Charles and his younger brother, Edward, purchased Carpita Bottling Company from their father in 1983. The company bottles and distributes soda and beer in Nakuru. Since purchasing the company, Charles has been instrumental in modernizing operations. One of the latest acquisitions is a filling machine that can be adjusted to fill at any average level desired. Because the bottles and cans filled by the company are exclusively the 12-grams size, when they received the machine, Charles set the fill level to 12 grams and left it that way. According to the manufacturer’s specifications, the machine will fill bottles or cans around the average, with a standard deviation of 0.15 grams. Charles just returned from a convention at which he attended a panel discussion related to problems with filling machines. One bottling company representative discussed a problem her company had. It failed to learn that its machine’s average fill went out of adjustment until several months later, when its cost accounting department reported some problems with beer production in bulk not matching output in bottles and cans. It turns out that the machine’s average fill had increased from 12 grams to 12.07 grams. With large volumes of production, this deviation meant a substantial loss in profits. Another company reported the same type of problem, but in the opposite direction. Its machine began filling bottles with slightly less than 12 grams on the average. Although the consumers could not detect the shortage in a given bottle, the state agencies responsible for checking the accuracy of packaged products discovered the problem in their testing and substantially fined the company for the underfill. These problems were a surprise to Charles. He had not considered the possibility that the machine might go out of adjustment and pose these types of problems. In fact, he became very concerned because the problems of losing profits and potentially being fined by the government were ones that he wished to avoid, if possible. After the convention, Charles and Edward decided to hire a consulting firm with expertise in these matters to assist them in setting up a procedure for monitoring the performance of the filling machine. The consultant suggested that they set up a sampling plan in which once a month, they would sample some number of bottles and measure their volumes precisely. If the average of the sample deviated too much from 12 grams, they would shut the machine down and make the necessary adjustments. Otherwise, they would let the filling process continue. The consultant identified two types of problems that could occur from this sort of sampling plan: 1. They might incorrectly decide to adjust the machine when it was not really necessary to do so. 2. They might incorrectly decide to allow the filling process to continue when, in fact, the true average had deviated from 12 grams. After carefully considering what the consultant told them, Charles indicated that he wanted no more than a 0.02 chance of the first problem occurring because of the costs involved. He also decided that if the true average fill had slipped to 11.99 grams, he wanted no more than a 0.05 chance of not detecting this with his sampling plan. He wanted to avoid problems with state and federal agencies. Finally, if the true average fill had actually risen to 12.007 grams, he wanted to be able to detect this 98% of the time with his sampling plan. Thus, he wanted to avoid the lost profits that would result from such a problem. In addition, Charles needs to determine how large a sample size is necessary to meet his requirements. As a student of Business Statistics advice Charles.
Charles and his younger brother, Edward, purchased Carpita Bottling Company from their father in 1983. The company bottles and distributes soda and beer in Nakuru. Since purchasing the company, Charles has been instrumental in modernizing operations.
One of the latest acquisitions is a filling machine that can be adjusted to fill at any average level desired. Because the bottles and cans filled by the company are exclusively the 12-grams size, when they received the machine, Charles set the fill level to 12 grams and left it that way. According to the manufacturer’s specifications, the machine will fill bottles or cans around the average, with a standard deviation of 0.15 grams.
Charles just returned from a convention at which he attended a panel discussion related to problems with filling machines. One bottling company representative discussed a problem her company had. It failed to learn that its machine’s average fill went out of adjustment until several months later, when its cost accounting department reported some problems with beer production in bulk not matching output in bottles and cans. It turns out that the machine’s average fill had increased from 12 grams to 12.07 grams. With large volumes of production, this deviation meant a substantial loss in profits.
Another company reported the same type of problem, but in the opposite direction. Its machine began filling bottles with slightly less than 12 grams on the average. Although the consumers could not detect the shortage in a given bottle, the state agencies responsible for checking the accuracy of packaged products discovered the problem in their testing and substantially fined the company for the underfill.
These problems were a surprise to Charles. He had not considered the possibility that the machine might go out of adjustment and pose these types of problems. In fact, he became very concerned because the problems of losing profits and potentially being fined by the government were ones that he wished to avoid, if possible. After the convention, Charles and Edward decided to hire a consulting firm with expertise in these matters to assist them in setting up a procedure for monitoring the performance of the filling machine.
The consultant suggested that they set up a sampling plan in which once a month, they would sample some number of bottles and measure their volumes precisely. If the average of the sample deviated too much from 12 grams, they would shut the machine down and make the necessary adjustments. Otherwise, they would let the filling process continue. The consultant identified two types of problems that could occur from this sort of sampling plan:
1. They might incorrectly decide to adjust the machine when it was not really necessary to do so.
2. They might incorrectly decide to allow the filling process to continue when, in fact, the true average had deviated from 12 grams.
