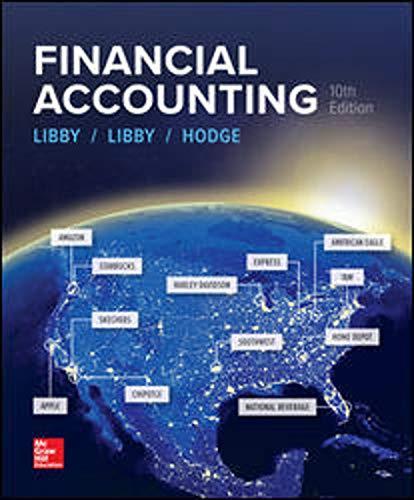
Chow’s Corporation has a Parts Division that does work for other Divisions in the company as well as for outside customers. The company’s Machine Products Division is currently purchasing 10,000 units of special parts at $29 per unit from an outside supplier every year. The special parts could also be produced by the Parts Division at variable production costs of $15 per unit.
However, in order to have time and space to produce the special part, the Parts Division would have to cut back production of another part, the H56 that it presently is producing. The H56 sells for $32 per unit and requires $19 per unit in variable production costs.
Packaging and shipping costs of the H56 are $3 per unit. Packaging and shipping costs for the special part would be only $1 per unit. The Parts Division is now producing and selling 40,000 units of the H56 each year. Production and sales of the H56 would drop by 20% if the special part is produced for the Machine Products Division.
a. What is the range of transfer prices within which both the Divisions’ profits would increase as a result of agreeing to the transfer of 10,000 special parts per year from the Parts Division to the Machine Products Division?
b. Is it in the best interests of Chow’s Corporation for this transfer to take place? Explain.

Trending nowThis is a popular solution!
Step by stepSolved in 3 steps with 3 images

- Desks Unlimited makes all types of office desks. The Computer Desk Division is currently producing 10,000 desks per year with a capacity of 15,000 desks. The variable costs assigned to each desk are $400 and annual fixed costs of the division are $900,000. The computer desk has a market price of $600. The Executive Division wants to buy 5,000 desks from the Computer division at $460 for its custom office design business. The Computer Division manager knows that the division will save $50 of the Variable costs since there will be no variable shipping or commissions to be paid on the transfer order. However, the Computer Desk manager refused the order because the price is below full cost. The Executive Division manager argues that the order should be accepted because it will lower the fixed cost per desk from $90 to $60 and will take the division to its capacity, thereby causing operations to be at their most efficient level. [This is how he came up with the offered $460 transfer…arrow_forwardArtisan Metalworks has a bottleneck in their production that occurs within the engraving department. Jamal Moore, the COO, is considering hiring an extra worker, whose salary will be $54,000 per year, to solve the problem. With this extra worker, the company could produce and sell 3,000 more units per year. Currently, the selling price per unit is $26.00 and the cost per unit is $7.75. Direct materials $3.40 Direct labor 1.10 Variable overhead 0.45 Fixed overhead (primarily depreciation of equipment) 2.80 Total $7.75 Using the information provided, calculate the annual financial impact of hiring the extra worker. Profit $fill in the blank 1arrow_forwardThe Trailer division of Baxter Bicycles makes bike trailers that attach to bicycles and can carry children or cargo. The trailers have a market price of $103 each. Each trailer incurs $38 of variable manufacturing costs. The Trailer division has capacity for 29,000 trailers per year and has fixed costs of $480,000 per year. 1. Assume the Assembly division of Baxter Bicycles wants to buy 5,200 trailers per year from the Trailer division. If the Trailer division can sell all of the trailers it manufactures to outside customers (and has no excess capacity), what price should be used on transfers between divisions? 2. Assume the Trailer division currently only sells 10,200 trailers to outside customers and has excess capacity. The Assembly division wants to buy 5,200 trailers per year from the Trailer division. What is the range of acceptable prices on transfers between divisions? 1. Transfer price per trailer 2. Transfer price per trailer will be at least but not more thanarrow_forward
- Management of the Crane Company would like the Food Division to transfer 11000 cans of its final product to the Restaurant Division for $40. The Food Division sells the product to customers for $80 per unit. The Food Division’s variable cost per unit is $43 and its fixed cost per unit is $9.If the Food Division has 11000 units available capacity, what is the minimum transfer price the Food Division should accept?arrow_forwardJupiter Game Company manufactures pocket electronic games. Last year Jupiter sold 25,000 games at $25 each. Total costs amounted to $525,000, of which $150,000 were considered fixed costs. In an attempt to improve its product, the company is considering replacing a component part that has a cost of $2.50 with a new and better part costing $4.50 per unit in the coming year. A new machine also would be needed to increase plant capacity. The machine would cost $18,000 with a useful life of six years and no salvage value. The company uses straight-line depreciation on all plant assets. (Ignore income taxes). 1) If the firm holds the sales price constant and makes the suggested changes, how many units of product will the company have to sell to make the same net income as last year?arrow_forwardElroy Racers makes bicycles. It has always purchased its bicycle tires from the M. Wilson Tires at $25 each but is currently considering making the tires in its own factory. The estimated costs per unit of making the tires are as follows: Direct materials $8 Direct labor $5 Variable manufacturing overhead $7 The company’s fixed expenses would increase by $60,000 per year if managers decided to make the tire.(b)What qualitative factors should Elroy Racers consider in making this decision?arrow_forward
