CASE STUDY - ERGONOMICS Read the case and answer the questions given below: At Deere and Company, assessors recommended changes in the construction department that would limit the physical toll taken on workers performing their routine tasks. Analysis and feedback from workers showed that lifting heavy objects was common, while poorly designed tools contributed to repetitive motion injuries. Further, observation revealed that Deere and Company was losing money on reduced productivity due to the work environment. Workers' compensation costs increased by 15 percent each year, and high numbers of first-aid cases led to staggering health care costs and huge losses in productivity due to absenteeism. However, a new ergonomics training program helped Deere and Company to reduce their injury rates and provide a healthier work environment for its employees. The course covered common issues, many of which appear at companies across industries. Are there any heavy or strenuous lifting/lowering tasks in the job? Do the hand tools they use have an awkward grip? Is the height of the work comfortable for them? Do they experience fatigue and discomfort doing the job? These questions were addressed and the root problems corrected with redesigned workspaces and new hand tools to help workers avoid strains and stress injuries. After implementation, Deere and Company reported an 83 percent reduction in back injuries, along with a 32 percent drop in health care compensation over the last ten years. By involving workers early in the process, the company came to understand the issues on its job floor and learned to address them in detail. Questions: How Ergonomics helped Deere in overcoming their issues? What actually reduced the health care compensation at Deere by 32%?
CASE STUDY - ERGONOMICS Read the case and answer the questions given below: At Deere and Company, assessors recommended changes in the construction department that would limit the physical toll taken on workers performing their routine tasks. Analysis and feedback from workers showed that lifting heavy objects was common, while poorly designed tools contributed to repetitive motion injuries. Further, observation revealed that Deere and Company was losing money on reduced productivity due to the work environment. Workers' compensation costs increased by 15 percent each year, and high numbers of first-aid cases led to staggering health care costs and huge losses in productivity due to absenteeism. However, a new ergonomics training program helped Deere and Company to reduce their injury rates and provide a healthier work environment for its employees. The course covered common issues, many of which appear at companies across industries. Are there any heavy or strenuous lifting/lowering tasks in the job? Do the hand tools they use have an awkward grip? Is the height of the work comfortable for them? Do they experience fatigue and discomfort doing the job? These questions were addressed and the root problems corrected with redesigned workspaces and new hand tools to help workers avoid strains and stress injuries. After implementation, Deere and Company reported an 83 percent reduction in back injuries, along with a 32 percent drop in health care compensation over the last ten years. By involving workers early in the process, the company came to understand the issues on its job floor and learned to address them in detail. Questions: How Ergonomics helped Deere in overcoming their issues? What actually reduced the health care compensation at Deere by 32%?
Chapter1: Making Economics Decisions
Section: Chapter Questions
Problem 1QTC
Related questions
Question
picture attach of the case study kindly read and answer question number 2 that is,
Q) what actually reduced the health care compensation at deere by 32%?

Transcribed Image Text:CASE STUDY - ERGONOMICS
Read the case and answer the questions given below:
At Deere and Company, assessors recommended changes in the construction
department that would limit the physical toll taken on workers performing their routine tasks.
Analysis and feedback from workers showed that lifting heavy objects was common, while
poorly designed tools contributed to repetitive motion injuries. Further, observation revealed
that Deere and Company was losing money on reduced productivity due to the work
environment. Workers' compensation costs increased by 15 percent each year, and high
numbers of first-aid cases led to staggering health care costs and huge losses in productivity
due to absenteeism.
However, a new ergonomics training program helped Deere and Company to reduce
their injury rates and provide a healthier work environment for its employees. The course
covered common issues, many of which appear at companies across industries. Are there any
heavy or strenuous lifting/lowering tasks in the job? Do the hand tools they use have an
awkward grip? Is the height of the work comfortable for them? Do they experience fatigue and
discomfort doing the job? These questions were addressed and the root problems corrected
with redesigned workspaces and new hand tools to help workers avoid strains and stress
injuries.
After implementation, Deere and Company reported an 83 percent reduction in back
injuries, along with a 32 percent drop in health care compensation over the last ten years. By
involving workers early in the process, the company came to understand the issues on its job
floor and learned to address them in detail.
Questions:
How Ergonomics helped Deere in overcoming their issues?
What actually reduced the health care compensation at Deere by 32%?
Expert Solution

This question has been solved!
Explore an expertly crafted, step-by-step solution for a thorough understanding of key concepts.
Step by step
Solved in 2 steps

Knowledge Booster
Learn more about
Need a deep-dive on the concept behind this application? Look no further. Learn more about this topic, economics and related others by exploring similar questions and additional content below.Recommended textbooks for you
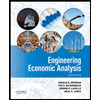
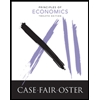
Principles of Economics (12th Edition)
Economics
ISBN:
9780134078779
Author:
Karl E. Case, Ray C. Fair, Sharon E. Oster
Publisher:
PEARSON
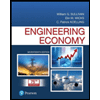
Engineering Economy (17th Edition)
Economics
ISBN:
9780134870069
Author:
William G. Sullivan, Elin M. Wicks, C. Patrick Koelling
Publisher:
PEARSON
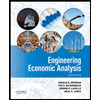
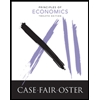
Principles of Economics (12th Edition)
Economics
ISBN:
9780134078779
Author:
Karl E. Case, Ray C. Fair, Sharon E. Oster
Publisher:
PEARSON
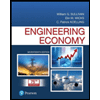
Engineering Economy (17th Edition)
Economics
ISBN:
9780134870069
Author:
William G. Sullivan, Elin M. Wicks, C. Patrick Koelling
Publisher:
PEARSON
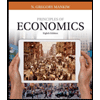
Principles of Economics (MindTap Course List)
Economics
ISBN:
9781305585126
Author:
N. Gregory Mankiw
Publisher:
Cengage Learning
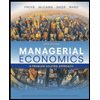
Managerial Economics: A Problem Solving Approach
Economics
ISBN:
9781337106665
Author:
Luke M. Froeb, Brian T. McCann, Michael R. Ward, Mike Shor
Publisher:
Cengage Learning
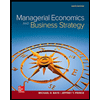
Managerial Economics & Business Strategy (Mcgraw-…
Economics
ISBN:
9781259290619
Author:
Michael Baye, Jeff Prince
Publisher:
McGraw-Hill Education