After carefully considering what the consultant told them, Charles indicated that he wanted no more than a 0.02 chance of the first problem occurring because of the costs involved. He also decided that if the true average fill had slipped to 11.99 grams, he wanted no more than a 0.05 chance of not detecting this with his sampling plan. He wanted to avoid problems with state and federal agencies. Finally, if the true average fill had actually risen to 12.007 grams, he wanted to be able to detect this 98% of the time with his sampling plan. Thus, he wanted to avoid the lost profits that would result from such a problem.
In addition, Charles needs to determine how large a
As a student of Business Statistics advice Charles.

Step by step
Solved in 3 steps

Charles and his younger brother, Edward, purchased Carpita Bottling Company from their father in 1983. The company bottles and distributes soda and beer in Nakuru. Since purchasing the company, Charles has been instrumental in modernizing operations.
One of the latest acquisitions is a filling machine that can be adjusted to fill at any average level desired. Because the bottles and cans filled by the company are exclusively the 12-grams size, when they received the machine, Charles set the fill level to 12 grams and left it that way. According to the manufacturer’s specifications, the machine will fill bottles or cans around the average, with a standard deviation of 0.15 grams.
Charles just returned from a convention at which he attended a panel discussion related to problems with filling machines. One bottling company representative discussed a problem her company had. It failed to learn that its machine’s average fill went out of adjustment until several months later, when its cost accounting department reported some problems with beer production in bulk not matching output in bottles and cans. It turns out that the machine’s average fill had increased from 12 grams to 12.07 grams. With large volumes of production, this deviation meant a substantial loss in profits.
Another company reported the same type of problem, but in the opposite direction. Its machine began filling bottles with slightly less than 12 grams on the average. Although the consumers could not detect the shortage in a given bottle, the state agencies responsible for checking the accuracy of packaged products discovered the problem in their testing and substantially fined the company for the underfill.
These problems were a surprise to Charles. He had not considered the possibility that the machine might go out of adjustment and pose these types of problems. In fact, he became very concerned because the problems of losing profits and potentially being fined by the government were ones that he wished to avoid, if possible. After the convention, Charles and Edward decided to hire a consulting firm with expertise in these matters to assist them in setting up a procedure for monitoring the performance of the filling machine.
The consultant suggested that they set up a sampling plan in which once a month, they would sample some number of bottles and measure their volumes precisely. If the average of the sample deviated too much from 12 grams, they would shut the machine down and make the necessary adjustments. Otherwise, they would let the filling process continue. The consultant identified two types of problems that could occur from this sort of sampling plan:
They might incorrectly decide to adjust the machine when it was not really necessary to do so.
They might incorrectly decide to allow the filling process to continue when, in fact, the true average had deviated from 12 grams.
After carefully considering what the consultant told them, Charles indicated that he wanted no more than a 0.02 chance of the first problem occurring because of the costs involved. He also decided that if the true average fill had slipped to 11.99 grams, he wanted no more than a 0.05 chance of not detecting this with his sampling plan. He wanted to avoid problems with state and federal agencies. Finally, if the true average fill had actually risen to 12.007 grams, he wanted to be able to detect this 98% of the time with his sampling plan. Thus, he wanted to avoid the lost profits that would result from such a problem.
In addition, Charles needs to determine how large a
As a student of Business Statistics advice Charles.
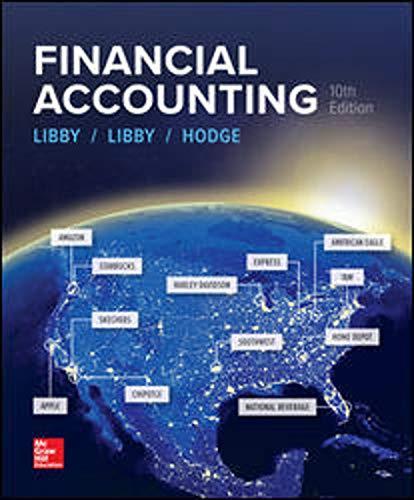
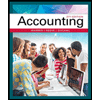
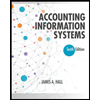
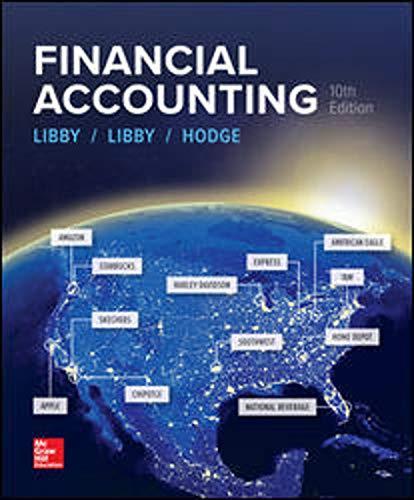
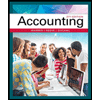
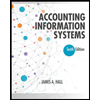
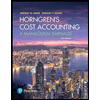
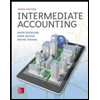
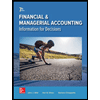