- Artisan Metalworks has a bottleneck in their production that occurs within the engraving department. Jamal Moore, the COO, is considering hiring an extra worker, whose salary will be $54,000 per year, to solve the problem. With this extra worker, the company could produce and sell 3,000 more units per year. Currently, the selling price per unit is $25.00 and the cost per unit is $7.80. Direct materials $3.50 Direct labor 1.10 Variable overhead 0.40 Fixed overhead (primarily depreciation of equipment) 2.80 Total $7.80 Using the information provided, calculate the annual financial impact of hiring the extra worker. Profit $_____ ______arrow_forwardBrandon Corporation, the maker of a variety of rubber products, is in the midst of a business downturn and has many idle facilities. Nationwide Tire Company has approached Brandon to produce 400,000 oversized tire tubes for $3.00 each. Brandon predicts that its variable costs will be $3.20 each. Its fixed costs, which had been averaging $2.50 per unit on a variety of products, will now be spread over twice as much volume. The president commented, "Sure we will lose $.20 each on the variable costs, but we will gain $1 per unit by spreading our fixed costs over more units. Therefore, we should take the offer because it would gain us $.80 per unit." Brandon currently has a volume of 400,000 units, sales of $1,600,000, variable costs of $1,200,000, and fixed costs of $1,000,000. Required: a. Compute the impact on operating profit if the special order is accepted. b. Based on your calculations, explain why you agree or do not agree with the president. c. Would it be beneficial for Brandon…arrow_forwardHH Co. uses corrugated cardboard to ship its product to customers. Currently, the company’s returns department incurs annual overhead costs of $126,000 and forecasts 6,000 returns per year. Management believes it has found a better way to package its products. As a result, the company expects to reduce the number of shipments that are returned due to damage by 3%. In addition, the initiative is expected to reduce the department’s annual overhead by $14,000.Compute the returns department’s standard overhead rate per return (a) before the sustainability improvement and (b) after the sustainability improvement.arrow_forward
- Artisan Metalworks has a bottleneck in their production that occurs within the engraving department. Jamal Moore, the COO, is considering hiring an extra worker, whose salary will be $54,000 per year, to solve the problem. With this extra worker, the company could produce and sell 2,900 more units per year. Currently, the selling price per unit is $25.00 and the cost per unit is $7.50. Direct materials $3.40 Direct labor Variable overhead Fixed overhead (primarily depreciation of equipment) Total 1.00 0.40 2.70 $7.50 Using the Information provided, calculate the annual financial Impact of hiring the extra worker. Profit $ ✓ Increasearrow_forwardRace Cars, Inc., produces model cars made from aluminum. It operates two production departments, Molding and Painting, and has three service departments, Administration, Accounting, and Maintenance. The accumulated costs in the three service departments were $250,000, $400,000 and $200,000, respectively. Management is concerned that the costs of its service departments are getting too high. In particular, managers would like to keep the costs of service departments under $3.50 per unit on average. You have been asked to allocate service department costs to the two production departments and compute the unit costs. The company decided that Administration costs should be allocated on the basis of square footage used by each production and service department. Accounting costs are allocated on the basis of number of employees. Maintenance cost are allocated on the basis of the dollar value of the equipment in each department. The use of each base by all departments during the current…arrow_forwardFutura Company purchases the 60,000 starters that it installs in its standard line of farm tractors from a supplier for the price of $10.40 per unit. Due to a reduction in output, the company now has idle capacity that could be used to produce the starters rather than buying them from an outside supplier. However, the company’s chief engineer is opposed to making the starters because the production cost per unit is $11.20 as shown below: Per Unit Total Direct materials $ 5.00 Direct labor 2.50 Supervision 1.70 $ 102,000 Depreciation 1.10 $ 66,000 Variable manufacturing overhead 0.40 Rent 0.50 $ 30,000 Total product cost $ 11.20 If Futura decides to make the starters, a supervisor would have to be hired (at a salary of $102,000) to oversee production. However, the company has sufficient idle tools and machinery such that no new equipment would have to be purchased. The rent charge above is based on space utilized in the plant. The total rent on the…arrow_forward
- AccountingAccountingISBN:9781337272094Author:WARREN, Carl S., Reeve, James M., Duchac, Jonathan E.Publisher:Cengage Learning,Accounting Information SystemsAccountingISBN:9781337619202Author:Hall, James A.Publisher:Cengage Learning,
- Horngren's Cost Accounting: A Managerial Emphasis...AccountingISBN:9780134475585Author:Srikant M. Datar, Madhav V. RajanPublisher:PEARSONIntermediate AccountingAccountingISBN:9781259722660Author:J. David Spiceland, Mark W. Nelson, Wayne M ThomasPublisher:McGraw-Hill EducationFinancial and Managerial AccountingAccountingISBN:9781259726705Author:John J Wild, Ken W. Shaw, Barbara Chiappetta Fundamental Accounting PrinciplesPublisher:McGraw-Hill Education
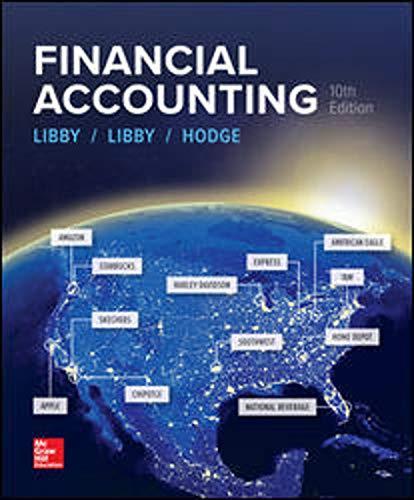
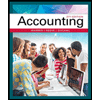
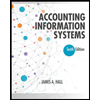
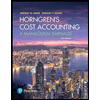
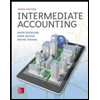
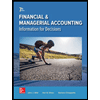