 1,600 June 2,200 March April 1,800 1,800 July August 1,800 1,400 Her operations manager is considering a new plan, which begins in January with 200 units of inventory on hand. Stockout cost of lost sales is $100 per unit. Inventory holding cost is $25 per unit per month. Ignore any idle-time costs. The plan is called plan C. Plan C: Keep a stable workforce by maintaining a constant production rate equal to the average gross requirements excluding initial inventory and allow varying inventory levels. Conduct your analysis for January through August.arrow_forwardb. Question 4 Fortis Utility Company uses 2,000 units per year which it stores at $0.50 per unit per annum. The cost to place an order is $100. Calculate: If the company decides to make the items on its own machine with a potential capacity of 4,000 units per year, calculate: i. the batch order quantity (BOQ) the annual ordering cost the annual carrying cost ii. the economic order quantity (EOQ) the number of orders. iii.arrow_forward
- Questions in red 10-12arrow_forwardEach Triam Deluxe gamer computer system consists of two speakers, a monitor, a system unit, a keyboard, and an installation kit. These pieces are packed together and shipped as a complete kit. In MRP terms, all of these items are level 1 items that make the level 0 kits. Complete the MRP records, using the following information: • Production plans for complete kits are as follows: Start assembling 4,500 kits in week 2 Start assembling 1,000 kits in weeks 3, 4, and 5 Start assembling 8,000 kits in week 6 • The gross requirements for the system unit have already been given to you. For the remaining items, you will need to figure out the gross requirements. • All scheduled receipts, lead times, and beginning inventory levels are shown. Click the icon to view the MRP records. Construct the material requirements plan for item System unit (enter your responses as whole numbers). System unit: Lead Time = 1 week; Minimum order quantity = 3,500 Week 1 2 3 Gross requirements 4,500 1,000…arrow_forwardQuestion 1 Consider again managing inventory for product 101, provided by Supplier A. Recall thatdemand for 101 is approximately d = 200 units per week. You pay a purchase cost p = $500per unit and value your inventory at r = $550 per unit. You estimate your inventory carry-ing cost rate at r = 18% per year; storing one item of product 101 in your DC requires anequivalent rent (storage cost) of s = $10 per unit per year.Use truckload shipping for your orders of product 101; recall then that your total fixedcost (k + F ) = $900 for any order of size no greater than Q = 700 units. You estimate atotal lead time (order processing plus transit time) of 12 days for these shipments.To reduce your logistics costs, you decide that it might be worthwhile to backorder someof the customer demand you face each cycle. When backordering, you will delay your out-bound shipping of some of your customers’ orders.arrow_forward
- Question: How do you use the Silver-Meal ordering policy to find the Total annual Cost for the damand and parameters listed below? Month Period Demand Jan. 1 110 Feb. 2 40 Mar. 3 150 Apr. 4 130 May 5 60 Jun. 6 30 Jul. 7 20 Aug. 8 30 Sep. 9 80 Oct. 10 120 Nov. 11 130 Dec. 12 100 Total 1000 Given cost parameter: Value Order cost $25 Unit cost $8 Holding cost rate (monthly) 5%arrow_forwardQuestion 7 Firm develop new products to a.gain market share and build brand equity b.keep their research and development teams gainfully employed c.take up slack in capacity d.gain first mover advantage and eliminate waste Question 8 Economic order quantity (EOQ) assumes all of the following conditions apply .demand is known and is constant over time .there are no shortages allowed.lead time for the receipt of orders is constant.Order quantity is received all at once true or false? question 10 Trade-offs in the new product development relate to A.Product / service design, time to market and profitability B.Proft. Expenditure and market share C.Time. cost and quality D.Market reach, product / service design and timingarrow_forwardQ7arrow_forward
arrow_back_ios
SEE MORE QUESTIONS
arrow_forward_ios
Recommended textbooks for you
- Practical Management ScienceOperations ManagementISBN:9781337406659Author:WINSTON, Wayne L.Publisher:Cengage,Operations ManagementOperations ManagementISBN:9781259667473Author:William J StevensonPublisher:McGraw-Hill EducationOperations and Supply Chain Management (Mcgraw-hi...Operations ManagementISBN:9781259666100Author:F. Robert Jacobs, Richard B ChasePublisher:McGraw-Hill Education
- Purchasing and Supply Chain ManagementOperations ManagementISBN:9781285869681Author:Robert M. Monczka, Robert B. Handfield, Larry C. Giunipero, James L. PattersonPublisher:Cengage LearningProduction and Operations Analysis, Seventh Editi...Operations ManagementISBN:9781478623069Author:Steven Nahmias, Tava Lennon OlsenPublisher:Waveland Press, Inc.
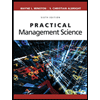
Practical Management Science
Operations Management
ISBN:9781337406659
Author:WINSTON, Wayne L.
Publisher:Cengage,
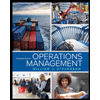
Operations Management
Operations Management
ISBN:9781259667473
Author:William J Stevenson
Publisher:McGraw-Hill Education
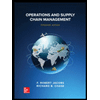
Operations and Supply Chain Management (Mcgraw-hi...
Operations Management
ISBN:9781259666100
Author:F. Robert Jacobs, Richard B Chase
Publisher:McGraw-Hill Education
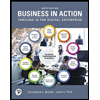
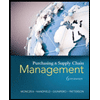
Purchasing and Supply Chain Management
Operations Management
ISBN:9781285869681
Author:Robert M. Monczka, Robert B. Handfield, Larry C. Giunipero, James L. Patterson
Publisher:Cengage Learning
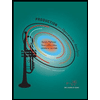
Production and Operations Analysis, Seventh Editi...
Operations Management
ISBN:9781478623069
Author:Steven Nahmias, Tava Lennon Olsen
Publisher:Waveland Press, Inc.